Final Gravel Pack
Summary
TLDRThis script discusses the critical aspects of drilling and completing horizontal wells, emphasizing the importance of understanding the process to mitigate risks. It highlights Dowell's tailored drilling fluids for minimal formation damage and the challenges of screen completions. The script introduces high-rate water packing and alternate path technologies for effective gravel packing in horizontal wells, which can prevent well failures and enhance production, ensuring a stable and long-lasting well performance.
Takeaways
- 🛠️ Comprehensive understanding of drilling and completing processes is crucial for horizontal wells due to high stakes and risks involved.
- 💧 Dowell offers tailored reservoir drilling fluids designed to minimize formation damage and suit specific well conditions.
- 🔍 Formation characteristics and completion techniques dictate the requirements for reservoir drilling fluids, emphasizing the importance of customization.
- 🚀 Excellent cuttings transport properties of Dowell's drilling fluids are vital for maintaining clean hole conditions before screen installation.
- 📊 Proper screen selection and sizing are critical to minimize problems in standalone screen completions, especially in formations with variable particle size distribution.
- 🔄 Thinned filter cakes should be easily removable to prevent hindrance to production after the well hole is conditioned.
- 🚫 Evidence suggests that hole collapse isn't always occurring in many wells, which can affect screen performance and production stability.
- 💡 High rate water packing is a method to eliminate well failures in horizontal wells, requiring a wellbore seal for successful gravel transport and settling.
- 🔄 The packing process involves an alpha wave that propagates towards the well's toe and a beta wave that completes the packing from toe to heel.
- 🛑 Incomplete packs due to high velocities or shale layer encounters can lead to water coning, premature water breakthrough, and loss of hydrocarbon reserves.
- 🔄 Alternate path technology, adapted for horizontal wells, uses viscosity instead of velocity for gravel packing, allowing for bypassing of bridges and complete interval packing.
Q & A
What is the significance of having a comprehensive understanding of the drilling and completing process when drilling a horizontal well?
-A comprehensive understanding of the drilling and completing process is crucial due to the high stakes and risks involved in drilling a horizontal well. It ensures that every event that occurs from the initial encounter with the formation can be managed properly to avoid altering the production and life of the well negatively.
What role do Dowell's reservoir drilling fluids play in the drilling process?
-Dowell's reservoir drilling fluids are tailored to suit specific well conditions and demonstrate minimal formation damage. They have excellent cuttings transport properties, which are essential for maintaining well integrity and ensuring the well's production efficiency.
Why is it important to leave the hole as clean as possible prior to running the screens?
-Leaving the hole as clean as possible before running the screens helps to minimize problems associated with standalone screen completions. Thinned filter cakes that are fully acidizable can be produced back through the sand screen, contributing to a more stable production rate with less risk of screen failure.
What are the challenges faced with standalone screen completions when the wellbore collapses onto a properly sized screen?
-While a stable production rate is usually observed when the wellbore collapses onto a properly sized screen, there is evidence that in many wells, the hole does not collapse as expected. This can lead to issues with screen plugging, excessive pressure drop, increased localized velocities, and erosion of the screen, potentially resulting in failure.
How does gravel packing of horizontal wells help in eliminating costly well failures?
-Gravel packing of horizontal wells provides an opportunity to create a stable and uniform filter cake that supports the wellbore and prevents sand production. This can eliminate the need for costly workovers and ensure the well's longevity and production efficiency.
What is a high rate water pack and why is it used for gravel packing a horizontal well?
-A high rate water pack is a completion method for gravel packing a horizontal well where gravel is added at low concentrations and transported with a high velocity. This method is used to quickly form a settled bed and propagate an alpha wave towards the toe of the well, ensuring a successful pack and preventing the formation of bridges that could lead to incomplete packing.
How does the use of sand cage software benefit the gravel packing process?
-Sand cage software can model the packing process, providing insights into how gravel will settle and how the alpha and beta waves will propagate. This helps in optimizing the gravel packing process and ensuring a complete and uniform pack throughout the well interval.
What are the common issues faced after a successful high rate water pack that may hinder production?
-Even after a successful high rate water pack, there may be issues with filter cake cleanup, which can hinder production. Operators often opt for post-acidizing treatments to enhance production, but the major problem is contacting the filter cake, which can lead to incomplete intervals being packed.
What is the alternate path technology and how does it differ from traditional gravel packing methods?
-The alternate path technology is an adaptation of gravel packing methods to meet the needs of horizontal applications. Unlike traditional methods that rely on velocity, alternate path technology uses viscosity to pack the annulus, allowing for bypassing of bridges and ensuring a complete pack even in the presence of varying downhole conditions.
How does the use of inflatable packers with the alternate path technology benefit long horizontal wells?
-Inflatable packers used with the alternate path technology allow for selective interval packing, which can be particularly useful in the later life of a well when water coning is present. This enables the isolation of the coning interval and continued production from other intervals, maximizing production and reserves.
