Pressure Control - Hydraulics - Airframes & Aircraft Systems #10
Summary
TLDRThis lesson delves into the intricacies of aircraft hydraulic systems, focusing on components that control and maintain pressure. It explains that large aircraft operate at 3000 psi, while smaller ones may at 1500 psi. The pressure is regulated by automatic cutout valves in fixed volume pumps or by the pump itself in variable volume systems. Relief valves manage excess pressure due to thermal expansion or system failures, returning fluid to the reservoir. Thermal relief valves are crucial for temperature-induced pressure changes. High-pressure relief valves safeguard against pump control system failures, and priority valves ensure primary services operate even when system pressure drops. The lesson also touches on pressure reducing valves for services requiring lower pressure, such as brakes.
Takeaways
- 🛫 The hydraulic system in large modern aircraft operates at a normal pressure of 3000 psi, while smaller aircraft may operate at 1500 psi.
- 🔧 In systems with a constant delivery fixed volume pump, the automatic cutout valve (CoV) regulates the maximum system pressure.
- 💧 Relief valves are used to manage excess pressure due to thermal expansion or system failures by returning fluid to the reservoir.
- 🌡️ Thermal relief valves are particularly important for lines isolated by non-return valves, where trapped fluid can expand with temperature increases.
- 🔄 Full flow relief valves or high-pressure relief valves are installed downstream of the pump to bypass full pump output in case of control system failure.
- 🛠️ Pressure maintaining valves or priority valves ensure that primary services receive priority in fluid supply when system pressure falls below a set value.
- ✈️ Aircraft with a single hydraulic system may use a pressure maintaining valve to give flying controls priority over other services.
- 💺 In aircraft like the Boeing 747, each primary flying control is fed by two separate hydraulic systems, eliminating the need for a pressure maintaining valve.
- 🔩 Pressure reducing valves are used to adjust the main system pressure to a level suitable for operations like wheel brakes.
- 📉 Brake control valves, or metering valves, are variable pressure reducing valves that control brake system pressure based on pilot input or auto brake selections.
Q & A
What is the normal operating pressure of the hydraulic system in a large modern aircraft?
-The normal operating pressure of the hydraulic system in a large modern aircraft is 3000 pounds per square inch (psi).
What might be the operating pressure for hydraulic systems in smaller aircraft?
-Smaller aircraft may have hydraulic systems operating at 1500 psi.
How is the maximum system pressure set and adjusted in a constant pressure variable volume pump system?
-In a constant pressure variable volume pump system, the maximum system pressure is set and adjusted by the spring in the control piston.
What is the role of the automatic cutout valve (CoV) in a hydraulic system?
-In a system using a constant delivery fixed volume pump, the automatic cutout valve (CoV) is responsible for setting and adjusting the system pressure.
What is the purpose of relief valves in a hydraulic system?
-Relief valves are used to relieve excess pressure caused by thermal expansion or failure of the normal system pressure control device by returning fluid back to the reservoir.
How do thermal relief valves function in a hydraulic system?
-Thermal relief valves are fitted in lines isolated by non-return valves or selectors. They allow a small amount of fluid to flow back to the reservoir if the pressure rises approximately 10% higher than normal, thus relieving the pressure.
What is the function of a full flow relief valve in a hydraulic system?
-A full flow relief valve, also known as a high pressure relief valve, is fitted downstream of the pump to bypass full pump output to the reservoir in the event of a failure of the normal pump control system.
How does a pressure maintaining valve or priority valve work in a hydraulic system?
-A pressure maintaining valve isolates secondary services from the pressure supply if system pressure falls below a predetermined value, thus giving priority to the operation of primary services.
Why are pressure reducing valves used in aircraft hydraulic systems?
-Pressure reducing valves are used to reduce main system pressure to a value suitable for the operation of services that require lower pressure, such as wheel brakes.
How does a brake control valve or metering valve regulate pressure in the brake system?
-A brake control valve or metering valve is a variable pressure reducing valve that controls pressure in the brake system according to the position of the pilot's brake pedals or auto brake selections.
What is the significance of having multiple hydraulic systems in modern aircraft?
-Most modern aircraft have multiple hydraulic systems to ensure redundancy and reliability. This allows for simultaneous supply of power for primary flying controls, enhancing flight safety.
