CNC Lathe Basics: How CNC Lathe Turning Works
Summary
TLDRIn this video, the process of CNC turning is explored, a key machining method used to create cylindrical parts with precision. The video covers various turning operations like straight turning, knurling, taper turning, threading, grooving, and drilling, and highlights their uses in industries. It also compares CNC turning with CNC milling, explaining their distinct applications. CNC turning is ideal for cylindrical parts such as shafts, pins, and bearings, while CNC milling is better for intricate details. The video ends with a call to action to explore Rapid Direct's CNC turning services for efficient and accurate part manufacturing.
Takeaways
- 😀 CNC turning is a machining process where a rotating workpiece is shaped by a stationary cutting tool.
- 😀 CNC stands for Computer Numerical Control, meaning the machine is operated through computer programming.
- 😀 Turning is primarily used for creating cylindrical or round parts, but it can also work with other shapes using specialized adapters.
- 😀 The six most common turning operations are straight turning, knurling, taper turning, threading, grooving, and drilling.
- 😀 Straight turning is the basic operation, used to create a uniform cylindrical surface, often seen in shafts, pins, and rods.
- 😀 Knurling adds textured patterns like diamond-shaped indentations to a cylindrical surface, improving grip for tools and machine parts.
- 😀 Taper turning gradually changes the diameter of a workpiece to create tapered shapes, useful for cones and wedges.
- 😀 Threading creates screw threads on cylindrical surfaces, essential for mechanical assemblies, with both internal and external threading.
- 😀 Grooving cuts narrow channels or grooves into the workpiece surface, useful for fluid flow or clearance for other components.
- 😀 Drilling in CNC turning involves creating holes in the workpiece, such as through holes, blind holes, or counterbores.
- 😀 CNC turning is ideal for cylindrical or rotational parts, while CNC milling is better for more complex shapes and features like slots and pockets.
Q & A
What is CNC turning?
-CNC turning is a machining process where a lathe machine rotates a workpiece while a cutting tool shapes it into the desired form. The CNC aspect means the process is controlled by a computer, with designs translated into machine-readable language.
What types of materials can be processed using CNC turning?
-CNC turning typically processes cylindrical or round materials, but with the use of compatible adapters, it can also work with materials of various shapes.
What is straight turning used for?
-Straight turning is used to create a straight, cylindrical surface along the length of a workpiece. It's essential for producing components like shafts, pins, and rods where a uniform diameter is required.
What is the purpose of knurling in CNC turning?
-Knurling adds texture or grip to a cylindrical surface by creating small diamond-shaped indentations. This is commonly seen in handles, knobs, or any surface where improved grip is necessary.
What is taper turning, and what is it used for?
-Taper turning involves gradually changing the diameter of a workpiece along its length to create a tapered shape. It’s used for making items like cones, wedges, or adding a slight taper to cylindrical parts for better fitting.
Why is threading important in CNC turning?
-Threading is crucial for creating screw threads on a cylindrical surface, enabling components like bolts and nuts to fasten securely. This operation is vital for many mechanical assemblies.
What is the purpose of grooving in CNC turning?
-Grooving involves cutting narrow channels or grooves into the surface of a workpiece. These grooves can be used for various purposes, such as fluid passage in machinery or creating clearance for other components.
How does drilling fit into CNC turning?
-Drilling in CNC turning involves making holes in the workpiece, whether through holes, blind holes, or counterbore and countersink holes. This is essential for creating openings and passages in cylindrical parts.
What is the key difference between CNC turning and CNC milling?
-In CNC turning, the workpiece rotates while the cutting tool remains stationary. In CNC milling, the cutting tool rotates and moves across the stationary workpiece. Turning is ideal for cylindrical parts, while milling is better for more complex shapes and features.
When should you choose CNC turning over CNC milling?
-CNC turning is ideal for creating cylindrical or rotational parts like shafts, pins, and cylindrical molds. It is also great for symmetrical parts due to the rotation ensuring uniformity. On the other hand, CNC milling is better for adding intricate details or features like pockets, holes, and slots.
