Akuntansi Biaya Bab 5 Job Order Costing
Summary
TLDRThis educational video introduces the concept of job order costing in cost accounting. It explores how costs for specific customer orders are accumulated, with a focus on direct materials, direct labor, and factory overhead. The video also explains how companies in manufacturing and service sectors can apply job order costing, using examples and practical applications. Key aspects include creating job order cost sheets, estimating overhead, and making necessary journal entries. By the end of the video, viewers should understand how to calculate production costs, track expenses, and prepare cost sheets for job orders.
Takeaways
- π Job Order Costing is a method of accumulating production costs based on specific customer orders or jobs, as discussed in the video.
- π The video emphasizes the difference between cost and expense, as well as the concept of fixed, variable, and semi-variable costs.
- π A key focus of the chapter is learning how to calculate the cost of goods produced under a job order costing system.
- π The traditional job order costing system involves accumulating direct materials, direct labor, and factory overhead for each job.
- π The video explains how to fill out a job order cost sheet (or 'Kartu Biaya'), which records details such as the job number, customer, product specifications, and various costs associated with the job.
- π Overhead costs are predetermined based on estimated rates and are applied throughout the production process to each job.
- π The importance of differentiating between direct and indirect materials, as well as direct and indirect labor, is highlighted in the cost sheet.
- π The role of factory overhead in job order costing is explained, and the use of a predetermined overhead rate helps simplify cost calculation during production.
- π The video introduces several basic accounting journal entries needed for job order costing, including those for material purchases, labor costs, overhead, and job completion.
- π Job order costing is applicable not only in manufacturing companies but also in service industries, where labor and overhead costs are tracked per job, often based on hours worked.
- π The concept of overhead control accounts, which track actual versus applied overhead costs, is explained in detail to ensure accurate cost allocation across jobs.
Q & A
What is the main topic of Chapter 5 in the script?
-Chapter 5 focuses on 'Job Order Costing', which is a method of calculating the cost of manufacturing products based on customer orders. It is introduced as a traditional costing system for determining the cost of producing specific items for individual customers.
How is job order costing different from process costing?
-Job order costing is used when products are made based on specific customer orders and involves tracking costs for each individual job. Process costing, on the other hand, is used for products that are produced in a continuous process, such as in mass production, and tracks costs over a period of time instead of individual jobs.
What are the three main components included in job order costing?
-The three main components of job order costing are direct materials, direct labor, and factory overhead. Each job incurs costs in these three categories, and they are tracked separately for accurate cost calculation.
What is the purpose of a job order cost sheet (Joko Sit)?
-A job order cost sheet (Joko Sit) is used to track and accumulate the costs associated with a specific job order. It records the direct materials used, labor hours worked, and factory overhead costs for each job, helping to determine the total cost of production for that order.
How are factory overhead costs allocated in job order costing?
-Factory overhead costs are allocated using a predetermined overhead rate, which is established in advance. This rate is based on expected total overhead costs divided by an estimated activity base, such as labor hours or machine hours, for the period.
What is a predetermined overhead rate, and why is it important?
-A predetermined overhead rate is a rate used to allocate factory overhead costs to jobs based on an estimated activity base, such as labor hours or machine hours. It is important because it allows for timely cost allocation and helps companies avoid waiting for actual overhead costs to be recorded.
How is the total cost of a job determined in job order costing?
-The total cost of a job in job order costing is determined by adding together the costs of direct materials, direct labor, and factory overhead. These costs are tracked on the job order cost sheet, and once all components are recorded, the total job cost can be calculated.
What kind of companies typically use job order costing?
-Job order costing is typically used by companies that produce customized products based on customer orders. This includes manufacturing companies that make unique products or service-based companies, such as construction or legal firms, where costs are tracked per job or contract.
What is the significance of separating direct and indirect materials in job order costing?
-Separating direct and indirect materials is significant in job order costing because direct materials are directly traceable to a specific job and are charged to that job. Indirect materials, on the other hand, are not directly traceable to a specific job and are charged to factory overhead.
Can job order costing be used in service companies, and if so, how?
-Yes, job order costing can be used in service companies, especially those that offer customized services like law firms or consulting agencies. In these cases, the job order cost sheet would track costs like labor hours, overhead, and any other direct costs associated with serving a specific client or contract.
