Job Order Costing - FEB UHAMKA
Summary
TLDRThis presentation from the University of Muhammadiyah Prof. Dr. Hamka's Faculty of Economics and Business focuses on Job Order Costing, a method used to calculate costs for manufacturing jobs. The presenters, Siska Aprilia and Alfian Rizki, explain the key components of Job Order Costing, such as direct materials, direct labor, and factory overhead, and provide a detailed example of how to calculate and allocate costs. They also cover journal entries related to Job Order Costing and discuss its application in both manufacturing and service industries, including an example from PT Semesta Raya.
Takeaways
- 😀 Job Order Costing (JOC) is a method used to accumulate production costs for custom orders or jobs based on individual customer specifications.
- 😀 Job Order Costing involves tracking direct materials, direct labor, and factory overhead for each job or order.
- 😀 Direct materials and direct labor are allocated directly to each job, while factory overhead is applied using a predetermined rate based on machine hours or labor hours.
- 😀 The process includes the creation of job cost sheets to track materials, labor, and overhead for each specific job or order.
- 😀 The accounting for job order costing includes several key journal entries, such as purchasing raw materials, allocating labor costs, and applying factory overhead.
- 😀 In job order costing, materials used in production are categorized into direct and indirect materials, with direct materials allocated to work in process (WIP) and indirect materials to factory overhead.
- 😀 Labor costs are divided into direct labor (charged to WIP) and indirect labor (charged to factory overhead).
- 😀 Factory overhead control is used to track the actual costs incurred for overhead, which are then applied to jobs based on a predetermined rate.
- 😀 The journal entries for finished goods include transferring the costs from WIP to finished goods and later recording the sale when the product is shipped to customers.
- 😀 In a manufacturing business, job order costing is used to calculate the cost of production for each job, including materials, labor, and overhead. The final cost is often marked up by a percentage for profit calculation.
Q & A
What is Job Order Costing (JOC)?
-Job Order Costing is a method of cost accumulation used to determine the cost of production for a specific order or job. It involves tracking direct materials, direct labor, and factory overhead for each job or customer order.
What is the primary purpose of Job Order Costing?
-The main purpose of Job Order Costing is to accurately track and assign costs to specific customer orders or jobs to determine the total cost of producing a product or service based on its unique specifications.
What types of costs are accumulated in Job Order Costing?
-Job Order Costing accumulates three main types of costs: direct materials, direct labor, and factory overhead. These are tracked individually for each job.
How does Job Order Costing work in relation to production jobs?
-In Job Order Costing, each job is treated as a separate cost unit. The costs associated with materials, labor, and overhead are accumulated specifically for that job, ensuring accurate cost allocation.
What is the purpose of the 'Cost Sheet' in Job Order Costing?
-The cost sheet, also known as the job order cost sheet, is a detailed record that includes all relevant information about a specific order, such as customer details, order specifications, and the costs of direct materials, labor, and overhead associated with the job.
What is the significance of Factory Overhead in Job Order Costing?
-Factory Overhead represents the indirect costs associated with production, such as depreciation, utilities, and factory supplies. In Job Order Costing, overhead is applied to each job based on a predetermined rate, usually related to machine hours or labor hours.
How are overhead costs applied in Job Order Costing?
-Overhead costs are applied to jobs based on a predetermined overhead rate, which is often calculated using a standard such as machine hours or labor hours. The applied overhead is then allocated to each job based on its usage of these resources.
Can Job Order Costing be used in service businesses?
-Yes, Job Order Costing can be used in service businesses. For service-based jobs, direct labor and related overhead costs are the primary components, as there are typically no physical materials involved.
What journal entries are involved in Job Order Costing?
-Job Order Costing involves several journal entries, such as: purchasing raw materials, recording labor costs, applying factory overhead, allocating costs to jobs, and recognizing completed jobs as finished goods or cost of goods sold when sold.
What happens when factory overhead is over-applied or under-applied in Job Order Costing?
-When factory overhead is over-applied, it means that more overhead was allocated to jobs than was actually incurred. This excess is typically transferred to the cost of goods sold. Conversely, under-applied overhead means that insufficient overhead was allocated, and adjustments are made accordingly.