Outlines
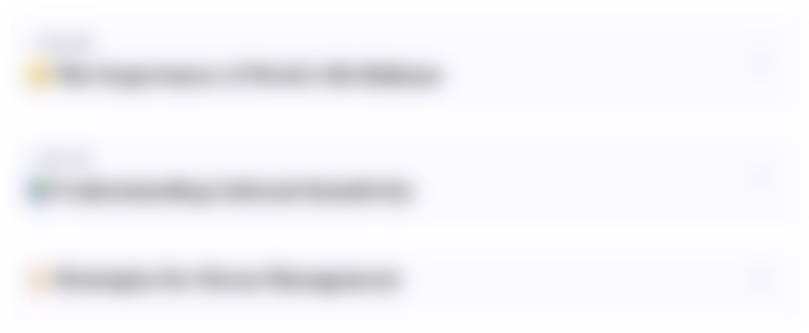
This section is available to paid users only. Please upgrade to access this part.
Upgrade NowMindmap
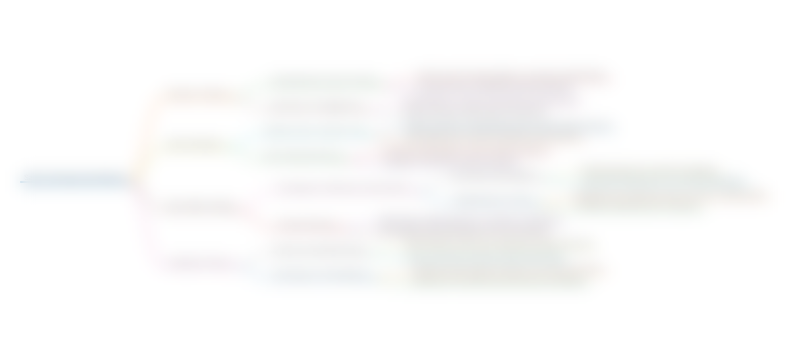
This section is available to paid users only. Please upgrade to access this part.
Upgrade NowKeywords
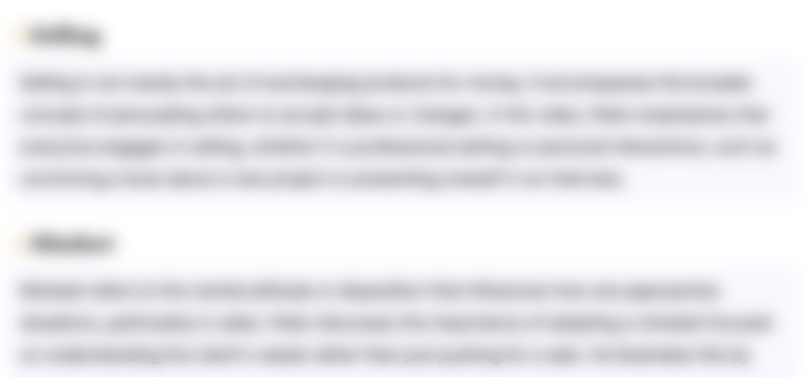
This section is available to paid users only. Please upgrade to access this part.
Upgrade NowHighlights
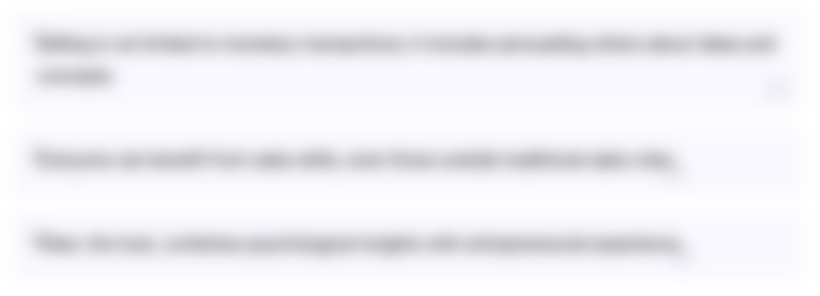
This section is available to paid users only. Please upgrade to access this part.
