MASTERCAM X5_BUBUT DASAR BIDANG BERTINGKAT
Summary
TLDRThis video lesson provides an in-depth tutorial on CNC machining, focusing on the use of Mastercam X5 for designing and programming parts. It covers the entire process, from basic design concepts such as dimensions and diameters to tool path creation for milling and turning operations. The instructor demonstrates key features of Mastercam X5, including operation management, tool settings, and post-processing to generate G-code. The tutorial also explains machine setup, tool selection, and simulating the machining process to ensure accuracy before executing the program on a CNC machine.
Takeaways
- π Mastercam X5 is introduced as a software tool for creating CNC machine code from design sketches.
- π The importance of understanding the dimensions and diameters of the object being machined is emphasized, as it directly impacts the design process in Mastercam.
- π The process begins by defining coordinates and drawing the basic shape using Mastercam's design tools.
- π Offset commands are used to create precise and repeated shapes based on set dimensions (e.g., diameter, length).
- π The trimming operation helps eliminate unnecessary lines, refining the design to focus only on the essential areas.
- π Fillet and chamfer operations are demonstrated, showing how to add rounded corners and smooth transitions between intersecting lines.
- π After completing the design, machine selection is crucial, with the example highlighting the use of a lathe (bubut) for cylindrical objects.
- π Toolpath creation, including roughing (roksin) and finishing operations, is explained as the main process for machining the object.
- π A detailed explanation of CNC lathe programming is given, highlighting the importance of correct tool settings, spindle speed, and cutting depths.
- π Post-processing is covered, explaining how to convert the toolpath into machine-readable code that will be executed on the CNC machine.
- π The final step involves loading the CNC program onto the machine, running a simulation, and ensuring everything works before execution.
Q & A
What is Mastercam X5, and how is it used in CNC machining?
-Mastercam X5 is a Computer-Aided Design (CAD) and Computer-Aided Manufacturing (CAM) software used to create designs and convert them into machine-readable programming code. It is primarily used for CNC machining, including lathe operations, by generating tool paths for the machining process.
Why is the diameter input in Mastercam X5 only half of the actual object diameter?
-In Mastercam X5, only half of the diameter is entered because the software assumes that the object is symmetric. This simplification reduces complexity and allows for easier and more efficient design input.
What is the purpose of the 'Operation Manager' in Mastercam X5?
-The 'Operation Manager' in Mastercam X5 helps manage and organize various machining operations. It allows users to monitor and control different toolpaths, setups, and machine parameters during the CNC machining process.
How do you set up the coordinates in Mastercam X5 for drawing an object?
-In Mastercam X5, you can set up the coordinates by pressing 'EP9' on the keyboard, which brings up the coordinate grid. The X-axis is for horizontal movements, and the Y-axis is for vertical movements. This helps in placing the design correctly on the workspace.
What role do offsets play in drawing with Mastercam X5?
-Offsets in Mastercam X5 allow users to create parallel or mirrored lines based on a specified distance. This tool is useful for designing symmetrical or evenly spaced features on the object being machined.
What is the purpose of the 'Trim' tool in Mastercam X5?
-The 'Trim' tool in Mastercam X5 is used to remove unnecessary lines or parts of the design. It helps clean up the drawing by eliminating unwanted elements, ensuring that only the required sections remain for machining.
Why do we use a lathe (bubut) machine for cylindrical shapes in machining?
-Lathe machines are ideal for cylindrical shapes because they rotate the workpiece while a cutting tool is applied. This allows for precise shaping of round objects, such as shafts and discs, by removing material layer by layer.
What are the two main methods of machining explained in the transcript?
-The two main methods of machining discussed are roughing (or rapping), which removes material in large amounts, and finishing, which refines the surface to the desired quality. Roughing is done first, followed by finishing for smooth results.
How do you set up the tool parameters for CNC machining in Mastercam X5?
