Toyota’s Lean Supply Chain: The Secret Behind JIT Manufacturing Success | MBA Case study analysis
Summary
TLDRToyota’s innovative lean supply chain, powered by Just In Time (JIT) manufacturing, has revolutionized the automotive industry by minimizing waste and maximizing efficiency. By producing only what is needed when it’s needed, Toyota reduces costs, improves product quality, and enhances flexibility in response to market demands. The system relies on strong supplier relationships, precise timing, and continuous improvement, while also addressing challenges like supply chain disruptions and transportation delays. Toyota’s approach has set a global benchmark, influencing industries like Amazon and Nike, and remains a game-changer in the world of manufacturing.
Takeaways
- 😀 Toyota is the largest automobile manufacturer in the world, producing over 10 million vehicles annually while maintaining high efficiency and low costs.
- 😀 Toyota pioneered the Just in Time (JIT) manufacturing system in the 1970s, which focuses on producing only what is needed, when it's needed, to minimize waste and improve efficiency.
- 😀 The lean supply chain approach at Toyota is built around eliminating waste in every process, including overproduction, waiting time, and excess inventory.
- 😀 Toyota’s JIT system minimizes inventory storage costs and reduces the risk of having obsolete or unused parts.
- 😀 The JIT system ensures flexibility in production, allowing Toyota to quickly adjust to market demand and avoid overproduction.
- 😀 Toyota's focus on Kaizen (continuous improvement) drives small, incremental changes that lead to significant operational improvements over time.
- 😀 Jidoka, or automation with a human touch, allows Toyota’s machines to stop automatically if a problem occurs, enabling workers to resolve issues before they escalate.
- 😀 The Canban system is a key part of JIT, ensuring that materials are only brought to the production line when they are needed, maintaining continuous flow.
- 😀 While JIT improves efficiency, it also makes Toyota vulnerable to supply chain disruptions. Any delay in material delivery can halt production.
- 😀 To mitigate JIT risks, Toyota maintains strong relationships with suppliers, employs multi-sourcing strategies, and uses strategic buffer inventories in critical areas.
- 😀 Toyota has invested heavily in logistics optimization and real-time data sharing to ensure timely deliveries of parts, reducing delays in production.
Q & A
What is the Just In Time (JIT) manufacturing system?
-Just In Time (JIT) is a production strategy where materials and components are delivered exactly when they are needed in the production process—no earlier and no later. This minimizes inventory costs, reduces waste, and ensures production flows smoothly, based on real-time demand.
How did Toyota's visit to American supermarkets influence their manufacturing strategy?
-Toyota’s visit to American supermarkets inspired their JIT approach. They observed how products were restocked only when needed, which sparked the idea of producing and delivering parts to the production line only when required, significantly reducing waste and improving efficiency.
What are the core principles of Toyota's lean supply chain?
-Toyota's lean supply chain focuses on minimizing waste while maximizing value. Key principles include continuous flow, waste reduction, production leveling (Heijunka), and ensuring that every task and process adds value to the final product.
How does JIT manufacturing help reduce waste in Toyota's production process?
-JIT minimizes waste by ensuring that parts and materials are delivered only when needed. This prevents overproduction, reduces the need for storage space, and minimizes the risk of having excess or obsolete inventory.
What is Kaizen, and why is it important to Toyota's lean supply chain?
-Kaizen, which means 'continuous improvement,' is a fundamental principle in Toyota’s lean supply chain. It involves making small, incremental changes to improve processes, reduce inefficiencies, and enhance overall productivity over time.
What is Jidoka, and how does it contribute to Toyota's efficiency?
-Jidoka refers to 'automation with a human touch.' In Toyota’s system, machines are programmed to stop automatically if a problem arises, allowing workers to intervene and solve the issue. This prevents defects from being passed down the line and ensures high quality.
What are the key benefits of Toyota's Just In Time system?
-The key benefits of Toyota's JIT system include reduced inventory costs, improved product quality, increased flexibility in responding to changes in customer demand, and a more efficient production process with fewer bottlenecks.
What challenges does Toyota face with its JIT manufacturing system?
-Challenges of JIT include vulnerability to supply chain disruptions, such as natural disasters or delays from suppliers. JIT also places pressure on suppliers to deliver parts on time and can struggle to handle sudden surges in demand due to the lack of buffer stock.
How does Toyota manage the risk of supply chain disruptions in its JIT system?
-Toyota manages the risk of disruptions by building strong relationships with suppliers, diversifying suppliers for critical parts, using strategic buffer inventories, and optimizing logistics to ensure timely deliveries. They also use advanced tracking systems to monitor real-time data and reduce delays.
Why is it crucial for Toyota to maintain close relationships with its suppliers?
