Heavy Section Mill 🔥👌 #satisfying #rolling #design #machine #steel #viral #engineering #viralvideo
Summary
TLDRThe video showcases a state-of-the-art medium section mill by SMS May, featuring innovative technologies for high productivity and flexibility. It highlights the mill's compact design, hydraulic adjustment systems, and automated processes for rolling a wide range of products with excellent geometrical and metallurgical properties. The mill's annual capacity is 800,000 metric tons, with plans to increase to one million. The script details the mill's operations, from raw material preparation to finished product handling, emphasizing efficiency and quality control.
Takeaways
- 🏭 High productivity and product quality are achieved through innovative technologies and new rolling methods in a modern medium section Mill.
- 🔧 The mill is designed for flexibility and cost-effective operation, with intelligent plant design and new technologies to minimize operating costs.
- 🚀 Annual capacity is 800,000 metric tons, with plans to increase to one million tons, showcasing the mill's scalability.
- 🛠️ The rolling schedule includes a wide range of products such as wide flanged beams, parallel flanged beams, channels, and angles, highlighting the mill's versatility.
- 🌐 The mill stands are of compact design following the CCS principle, allowing for close tolerances and rapid schedule changeover.
- 🔄 The use of hydraulic adjustment systems and automatic gauge control ensures high availability and quick, fully automated role changing.
- 🔥 A walking beam furnace is used for precise and uniform heating, with a capacity of 240 tons per hour.
- 💦 High-pressure water descaling ensures outstanding surface quality of the products.
- 🔄 The compact group consists of three Universal CCS rolling stands, each with a nominal roll force of 5,500 k, emphasizing the mill's robustness.
- 📊 The mill is equipped with a material tracking system and online process models for path schedules and Mill parameters, ensuring reproducible processes with constant quality.
- 📦 The final products are efficiently processed through a compact roller straightener, cold saws, and automated piling machines, with capabilities for computer-controlled marking and weighing.
Q & A
What are the key demands of plant users on a modern medium section Mill?
-The key demands include high productivity, product quality, flexibility, and cost-effective operation.
How are these demands fulfilled in a modern medium section Mill?
-By implementing innovative technologies, new rolling methods, control systems, optimizing the finishing line with new straightening technologies, and efficient utilization of beam blanks.
What is the annual capacity of the medium section Mill mentioned in the script?
-The annual capacity is 800,000 metric tons, with plans to increase to a million tons.
What types of products can be produced in the described medium section Mill?
-Wide flanged beams, parallel flanged beams, channels steel, and equal and unequal angles.
What is the significance of the CCS principle used in the Mill stands?
-The CCS (Compact Cross Section) principle allows for compact design, leading to advantages such as rolling to close tolerances, hydraulic adjustment systems, rapid schedule changeover, high availability, and quick, fully automated roll changing.
What is the role of the walking beam furnace in the Mill?
-The walking beam furnace is designed for hot and cold charging, providing precise and uniform heating to rolling temperature, with a capacity of 240 tons per hour.
How does the descaling process contribute to surface quality in the Mill?
-Descale with high-pressure water ensures outstanding surface quality.
What is the patented xh rolling method and how does it benefit the Mill?
-The patented xh rolling method allows for a large product range with only a small number of rolls and guides, enhancing flexibility and efficiency.
What is the purpose of the selective cooling section for angles?
-The selective cooling section ensures uniform cooling across the top saw, which can also be used for sampling.
How does the compact roller straightener (CRS) contribute to the quality of the final product?
-The CRS has fully hydraulic adjustment and individual drives of the rolls ensure optimized torque distribution, leading to high-quality straightened products.
What are the capabilities of the cold saws in terms of cutting finished lengths?
-The cold saws can cut finished lengths from 4.5 meters to a maximum of 37 meters, with reduced noise emissions.
How does the Mill ensure high flexibility and productivity?
-High flexibility is achieved through practice-oriented plant design concepts, while productivity is enhanced by integrated automation. High quality with close tolerances is ensured by new technologies such as automatic quick changing of rolls and straightening rolls.
