Motors 101
Summary
TLDRThis video delves into the workings of electric motors, which consume half of global electricity and power 70% of industry. Focusing on three-phase asynchronous AC induction motors, it explains their layout, components, and how they generate mechanical torque. It covers the stator and rotor interaction, the concept of slip, and the importance of motor design for different applications. The video also discusses motor efficiency, speed control, and the significance of the nameplate for technical specifications, emphasizing the need for careful management to maximize motor performance and efficiency.
Takeaways
- 🔌 Electric motors are responsible for approximately half of global electricity consumption and about 70% of industrial power use.
- 🚗 DC brushless motors are favored in electric vehicles due to their high torque and efficiency.
- 🔄 AC motors, which use alternating current, are more common and account for a significant portion of motor load in industrial power consumption.
- 🌀 The focus of the video is on three-phase asynchronous AC induction motors, which are prevalent in everyday applications like refrigeration and air conditioning units.
- 🏗️ The key components of an induction motor include the stator coils, rotor, and termination box for power input.
- 🔧 The rotor, also known as the armature, provides mechanical power output and is magnetically coupled to the stationary stator.
- 🔑 The motor shaft often has a key to prevent slippage within the load sleeve, ensuring proper mechanical connection.
- 📜 The nameplate on a motor provides crucial electrical and mechanical information necessary for operation and maintenance.
- 🌀 The operation of an induction motor relies on the generation of a rotating magnetic field by the stator, which induces a current in the rotor, creating torque.
- 🔌 The speed of the rotor is slightly less than the electrical frequency due to the slip, a measure of the difference in speed between the rotating magnetic field and the rotor.
- ⚙️ Induction motors are valued for their simple and robust design, which allows them to maintain a constant speed across a range of loads.
- 🔄 The design of the rotor, such as the squirrel cage rotor, influences the motor's mechanical performance, including starting torque and speed-torque characteristics.
- 🏢 Standard frame sizes and nameplate information, as set by organizations like NEMA, facilitate easy motor replacement and customization for specific applications.
- 📊 The nameplate also includes specifications like efficiency, power factor, voltage rating, and service factor, which are critical for understanding the motor's capabilities and limitations.
Q & A
What percentage of global electricity is consumed by electric motors?
-Electric motors consume around half of global electricity.
What percentage of industrial power consumption is attributed to electric motors?
-Electric motors are responsible for about 70% of industrial power consumption.
Why are DC brushless motors popular in electric vehicles?
-DC brushless motors are popular in electric vehicles because of their high torque and efficiency.
What type of motors are more common and make up most of the motor load in industrial power consumption?
-AC Motors are much more common and make up most of the motor load, being responsible for about 70% of industrial power consumption.
What specific type of AC Motors does the video focus on?
-The video focuses on three phase asynchronous AC induction motors.
What is the function of the termination box in a motor?
-The termination box is where the wires come in to provide three phase electric power to the motor.
How is the stator related to the rotor in an induction motor?
-The stator is magnetically coupled to the rotor but does not physically touch it. The stator remains stationary while the rotor rotates.
What is the role of the rotor in an induction motor?
-The rotor, sometimes called the armature, is the moving or rotating piece of the motor that provides the mechanical power output to the load through the shaft.
What is the purpose of the key and keyway on the motor shaft?
-The key and keyway ensure that the shaft doesn't slip inside the load sleeve, linking it with the load such as a fan or pump.
What is the phenomenon called when the rotor speed is slightly less than the electrical speed due to losses in the induction process?
-The difference in speed is called the slip.
Why is a variable frequency drive needed to change the speed of an AC motor?
-A variable frequency drive is needed to change the speed of a motor because AC Motors run at a fixed speed when directly connected to the electrical system.
What is the typical motor inrush current when started across the line?
-A typical motor inrush current when started across the line is six to eight times the rate at full load current.
What is the significance of the service factor in motor operation?
-The service factor is an overload rating at nameplate voltage and frequency, indicating the allowable overload for a motor. It is used for short periods and helps to compensate for low or unbalanced voltage supply.
What does the nameplate of a motor typically include, and why is it important?
-The nameplate includes necessary electrical and mechanical information such as frame designation, manufacturer's type, power rating, duty rating, max ambient temperature, insulation designation, service factor, speed, electrical frequency, phase, efficiency, power factor, and voltage rating. It is important for installation, operation, and maintenance of the motor.
Why might a motor run in the reverse direction if the power connection phases are swapped?
-You can reverse the direction of a motor by swapping two of the three phases of the incoming power connection. If the phasing is incorrect, it will cause the motor to spin in the opposite direction during startup.
How does the design of the rotor affect the motor's mechanical operation?
-The design of the rotor is very important as it influences how the motor will operate mechanically. Most induction machines have a squirrel cage rotor, and modifications to the shape and size of the conductors can minimize starting currents or vary the speed and torque relationship.
