My Race Car Is Rust
Summary
TLDRThe transcript describes disassembling a land speed car after subjecting it to corrosive salt water at the Bonneville Salt Flats. Despite attempts to protect components, saltwater seeped in and caused corrosion. A toolkit was created during disassembly to aid reassembly. Many parts needed replacing due to corrosion damage including wheel bearings, steering components, engine parts, fasteners, and brake lines. The frame was media blasted and painted for protection. New locator cups were welded to the frame and trailer to ease loading. Electronic components were relocated and rewired. A new throttle by wire system improved throttle feel. Lessons were learned about properly sealing and protecting components for future land speed events.
Takeaways
- ๐ฅ The salt spray test simulates many years of corrosion in just a few hours, rapidly deteriorating metal components and coatings.
- ๐ Driving a car in the Bonneville Salt Flats, especially when wet, can accelerate corrosion, packing years of wear into just a few days.
- ๐ฅ Exposing a car to salt without proper protection leads to extensive salt penetration and corrosion, necessitating a complete disassembly and rebuild.
- ๐ Keeping track of tools used during disassembly can help assemble a dedicated toolkit for the car, ensuring all necessary tools are available for reassembly.
- ๐ง Certain parts like front wheel bearings and steering components are particularly vulnerable to salt damage and may require special attention or replacement.
- ๐ซ It's critical to use proper lubrication and protection against corrosion for key components, such as using grease in zerk fittings to prevent seizing.
- ๐ฑ Adopting modern solutions, like throttle by wire systems, can improve functionality and reduce mechanical complexity.
- ๐ป Utilizing digital tools and technologies, such as 3D printing, can aid in creating custom parts and adapters, despite the potential for maintenance and errors.
- ๐ Proactive maintenance and immediate cleaning after exposure to corrosive environments can significantly prolong a vehicle's lifespan.
- ๐ฉ Design modifications, like adding body panels and sealing off wheel wells, can help minimize future corrosion and extend the vehicle's usability.
Q & A
What is the purpose of the salt spray test mentioned in the video script?
-The salt spray test is used to assess the long-term durability and corrosion resistance of metals and coatings by simulating many years of corrosion in just a few hours.
Why is driving a car on the Bonville Salt Flats, especially when wet, compared to an accelerated corrosion test?
-Driving on the Bonville Salt Flats when wet exposes the car to salt water, which gets into every crack and crevice, accelerating corrosion and mimicking many years of wear in just a few days.
What was the consequence of not immediately cleaning the car after exposure to salt?
-The consequence was that the car continued to corrode under the table where it was stored, highlighting the importance of prompt and thorough cleaning to prevent corrosion.
What approach was taken to disassemble the car, and why was it necessary?
-The approach involved calling an overqualified intern, Dave, for help, tracking the tools used for disassembly to create a toolkit, and fully disassembling the car for a total rebuild to address corrosion damage.
How did the front suspension and wheel bearings fare against the salt exposure, and what was the planned solution?
-The front suspension and wheel bearings suffered significantly due to inadequate protection and grease, leading to the decision to replace them with sealed roller bearings packed with grease.
What issues were encountered with the steering mechanism, and how were they addressed?
-The steering mechanism was severely corroded, requiring the use of a press to disassemble it. The issue was attributed to a lack of lubrication, and a plan was made to ensure proper greasing in the future.
What modifications were made to the car's toolkit, and why?
-A toolkit was assembled based on the disassembly process, excluding tools not used and adding a wiring fix kit, to ensure all necessary tools were available for reassembly and future repairs.
How did the ceramic coating on the exhaust and other coatings on fasteners hold up to salt exposure?
-The ceramic coating on the exhaust and other coatings on fasteners showed varying degrees of corrosion, with some coatings performing better than others in resisting salt-induced damage.
What novel approach was taken for securing the car to the trailer, and why was it considered necessary?
-Cup and Cone locators were added to secure the car on the trailer more effectively, facilitating easier loading and unloading while providing stability during transport.
What challenges were faced with the throttle system, and how were they resolved?
-The original mechanical throttle system had poor feel due to long and curved cable routing. It was replaced with a throttle-by-wire system for improved packaging and throttle response.