Outlines
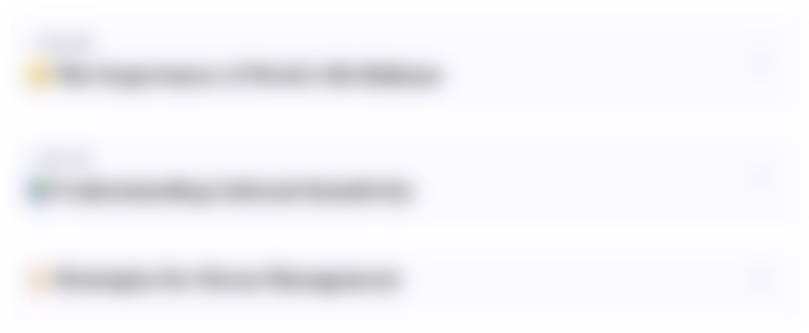
This section is available to paid users only. Please upgrade to access this part.
Upgrade NowMindmap
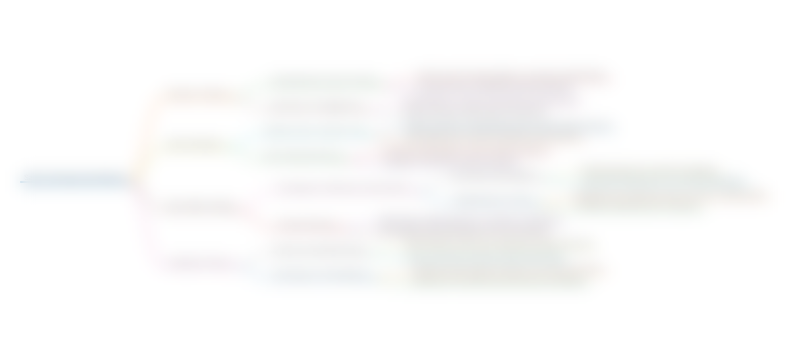
This section is available to paid users only. Please upgrade to access this part.
Upgrade NowKeywords
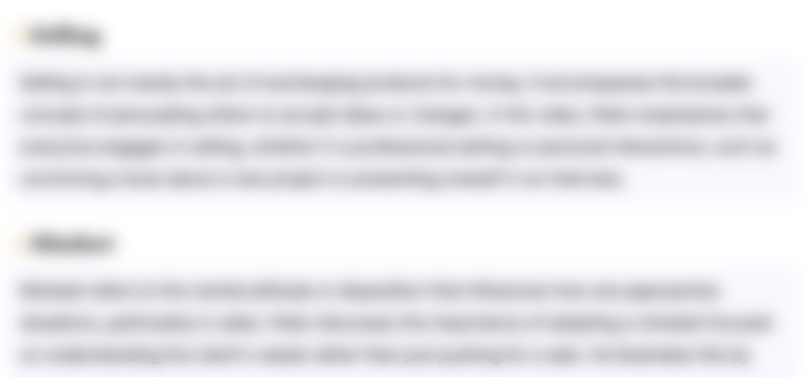
This section is available to paid users only. Please upgrade to access this part.
Upgrade NowHighlights
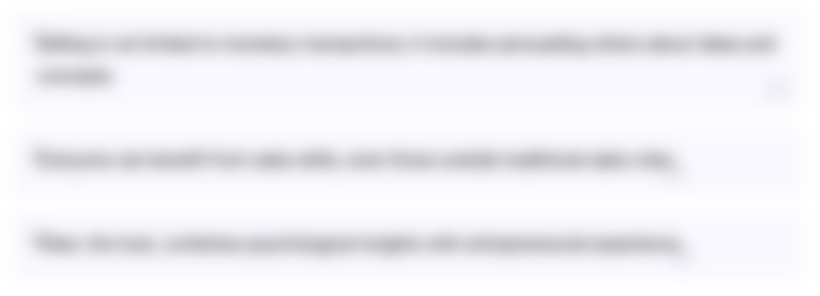
This section is available to paid users only. Please upgrade to access this part.
