Frederick Taylor Scientific Management
Summary
TLDRFrederick Taylor, the father of scientific management, revolutionized workplace efficiency with his systematic approach to optimizing tasks. By dividing labor into simple steps, emphasizing hierarchy, and advocating for the selection and training of 'first-class' workers, Taylor's methods significantly boosted productivity. His time and motion studies, exemplified by the shovel experiments, sought the most efficient task execution. Though his techniques led to increased profits and standardized products, they also resulted in worker dehumanization and burnout, highlighting the mixed outcomes of Taylorism.
Takeaways
- 🛠️ Frederick Taylor is recognized as a founding father of organizational studies, known for his scientific management approach.
- 🔧 Taylor was a mechanical engineer and management consultant who aimed to improve efficiency in factories through standardized work processes.
- 📚 He introduced the concept of 'scientific management' or 'Taylorism', which involved applying scientific methods to work to break away from unproven practices.
- 🔑 Division of labor was a key principle for Taylor, advocating for the breaking down of work into simple, separate steps performed by different workers.
- 🔑🔍 Taylor's focus was on determining the 'one best way' to perform tasks, emphasizing standardization to increase productivity.
- 🏢 He supported a clear hierarchy in organizations, with managers at the top designing and enforcing work processes, and workers following instructions.
- 💼 Taylor believed in selecting, training, and compensating high-performing 'first-class' employees, with the most productive workers receiving higher pay.
- 🕒 His method included 'time and motion studies' to find the most efficient way to perform tasks, reducing the time and effort required.
- 💡 The 'shovel experiment' is a notable example of Taylor's approach, where he determined the ideal weight for a shovel to maximize productivity.
- 🚗 Henry Ford took Taylor's principles to the next level, applying them to the automobile industry and revolutionizing production with the assembly line.
- 🔄 The outcomes of Taylor's work are mixed, with significant productivity gains but also negative impacts such as dehumanization and employee burnout.
Q & A
Who is Frederick Taylor and what is his contribution to organizational studies?
-Frederick Taylor is considered a founding father of organizational studies. He introduced the concept of scientific management, which aimed to make organizations more standardized, efficient, and productive by closely studying work processes.
What was the context for the development of Taylor's scientific management approach?
-Factories were rapidly expanding, and there were no standardized ways to manage large groups of workers or complex tasks. Taylor saw the need for a systematic approach to improve efficiency and productivity in these environments.
What does the term 'scientific management' refer to in the context of Taylor's work?
-Scientific management refers to the application of scientific principles to work. It involves careful and systematic study of tasks at a micro level to find the most efficient ways to perform work and speed up processes.
What is the concept of 'Division of labor' as advocated by Taylor?
-Division of labor is the practice of breaking down work processes into very small, simple, and separate steps. Instead of one person doing an entire project from start to finish, each person performs only one or two specific steps, which are then passed on to the next person.
How did Taylor's belief in hierarchy influence his approach to management?
-Taylor believed in a clear chain of command, separating employees at the bottom of the organization from managerial staff at the top. Managers were responsible for designing work processes and enforcing how work was performed, while employees followed directions.
What was Taylor's perspective on selecting, training, and compensating workers?
-Taylor advocated for the selection and training of high-performing workers, or 'first-class employees,' and matching them to jobs best suited for them. He believed that the most productive workers should be paid more, and he was critical of employees who did not meet higher standards.
Can you explain Taylor's method of 'time and motion studies'?
-Time and motion studies involved determining the least amount of time and the fewest number of motions required to perform each task. Taylor aimed to make employees work as efficiently as machines, breaking down tasks to find the most productive methods.
What is an example of Taylor's time and motion study, and what was its outcome?
-Taylor's shovel experiments are an example of time and motion studies. He tested different shovel sizes to find the optimal amount of material a shovel should hold to maximize productivity. The result was that a shovel holding 21.5 pounds of sand or coal was the most efficient.
How did Taylor's work influence the development of the assembly line in manufacturing?
-Taylor's principles of efficiency and standardization were taken to the next level by Henry Ford, who applied them to the development of the assembly line. This innovation significantly reduced the time it took to manufacture a car, increasing productivity and reducing costs.
What are some of the mixed outcomes of Taylor's work on productivity and employee treatment?
-While Taylor's work led to significant increases in productivity and more consistent, higher-quality products, it also resulted in some negative outcomes. Companies often failed to pay employees more as Taylor advised, leading to deskilled and expendable workers in a harsh, dehumanizing work environment.
How has Taylor's influence persisted in modern work practices, even outside of manufacturing?
-Taylor's influence can be seen in various industries, from the specific design of tools like shovels to the streamlined processes in fast food restaurants and other service industries. His emphasis on efficiency and standardization has shaped how tasks are performed and how products are made.