What are the benefits of using the all pack system with the alternate path technology in long horizontal wells?
-The all pack system with alternate path technology ensures a tight gravel pack over the entire screen length, resulting in minimum drawdown and contributing to a long-lasting completion. It eliminates the potential for water coning, leading to higher production rates and more reserves being recovered.
Outlines
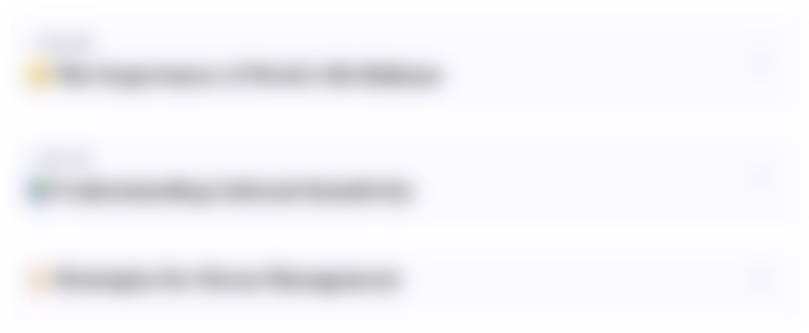
This section is available to paid users only. Please upgrade to access this part.
Upgrade NowMindmap
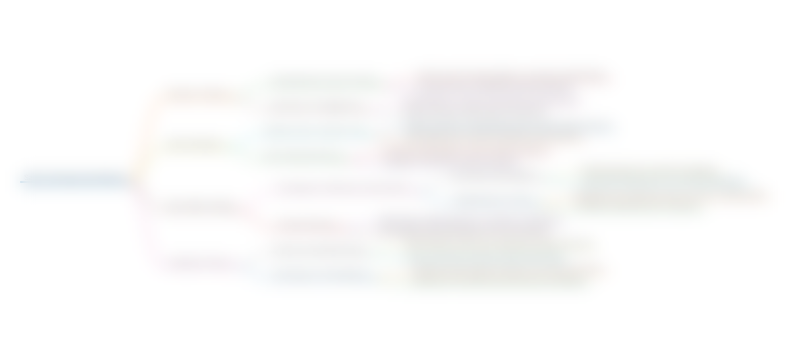
This section is available to paid users only. Please upgrade to access this part.
Upgrade NowKeywords
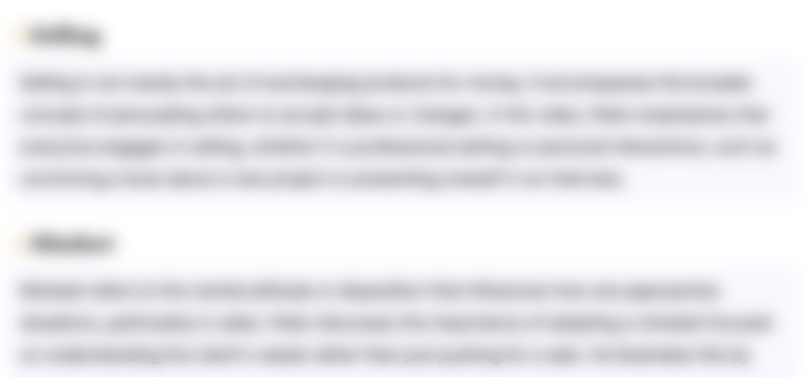
This section is available to paid users only. Please upgrade to access this part.
Upgrade NowHighlights
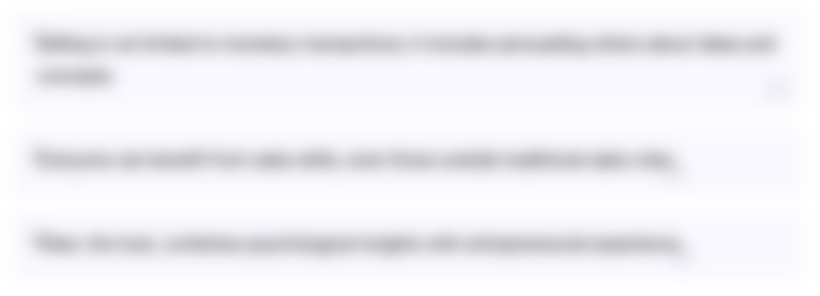
This section is available to paid users only. Please upgrade to access this part.
Upgrade NowTranscripts
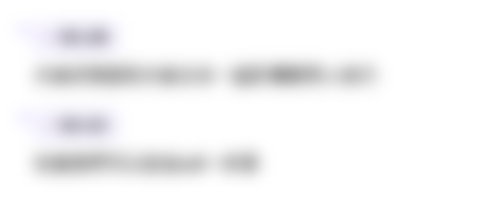
This section is available to paid users only. Please upgrade to access this part.
Upgrade Now5.0 / 5 (0 votes)