-Maintaining close relationships with suppliers is crucial for Toyota's JIT system because it ensures that parts are delivered exactly when needed. Strong supplier partnerships reduce the risk of delays, promote reliability, and help Toyota maintain a smooth production flow.
Outlines
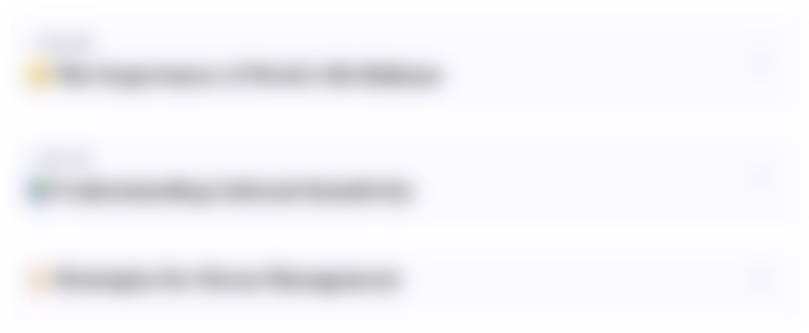
This section is available to paid users only. Please upgrade to access this part.
Upgrade NowMindmap
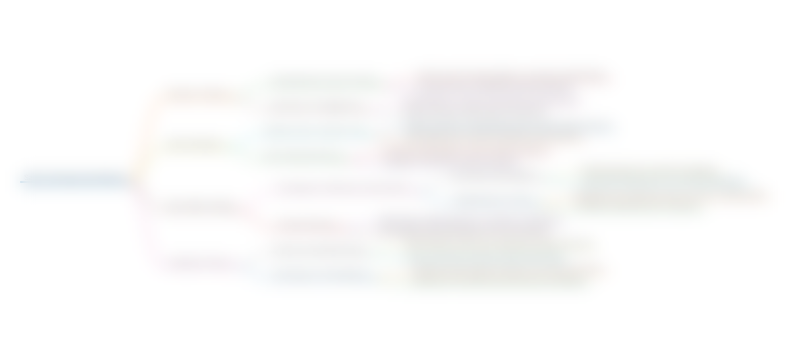
This section is available to paid users only. Please upgrade to access this part.
Upgrade NowKeywords
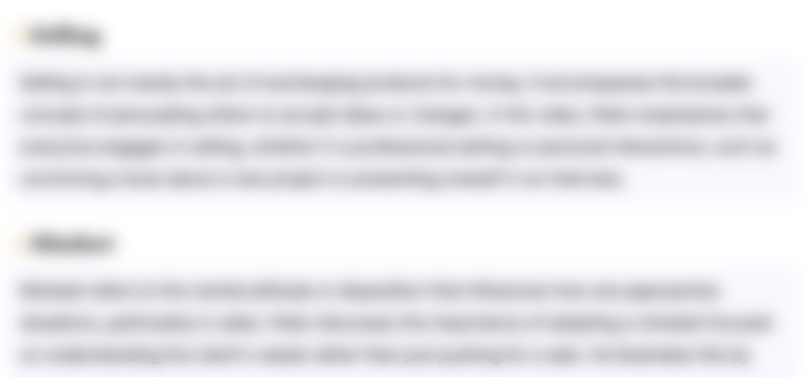
This section is available to paid users only. Please upgrade to access this part.
Upgrade NowHighlights
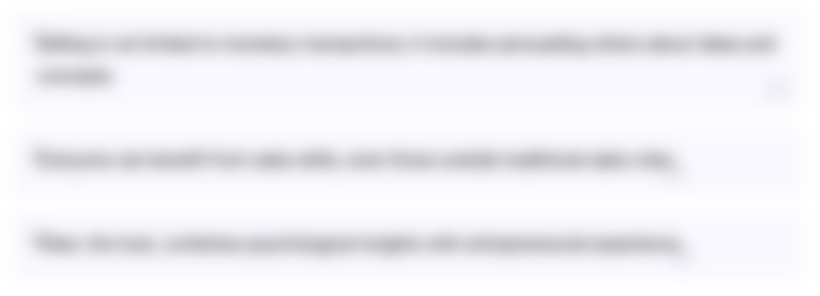
This section is available to paid users only. Please upgrade to access this part.
Upgrade NowTranscripts
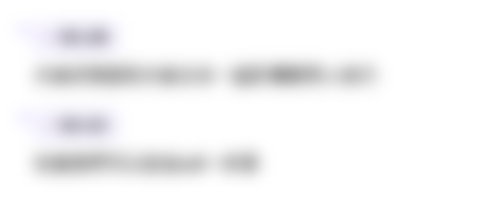
This section is available to paid users only. Please upgrade to access this part.
