Cement Manufacturing
Summary
TLDRThis video explains the two methods of manufacturing Portland cement: the wet process and the dry process. In the wet process, clay is purified and mixed with crushed limestone to create a raw slurry. In the dry process, raw materials are mixed, dried, pulverized, and made into a fine powder called raw meal. Both methods produce a charge that is introduced into a rotary kiln, where it undergoes chemical reactions at high temperatures to form clinker cement. The clinker is then cooled, ground into a fine powder, and mixed with gypsum to produce the final cement product.
Takeaways
- 🛠️ Portland cement is manufactured by two methods: wet process and dry process.
- 💧 In the wet process, clay is purified by washing in a wash mill.
- 🪨 Limestone is crushed into small particles and mixed with purified clay to get raw slurry in the wet process.
- 🌞 In the dry process, raw materials are mixed in proper proportions, dried, pulverized, and crushed into fine particles to create a uniform mixture.
- 📦 The resulting powder in the dry process is called raw material.
- 🔥 The raw slurry or raw meal obtained by either process is called charge and is introduced into a rotary kiln.
- 🔄 A rotary kiln consists of a steel cylinder about 150 meters long and 4 meters in diameter, rotating 30 to 60 turns per hour.
- 🚚 At one end of the cylinder, a screw conveyor slowly allows the charge into the cylinder, while at the other end, a burner burns coal or oil.
- 🌡️ The charge moves towards the hot end of the kiln, where the temperature is around 1700 to 1900 degrees centigrade.
- 🧪 Chemical reactions between calcium oxide and aluminum silicates occur, forming a mixture of calcium silicates and calcium aluminates.
- 🏗️ The resultant product consists of gray, hard balls called clinker cement.
- 🌬️ Clinker cement is cooled, ground to a fine powder, and mixed with 2-3% gypsum to produce the final cement product.
Q & A
What are the two methods of manufacturing Portland cement?
-The two methods of manufacturing Portland cement are the wet process and the dry process.
What is the first step in the wet process of cement manufacturing?
-In the wet process, the first step is the purification of clay by washing in a wash mill.
How are limestone and clay mixed in the wet process?
-In the wet process, limestone is crushed into small particles and mixed with purified clay in proper proportions to obtain raw slurry.
What is the initial step in the dry process of cement manufacturing?
-In the dry process, the initial step involves mixing the raw materials in proper proportions.
What is the purpose of drying and pulverizing the mixture in the dry process?
-The purpose of drying and pulverizing the mixture in the dry process is to create a uniform fine powder known as raw meal.
What is the role of a rotary kiln in cement manufacturing?
-A rotary kiln is used to introduce the charge (raw slurry or raw meal) and subject it to high temperatures for chemical reactions to occur.
What are the dimensions and rotation speed of a typical rotary kiln?
-A typical rotary kiln is about 150 meters long and 4 meters in diameter, rotating at 30 to 60 turns per hour.
What is the temperature range at the burning end of the kiln?
-The temperature at the burning end of the kiln is around 1700 to 1900 degrees centigrade.
What chemical reactions occur at the high-temperature end of the kiln?
-At the high-temperature end of the kiln, chemical reactions take place between calcium oxide and aluminium silicates, forming a mixture of calcium silicates and calcium aluminates.
What is the final product of the chemical reactions in the kiln called?
-The final product of the chemical reactions in the kiln is called clinker cement, which consists of gray, hard balls.
How is clinker cement processed before it becomes Portland cement?
-Clinker cement is cooled, ground into a fine powder, and mixed with 2 to 3 percent of gypsum to become Portland cement.
Outlines
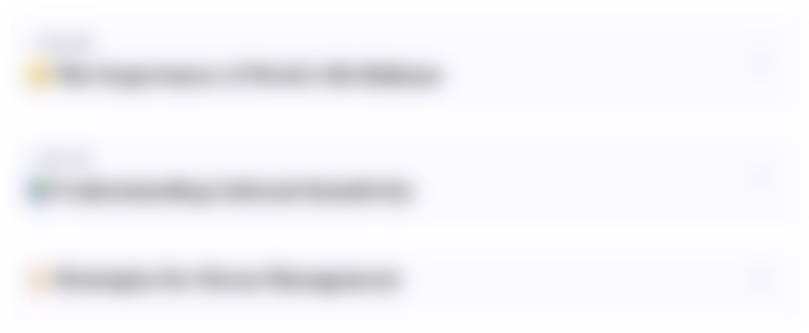
This section is available to paid users only. Please upgrade to access this part.
