Program CNC Turning Menggunakan MasterCAM X9 (Pembuatan PIN)
Summary
TLDRThis video provides a detailed tutorial on using Mastercam X9 for designing and machining a workpiece. It covers the entire process from opening the software, setting up the machine and tool parameters, to creating designs and simulating operations. The video walks through drawing lines, defining workpieces, setting spindle speeds, and performing cutting operations such as facing, turning, and threading. After completing the simulations, the tutorial demonstrates how to generate and save the CNC program to execute the design. This guide is essential for users looking to understand Mastercam X9's features and machining techniques.
Takeaways
- 😀 The tutorial starts with opening Mastercam X9 software and selecting the appropriate settings for the project, including choosing the plane and tool diameter.
- 😀 The user is guided to create a basic design by first drawing a line with specific dimensions and coordinates.
- 😀 The first drawing step involves creating a 12 mm diameter line at a certain Y-coordinate (0.3) to form the shape needed for the project.
- 😀 The next step is to create a line with a 12 mm diameter extending 10 units to the left, completing the basic shape of the workpiece.
- 😀 The user selects a CNC machine and sets the properties for the machine, including spindle settings and stock setup for the workpiece.
- 😀 The stock size is automatically detected as 60 mm in diameter and 90 mm in length, with an additional allowance for part removal.
- 😀 The first machining operation is flashing, where a face operation is set up with a specific tool number, speed, and feed rates.
- 😀 For turning operations, the correct tool and parameters are selected, and the cutting depth, speed, and feed rates are adjusted for efficient cutting.
- 😀 The process continues with the creation of grooves, selecting the right tool and adjusting cutting parameters for smooth operation.
- 😀 The simulation feature is used to verify the machining process, ensuring the desired result matches the workpiece design before actual machining begins.
Q & A
What is the first step in using Mastercam X9 for machining?
-The first step is to open the Mastercam X9 software by double-clicking on its icon. This will display the initial screen where you can begin your work.
How do you set up the WCS (Work Coordinate System) in Mastercam X9?
-To set up the WCS, you need to select 'plan' and then 'LED'. You use the +D +Z option to define the WCS, which allows you to set the correct orientation for the part being machined.
What is the purpose of defining a diameter in the drawing process?
-Defining the diameter in the drawing process ensures that the part is accurately modeled with the correct dimensions, allowing for precise machining operations.
What machine type should be selected for this particular job in Mastercam X9?
-The machine type selected in this process is an LED machine, and the machine list is chosen based on the design specifications of the part.
What is the significance of the 'Spindle' option in the setup?
-The 'Spindle' option is crucial for determining the rotation of the cutting tool during machining. It is configured under the 'Stock Setup' section to define the workpiece's dimensions and machining parameters.
How is the stock material size determined in Mastercam X9?
-The stock material size is determined by selecting 'Make from Two Points,' which allows you to specify the start and end points of the workpiece, automatically calculating the diameter and length of the stock.
What is the importance of the 'Face Milling' operation in this tutorial?
-The 'Face Milling' operation is essential for smoothing the top surface of the workpiece. It prepares the surface for further operations by removing excess material.
What cutting tool parameters are adjusted for the roughing operation?
-In the roughing operation, parameters such as tool number, spindle speed (RPM), and feed rate are adjusted. The cutting depth is also defined to ensure optimal material removal without damaging the part.
Why is a finishing operation important in Mastercam X9?
-A finishing operation is important for achieving a high-quality surface finish on the part. It uses finer tool settings and more precise cutting depths to ensure the part meets the required specifications.
What is the function of the 'Groove' operation in this process?
-The 'Groove' operation is used to create specific grooves or channels on the workpiece. It involves defining the tool path and parameters, such as direction and depth, to ensure the grooves are formed accurately.
How do you simulate the machining process in Mastercam X9?
-To simulate the machining process, you select all operations and use the 'Verify' function. This will show a visual representation of how the part will be machined, allowing you to check for errors or necessary adjustments before actual machining.
What steps are involved in generating the G-code for the part?
-After simulating the machining process, you can generate the G-code by selecting the 'Post Operation' option. The G-code is then saved and can be edited to adjust specific parameters like tool numbers and spindle speeds before sending it to the CNC machine.