-To set up tool parameters in Mastercam X5, you need to select the appropriate tool, define the spindle speed (RPM), feed rate, and cutting depth. These parameters are essential for controlling the machining process and ensuring accurate results.
What is the significance of post-processing in CNC machining?
-Post-processing in CNC machining involves converting the tool paths created in Mastercam into machine-readable G-code. This process generates the final programming code that instructs the CNC machine how to perform the required operations on the workpiece.
Outlines
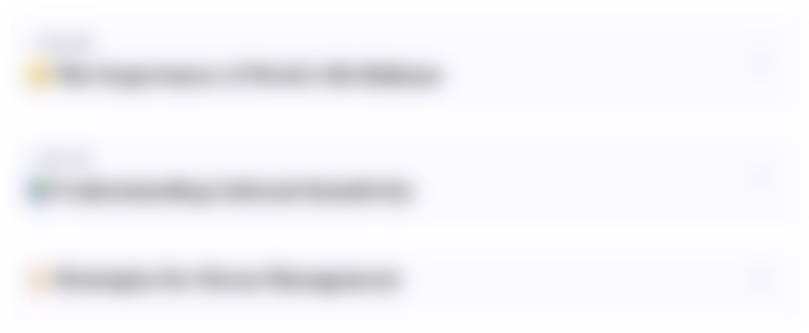
This section is available to paid users only. Please upgrade to access this part.
Upgrade NowMindmap
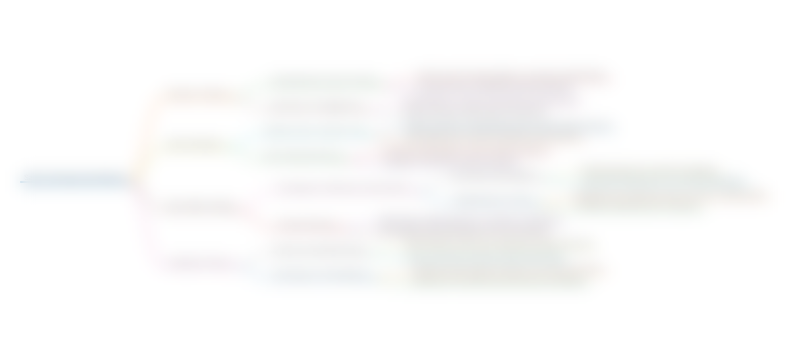
This section is available to paid users only. Please upgrade to access this part.
Upgrade NowKeywords
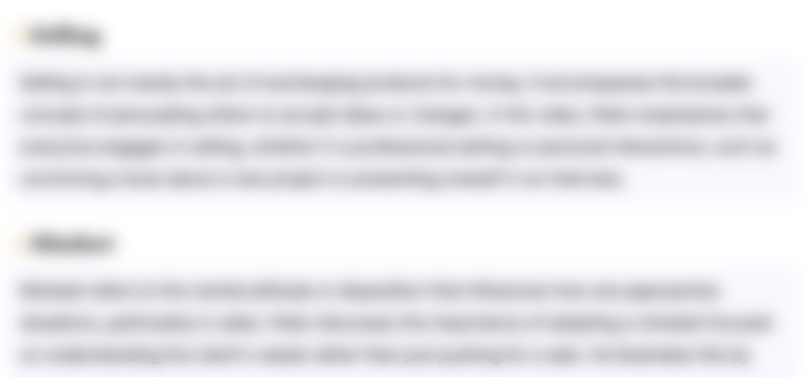
This section is available to paid users only. Please upgrade to access this part.