Upgrade NowTranscripts
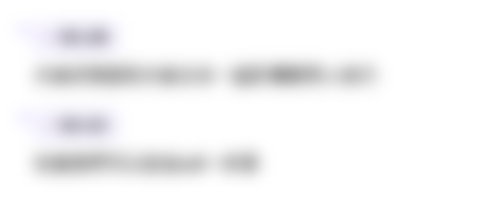
This section is available to paid users only. Please upgrade to access this part.
Upgrade NowBrowse More Related Video
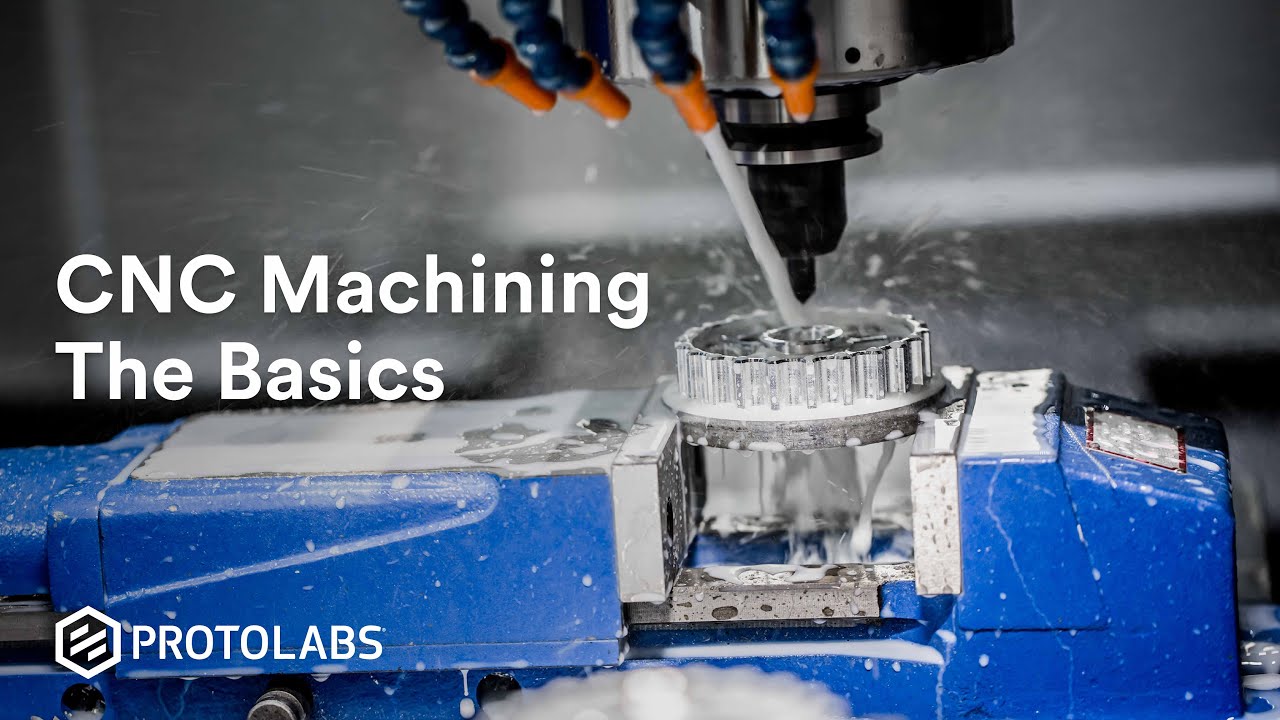
CNC machining - What is it and How Does it Work? (Must Know Basics)
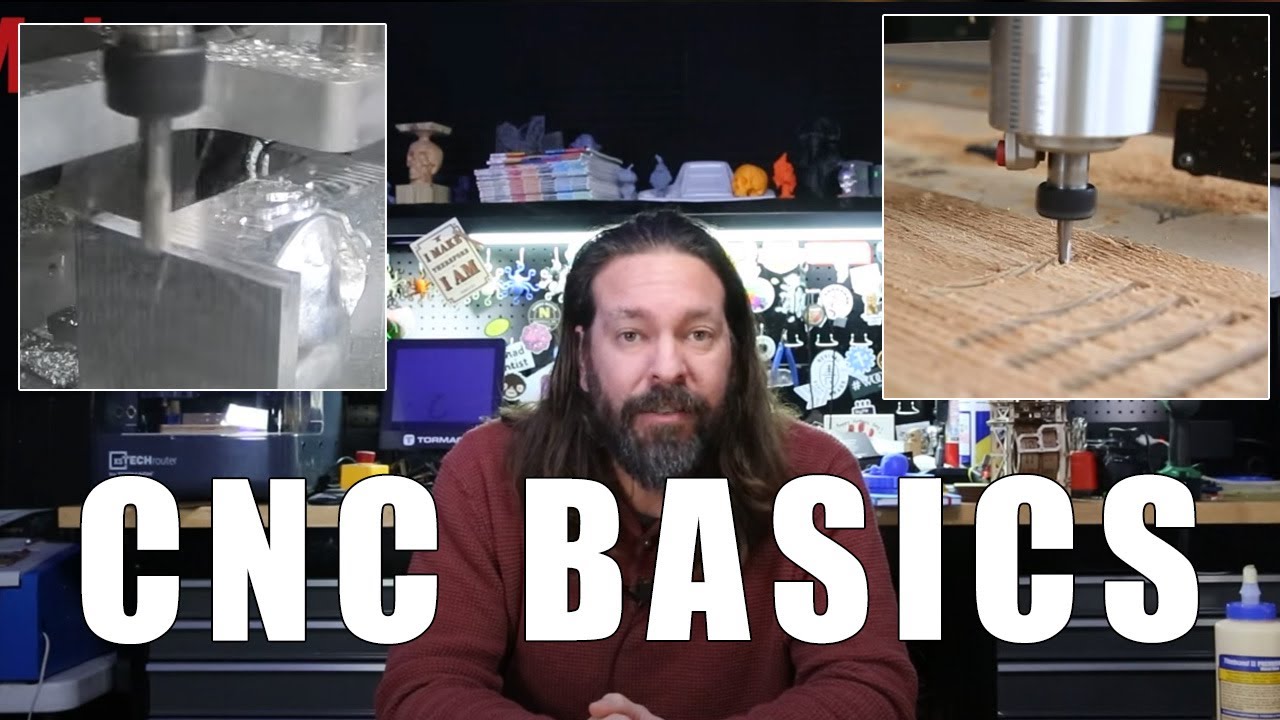
CNC Basics - Everything a Beginner Needs To Know
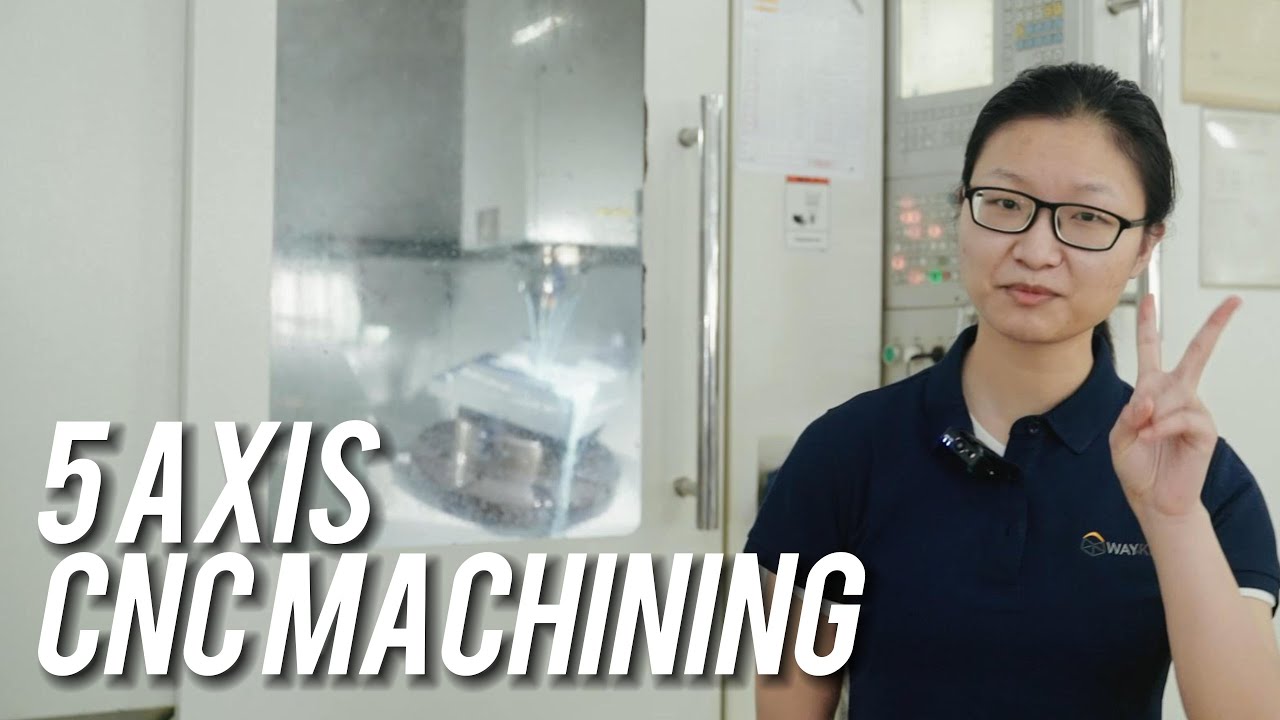
