Persiapan Penerapan Warehouse Management System (WMS) | Life At Rapier Eps.5
Summary
TLDRIn this video, the team discusses the implementation of a new warehouse system to replace the manual processes currently in place at a customer's warehouse. They explain the steps of the system, from inventory management to order fulfillment, highlighting its advantages, such as improved efficiency and minimized errors. The video also covers the challenges faced in the current manual system, including stock discrepancies and delays in order delivery. By transitioning to the new system, the team aims to optimize warehouse operations and improve customer satisfaction through better monitoring and faster processing.
Takeaways
- 😀 The company is working on implementing an automated warehouse system to replace the existing manual process.
- 😀 The system aims to simplify tasks, reduce administrative input, and improve efficiency through automation.
- 😀 The warehouse has a large space with 1000 square meters dedicated to storage, with multiple levels for optimized item storage.
- 😀 The warehouse operations currently handle about 51-100 units per day for outbound shipments, and 3-4 full container loads per month.
- 😀 The system upgrade involves the use of serial numbers and barcode scanning to streamline inventory management.
- 😀 The company hopes the new system will reduce errors, such as stock discrepancies and wrong shipments, which have been common with manual processes.
- 😀 Inventory counting (opname) is done monthly, but the process can be slow due to lack of proper rack numbering in the past.
- 😀 The company plans to improve outbound logistics, ensuring products are properly inspected and ready for delivery before being sent to customers.
- 😀 Driver responsibilities extend beyond delivery to include warehouse tasks, making them multifunctional in the operations.
- 😀 A primary concern with the manual system is the loss of goods or mix-ups during delivery, which the new system aims to address by providing better monitoring tools.
Q & A
What is the main goal of the warehouse project described in the transcript?
-The main goal of the warehouse project is to migrate from a manual system to an automated one, which will help streamline processes, improve efficiency, and reduce the time spent on administrative tasks.
What is the role of Mas Ari in the warehouse system implementation?
-Mas Ari's role is to oversee the implementation of the new warehouse system, ensuring the proper operation of the inbound and outbound goods, managing stock levels, and facilitating the transition to the new automated system.
How does the new system improve the process of tracking inventory?
-The new system improves inventory tracking by using QR codes and serial numbers, allowing users to scan items for automatic updates in the system rather than manually entering data, thus speeding up the process and reducing human error.
What kind of system is being implemented in the warehouse?
-An automated warehouse management system is being implemented, which includes scanning QR codes and serial numbers to streamline the inventory management process and reduce manual input.
What are some challenges faced in the current manual system?
-The current manual system leads to inefficiencies, such as slower inventory tracking, potential human error, and time-consuming administrative tasks. Stock discrepancies and difficulties in monitoring orders are also significant challenges.
How will the new system affect outbound and inbound goods?
-The new system will make the process of handling inbound and outbound goods more efficient by automating the recording of goods, providing clearer visibility on stock levels, and reducing errors in stock management and order fulfillment.
What is the concern regarding barcode scanning in the new system?
-The primary concern with barcode scanning is ensuring that barcodes do not become an issue, such as being misplaced or unreadable, which could disrupt the efficiency of the new system.
How often does the warehouse perform stock checks, and how does the new system address this?
-Stock checks are performed once a month, but the process is time-consuming due to the manual nature of the system. The new system aims to make this process more efficient by automating stock tracking and providing real-time updates.
How is the shipping process managed in the warehouse?
-The shipping process involves drivers who first pick up goods from the warehouse and transport them to a buffer warehouse for quality checks. After the goods are inspected, they are shipped to the end customer, usually within 1-2 days.
What are the main concerns about warehouse operations before the new system?
-Before the new system, the main concerns were stock discrepancies, missing goods, wrong shipments, and delays in monitoring orders. The goal of the new system is to minimize these issues and improve overall efficiency.
Outlines
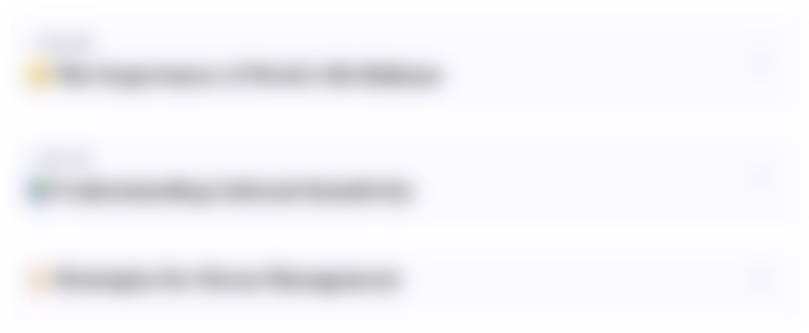
This section is available to paid users only. Please upgrade to access this part.
