PLC Basics | Programmable Logic Controller
Summary
TLDRThis video introduces the basics of Programmable Logic Controllers (PLCs), the backbone of industrial automation. Initially replacing relays, PLCs are computers without typical peripherals, designed for robust control applications. The video covers the structure of PLCs, including CPU modules and I/O devices, and their evolution to include various input/output types and programming capabilities. It also touches on the diversity of programming languages used, with a mention of the IEC 61131 standard aiming for interoperability. The script encourages viewers to explore more PLC programming resources on realpars.com for career advancement in automation and controls engineering.
Takeaways
- ๐ฅ๏ธ Programmable Logic Controllers (PLCs) are specialized computers used in industrial automation, designed to replace traditional relay systems.
- ๐ PLCs initially simplified the process of controlling machines, which was previously time-consuming and complex with relays.
- ๐ ๏ธ PLCs are more reliable than relays, requiring less downtime for maintenance due to their lower failure rates.
- ๐ก๏ธ Compared to relays, PLCs are more energy-efficient, produce less heat and soot, and require less physical space.
- ๐ A typical PLC setup consists of a CPU module and input/output (I/O) devices, which can be integrated or separate and connected via a backplane or data cables.
- ๐ก PLCs can be expanded beyond simple digital I/O to include analog and other numerical inputs and outputs, enhancing their functionality.
- ๐งฉ PLCs have built-in calculation capabilities, allowing for complex operations such as statistical process control (SPC) and PID controllers to be integrated into the program.
- โจ๏ธ Most PLCs are programmed using applications on standard PCs, communicating with the PLC via Ethernet or proprietary communication protocols.
- ๐ข There is no universal programming language for PLCs; manufacturers have their own 'Ladder Logic' with variations in capabilities and syntax.
- ๐ The IEC 61131 standard attempts to provide a unified approach to PLC programming, defining multiple programming languages with different strengths.
- ๐ The script encourages viewers to visit realpars.com for further training materials and to subscribe to their training series for professional development in automation and controls engineering.
Q & A
What is a PLC and why is it considered the workhorse of industrial automation?
-A PLC, or programmable logic controller, is a special-purpose computer used in industrial automation. It is considered the workhorse because it replaces complex relay-based logic systems, offering more reliability, flexibility, and efficiency in controlling industrial processes.
Why were relays replaced by PLCs in industrial automation?
-Relays were replaced by PLCs because they were time-consuming and challenging to set up, required frequent maintenance, used a lot of electricity, generated heat and soot, and took up a lot of space. PLCs offer more efficient, reliable, and easily modifiable control systems.
What are the main components of a PLC system?
-The main components of a PLC system include the CPU module and input/output (I/O) devices. The CPU communicates with the I/O devices, which can be either part of the CPU or in separate modules. These components are typically housed in a control panel on the factory floor.
How do PLCs communicate with I/O devices located far away from the CPU?
-PLCs can communicate with I/O devices located far away from the CPU using data cables. This allows the PLC to control processes that are not limited to a single cabinet or even the same building.
What types of inputs and outputs can PLCs handle?
-PLCs can handle both digital and analog inputs and outputs. Over time, manufacturers have added analog and other numerical inputs and outputs, allowing for more complex calculations and control capabilities within the PLC program.
How are PLCs programmed?
-PLCs are programmed using applications running on standard desktop or laptop PCs. They communicate with the PLC via Ethernet or proprietary communication buses, with Ethernet and USB being common in recent years.
Why is there a lack of standardization in PLC programming languages?
-There is a lack of standardization because different manufacturers have developed their own versions of 'Ladder Logic' and other programming languages, leading to variations in capabilities, implementation methods, and processing order of the control logic.
What is the IEC 61131 standard, and why is it important?
-The IEC 61131 standard, established by the American National Standards Institute (ANSI), defines several programming languages for PLCs with different strengths and weaknesses. It aims to bring order and interoperability to the diverse and chaotic landscape of PLC programming.
How does local programming standards affect the choice of programming language for PLCs?
-Local programming standards, set by your boss or the customer, will usually specify which programming language you should use for PLC programming. This ensures consistency and meets specific project or organizational requirements.
Where can you find more training materials for PLC programming?
-You can find more training materials for PLC programming at realpars.com. They offer a variety of videos and training series designed to help you learn PLC programming and advance in the field of automation and controls engineering.