Upgrade NowBrowse More Related Video
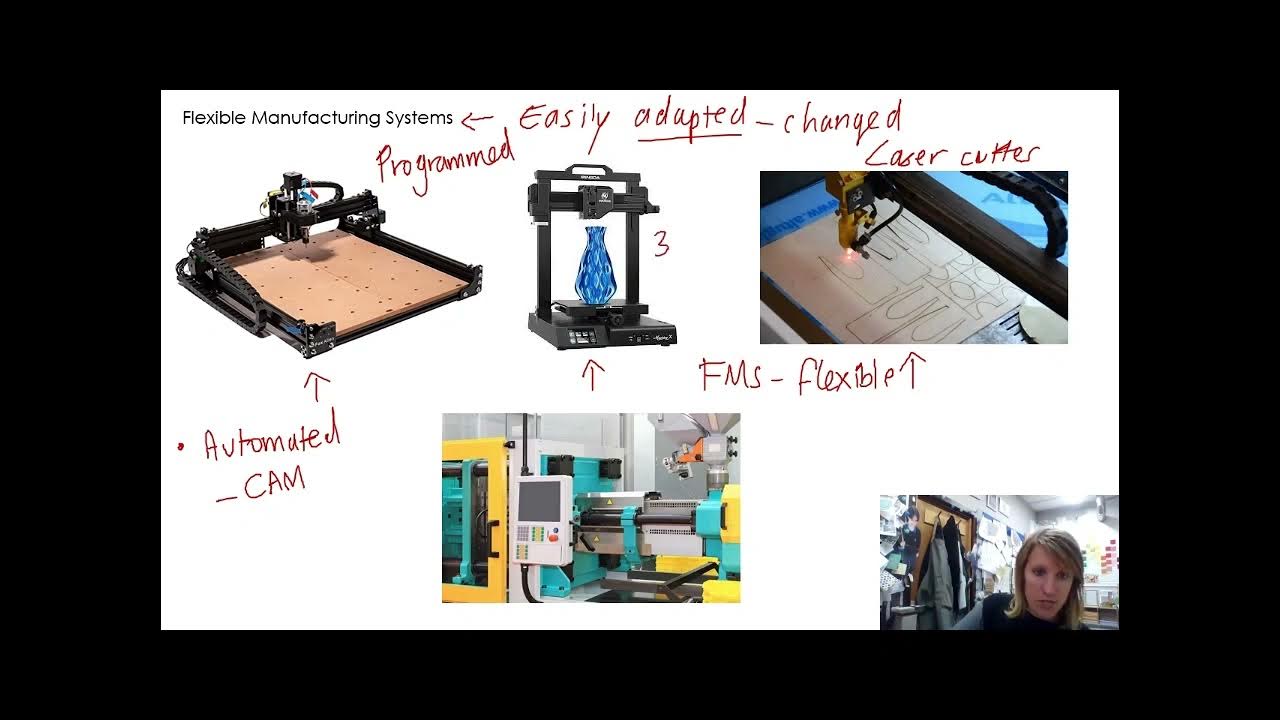
Video 2 - Flexible and Lean Manufacturing

Modelo Toyota de Produção - Just In Time & Kanban
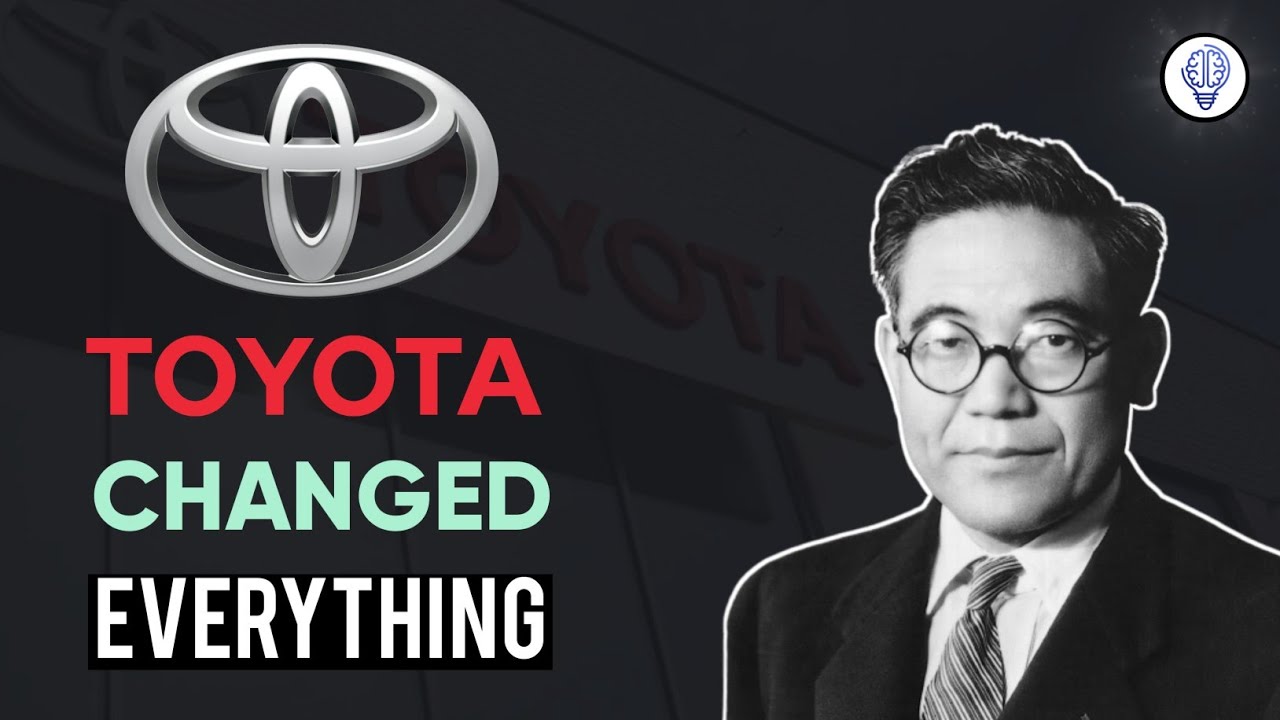
How did Toyota beat FORD & GM using its GENIUS Supply Chain Model?