Outlines
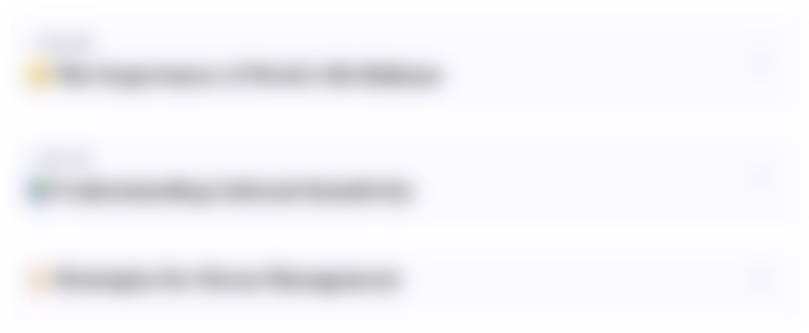
This section is available to paid users only. Please upgrade to access this part.
Upgrade NowMindmap
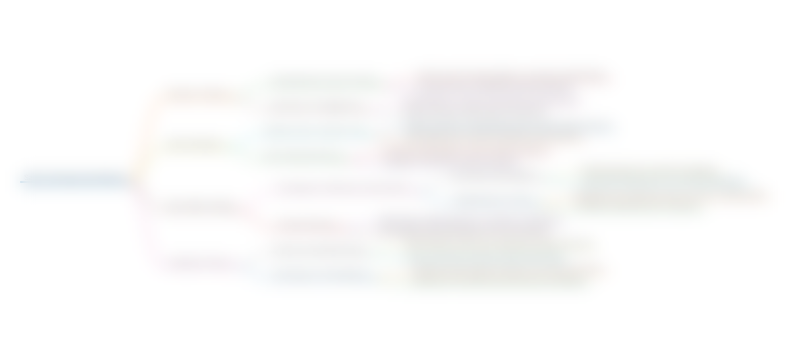
This section is available to paid users only. Please upgrade to access this part.
Upgrade NowKeywords
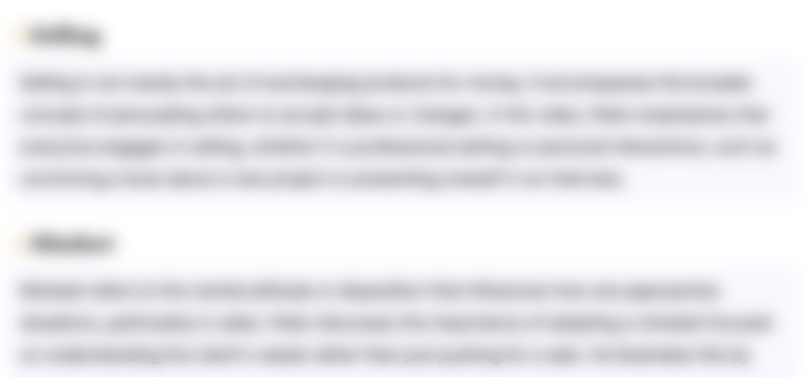
This section is available to paid users only. Please upgrade to access this part.
Upgrade NowHighlights
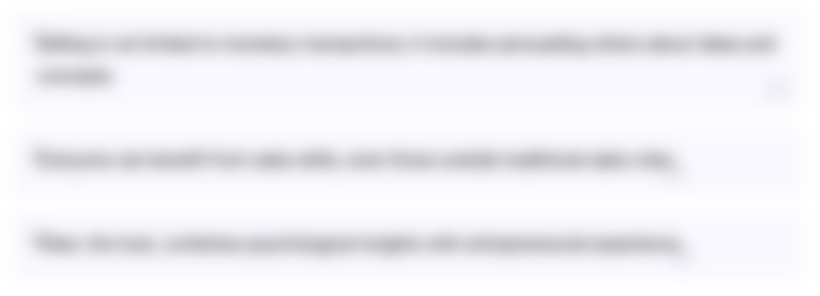
This section is available to paid users only. Please upgrade to access this part.
Upgrade NowTranscripts
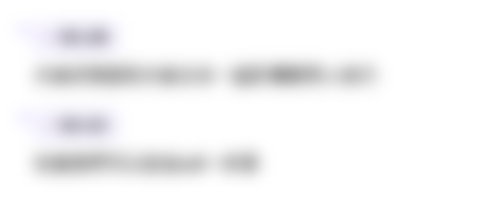
This section is available to paid users only. Please upgrade to access this part.