Upgrade NowMindmap
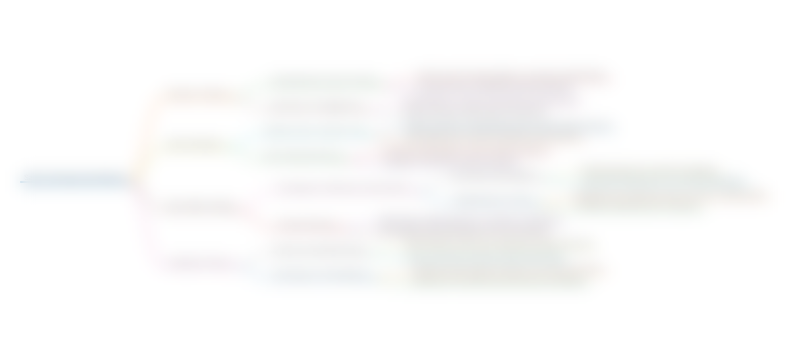
This section is available to paid users only. Please upgrade to access this part.
Upgrade NowKeywords
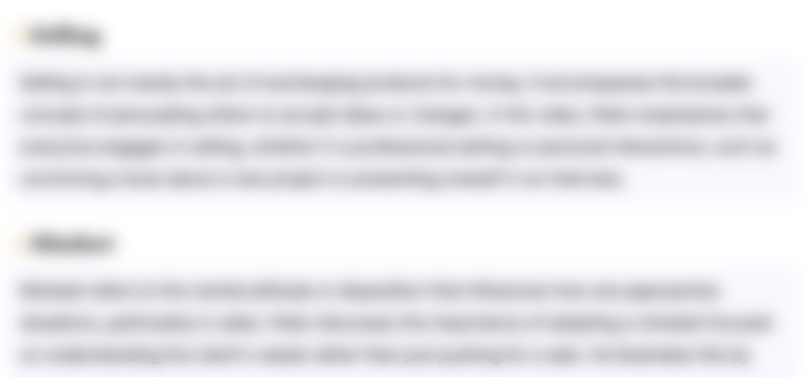
This section is available to paid users only. Please upgrade to access this part.
Upgrade NowHighlights
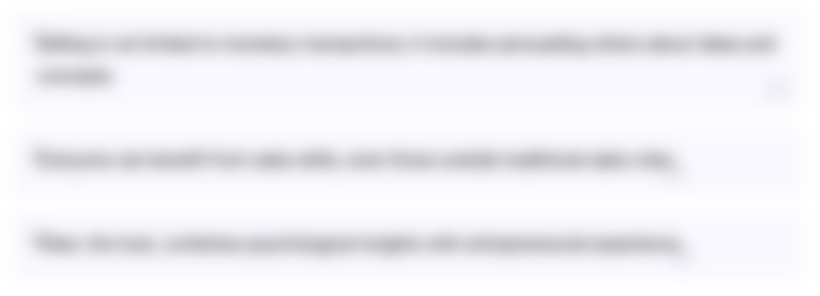
This section is available to paid users only. Please upgrade to access this part.
Upgrade NowTranscripts
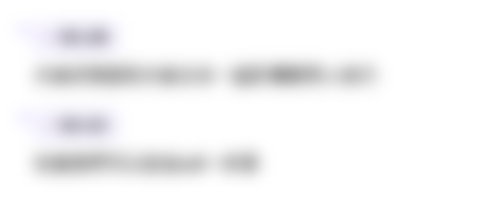
This section is available to paid users only. Please upgrade to access this part.