5 Axis CNC Machining For Your Parts | WayKen Rapid Manufacturing
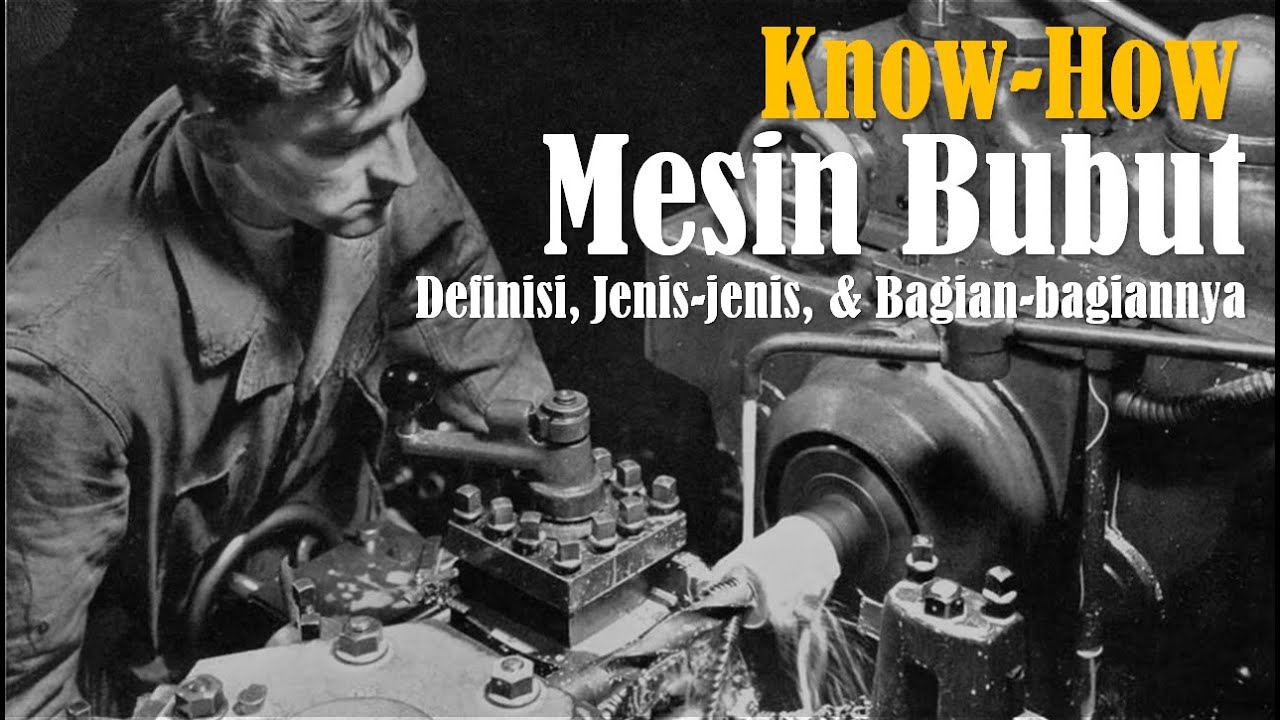
MESIN BUBUT - DEFINISI, CARA KERJA, JENIS-JENIS DAN BAGIAN-BAGIAN MESIN BUBUT
