All Lathe Machine Operations: Turning, Facing, Taper Turning, Boring, Knurling, Tapping, Forming
Summary
TLDRThis video provides an in-depth look at various lathe machine operations, such as plain turning, taper turning, thread cutting, grooving, knurling, and more. It covers the key processes used to shape and finish cylindrical and conical workpieces, including rough and fine turning, chamfering, filing, and polishing. Additionally, the video explains specialized operations like drilling, boring, tapping, and undercutting, along with the use of attachments for milling and grinding. Each operation is explained with its purpose, process, and the tools involved, offering a comprehensive guide for both beginners and professionals in machining.
Takeaways
- 😀 Facing is a lathe operation that reduces the length of a workpiece by feeding the tool perpendicular to the lathe axis. It involves both roughing and finishing stages with specific depths of cut.
- 😀 Plain turning removes excess material to produce a cylindrical surface, and rough turning uses high feed rates and deep cuts for fast material removal.
- 😀 Taper turning creates a conical shape by gradually reducing the diameter of the workpiece, essential for producing conical components.
- 😀 Knurling is a process that imprints a diamond-shaped texture on a workpiece for better gripping, typically done at low speeds with a knurling tool.
- 😀 Thread cutting is used to create external or internal helical grooves, and the direction of the tool movement determines the type of thread (left or right-hand).
- 😀 Grooving reduces the diameter of a workpiece at specific points, often using a specialized groove tool similar to a parting-off tool.
- 😀 Polishing and filing are finishing operations performed after turning to remove burrs and improve the workpiece’s surface quality.
- 😀 Drilling is performed by rotating a tool to create cylindrical holes in the workpiece, typically mounted in a chuck or faceplate.
- 😀 Reaming is used for finishing and sizing drilled holes, providing a smooth, accurate inner surface with a reamer tool.
- 😀 Milling and grinding are additional lathe machine operations that use rotating cutters and abrasive wheels to remove material and finish workpieces, often with special attachments.
Q & A
What is the purpose of turning in lathe machine operations?
-Turning is the operation of removing excess material from a workpiece to produce a cylindrical surface to the desired length. The workpiece is rotated, and the tool moves in a longitudinal direction to provide feed and remove material.
How does rough turning differ from plain turning?
-In rough turning, the focus is on removing excess material quickly with higher feed rates and larger depths of cut (2mm to 4mm) compared to plain turning, which produces a smooth cylindrical surface with lighter cuts.
What is shoulder turning, and when is it used?
-Shoulder turning is the process of machining the area between two diameters on a workpiece, creating a shoulder. It is used when the workpiece has different diameters and needs to be turned from one diameter to another.
Explain the process and purpose of chamfering in lathe operations.
-Chamfering is the operation of beveling the edges of a cylindrical workpiece to prevent damage to sharp edges and facilitate easier assembly, especially for bolts and shafts.
What is the difference between external and internal thread cutting?
-External thread cutting forms threads on the outer surface of the workpiece, while internal thread cutting creates threads on the inner surface. Both operations are done by moving the tool longitudinally while the workpiece rotates.
Why is knurling performed, and what type of tool is used?
-Knurling is done to create a diamond-shaped pattern on a workpiece to improve grip, especially on handles or gauges. It is performed using a knurling tool, which consists of a set of hardened steel rollers.
What are the key differences between filing and polishing operations?
-Filing is a finishing operation performed to remove burrs, sharp corners, and feed marks, often using a flat single-cut file. Polishing follows filing and improves the surface quality of the workpiece, usually with finer abrasives or polishing compounds.
How does the taper turning process work, and what is its purpose?
-Taper turning is used to create a conical shape by gradually reducing the diameter of a cylindrical workpiece. It is often employed when a workpiece needs to have a tapered end or intermediate section.
What is the function of the drilling operation in lathe machining?
-Drilling is the operation of producing cylindrical holes in a workpiece. The drill rotates while the workpiece is held stationary, typically in a chuck or faceplate, and the depth of the hole is controlled by the movement of the tailstock spindle.
What are the benefits of using a grinding operation in lathe machining?
-Grinding removes small amounts of material using an abrasive wheel to finish or size a workpiece. It is particularly useful for improving surface quality, sharpening tools, or achieving precise dimensions on hardened materials.
