Job Order Costing
Summary
TLDRIn this video, the concept of job order costing is explained using the example of a firm manufacturing playground equipment. Unlike firms with homogeneous products (like oil), which use process costing, businesses with multiple, distinct products, such as slides and swings, need job order costing. The video illustrates how to create a job cost sheet that includes costs for direct materials, labor, and applied manufacturing overhead, using an example job (a237) to demonstrate how to calculate these costs, ultimately totaling $1,700 for the slide job.
Takeaways
- 😀 Job order costing is used by firms that manufacture different products, like playground equipment, to track the costs associated with each unique job.
- 😀 Process costing, on the other hand, is used by companies that produce homogeneous products, such as oil, where costs are uniform across all units.
- 😀 In job order costing, each product has distinct raw materials, labor, and costs, requiring a separate cost sheet for each order.
- 😀 A job cost sheet includes three main sections: direct materials, direct labor, and manufacturing overhead.
- 😀 The direct materials section of a job cost sheet lists the cost of raw materials used for the job.
- 😀 The direct labor section lists the total labor cost, which is calculated by multiplying hours worked by the hourly wage rate.
- 😀 Manufacturing overhead is applied based on a predetermined rate, usually tied to a cost driver like labor hours.
- 😀 For example, if the cost driver is labor hours, the overhead is calculated by multiplying the number of labor hours by the overhead rate.
- 😀 The total cost of a job is calculated by adding the costs for direct materials, direct labor, and applied manufacturing overhead.
- 😀 Job order costing helps companies determine the total cost of fulfilling specific customer orders, aiding in pricing decisions and ensuring profitability.
Q & A
What is job order costing, and when is it used?
-Job order costing is a costing method used when a firm manufactures different types of products, each with varying costs. It is used in situations where products are distinct and require different resources and processes, such as a playground equipment manufacturer.
How does job order costing differ from process costing?
-Job order costing is used for firms with different products that require specific costing, while process costing is used for firms that produce a homogeneous product, like oil, where costs are applied uniformly across the production.
What is a job cost sheet, and what does it include?
-A job cost sheet is a document used to track the costs associated with a specific job. It typically includes sections for direct materials, direct labor, and applied manufacturing overhead.
What types of costs are tracked on a job cost sheet?
-The costs tracked on a job cost sheet include direct materials, direct labor, and applied manufacturing overhead.
What is direct labor, and how is it calculated?
-Direct labor refers to the work performed by employees directly involved in producing a product. It is calculated by multiplying the number of labor hours worked by the labor rate per hour.
How is manufacturing overhead applied in job order costing?
-Manufacturing overhead is applied based on a predetermined overhead rate, which is typically calculated using a cost driver, such as labor hours. The applied overhead is calculated by multiplying the labor hours by the predetermined overhead rate.
What is the cost driver in the example given in the script?
-In the example, the cost driver is labor hours, meaning manufacturing overhead is applied based on the number of labor hours worked.
How is the total cost for a job calculated?
-The total cost for a job is calculated by adding the costs of direct materials, direct labor, and the applied manufacturing overhead.
In the example, what is the cost of direct materials for job A237?
-In the example, the direct materials for job A237 cost $1,000.
How do you calculate the applied manufacturing overhead for job A237?
-The applied manufacturing overhead for job A237 is calculated by multiplying the number of labor hours (50) by the predetermined overhead rate ($4), resulting in $200.