Outlines
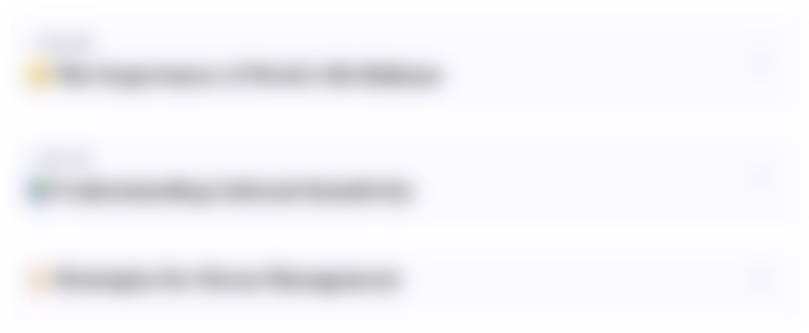
This section is available to paid users only. Please upgrade to access this part.
Upgrade NowMindmap
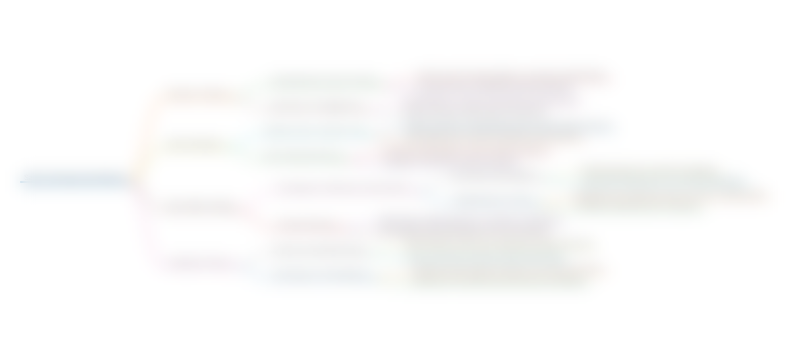
This section is available to paid users only. Please upgrade to access this part.
Upgrade NowKeywords
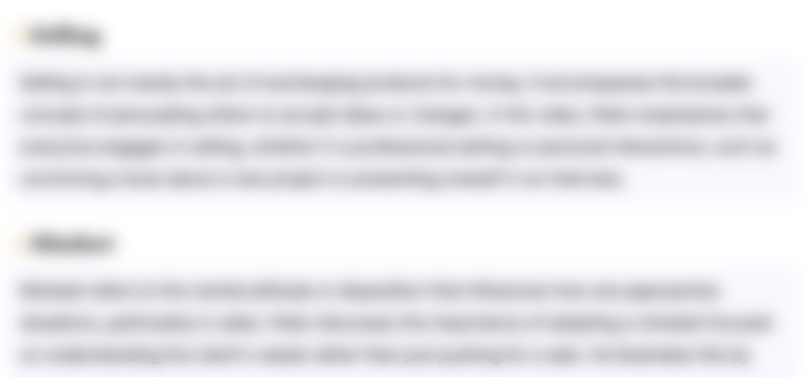
This section is available to paid users only. Please upgrade to access this part.
Upgrade NowHighlights
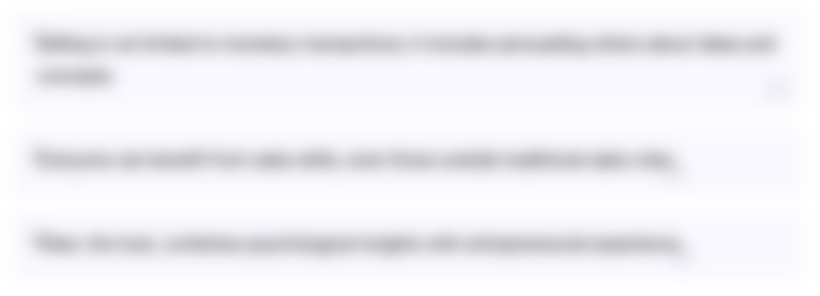
This section is available to paid users only. Please upgrade to access this part.
Upgrade NowTranscripts
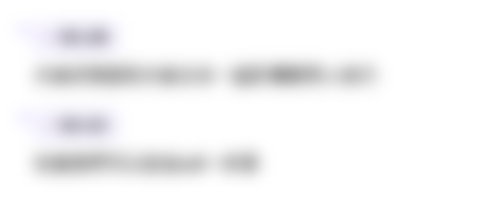
This section is available to paid users only. Please upgrade to access this part.
Upgrade NowBrowse More Related Video
5.0 / 5 (0 votes)