Staff PPIC, Apa Jobdesk nya, Aktivitas nya & Skill yang dibutuhkan
Summary
TLDRThis video explains the crucial role of a PPIC (Production Planning and Inventory Control) staff in the manufacturing industry. The PPIC department is responsible for production planning, forecasting demand, scheduling, and inventory management to ensure smooth production operations. Key responsibilities include coordinating with sales, calculating production capacity, managing raw materials, and monitoring stock levels. Essential skills for PPIC staff include understanding production processes, data analysis, inventory control, forecasting, and problem-solving. The video emphasizes the importance of both technical and interpersonal skills for effective production and inventory management in manufacturing.
Takeaways
- 😀 PPIC stands for Production Planning and Inventory Control, which is responsible for production planning and inventory management in manufacturing.
- 😀 PPIC ensures the smooth operation of production by forecasting customer demand, scheduling production, and managing inventory levels.
- 😀 The PPIC department handles two major functions: production planning and inventory control, ensuring that products are produced efficiently and meet market demand.
- 😀 Key responsibilities of PPIC staff include calculating customer demand, determining production capacity, and creating production schedules.
- 😀 PPIC staff collaborate with the sales/marketing department to forecast customer demand and adjust production accordingly.
- 😀 Effective production planning requires PPIC staff to determine optimal raw material levels, create daily, weekly, and monthly production schedules, and monitor actual production performance.
- 😀 PPIC staff must also ensure the accuracy of inventory levels by conducting regular stock audits and monitoring material consumption.
- 😀 Essential hard skills for PPIC staff include proficiency in production processes, production planning methods (MRP), data analysis, and knowledge of ERP software like SAP or Oracle.
- 😀 Soft skills required for PPIC staff include effective communication, problem-solving, time management, attention to detail, teamwork, and adaptability to production changes.
- 😀 Adherence to quality management standards (e.g., ISO 9001) is a critical aspect of the PPIC staff’s role to ensure production meets industry standards.
- 😀 PPIC staff play a crucial role in ensuring products are delivered on time and production runs smoothly by addressing potential issues quickly and effectively.
Q & A
What does PPIC stand for, and what is its primary responsibility?
-PPIC stands for Production Planning and Inventory Control. Its primary responsibility is to ensure that production runs according to plan, manages raw material and product inventories, and coordinates with various departments to meet customer demands.
What are the two main functions of the PPIC department?
-The two main functions of the PPIC department are Production Planning and Inventory Control.
How does PPIC contribute to production planning?
-PPIC contributes to production planning by forecasting customer demand, calculating production capacity, determining material requirements, and creating production schedules that align with customer demand and inventory levels.
What is the importance of inventory control within PPIC?
-Inventory control is crucial within PPIC as it ensures that raw materials and finished products are stocked at optimal levels, preventing shortages or overstock situations that could disrupt production and meet customer delivery targets.
What are some of the key tasks a PPIC staff member performs in production planning?
-A PPIC staff member performs tasks such as forecasting customer demand, calculating production capacity, creating production schedules, monitoring production progress, and generating production reports.
What skills are necessary for managing inventory control effectively?
-To manage inventory control effectively, a PPIC staff member needs to be proficient in monitoring stock levels, performing regular stock checks, optimizing inventory levels, and identifying discrepancies between actual material usage and the bill of materials.
What is 'snop sales and operation planning' in the context of PPIC?
-SNOP (Sales and Operations Planning) is a meeting where PPIC coordinates with sales and marketing to forecast customer demand, ensuring that production planning aligns with those projections.
Why is it important for PPIC staff to collaborate with other departments like purchasing and production?
-Collaboration with other departments like purchasing and production is essential for PPIC staff to ensure that the necessary raw materials are available for production on time, and that production schedules align with actual production capacity and demand.
What are the key hard skills required for a PPIC staff member?
-Key hard skills include an understanding of the production process, proficiency in production planning methods (like MRP), inventory management, data analysis, software proficiency (e.g., SAP or Oracle), and knowledge of quality management systems like ISO 9001.
