The best Example of a Full Six Sigma Project
Summary
TLDRIn this video, Paul Allen takes viewers through an injection molding case study focused on optimizing machine efficiency and improving product quality. The project aimed to reduce cycle time by 15% and improve process capability (Cpk) to 1.67. By stabilizing variables such as machine settings and maintenance procedures, and conducting a structured Design of Experiments (DOE), the team efficiently found the best settings for the process. The result was a 20% reduction in cycle time, near-zero defects, and a significant improvement in overall efficiency and product quality, showcasing the power of DOE in process optimization.
Takeaways
- 😀 The video introduces a case study on improving an injection molding process, with the main focus on increasing machine speed and optimizing quality.
- 😀 The objective of the project is not to reduce defects, but to enhance process efficiency and speed while maintaining quality standards.
- 😀 The team aims to reduce cycle time by 15% and achieve a process capability (CpK) of 1.67.
- 😀 A comprehensive process flow diagram is used to analyze and identify areas that lack standard operating procedures, which are essential to ensuring stable operations.
- 😀 Standardization of machine settings, robot settings, maintenance, and measurement procedures is critical to creating a controlled environment before improving the process.
- 😀 Design of Experiments (DOE) is used to systematically explore the best machine settings, such as injection speed, cooling time, and holding pressure, to optimize both speed and quality.
- 😀 A screening DOE (Taguchi L12) was conducted to identify key variables and their effects on flatness and cycle time, with a minimal number of tests (12 setups).
- 😀 The complexity of optimizing machine settings is highlighted, with over 1.5 trillion possible combinations of settings, making manual optimization impractical.
- 😀 Regrind material was included in the experiment to test its impact on process performance, as many companies typically neglect this variable.
- 😀 The DOE approach is efficient because it uses a pre-designed pattern (L12) to extract maximum information with minimal data collection, ensuring accurate results.
- 😀 After conducting 20 tests, optimal settings were identified, significantly improving flatness, cycle time, and overall process capability, achieving near-zero defects and faster cycle times.
Q & A
What is the main focus of the injection molding case study presented in the video?
-The main focus is to increase the capacity of the injection molding machine by reducing cycle time and improving process capability, aiming to speed up the process while maintaining or improving quality.
What is the target cycle time reduction mentioned in the video?
-The target is to reduce the cycle time by 15%.
Why is flatness a critical factor in the quality of the molded parts?
-Flatness is a key factor because inconsistent flatness, especially from one cavity, leads to defects. One cavity was causing around 4% of defects due to poor flatness, which impacts overall product quality.
What is the role of standard operating procedures (SOP) in improving the injection molding process?
-SOPs help to establish consistent and controlled processes, ensuring that variables like machine settings, maintenance, and measurements are standardized, which is crucial for achieving optimal performance and high-quality outputs.
What is the significance of using Design of Experiments (DOE) in this case study?
-DOE is crucial for systematically testing and determining the best machine settings. It helps identify the optimal combination of variables to achieve the fastest and most efficient production process with the best quality.
What challenges arise when trying to find the best settings for the injection molding process?
-The challenge lies in the sheer number of possible combinations of machine settings (1.5 trillion), which makes it impossible to manually determine the best settings. Only structured approaches like DOE can effectively handle this complexity.
How does the video explain the role of regrind material in the process?
-Regrind material, which is often not controlled, is included in the experiment to examine its effect on the process. It was incorporated into the testing as an additional variable that could impact quality and efficiency.
What is the key takeaway from the Taguchi L12 screening DOE used in the video?
-The key takeaway is that the Taguchi L12 design allows for maximum information extraction from a minimal number of tests (12 setups), making it an efficient way to identify the best settings without exhaustive testing.
How did the screening DOE help improve the injection molding process?
-The screening DOE helped identify the most influential variables, such as screw speed and holding pressure, which were then adjusted to reduce variability in flatness and optimize cycle time, resulting in significant process improvements.
What results were achieved after applying the best settings from the experiments?
-After applying the best settings, the cycle time was reduced by approximately 20%, and the process capability (Cpk) improved drastically, achieving near-zero defects and faster production, well exceeding the initial targets.