Outlines
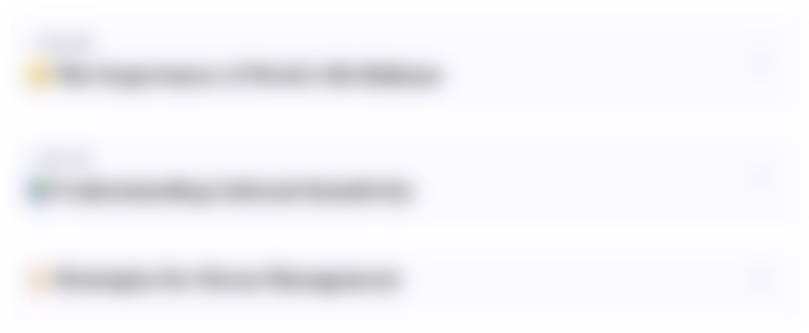
This section is available to paid users only. Please upgrade to access this part.
Upgrade NowMindmap
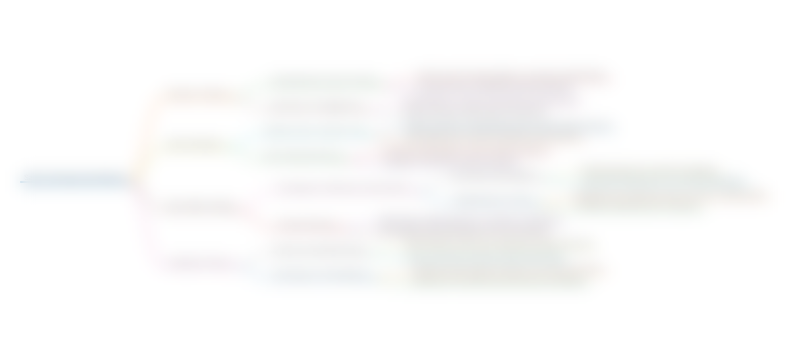
This section is available to paid users only. Please upgrade to access this part.
Upgrade NowKeywords
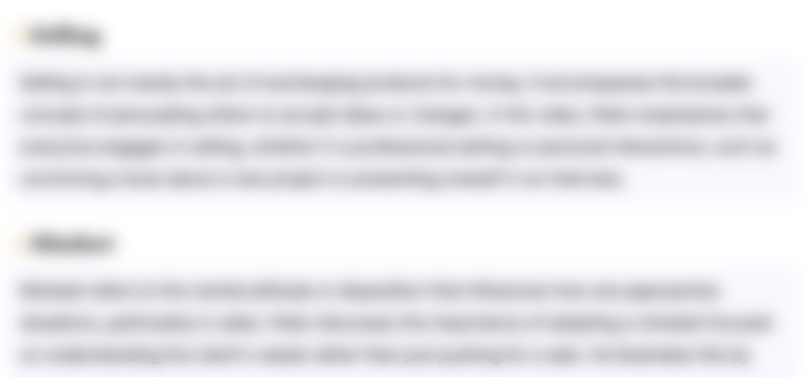
This section is available to paid users only. Please upgrade to access this part.
Upgrade NowHighlights
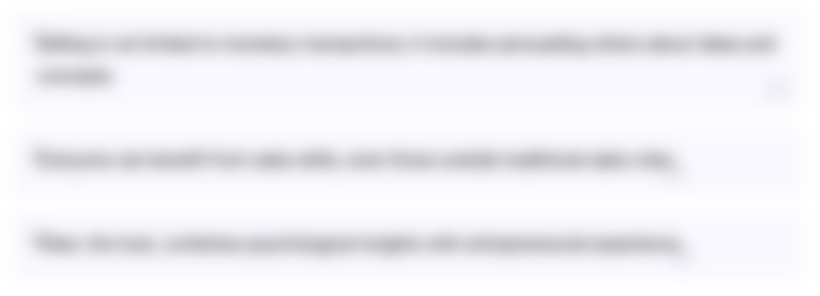
This section is available to paid users only. Please upgrade to access this part.
Upgrade NowTranscripts
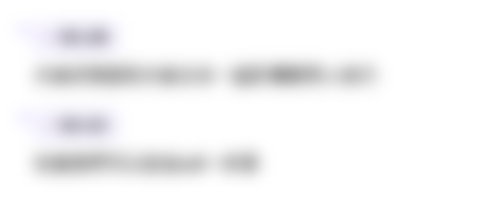
This section is available to paid users only. Please upgrade to access this part.