Just in Time Production Explained | Toyota, Dell and Walmart Examples

⚙ Lean Manufacturing | A pursuit of perfection
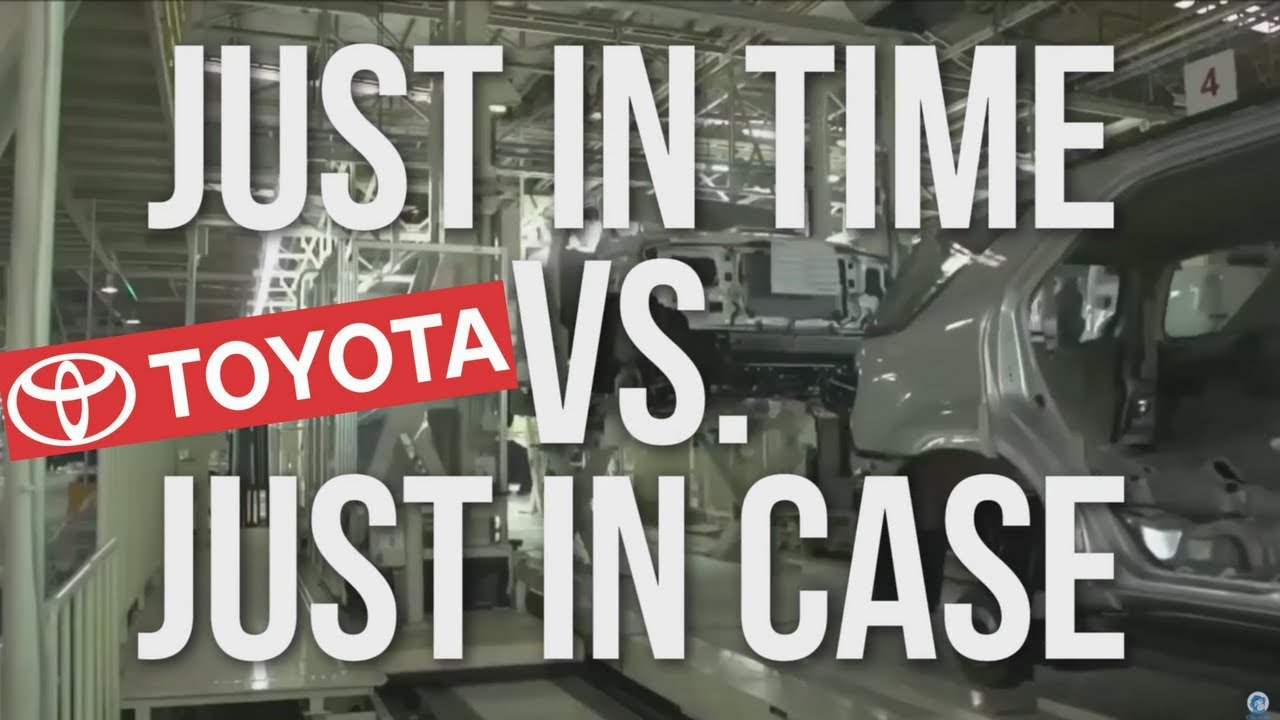
Just in Time by Toyota: The Smartest Production System in The World
5.0 / 5 (0 votes)