14 Sistem Biaya Job Order dan Process Cost
Summary
TLDRThis video script discusses two key costing methods in management accounting: Job Order Costing and Process Costing. Job Order Costing is used for custom, unique orders, where each product or service is tailored to a specific customer request, with costs tracked by individual jobs. In contrast, Process Costing is applied in industries producing homogeneous goods in bulk, with costs accumulated by process or department over a set period. The video highlights the differences in product variety, cost accumulation, and cost calculation methods between these two systems, offering clear examples from industries like manufacturing and construction.
Takeaways
- 😀 Job Order Costing (JOC) is a cost calculation system based on customer orders, where products or services are unique to each customer order.
- 😀 In Job Order Costing, each job or order uses different resources, and the cost is accumulated for each individual order, not periodically.
- 😀 A typical example of Job Order Costing includes custom machines ordered by clients or construction projects managed by contractors.
- 😀 Process Costing, on the other hand, is used for mass production of identical products and is continuous, without the need for specific customer orders.
- 😀 In Process Costing, costs are accumulated based on processes or departments, and the cost per unit is calculated periodically (e.g., monthly or yearly).
- 😀 Examples of companies using Process Costing include large manufacturers like Indofood, Unilever, cement plants, and chemical companies.
- 😀 The key distinction between Job Order and Process Costing is that Job Order focuses on unique, customer-specific orders, while Process Costing focuses on mass production of similar products.
- 😀 In Job Order Costing, the cost per unit is determined by dividing the total cost of a job by the number of units produced in that specific job.
- 😀 In Process Costing, the cost per unit is calculated by dividing the total process cost for a department by the number of units produced during a given period.
- 😀 Job Order Costing provides reports on production costs only after the completion of a job, whereas Process Costing allows for periodic cost calculations (e.g., weekly, monthly).
- 😀 The choice between Job Order Costing and Process Costing depends on the nature of production—Job Order is used for customized, diverse products, while Process Costing is used for homogenous mass-produced goods.
Q & A
What is job order costing and how is it used?
-Job order costing is a method used to calculate the costs of producing products or providing services based on specific customer orders. It is typically used when products are unique and vary according to customer specifications. Costs are tracked and accumulated for each individual order or job.
What are the main characteristics of job order costing?
-The main characteristics of job order costing include: production of unique, customer-specific products; costs accumulated for each individual job or order; the product is usually a single unit; and reports are generated after the completion of each job.
Can you provide an example of a company that would use job order costing?
-Examples of companies that use job order costing include those producing custom machinery (e.g., Hitachi) or companies managing construction projects (e.g., contractors) or advertising firms producing ads based on specific client requests.
What is process costing and when is it used?
-Process costing is a costing method used for mass production of similar products, typically produced in large quantities or continuously. It is ideal for industries where products are homogeneous and production happens without waiting for customer orders.
What are the key characteristics of process costing?
-Key characteristics of process costing include: continuous or mass production of similar products; costs accumulated by department or process rather than individual jobs; and periodic cost calculations (e.g., monthly, annually).
Give examples of industries or companies that use process costing.
-Industries that use process costing include food manufacturing (e.g., Indofood), chemical manufacturing, cement production, and petroleum companies. These industries produce large quantities of homogeneous products.
How is cost calculated in job order costing?
-In job order costing, the total cost of a specific job or order is calculated by summing up all the costs (materials, labor, and overhead) associated with that particular order. The cost per unit is then calculated by dividing the total cost of the job by the number of units produced.
How is cost calculated in process costing?
-In process costing, the total cost is accumulated by each department or process. The cost per unit is calculated by dividing the total cost of a particular department or process by the total units produced in that process over a set period (e.g., monthly).
What is the difference in how costs are accumulated in job order costing vs. process costing?
-In job order costing, costs are accumulated for each specific job or order. In process costing, costs are accumulated by department or process, reflecting the continuous and mass production of products.
What is the main difference in the type of products produced under job order costing versus process costing?
-The main difference lies in the product type: job order costing is used for producing diverse, customer-specific products, whereas process costing is used for producing homogeneous products in large quantities.