Upgrade NowTranscripts
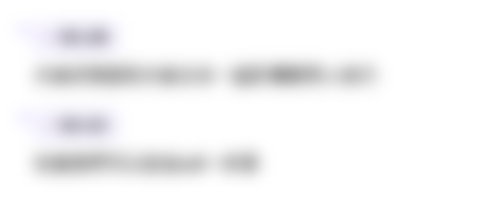
This section is available to paid users only. Please upgrade to access this part.
Upgrade NowBrowse More Related Video
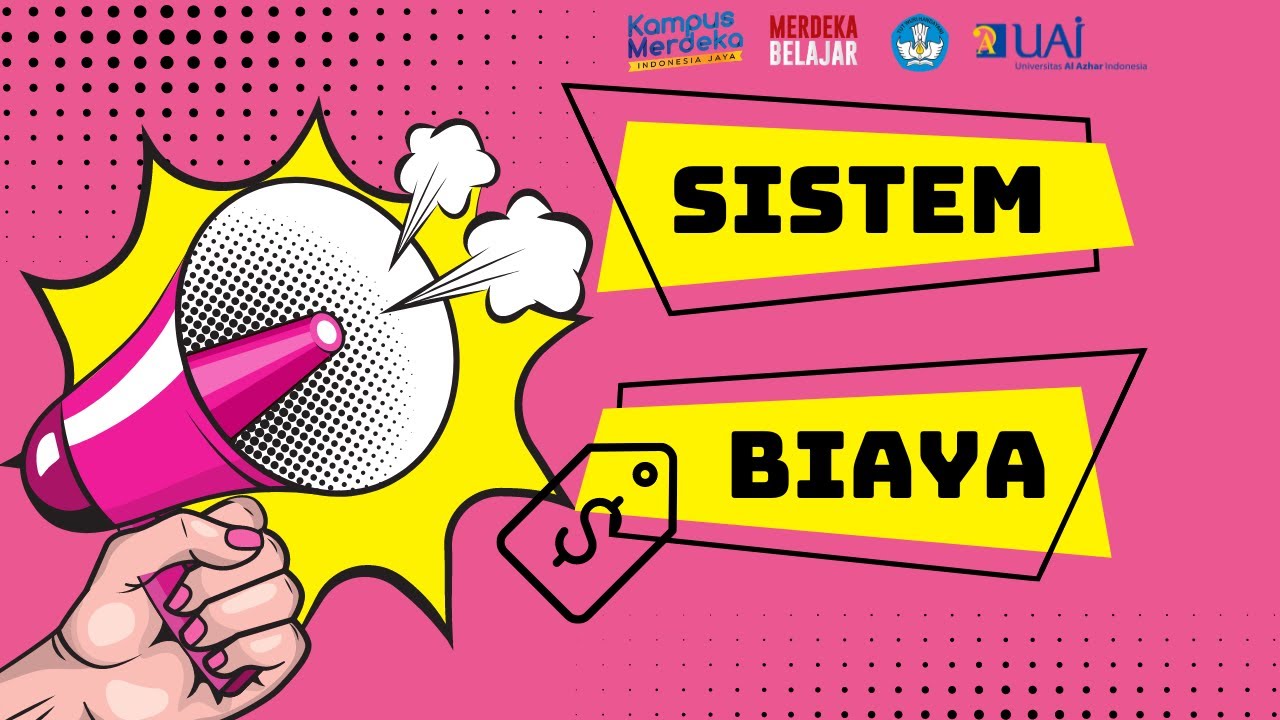