What is the difference between a squirrel cage rotor and a wound rotor?
-A squirrel cage rotor is made up of axial conduction bars and radial shorting rings, and it is the most common type due to its simplicity. A wound rotor, on the other hand, can be used for high starting torque but requires brushes and commutators.
Outlines
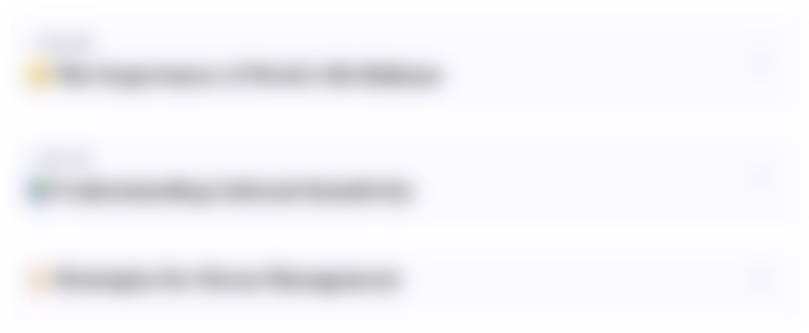
This section is available to paid users only. Please upgrade to access this part.
Upgrade NowMindmap
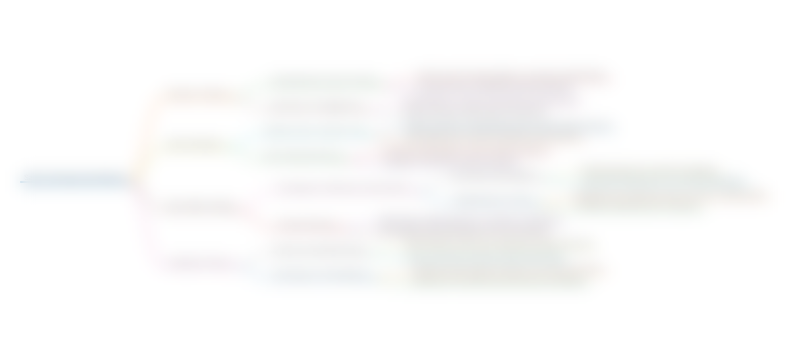
This section is available to paid users only. Please upgrade to access this part.
Upgrade NowKeywords
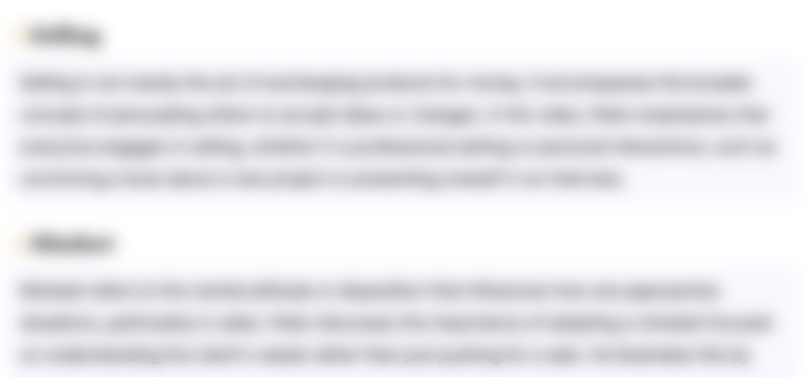
This section is available to paid users only. Please upgrade to access this part.
Upgrade NowHighlights
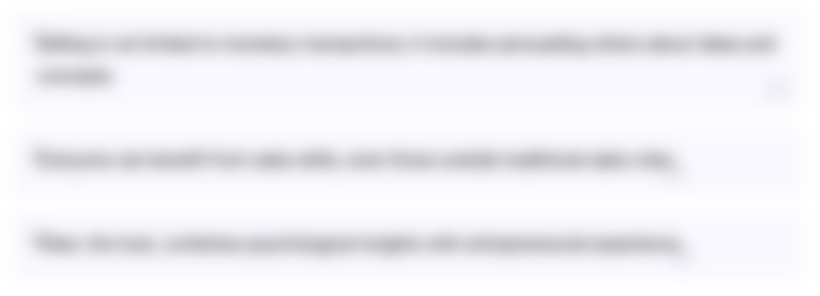
This section is available to paid users only. Please upgrade to access this part.
Upgrade NowTranscripts
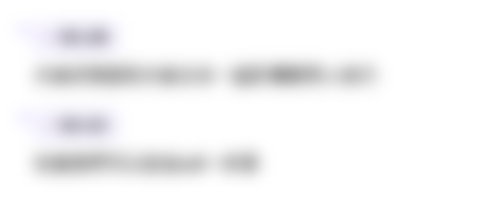
This section is available to paid users only. Please upgrade to access this part.
Upgrade NowBrowse More Related Video
5.0 / 5 (0 votes)