Outlines
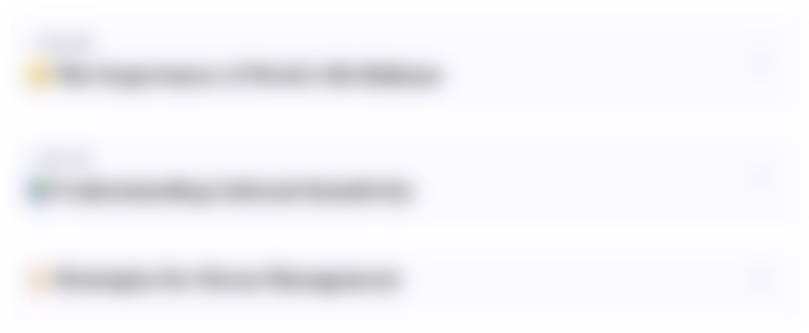
This section is available to paid users only. Please upgrade to access this part.
Upgrade NowMindmap
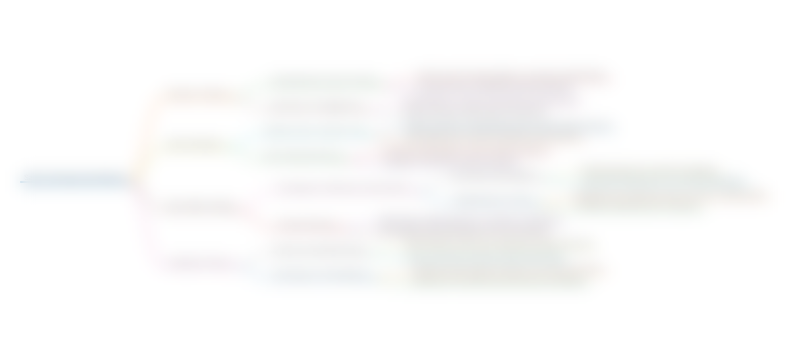
This section is available to paid users only. Please upgrade to access this part.
Upgrade NowKeywords
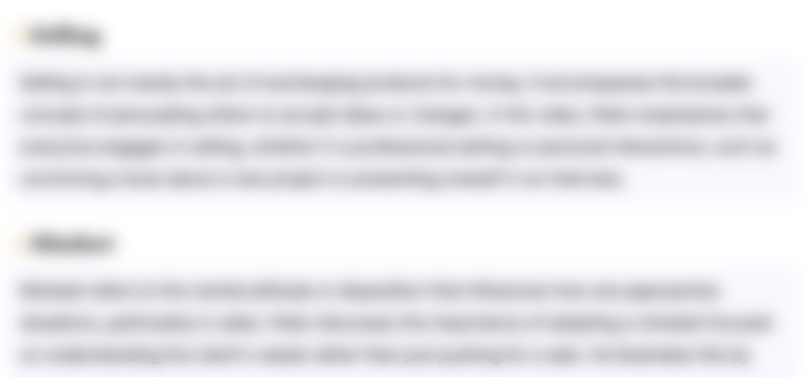
This section is available to paid users only. Please upgrade to access this part.
Upgrade NowHighlights
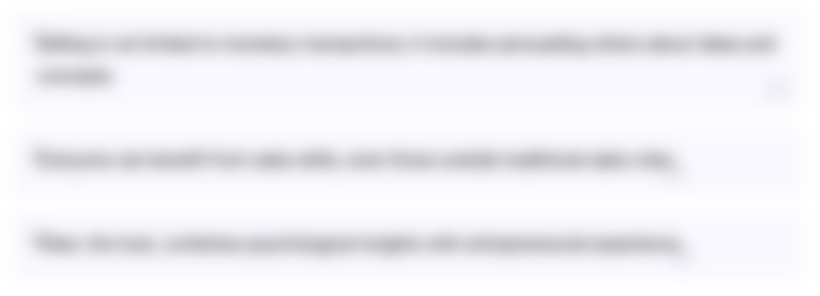
This section is available to paid users only. Please upgrade to access this part.
Upgrade NowTranscripts
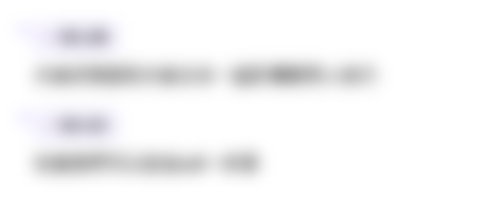
This section is available to paid users only. Please upgrade to access this part.
Upgrade Now5.0 / 5 (0 votes)