14 Sistem Biaya Job Order dan Process Cost
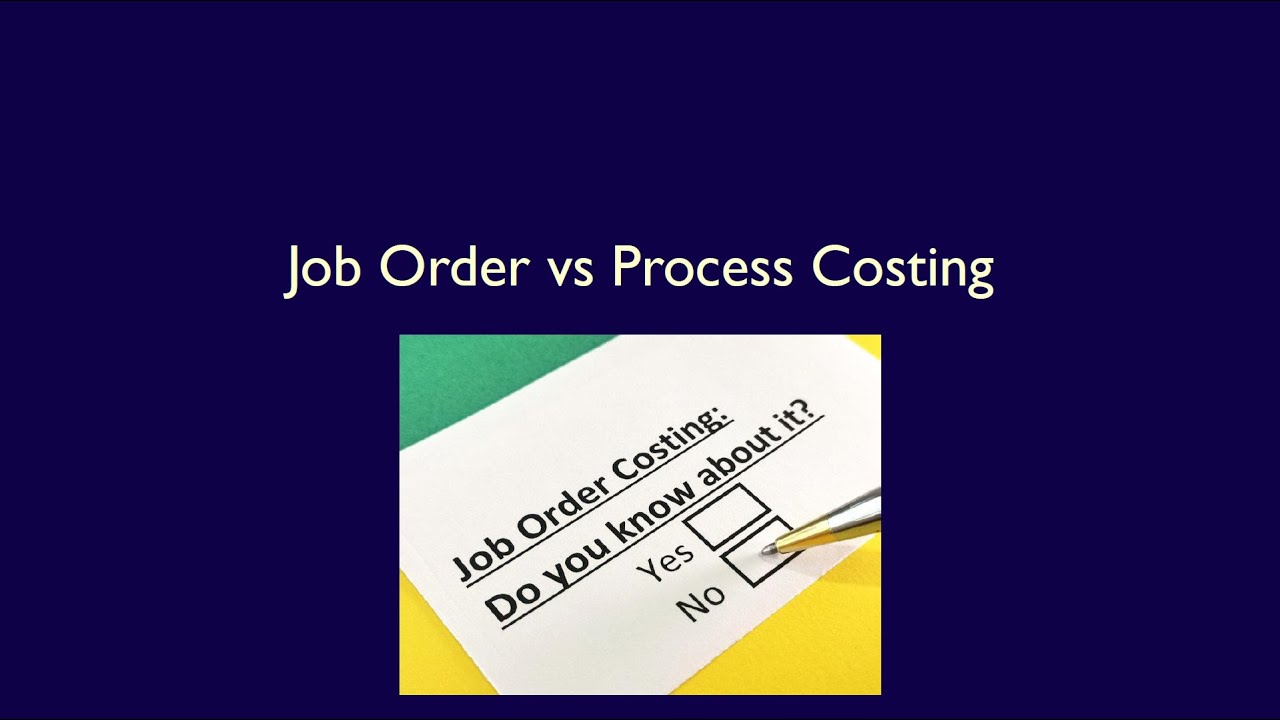
Module 5, Video 1: Job vs Process Costing Explained

Job Order Costing
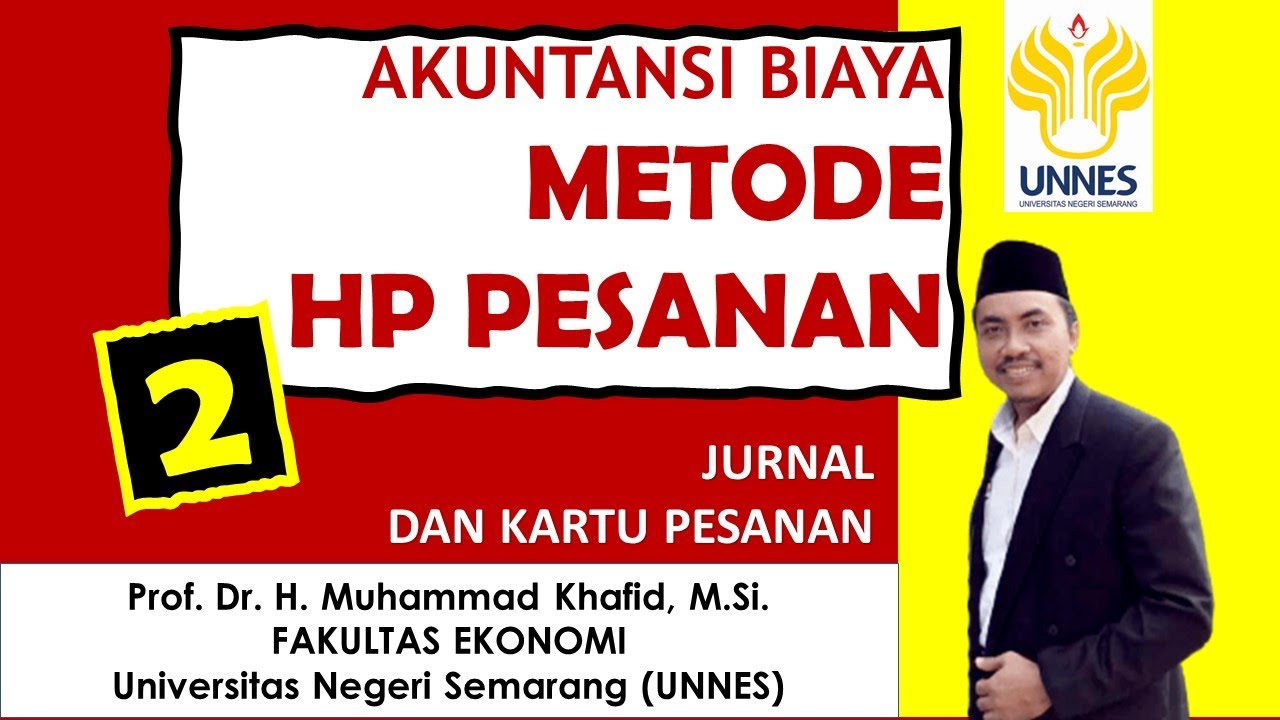
METODE HARGA POKOK PESANAN 2 : JURNAL DAN KARTU PESANAN