Upgrade NowBrowse More Related Video
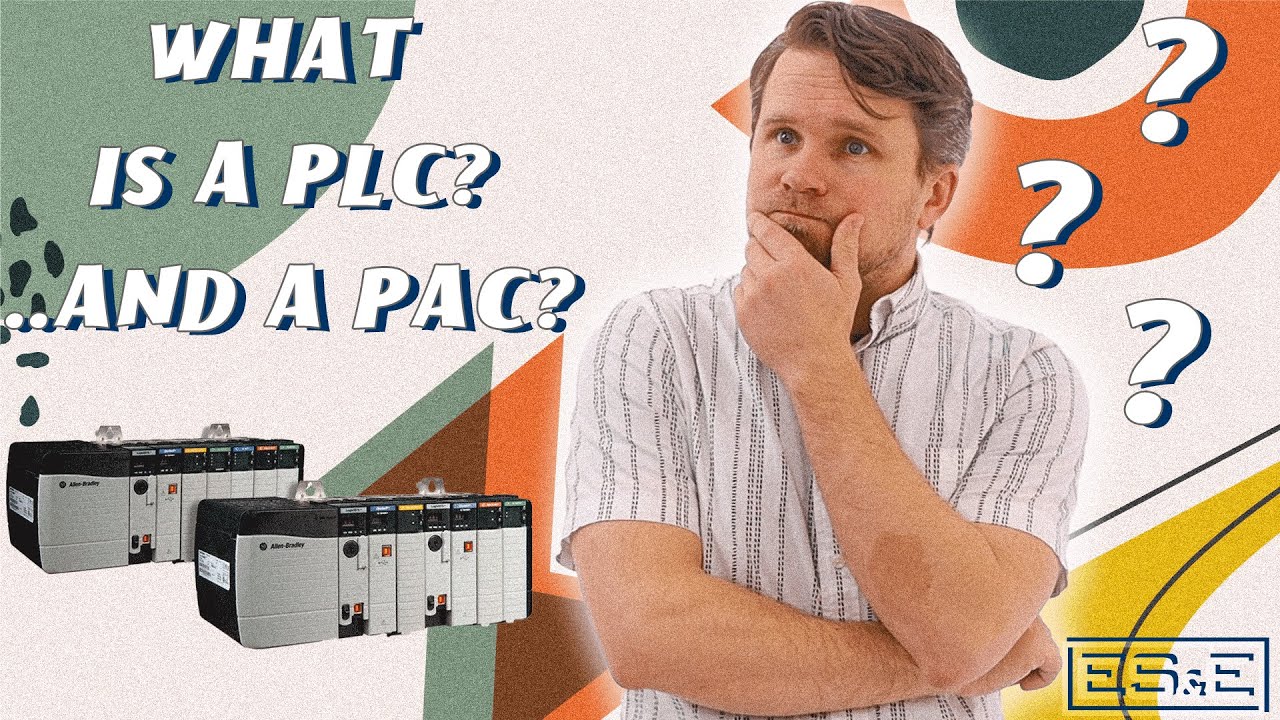
What is a PLC?...and a PAC?!?

AWAL BELAJAR Ngobrol Santai Tentang PLC (Programmable Logic Controller)

Electrical Review - PLC Basics Part 1