Outlines
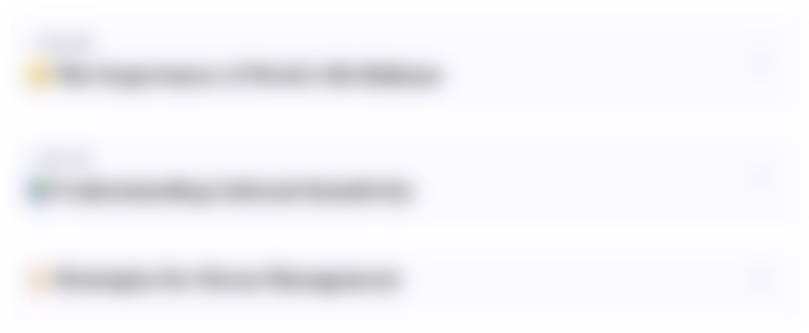
此内容仅限付费用户访问。 请升级后访问。
立即升级Mindmap
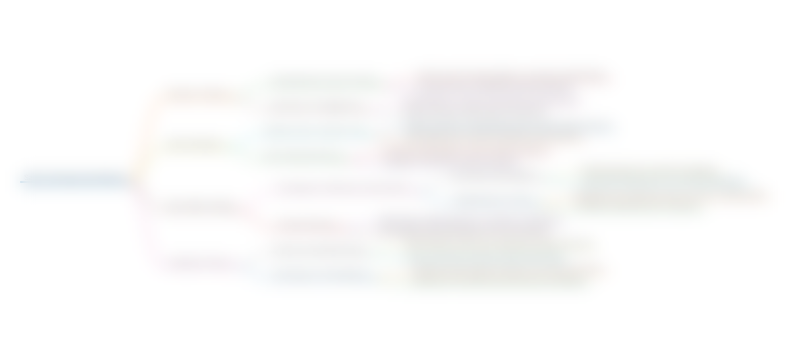
此内容仅限付费用户访问。 请升级后访问。
立即升级Keywords
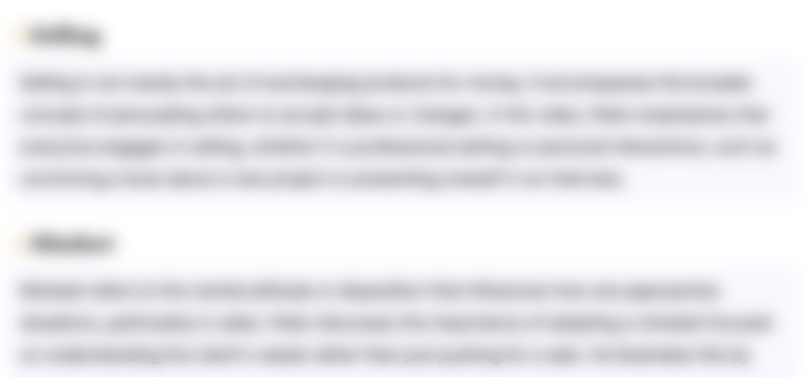
此内容仅限付费用户访问。 请升级后访问。
立即升级Highlights
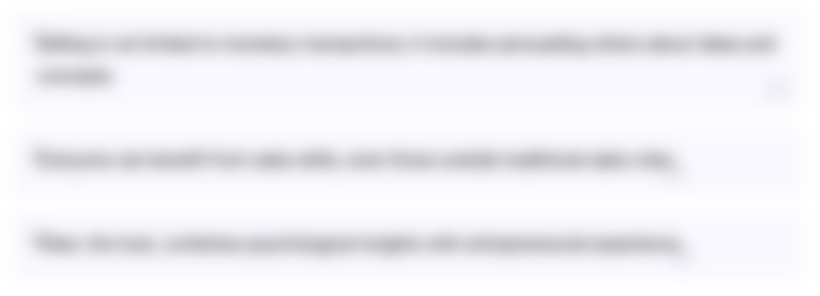
此内容仅限付费用户访问。 请升级后访问。
立即升级Transcripts
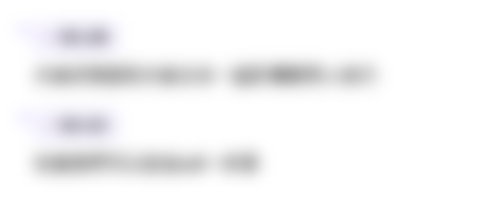
此内容仅限付费用户访问。 请升级后访问。
立即升级5.0 / 5 (0 votes)