Outlines
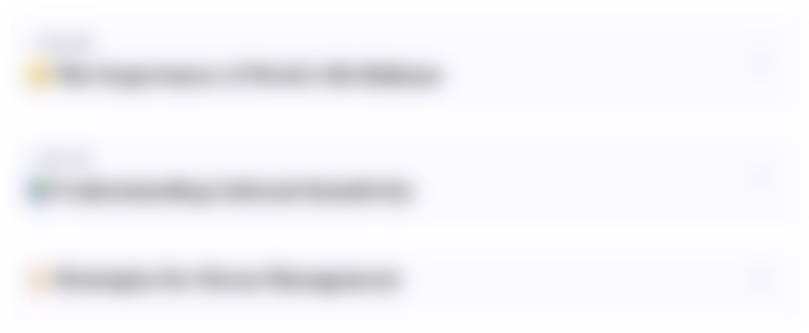
此内容仅限付费用户访问。 请升级后访问。
立即升级Mindmap
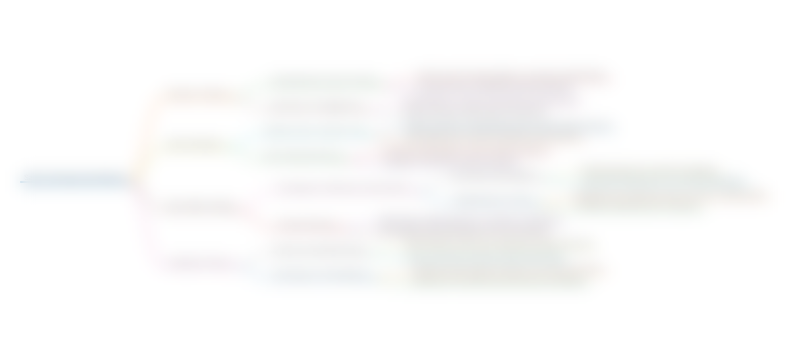
此内容仅限付费用户访问。 请升级后访问。
立即升级Keywords
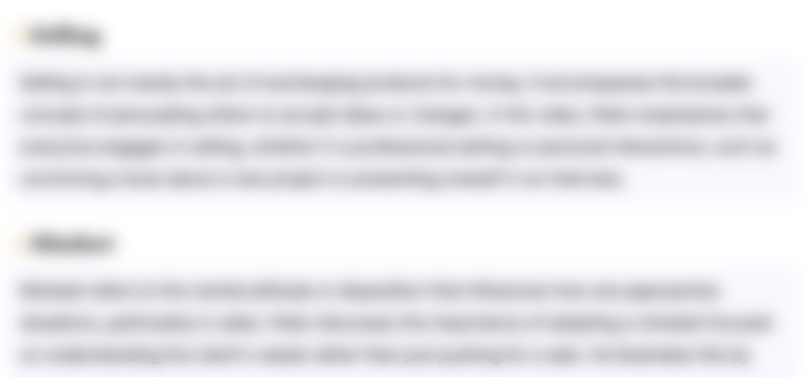
此内容仅限付费用户访问。 请升级后访问。
立即升级Highlights
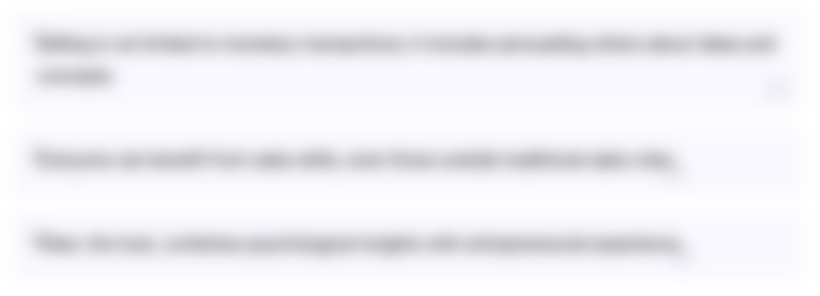
此内容仅限付费用户访问。 请升级后访问。
立即升级Transcripts
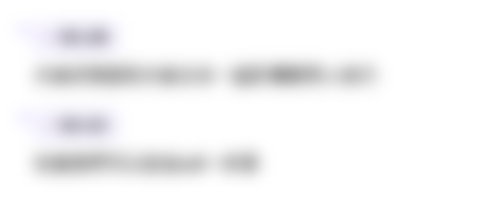
此内容仅限付费用户访问。 请升级后访问。
立即升级5.0 / 5 (0 votes)