Upgrade NowBrowse More Related Video

AIK I Materi ke 14_Tarjih Sebagai Metode Ijtihad Muhammadiyah
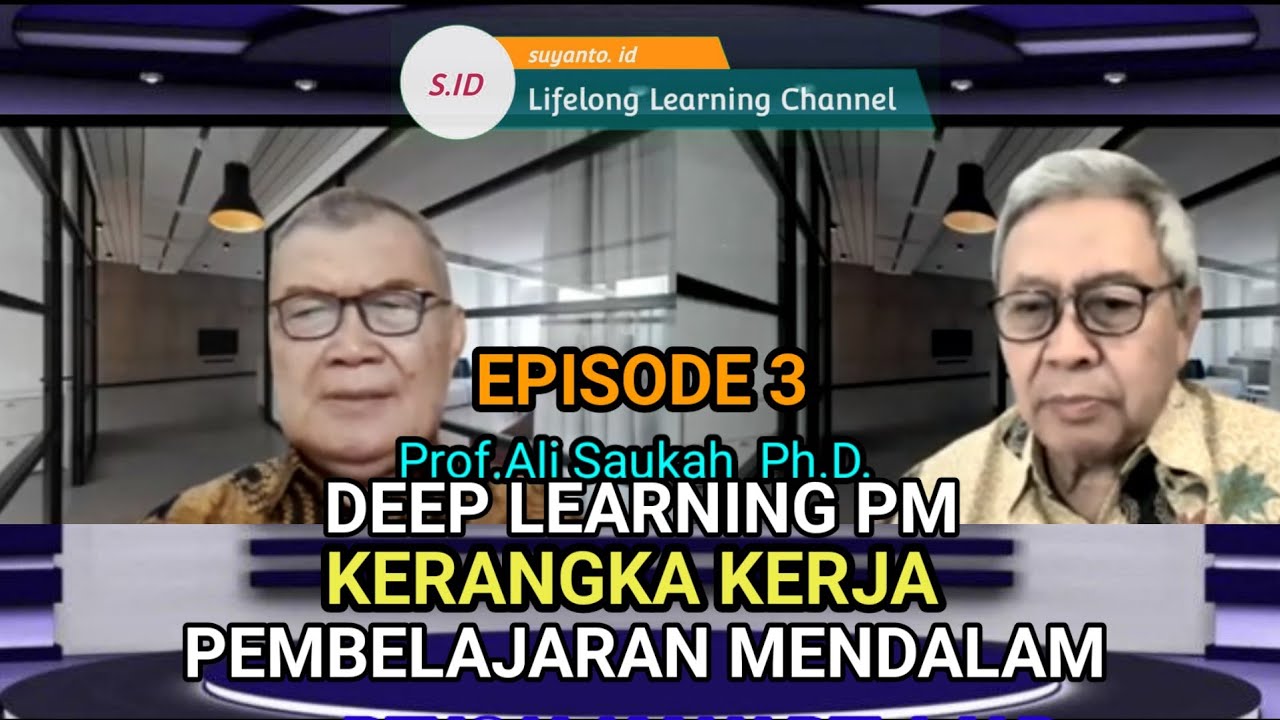
Prof. Ali Saukah: Kemitraan Guru dgn Guru dalam PM English-Eps.3 @Suyantoid
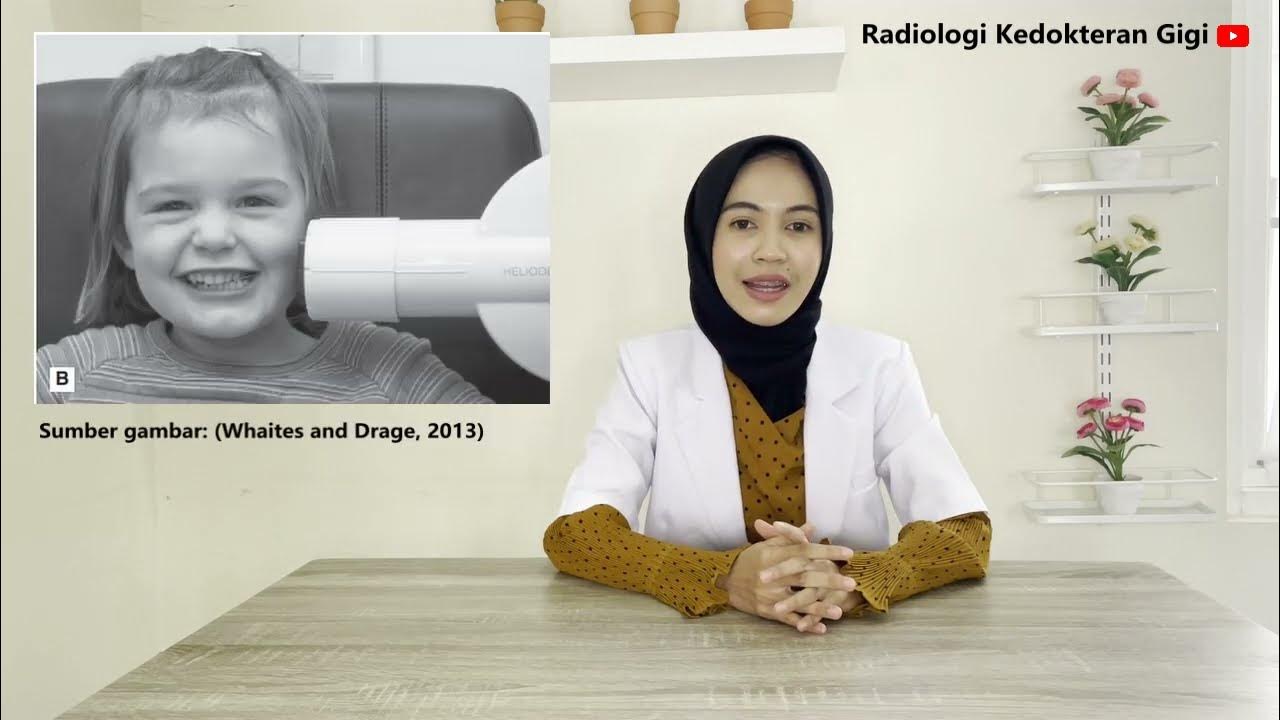
Mengenal Teknik Radiografi Intra Oral Bitewing