Introduction to Industrial Automation | Introduction and History
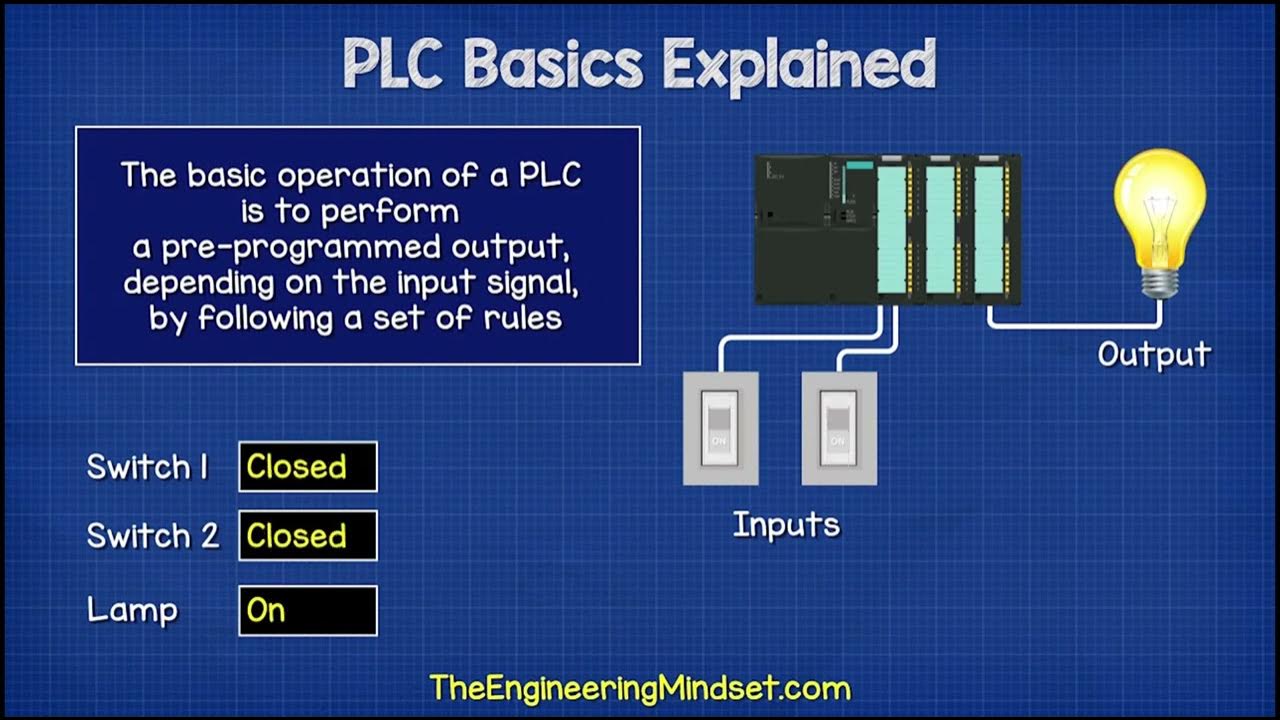
1. Berkenalan Dengan Kerja Perangkat Kontrol PLC
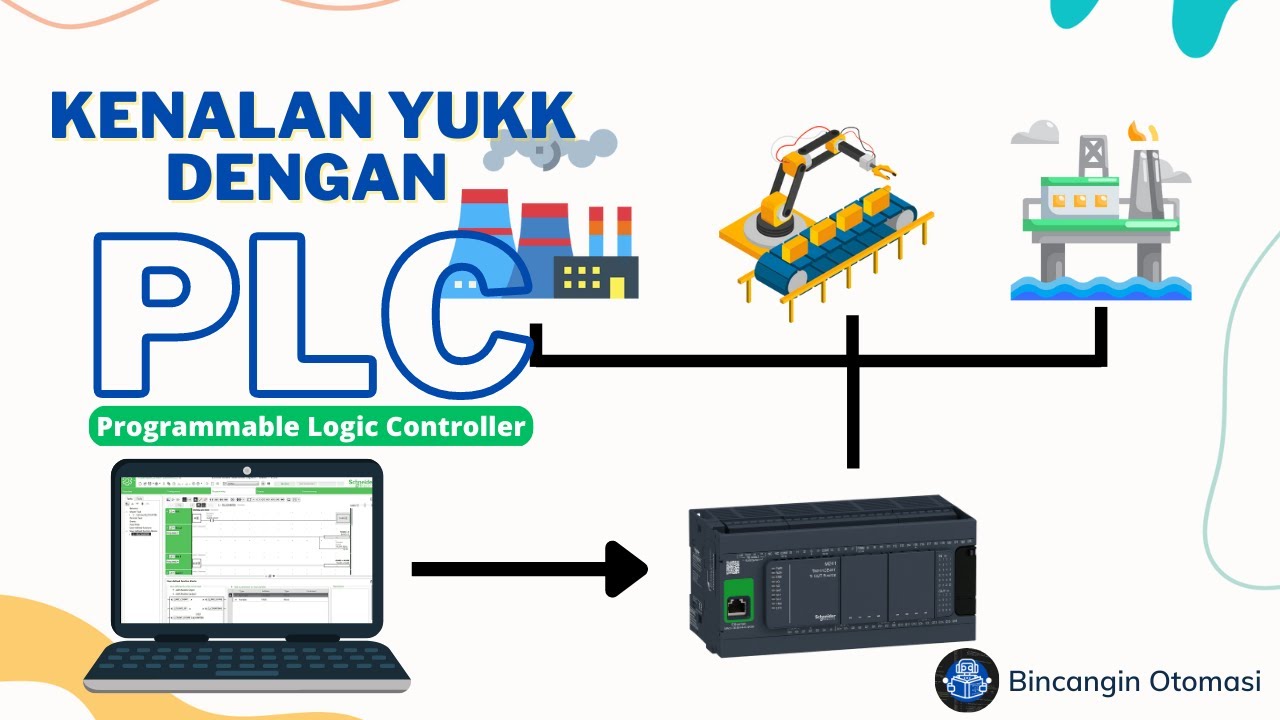
Belajar PLC | Pengenalan Programmable Logic Controller #1
5.0 / 5 (0 votes)