Outlines
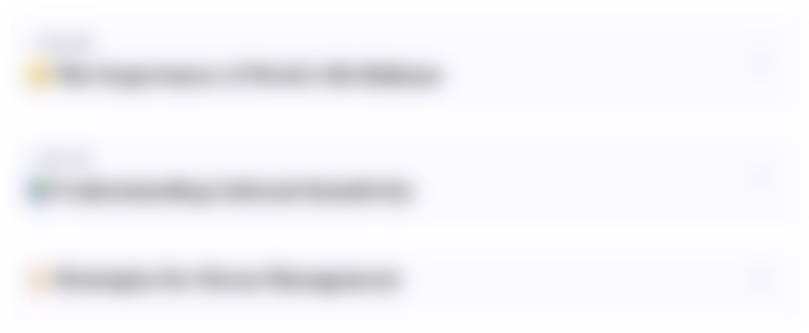
此内容仅限付费用户访问。 请升级后访问。
立即升级Mindmap
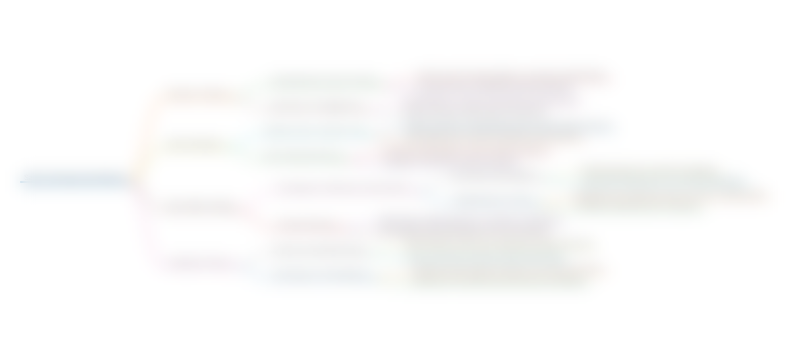
此内容仅限付费用户访问。 请升级后访问。
立即升级Keywords
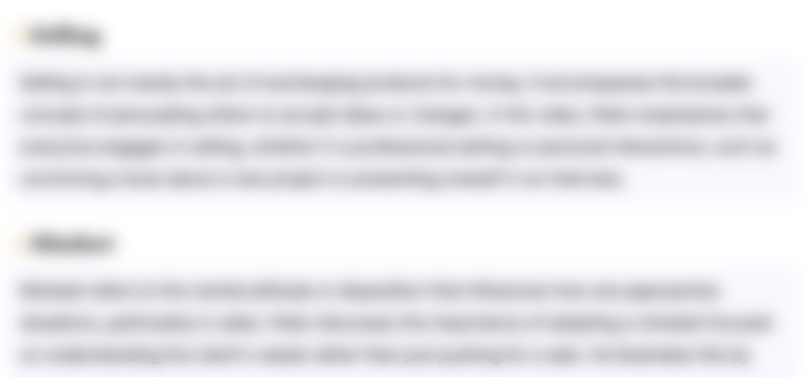
此内容仅限付费用户访问。 请升级后访问。
立即升级Highlights
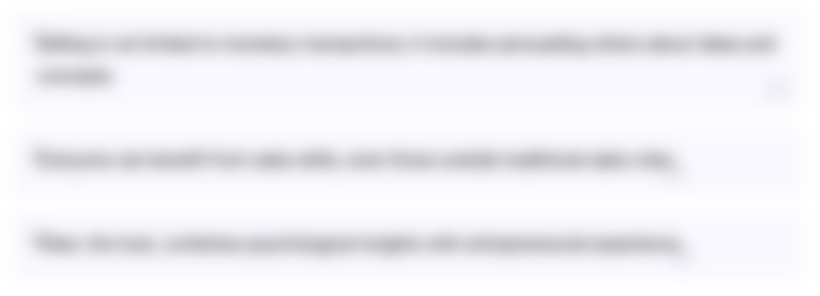
此内容仅限付费用户访问。 请升级后访问。
立即升级Transcripts
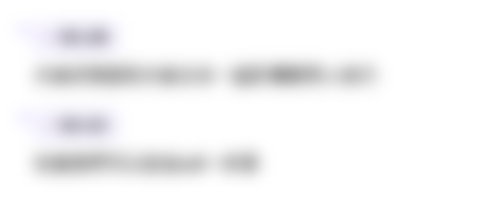
此内容仅限付费用户访问。 请升级后访问。
立即升级5.0 / 5 (0 votes)