Outlines
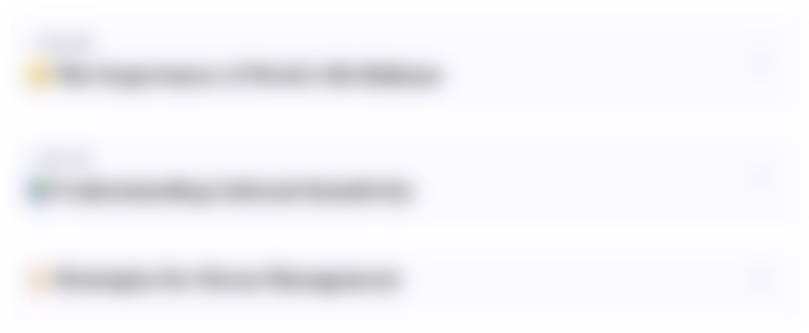
This section is available to paid users only. Please upgrade to access this part.
Upgrade NowMindmap
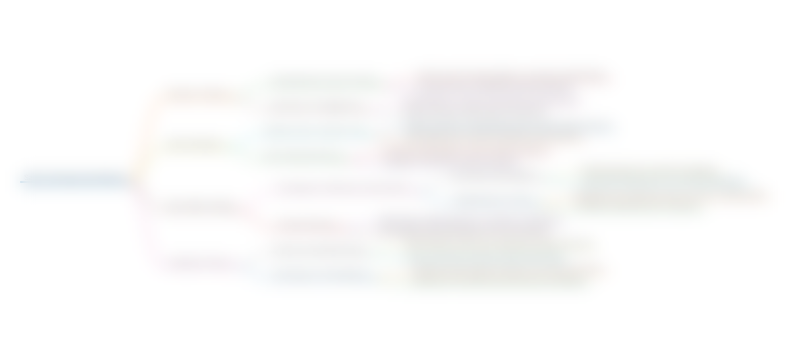
This section is available to paid users only. Please upgrade to access this part.
Upgrade NowKeywords
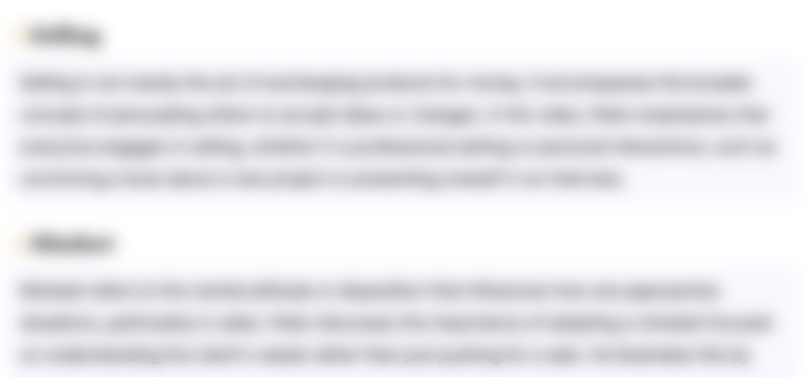
This section is available to paid users only. Please upgrade to access this part.
Upgrade NowHighlights
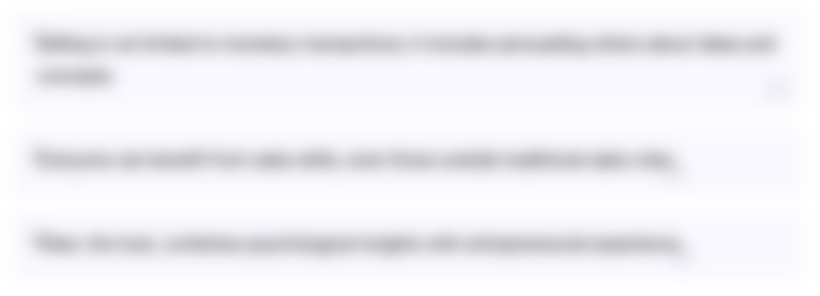
This section is available to paid users only. Please upgrade to access this part.
Upgrade NowTranscripts
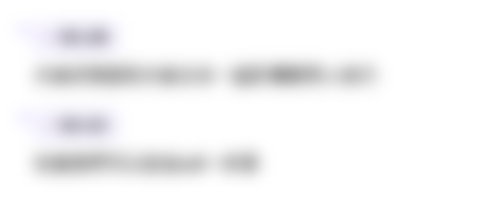
This section is available to paid users only. Please upgrade to access this part.
