setting benda kerja di mesin cnc milling GSK
Summary
TLDRThis video guides viewers through the step-by-step process of setting up a CNC machine, focusing on precise calibration of the X, Y, and Z axes. It covers the use of auxiliary tools like the Centrofix for accurate positioning, including how to set the machine’s zero point at the workpiece’s left corner. Viewers will learn how to adjust the spindle, set the machine’s coordinates, and ensure all axes are correctly aligned. The video also includes troubleshooting tips and emphasizes the importance of accurate setup for smooth and safe CNC operations.
Takeaways
- 😀 The Centrofix tool is essential for setting the X and Y axes of the CNC machine, ensuring the tool is centered and properly aligned.
- 😀 Setting the zero point for the workpiece is crucial, typically at the left bottom corner of the material, to ensure accurate machining operations.
- 😀 The machine's spindle speed should be controlled, with a maximum of 300 RPM for safety and optimal performance during tool setup.
- 😀 Manual adjustments are necessary to fine-tune the positioning of the tool, ensuring it aligns correctly with the workpiece.
- 😀 The CNC machine's X, Y, and Z axes need to be aligned with the workpiece's coordinates to ensure precision throughout the machining process.
- 😀 To set the Z-axis correctly, it's important to adjust the height of the tool relative to the workpiece, ensuring proper contact with the material.
- 😀 After setting the zero points, the next step is to verify the alignment of the X, Y, and Z axes using the CNC machine’s control panel.
- 😀 When setting the X and Y axes, the tool must be moved manually to avoid errors, and fine adjustments should be made for perfect alignment.
- 😀 During tool setup, careful attention should be given to ensure that all adjustments are done slowly and steadily, especially when using tools like Centrofix.
- 😀 Before running a machining program, the machine coordinates (X, Y, Z) and workpiece coordinates should be verified and matched to avoid errors during production.
Q & A
What is the purpose of the *Centrofix* tool in this CNC setup?
-The *Centrofix* tool is used for setting the X and Y axes of the CNC machine. It helps to align the machine's coordinate system with the workpiece to ensure accurate machining.
How do you set the X and Y axes in this process?
-To set the X and Y axes, first secure the *Centrofix* tool onto the machine arbor. Then, rotate the spindle to check the movement, set it to the proper speed (300 RPM), and move the machine to align the workpiece's lower-left corner with the machine's zero point.
Why is it important to set the spindle to 300 RPM during this process?
-Setting the spindle to 300 RPM ensures that the machine operates within safe limits. If the spindle speed is too high, it can lead to potential damage or inaccuracies in the setup.
What does the *M3* command do in this setup?
-*M3* is a command used to start the spindle's rotation in a clockwise direction. It is critical for initializing the spindle's operation during the CNC setup.
How do you calibrate the Z-axis on the CNC machine?
-The Z-axis is calibrated by lowering the tool until it touches the surface of the workpiece. Then, a 50mm offset is applied to adjust the zero point accurately for the machining process.
What is the purpose of using the *G54* work coordinate system?
-The *G54* work coordinate system is used to synchronize the machine's coordinates with the workpiece coordinates. It ensures that the machine's movements correspond accurately to the physical location of the workpiece.
How can you verify that the X, Y, and Z axes are correctly set?
-You can verify the settings by manually testing the movements of the machine along each axis and ensuring that the machine's coordinates match the desired zero points for the workpiece.
What steps are taken after setting the X, Y, and Z axes?
-After setting the axes, the system is calibrated by ensuring the coordinates match the workpiece's position. Then, the machine is reset, and safety checks are performed before the actual machining process begins.
Why is it important to adjust the spindle speed to 100% during the setup?
-Adjusting the spindle speed to 100% ensures that the spindle operates at its full intended speed, which is necessary for the accurate execution of the machining task.
What does pressing the *Zero* button do during the setup process?
-Pressing the *Zero* button sets the current position as the zero point for each axis. This ensures that the machine's movements and the tool's actions are aligned with the workpiece's exact location.