Upgrade NowBrowse More Related Video

Overview and basics of SAP Warehouse Management

The Barcode Warehouse, TagworX and Zebra Avant case study
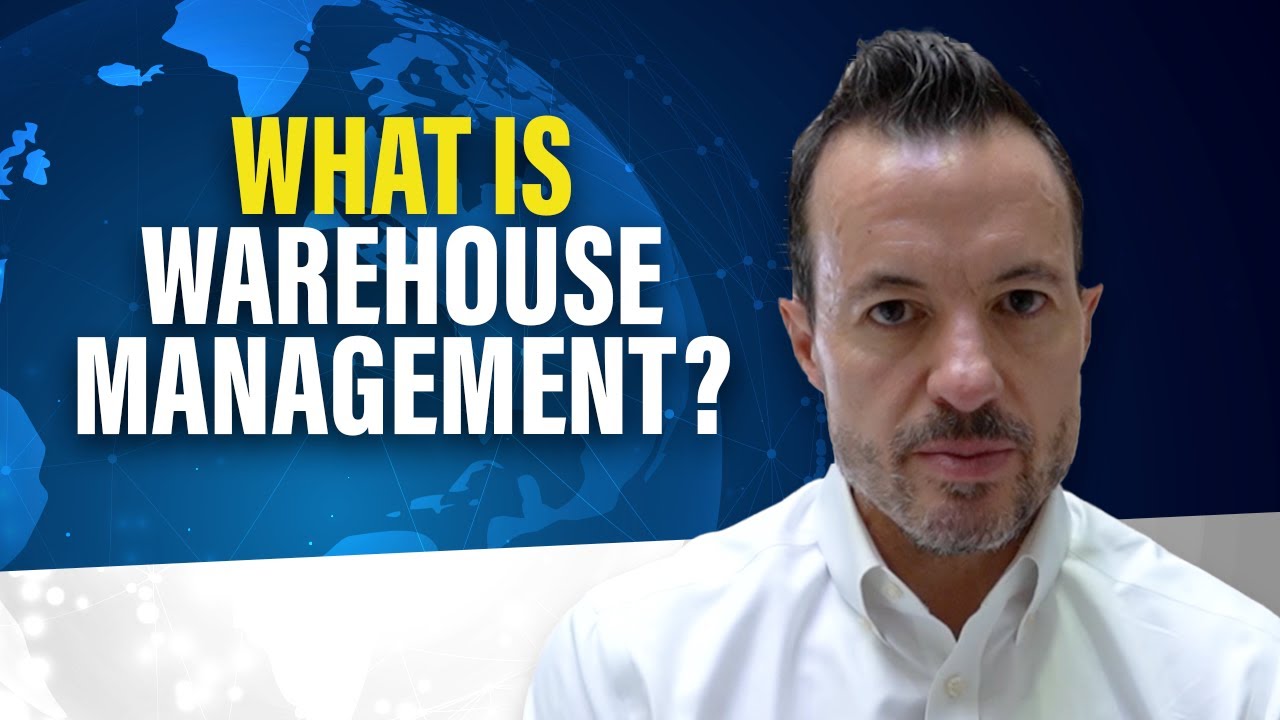
What is Warehouse Management? [Intro to Inventory Management, Pick Pack Ship, WMS Software, etc]

FUNCIONES del ALMACÉN - Administración EFECTIVA de Almacenes y Control de Inventarios - Video 3
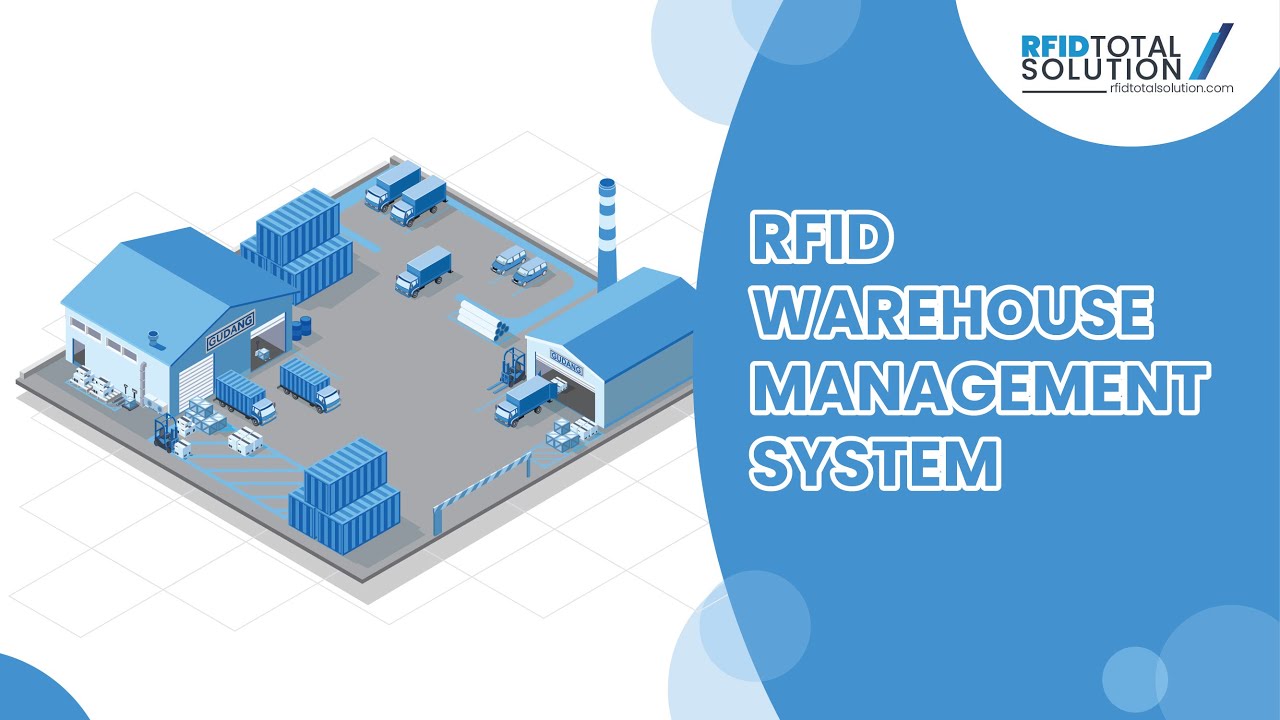
RFID Warehouse Management

Gudang Modern BGR Logistics Palembang
5.0 / 5 (0 votes)