Upgrade NowHighlights
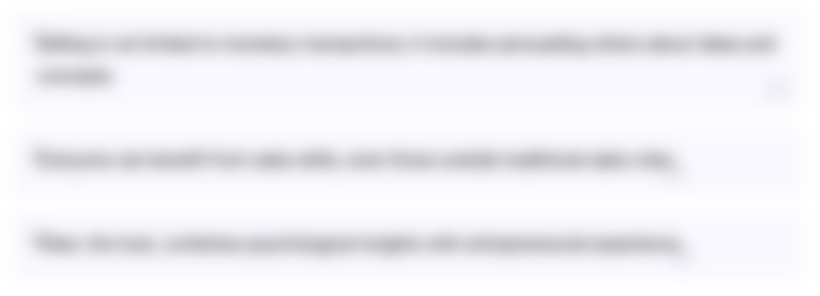
This section is available to paid users only. Please upgrade to access this part.
Upgrade NowTranscripts
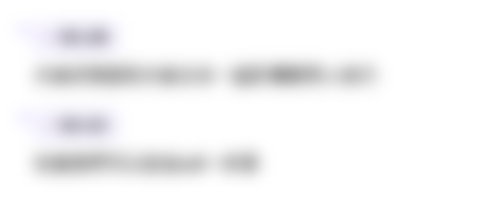
This section is available to paid users only. Please upgrade to access this part.
Upgrade NowBrowse More Related Video
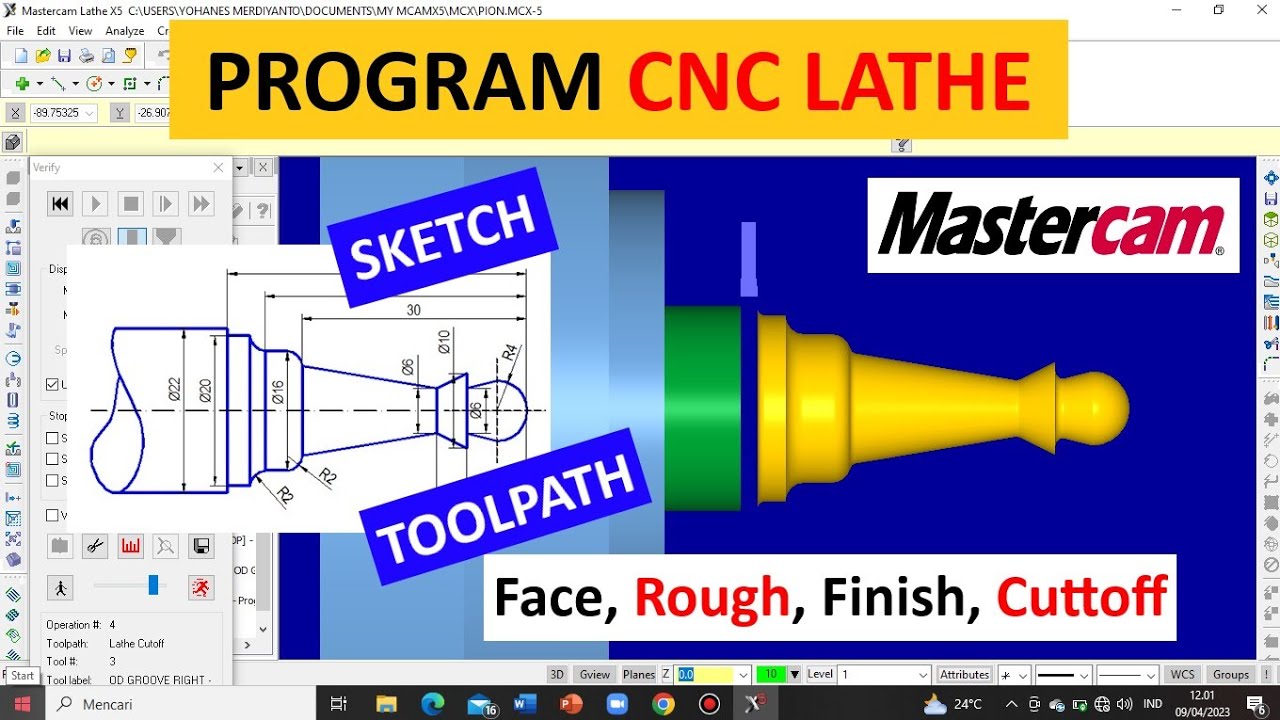
TUTORIAL MASTERCAM X5 MEMBUAT PION || CNC Turning (Lathe) || Simpel & Mudah dipahami !!