Outlines
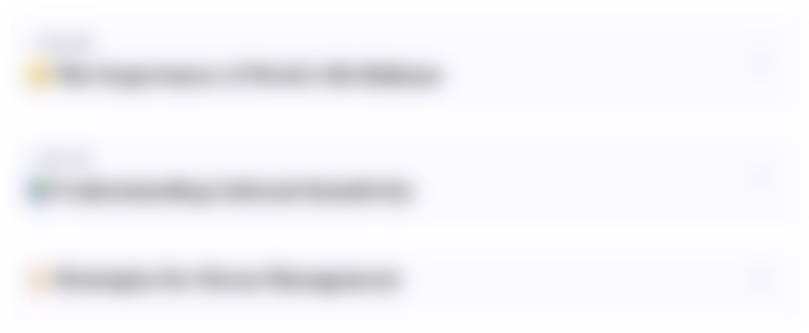
This section is available to paid users only. Please upgrade to access this part.
Upgrade NowMindmap
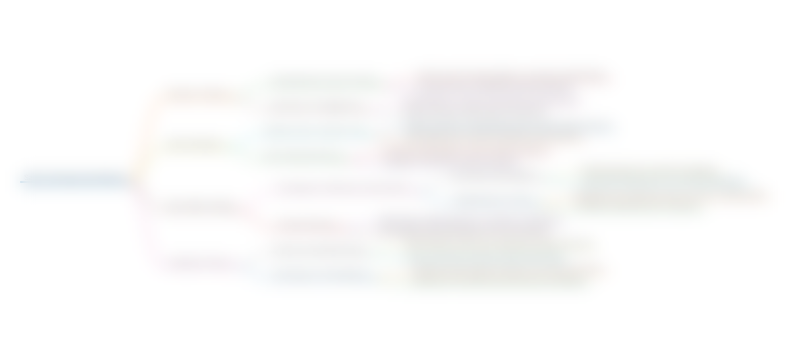
This section is available to paid users only. Please upgrade to access this part.
Upgrade NowKeywords
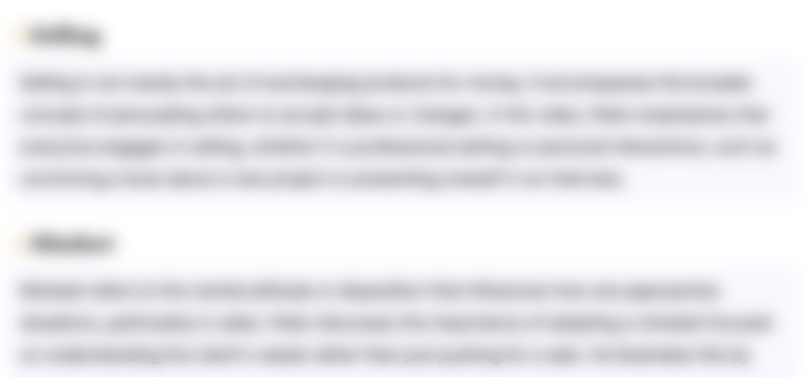
This section is available to paid users only. Please upgrade to access this part.
Upgrade NowHighlights
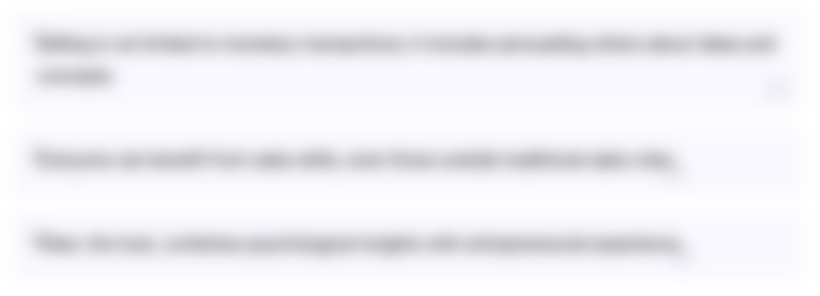
This section is available to paid users only. Please upgrade to access this part.
Upgrade NowTranscripts
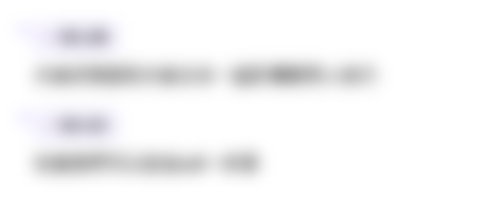
This section is available to paid users only. Please upgrade to access this part.
Upgrade NowBrowse More Related Video
5.0 / 5 (0 votes)