What soft skills are essential for a successful PPIC staff member?
-Essential soft skills include effective communication, problem-solving, time management, attention to detail, teamwork, and adaptability to changes in production schedules or customer demands.
Outlines
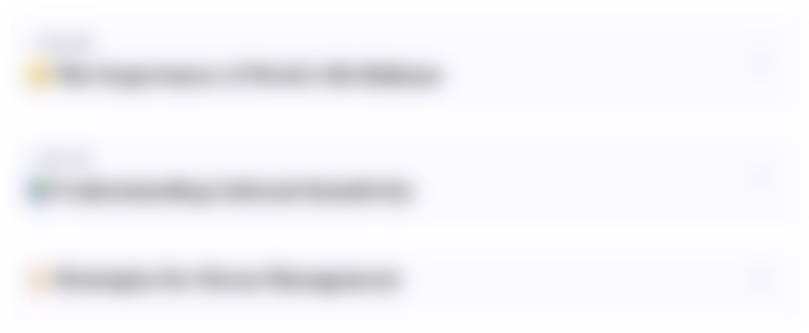
This section is available to paid users only. Please upgrade to access this part.
Upgrade NowMindmap
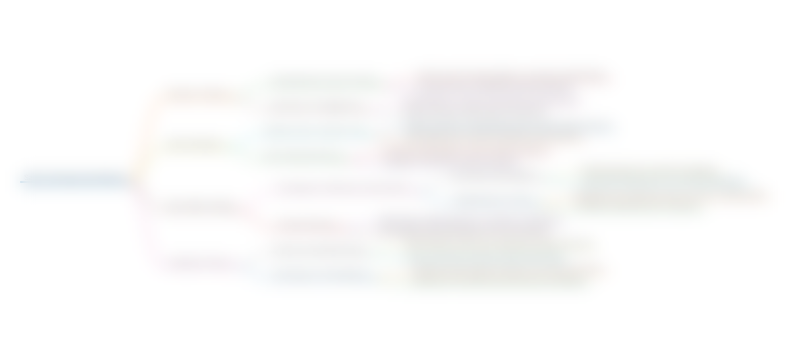
This section is available to paid users only. Please upgrade to access this part.
Upgrade NowKeywords
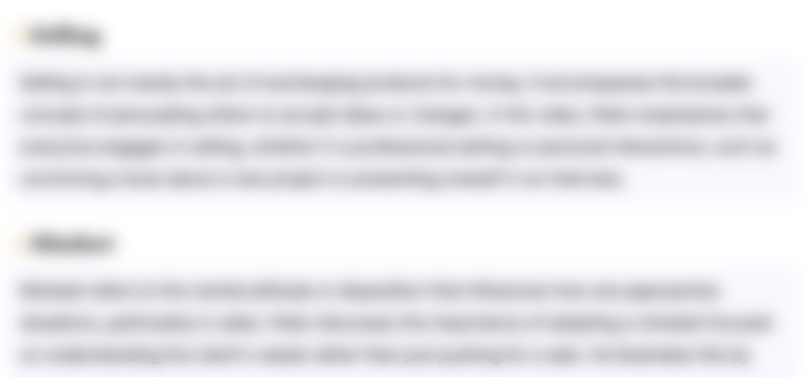
This section is available to paid users only. Please upgrade to access this part.
Upgrade NowHighlights
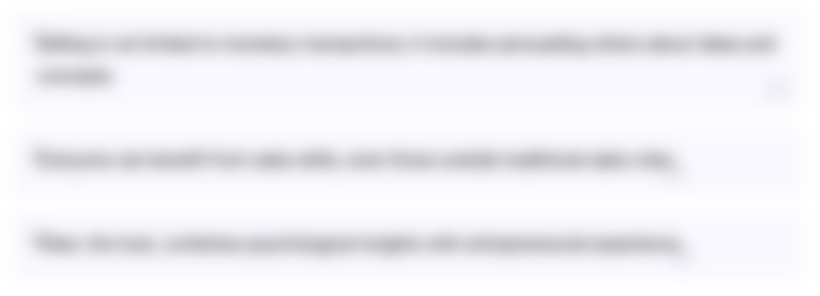
This section is available to paid users only. Please upgrade to access this part.
