How Pneumatic Control Valve Works | Control Valve Actuator Types | Control Valve Positioner Types
Summary
TLDRThis video script delves into the world of control valves, essential in regulating industrial processes like temperature and pressure. It introduces the components of a control valve, including the body, bonnet, plug, actuator, and positioner. The video explains how a positioner translates PLC commands into actuator movements, using an example of controlling liquid temperature in a tank. It also covers different types of actuators and positioners, highlighting the benefits of digital positioners for precise control and easy calibration through digital communication protocols.
Takeaways
- 🔄 **Control Systems Overview**: The script explains the necessity of a control system, including a PLC (Programmable Logic Controller), sensors, transmitters, and a final control element like a pump or valve, to manage process parameters such as temperature and pressure.
- 🛠️ **Role of Control Valves**: Control valves are not just for starting and stopping flow but also for throttling it to achieve specific process goals like regulating temperature or liquid levels.
- 🌡️ **Temperature Control Example**: An example is given where a control valve regulates the temperature of a liquid in a tank by controlling the flow of a heat-generating additive.
- 📡 **PLC and Sensor Integration**: The PLC sends commands to the control valve based on its logic and feedback from temperature sensors, typically using a 4-20mA DC signal.
- 🔧 **Positioner and Actuator Functions**: The positioner acts as an interface between the PLC and the actuator, converting the PLC's signal into a form that the actuator can use to move the valve stem.
- 💬 **Signal Conversion Process**: The positioner contains an I to P Transducer that converts the electrical current signal from the PLC into a pneumatic signal that the actuator can understand.
- 🔌 **Electro-Pneumatic Positioners**: These positioners are used with pneumatic actuators and include an I to P Transducer to convert electrical signals to pneumatic pressure.
- 🔄 **Feedback Mechanism**: Both the PLC and the positioner require feedback to ensure the valve is adjusted correctly; the positioner receives mechanical feedback from the control valve.
- 📱 **Digital Positioners**: These use a microprocessor for more accurate control and can communicate with the PLC or DCS using digital protocols, simplifying calibration and allowing for remote feedback.
- 🔑 **Actuator Types**: Actuators are categorized into Pneumatic, Hydraulic, Electric, and Manual, with pneumatic actuators being the most common due to their simplicity and safety.
- ❓ **Engagement Invitation**: The script concludes with an invitation for viewers to ask questions or share experiences with control valves, and to subscribe for more content.
Q & A
What is the primary function of a Programmable Logic Controller (PLC) in a control system?
-A PLC is used to control various parameters of a process, such as temperature and pressure, by sending commands to final control elements like pumps, heaters, or control valves.
What are the main components required to send data to a PLC?
-Sensors and transmitters are needed to collect data and send it to the PLC for processing and control.
What is a 'Final Control Element' in the context of a control system?
-A Final Control Element is a piece of equipment, such as a pump, heater, or control valve, that carries out the commands issued by the PLC.
How do control valves differ from regular valves in terms of their function?
-Control valves are not only used to fully start and stop the flow but also to control, adjust, or throttle the flow of a liquid for precise process control, such as temperature or level control.
What is a 'Globe valve' and what are its main parts?
-A Globe valve is a common type of control valve that includes the body through which fluid passes, the bonnet that covers the inner parts, the plug that controls the flow, and the actuator that moves the plug.
What is the role of an 'Actuator' in a control valve system?
-An Actuator transfers mechanical power to the plug of a control valve using a stem, receiving commands from the Positioner to open or close the valve.
What is the purpose of a 'Positioner' in a control valve system?
-A Positioner serves as an interface between the PLC and the Actuator, adjusting the plug's position to open or close the valve precisely according to the PLC's commands.
How does a Positioner convert the PLC's command signal into a signal that the Actuator can understand?
-A Positioner contains an 'I to P Transducer' that converts the 4-20mA DC electrical current signal from the PLC into a 3-15PSI pneumatic air pressure signal for the Actuator.
What is the significance of the 'Air supply' input in a Positioner?
-The Air supply input provides clean, filtered, and regulated air with sufficient pressure to the Positioner, which, along with a built-in pressure amplifier, enables the conversion of the pneumatic signal into enough force to move the Actuator.
How does a Positioner receive feedback to ensure the valve is opened to the correct percentage?
-A Positioner receives mechanical feedback from the control valve, which allows it to adjust the valve stem position precisely to match the command from the PLC.
What are the three main categories of Positioners mentioned in the script?
-The three main categories of Positioners are Electro-Pneumatic Positioners (I/P Positioners), Pneumatic Positioners, and Digital Positioners or Digital Valve Controllers.
How do Digital Positioners differ from other types of Positioners?
-Digital Positioners use a microprocessor to replace the mechanical position feedback, allowing for more accurate valve position adjustments and the ability to communicate via digital protocols like HART or Fieldbus.