Outlines
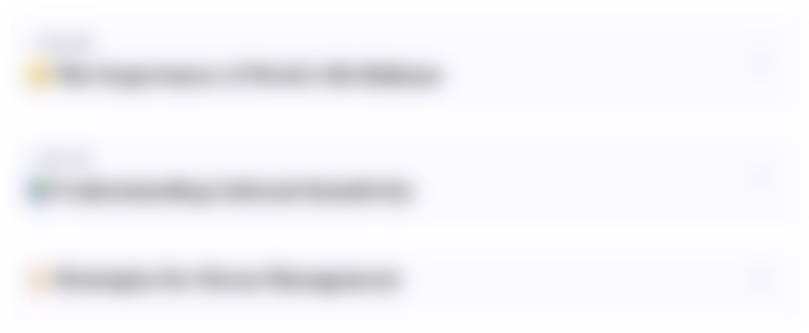
此内容仅限付费用户访问。 请升级后访问。
立即升级Mindmap
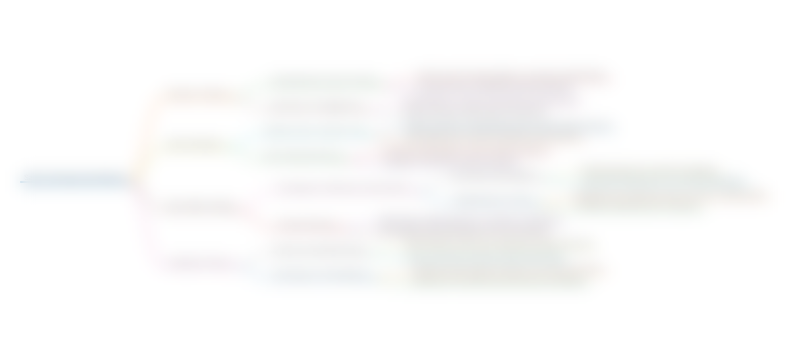
此内容仅限付费用户访问。 请升级后访问。
立即升级Keywords
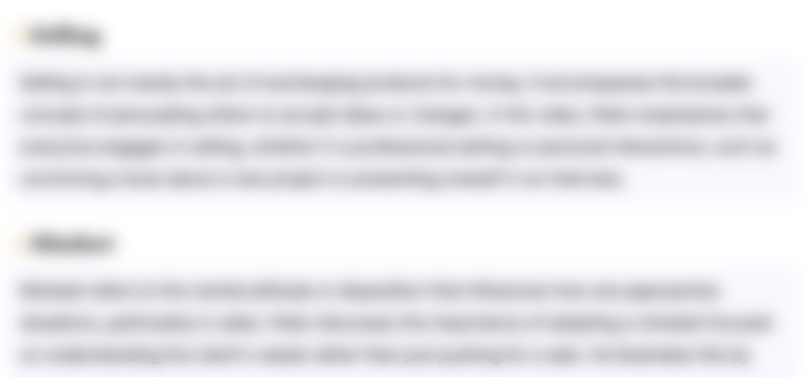
此内容仅限付费用户访问。 请升级后访问。
立即升级Highlights
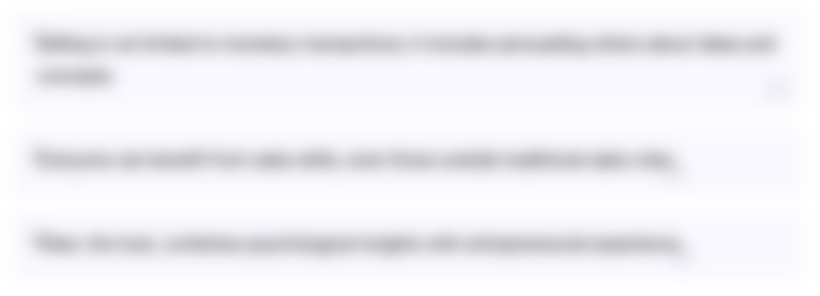
此内容仅限付费用户访问。 请升级后访问。
立即升级Transcripts
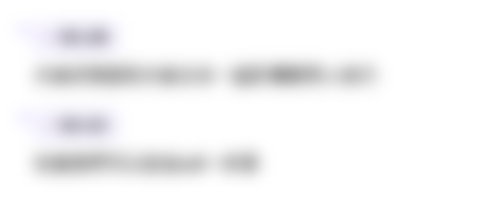
此内容仅限付费用户访问。 请升级后访问。
立即升级5.0 / 5 (0 votes)