Métodos de Produção de Comprimidos
Summary
TLDRThis video script delves into the methods used in tablet manufacturing within the pharmaceutical industry. It covers three primary processes: wet granulation, dry granulation, and direct compression. Wet granulation and dry granulation both involve transforming a powder mixture into granules to improve fluidity and compressibility, but dry granulation eliminates the need for moisture, which preserves heat-sensitive ingredients. Direct compression simplifies the process further by directly compacting the mixture into tablets. The script highlights the advantages and disadvantages of each method, emphasizing speed, stability, and the potential for tablet degradation.
Takeaways
- 😀 Wet granulation involves mixing the active pharmaceutical ingredient (API) with excipients, adding a liquid binder, and forming granules, followed by drying and calibrating them for uniformity.
- 😀 Dry granulation skips the use of liquids, instead compacting the API and excipients into large briquettes, which are then broken down into granules and calibrated.
- 😀 Direct compression is the simplest method, where API and excipients are mixed and directly compressed into tablets without the need for granulation or drying.
- 😀 Wet granulation improves powder flowability and compressibility, resulting in better tablet uniformity, but involves longer processing times due to the liquid addition and drying stages.
- 😀 Dry granulation is faster than wet granulation and avoids moisture-sensitive issues, but it produces tablets with higher friability and lower hardness.
- 😀 Direct compression is the fastest and cost-effective method, with no need for liquid or heat, making it suitable for stable drugs but resulting in tablets with lower hardness and higher friability.
- 😀 The major disadvantage of dry granulation and direct compression is the production of tablets with high friability, meaning they are more prone to breaking or losing powder.
- 😀 Wet granulation is not suitable for heat-sensitive or moisture-sensitive drugs due to the use of liquids and drying stages.
- 😀 Dry granulation is ideal for moisture-sensitive or heat-sensitive drugs since it avoids both heat and moisture during processing.
- 😀 Tablet formation through compression uses a system of matrices and punches to compact the granules or powder into tablets. The process includes applying pressure to form and eject the tablet.
Q & A
What are the main methods used in tablet manufacturing in the pharmaceutical industry?
-The three main methods for tablet manufacturing in the pharmaceutical industry are wet granulation, dry granulation, and direct compression.
What is the purpose of granulation in tablet manufacturing?
-Granulation transforms a mixture of powders into granules, improving characteristics such as flowability and compressibility, which ensures better consistency in tablet formation.
What is the difference between wet granulation and dry granulation?
-Wet granulation involves the use of a liquid to form granules, followed by drying to eliminate excess moisture, while dry granulation involves compressing powders to form large tablets (briquettes), which are then granulated.
What are the main steps involved in wet granulation?
-The steps in wet granulation include mixing the drug with excipients, adding the wetting liquid, mixing to form a paste, granulating, drying the granules, and calibrating the granules for uniform size.
Why is drying important in wet granulation?
-Drying removes the excess liquid added during the wetting stage, resulting in dry granules that are ready for further processing.
What is the advantage of dry granulation compared to wet granulation?
-Dry granulation is advantageous because it does not require liquids, which means it can be used for heat-sensitive or moisture-sensitive drugs. It also reduces the process time since there is no need for drying.
What are the disadvantages of dry granulation?
-The main disadvantages of dry granulation include high friability (tendency to lose powder during storage) and low hardness, making the tablets more prone to disintegration.
What is direct compression in tablet manufacturing?
-Direct compression is a method where the drug and excipients are directly compacted into tablets without the need for granulation. It involves fewer steps and is faster and more cost-effective.
What are the benefits of direct compression over other methods?
-Direct compression is quicker, simpler, and more stable, as it avoids the use of water or heat. It also results in tablets that disintegrate more quickly.
What are the potential issues with direct compression?
-Direct compression can lead to tablets with high friability and low hardness, similar to dry granulation. It is also more susceptible to a defect known as capping, where part of the tablet's surface may break off due to air pockets.