Upgrade NowBrowse More Related Video
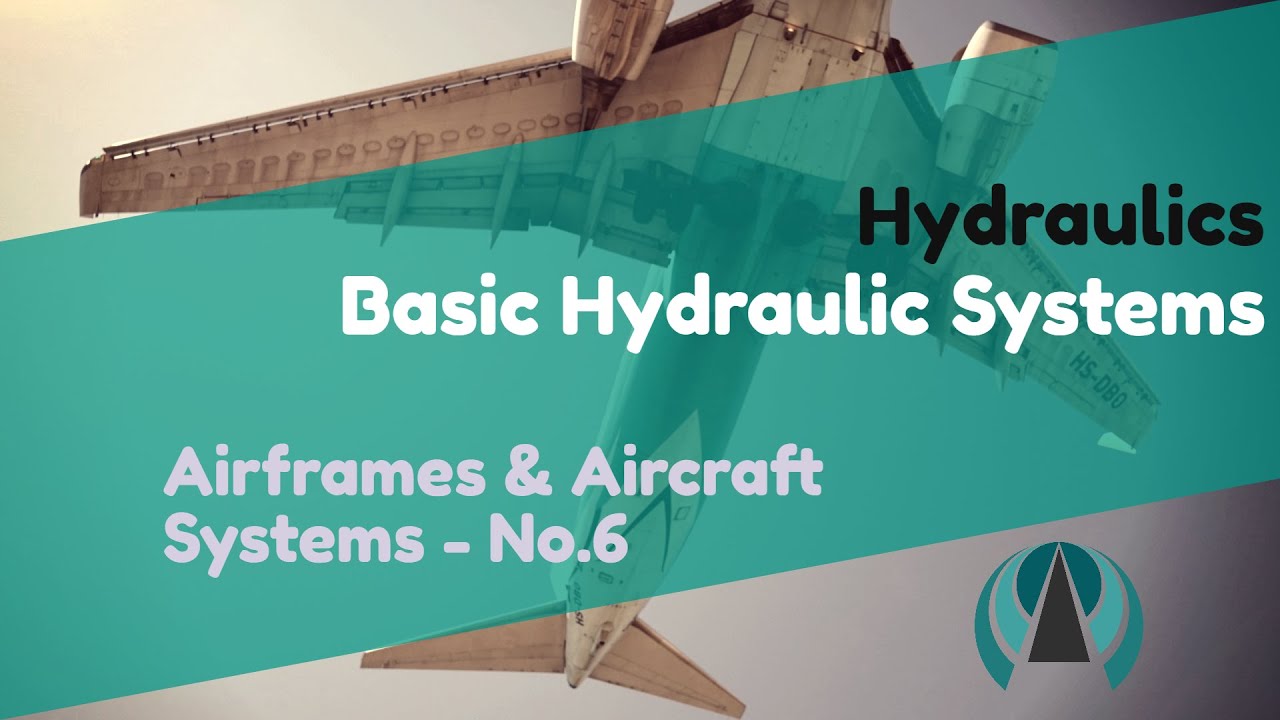
Basic Hydraulic Systems - Hydraulics - Airframes & Aircraft Systems #6

Components & Brake Kinetic Energy - Aircraft Brakes - Airframes & Aircraft Systems #24

Hydraulics - Basic Principles of Hydromechanics - Airframes & Aircraft Systems #4