Upgrade NowTranscripts
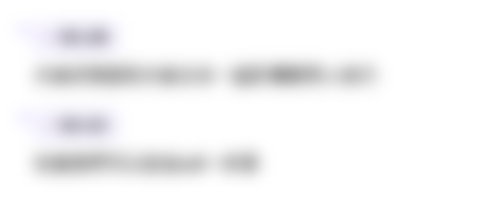
This section is available to paid users only. Please upgrade to access this part.
Upgrade NowBrowse More Related Video
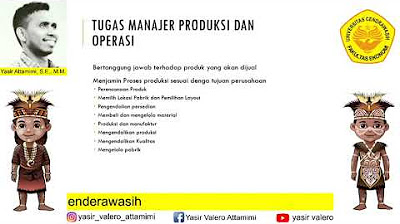
Materi kuliah Pengantar Bisnis, Pertemuan Ke-5
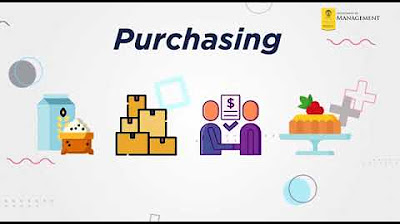
Pengantar Bisnis Sesi 11 Produksi dan Manajemen Operasi

UNDERSTAND MANUFACTURING ACCOUNTS WITHIN 10 MINUTES!!!
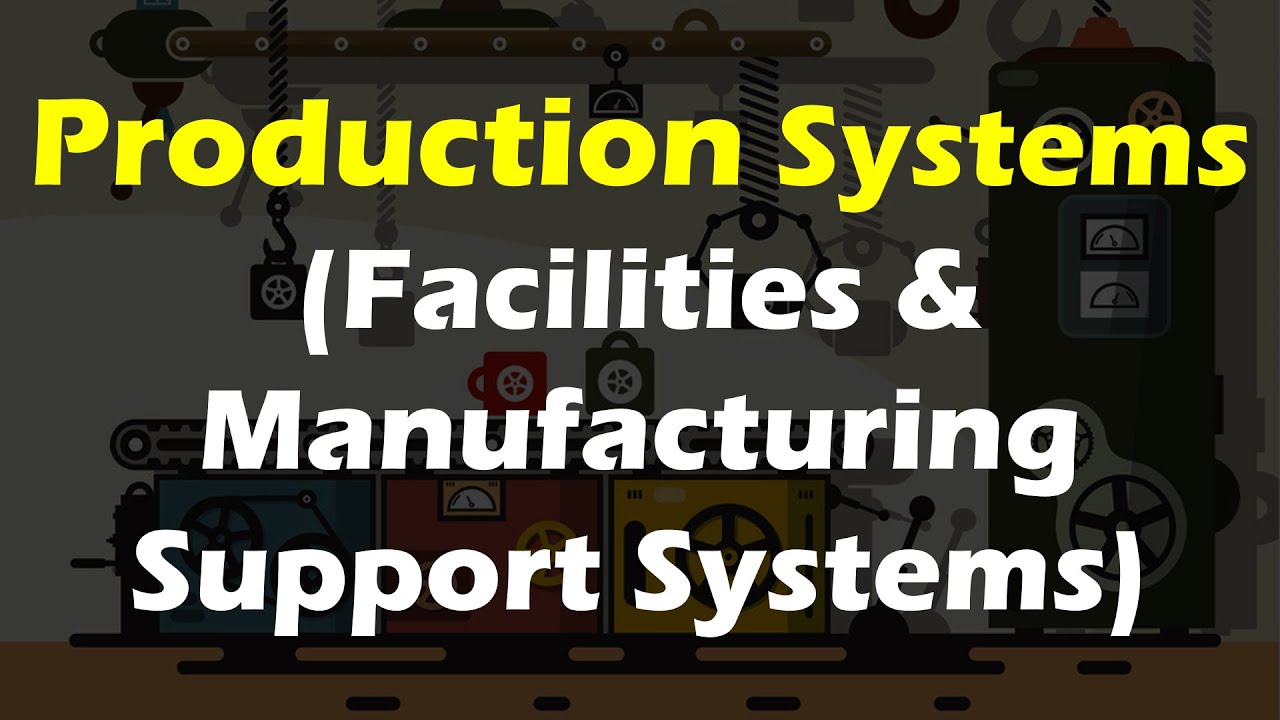
Production Systems - Facilities & Manufacturing Support Systems
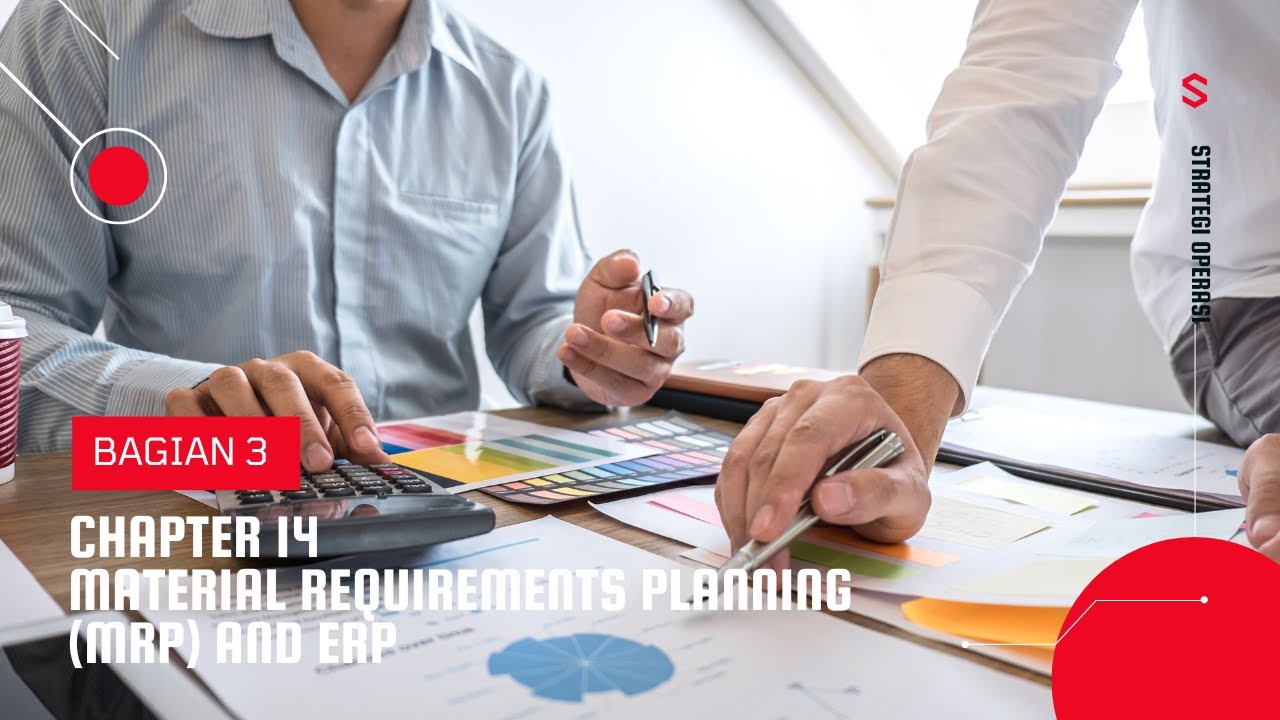
Chapter 14. Material Requirements Planning (MRP) and ERP - Part 3

What is the Material Requirement planning (MRP)? | MRP Process
5.0 / 5 (0 votes)