What are the four categories of Actuators mentioned in the script?
-The four categories of Actuators are Pneumatic, Hydraulic, Electric, and Manual, each with its own advantages and applications.
How can Digital Positioners improve the calibration process of control valves?
-Digital Positioners enable easier calibration of control valves using handheld communicators and digital communication protocols, reducing the need for time-consuming and difficult mechanical adjustments.
Outlines
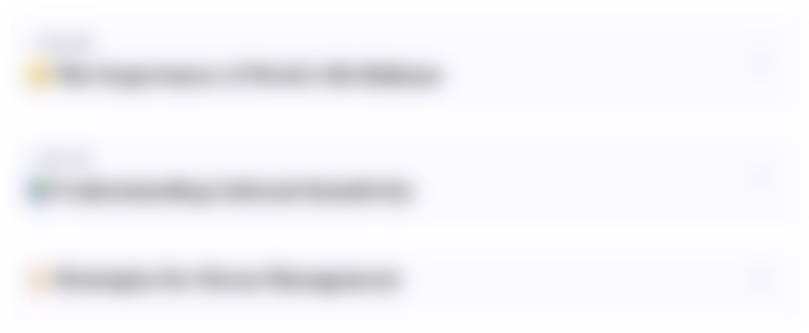
此内容仅限付费用户访问。 请升级后访问。
立即升级Mindmap
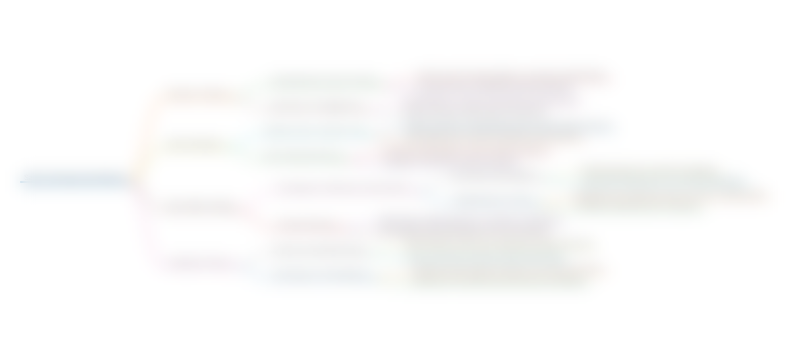
此内容仅限付费用户访问。 请升级后访问。
立即升级Keywords
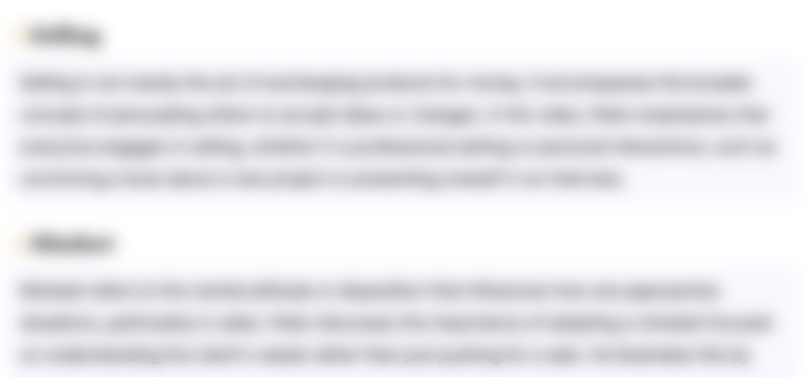
此内容仅限付费用户访问。 请升级后访问。
立即升级Highlights
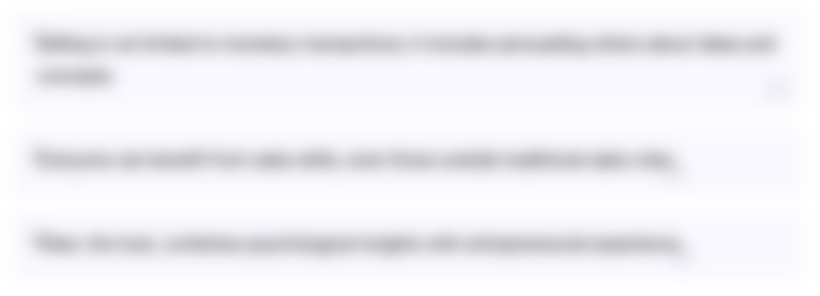
此内容仅限付费用户访问。 请升级后访问。
立即升级Transcripts
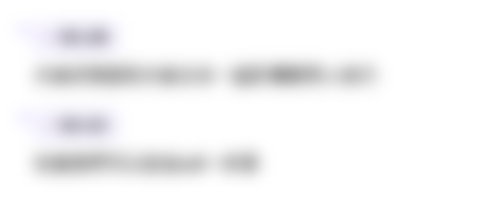
此内容仅限付费用户访问。 请升级后访问。
立即升级5.0 / 5 (0 votes)