Upgrade NowMindmap
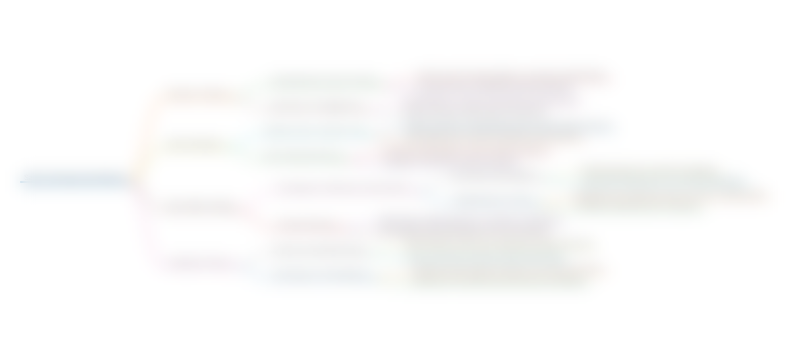
This section is available to paid users only. Please upgrade to access this part.
Upgrade NowKeywords
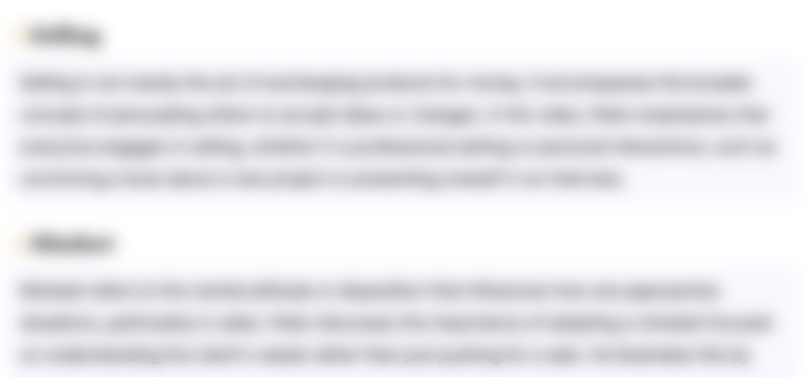
This section is available to paid users only. Please upgrade to access this part.
Upgrade NowHighlights
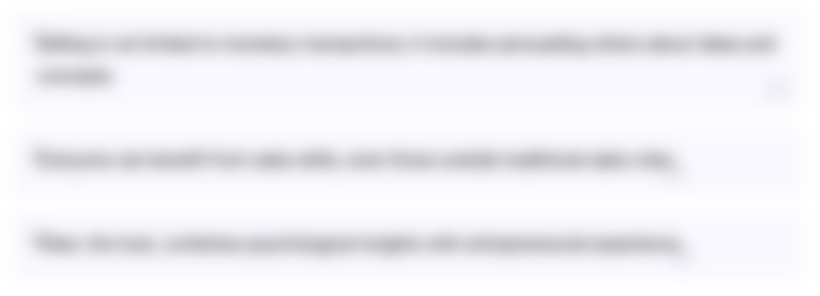
This section is available to paid users only. Please upgrade to access this part.
Upgrade NowTranscripts
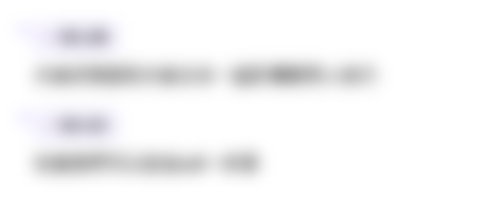
This section is available to paid users only. Please upgrade to access this part.
Upgrade NowBrowse More Related Video
5.0 / 5 (0 votes)