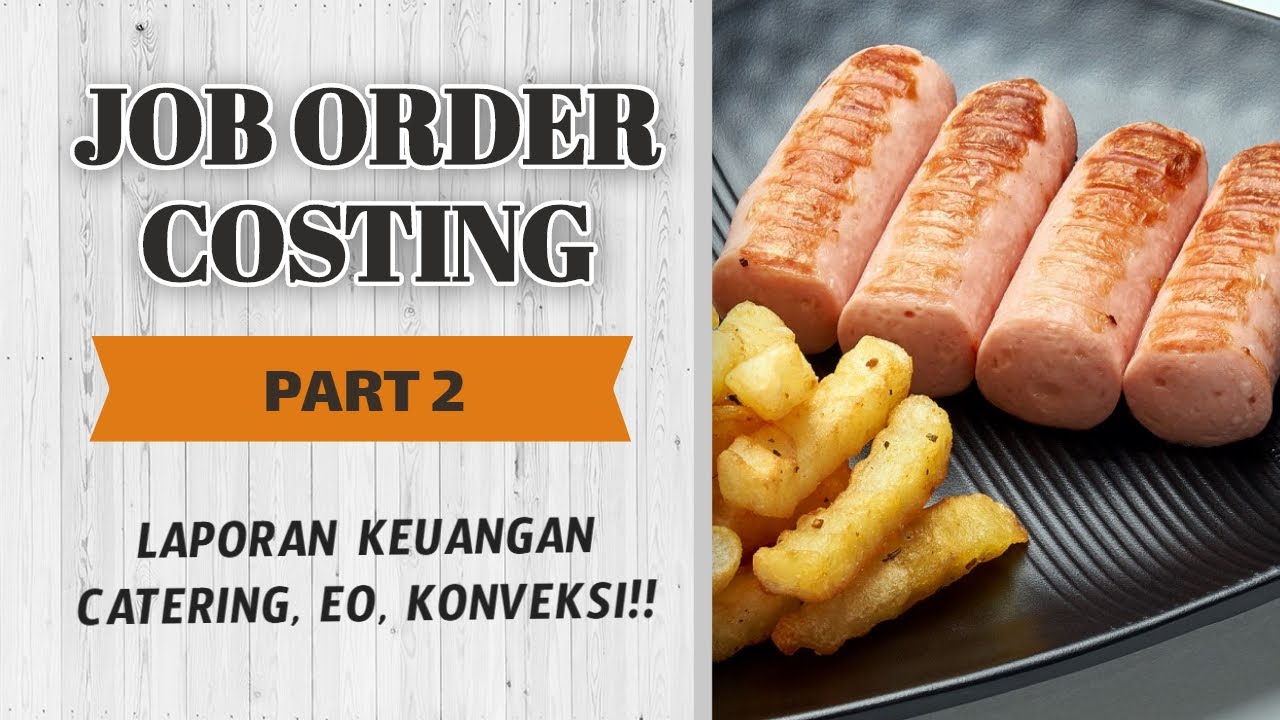
Job Order Costing [PART 2] - Laporan ala Cost Accounting, bisa untuk Catering atau Konveksi lho...

Harga Pokok Pesanan dengan Variabel Costing
5.0 / 5 (0 votes)