Outlines
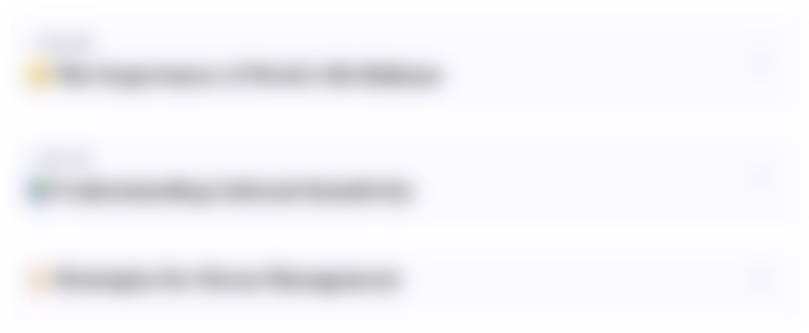
This section is available to paid users only. Please upgrade to access this part.
Upgrade NowMindmap
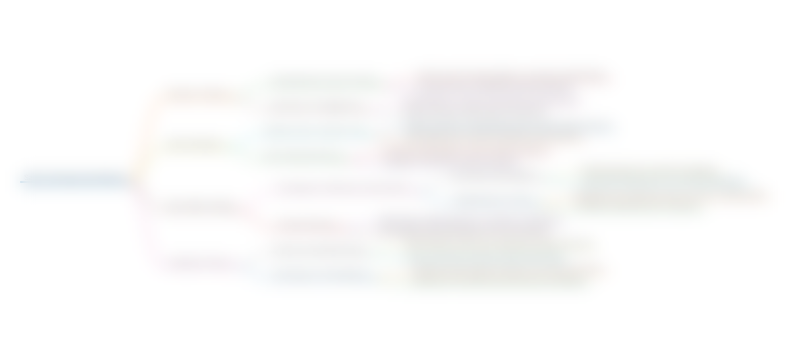
This section is available to paid users only. Please upgrade to access this part.
Upgrade NowKeywords
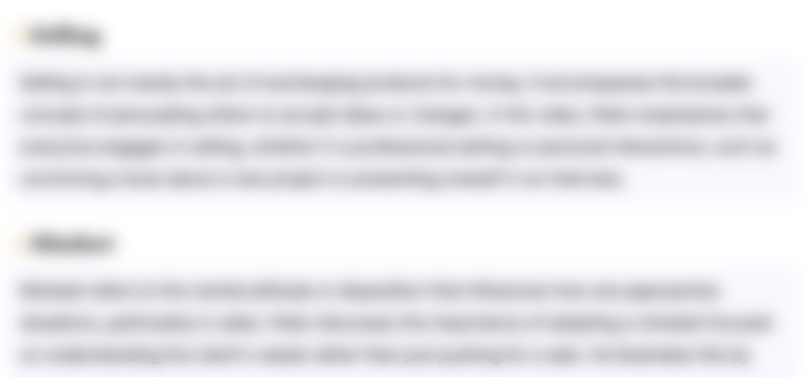
This section is available to paid users only. Please upgrade to access this part.
Upgrade NowHighlights
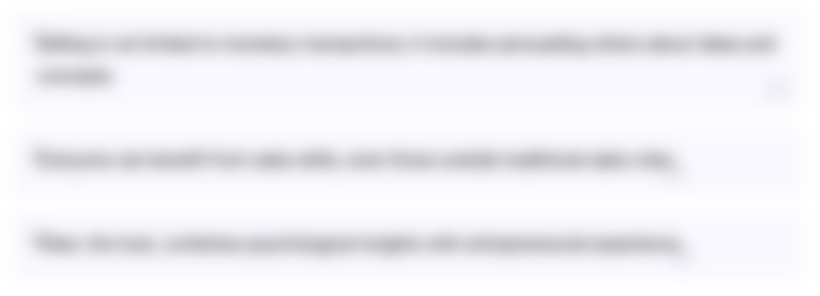
This section is available to paid users only. Please upgrade to access this part.
Upgrade NowTranscripts
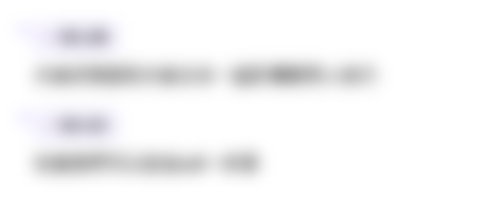
This section is available to paid users only. Please upgrade to access this part.
Upgrade NowBrowse More Related Video
5.0 / 5 (0 votes)