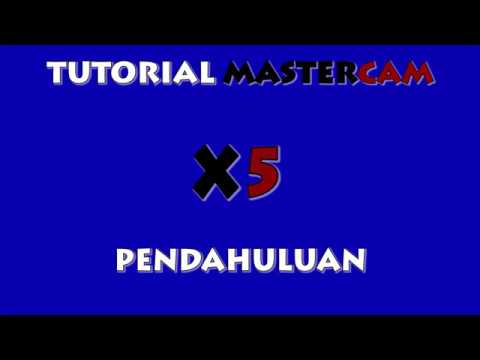
#1 - Pengenalan MasterCam

Program CNC Turning Menggunakan MasterCAM X9 (Pembuatan PIN)
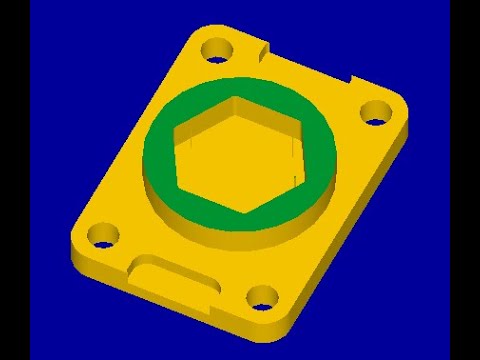
Tutorial Mastercam X5 CNC Mill / Fraish