Outlines
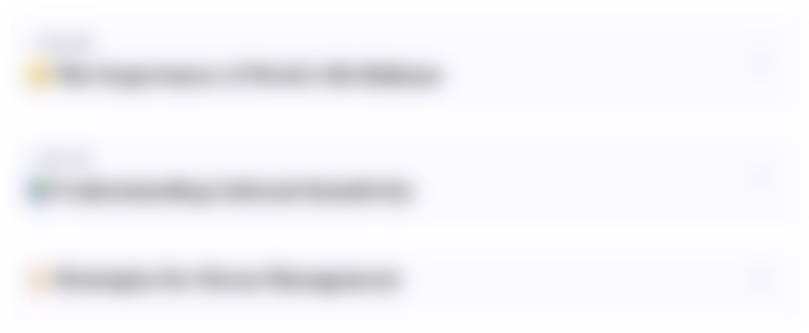
This section is available to paid users only. Please upgrade to access this part.
Upgrade NowMindmap
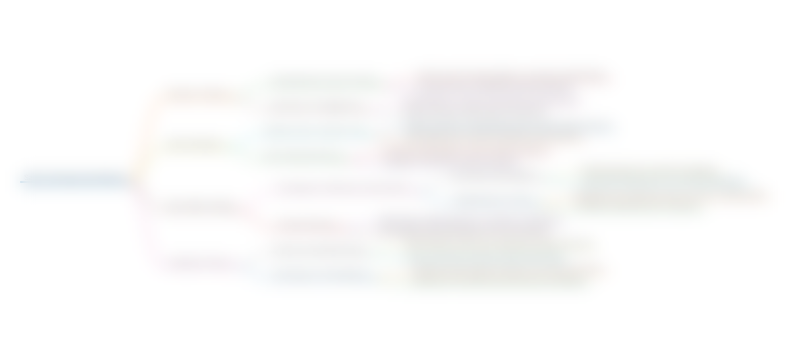
This section is available to paid users only. Please upgrade to access this part.
Upgrade NowKeywords
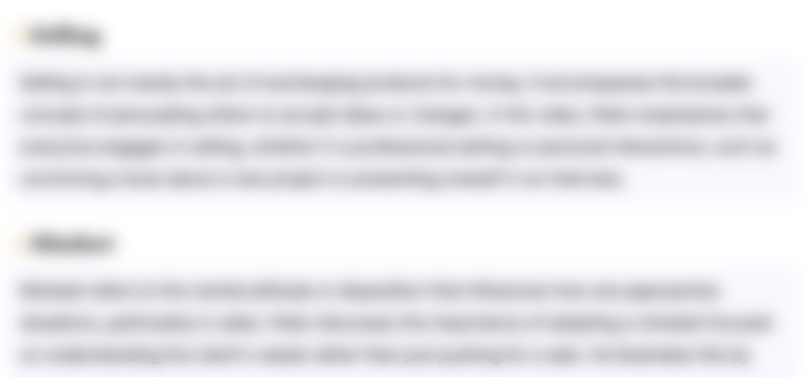
This section is available to paid users only. Please upgrade to access this part.
Upgrade NowHighlights
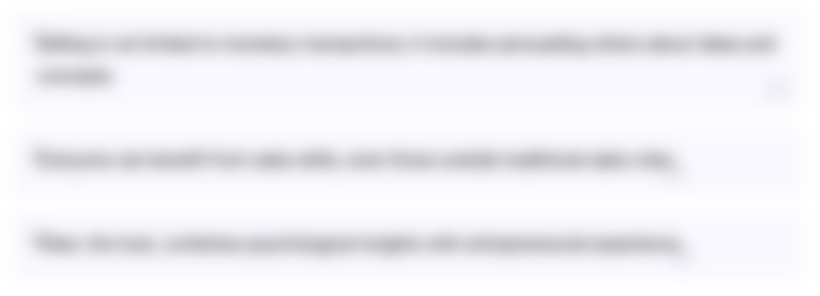
This section is available to paid users only. Please upgrade to access this part.
Upgrade NowTranscripts
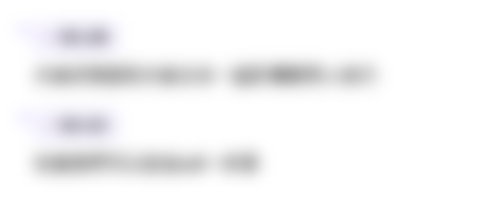
This section is available to paid users only. Please upgrade to access this part.
Upgrade Now5.0 / 5 (0 votes)