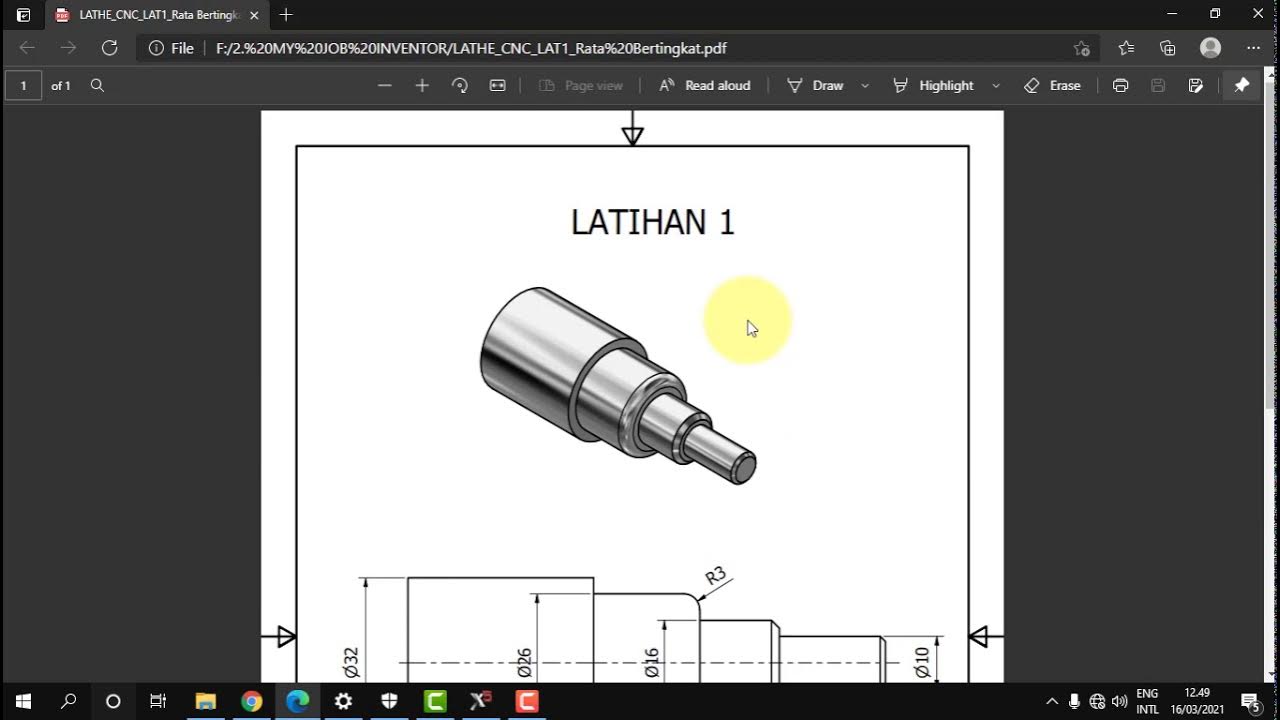
MASTERCAM X5_BUBUT DASAR BIDANG BERTINGKAT

All Lathe Machine Operations: Turning, Facing, Taper Turning, Boring, Knurling, Tapping, Forming
5.0 / 5 (0 votes)