Outlines
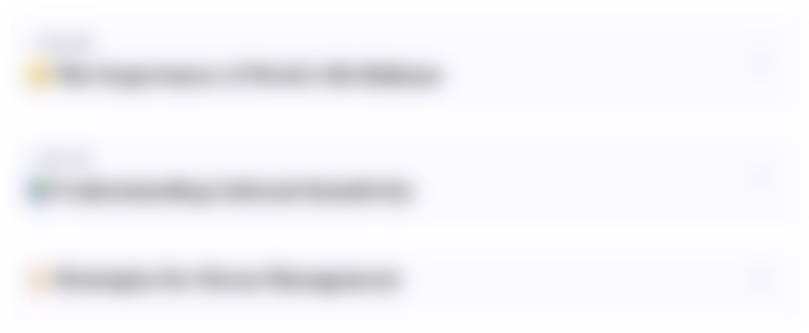
This section is available to paid users only. Please upgrade to access this part.
Upgrade NowMindmap
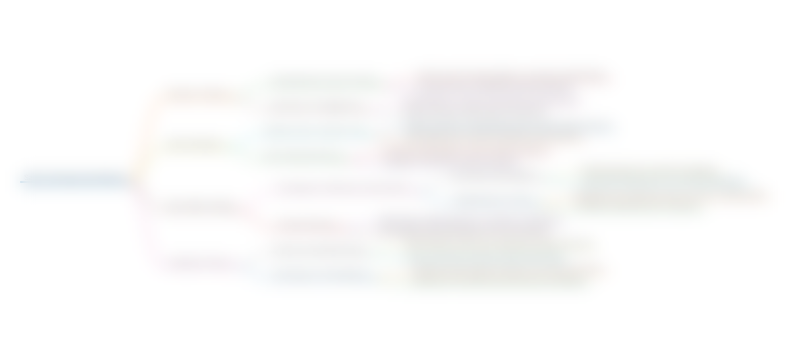
This section is available to paid users only. Please upgrade to access this part.
Upgrade NowKeywords
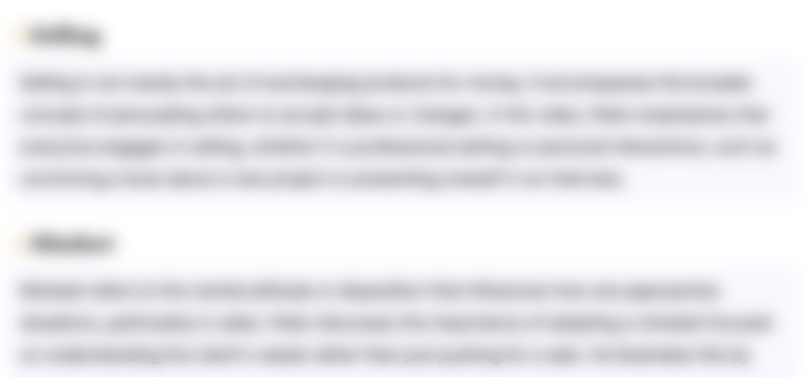
This section is available to paid users only. Please upgrade to access this part.
Upgrade NowHighlights
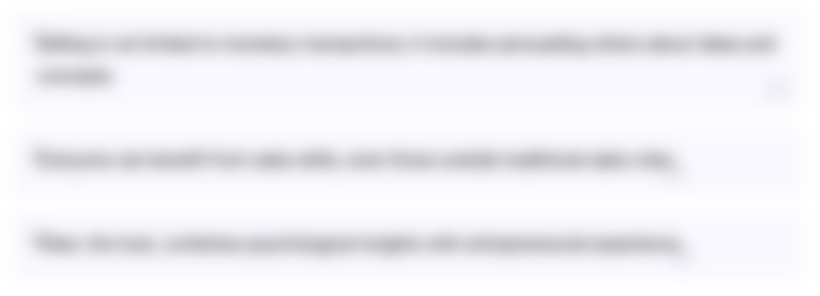
This section is available to paid users only. Please upgrade to access this part.
Upgrade NowTranscripts
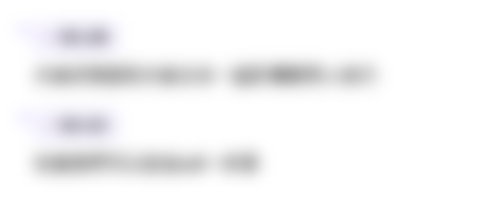
This section is available to paid users only. Please upgrade to access this part.
Upgrade NowBrowse More Related Video
5.0 / 5 (0 votes)