Hydraulic Pumps - Hydraulics - Airframes & Aircraft Systems #7
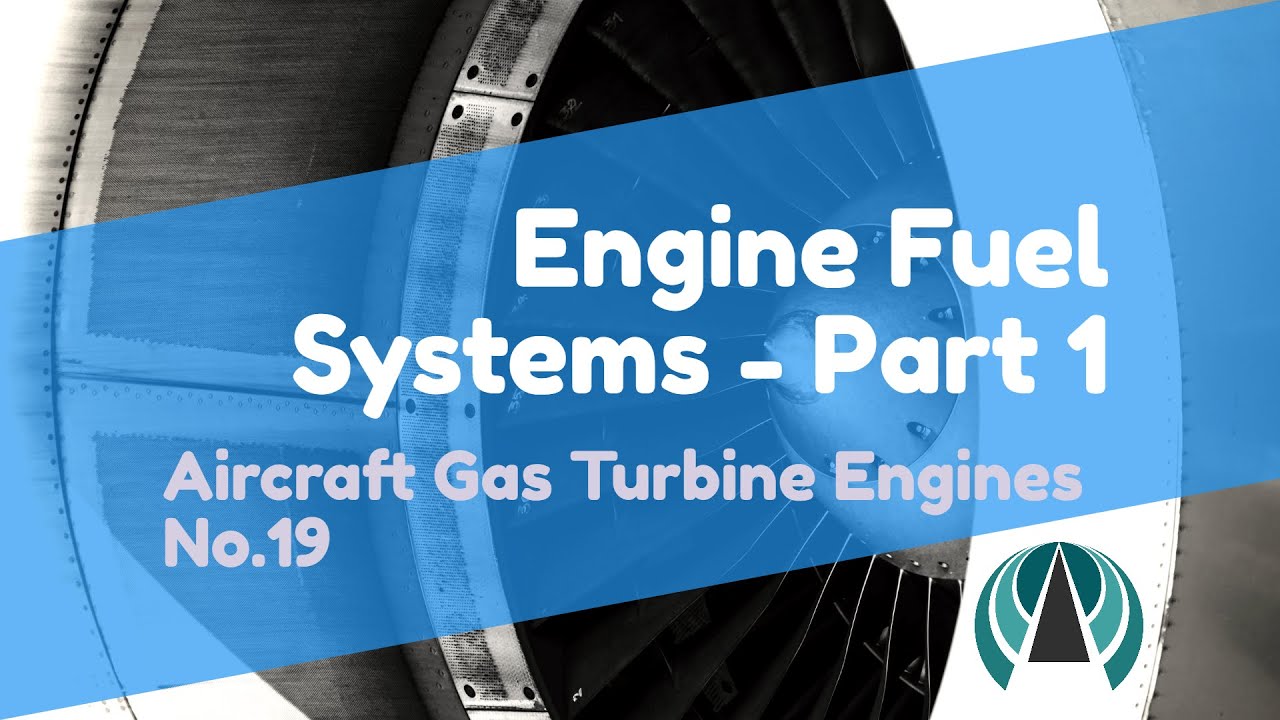
Engine Fuel Systems Part 1 - Aircraft Gas Turbine Engines #19
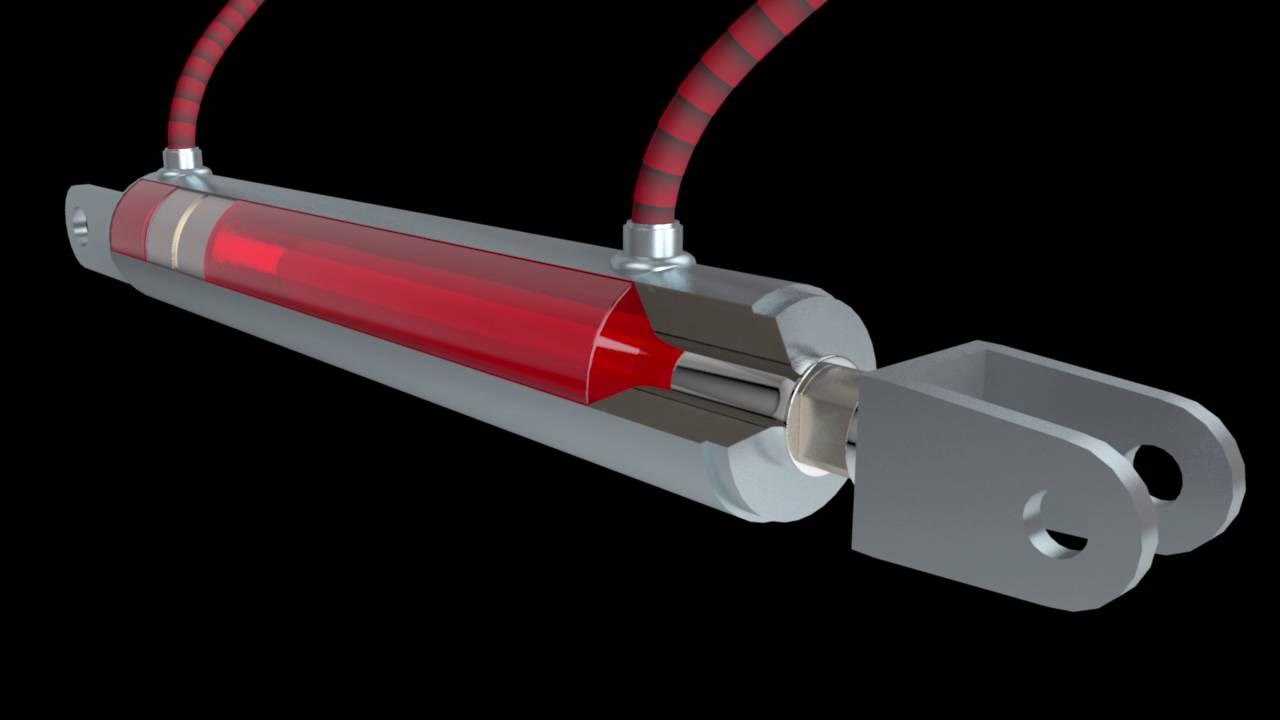
Aircraft Systems - 07 - Hydraulic System
5.0 / 5 (0 votes)