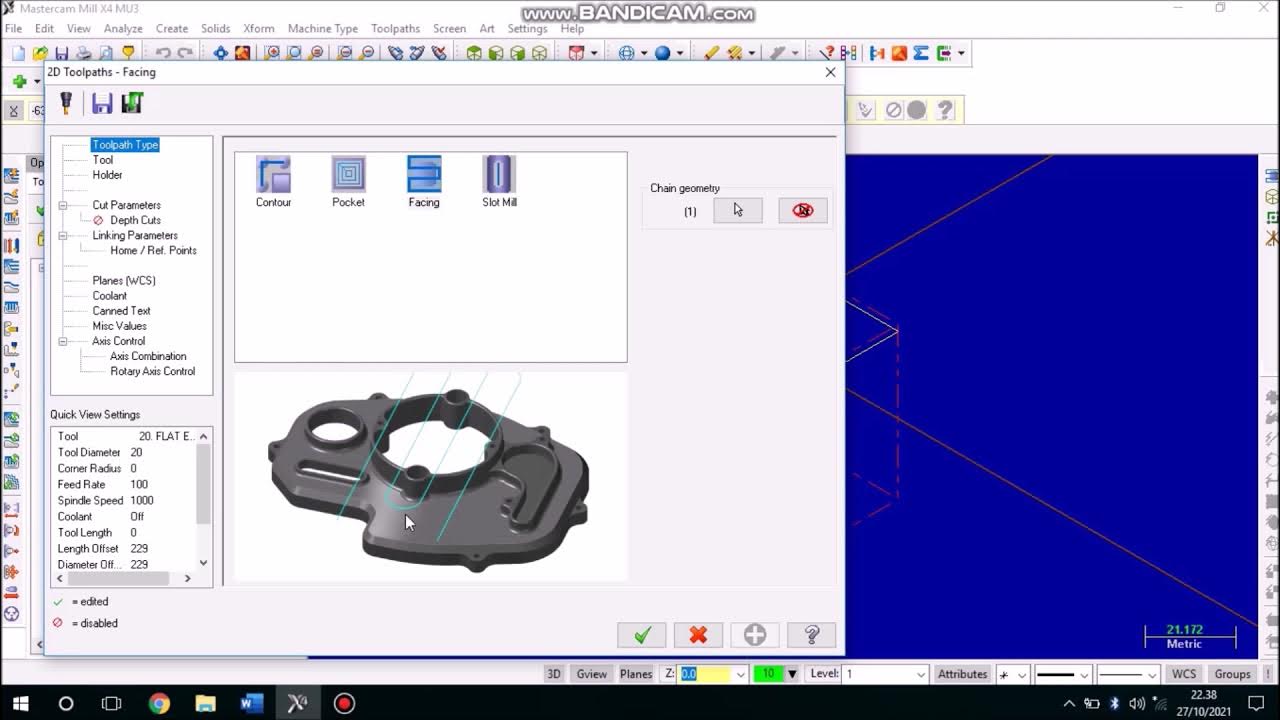
Job Facing Master CAM Mill
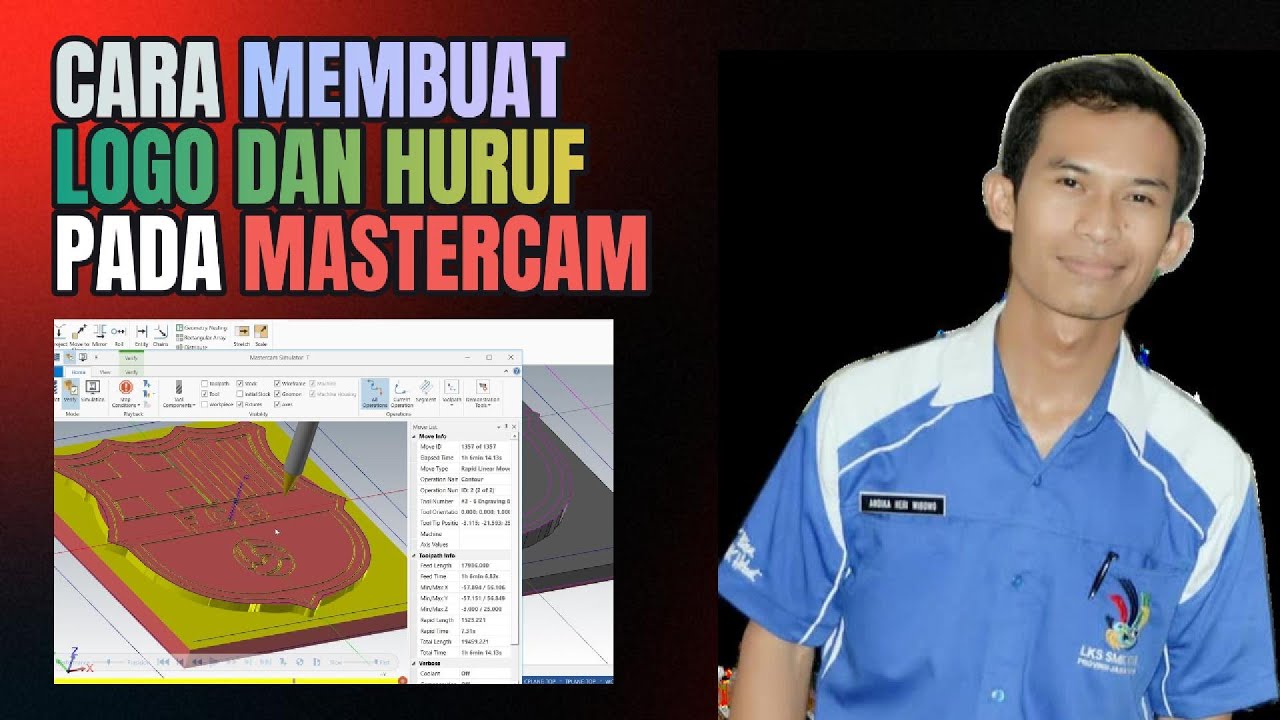
Cara membuat LOGO dan Tulisan pada software Mastercam 2017 - Logo Barcelona
5.0 / 5 (0 votes)