Alat Peraga Papan Jalan SIBILABUL (Operasi Bilangan Bulat) Kls 4 SD Pendidikan Matematika Realistik
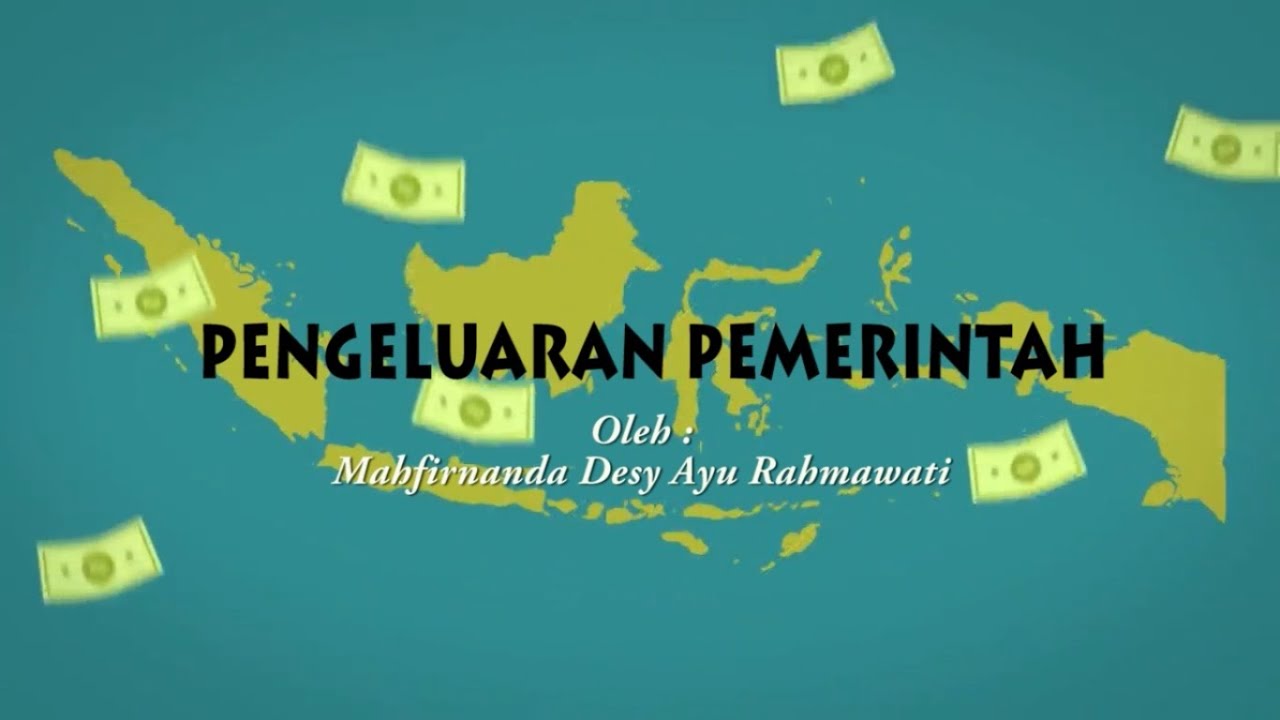
PENGELUARAN PEMERINTAH - Ekonomi Publik #EPUMM #materipembelajaran

Prof. Dr. İsmet BAŞER - Haploit Bitki Üretimi
5.0 / 5 (0 votes)