Velocidade de injeção
Summary
TLDRIn this video, Marcelo explains the concept of injection speed (fill speed) in plastic molding, emphasizing its critical role in achieving optimal product quality. He describes how controlling the speed at which material fills the mold cavity can prevent defects like surface marks, underfills, or turbulence. By adjusting the speed profile during the injection process, manufacturers can improve the strength, flexibility, and appearance of molded parts, especially in complex molds or thin-walled products. Marcelo also highlights the importance of considering material properties and machine capabilities to fine-tune injection speeds and resolve common molding issues.
Takeaways
- 😀 Injection speed refers to how quickly material is injected into the mold cavity, affecting the final product's structure and quality.
- 😀 The speed is typically measured in units like cubic centimeters per second or millimeters per second, depending on the injection system's characteristics.
- 😀 Adjusting the injection speed can solve common molding issues, such as uneven filling, shrink marks, or flow lines.
- 😀 Higher injection speeds can lead to turbulence within the cavity, which may result in defects like visible marks or surface irregularities.
- 😀 The use of highly fluid materials requires faster injection speeds to ensure efficient mold filling, especially for thin-walled parts.
- 😀 A profile of injection speed, which varies throughout the injection cycle, can help manage material flow and prevent defects.
- 😀 Excessive injection speed can cause the polymer material to flow too quickly, leading to possible product defects like bursts or surface blemishes.
- 😀 The variation of injection speed at different stages of the process is important for achieving optimal material organization and avoiding problems.
- 😀 Injection speed adjustments help in balancing the flow of material, particularly in regions with different thicknesses, like near fasteners or clips.
- 😀 Using a well-calibrated injection speed profile can improve the mechanical properties of the final product, such as impact resistance and flexural strength.
Q & A
What is injection speed in plastic molding?
-Injection speed refers to the rate at which molten plastic is injected into the mold cavity. It is typically measured in units such as cubic centimeters per second or millimeters per second.
How does injection speed affect the final product?
-The speed at which the plastic is injected affects the filling of the mold. If the speed is too high, it can create turbulence, leading to defects like flow marks or air pockets. If the speed is too slow, the material might not fill the mold completely, causing incomplete parts.
Why is the injection speed important for materials with different fluidities?
-Materials with different fluidities require different injection speeds. Highly fluid materials often require faster injection to fill the mold efficiently, while more viscous materials may need slower speeds to avoid excessive pressure and turbulence.
What is a speed profile in injection molding?
-A speed profile is the variation of the injection speed throughout the molding process. It adjusts the speed at different points of the filling cycle to optimize material flow, especially in molds with varying thicknesses or complex features.
What problems can arise if the injection speed is too high?
-If the injection speed is too high, it can cause turbulence inside the mold, leading to defects like flow marks, surface imperfections, and uneven distribution of material, especially in more intricate mold designs.
How does injection speed affect the packing phase of molding?
-During the packing phase, if the speed is too high, the material may not pack properly, leading to voids or inconsistent material density. By adjusting the speed, particularly slowing down in certain areas, proper packing and material distribution are achieved.
How can varying the injection speed help solve common molding defects?
-Varying the injection speed helps address defects such as incomplete filling, air pockets, and flow marks. For example, speeding up the injection in smaller areas and slowing it down for thicker sections can ensure proper filling and reduce the chances of defects.
What role does the hydraulic system play in controlling injection speed?
-The hydraulic system controls the injection speed by pushing the molten plastic through the nozzle and into the mold. The speed is determined by the hydraulic pressure applied to the injection machine's cylinder.
What happens if the injection speed is too low during molding?
-If the injection speed is too low, the material may not fill the mold properly, leading to incomplete parts, especially in regions with complex geometries or thin walls. It can also result in longer cycle times.
How can adjusting the injection speed improve part strength and quality?
-Adjusting the injection speed helps in achieving uniform material distribution, avoiding defects, and ensuring proper packing. This leads to improved part strength, such as better resistance to impact and flexion, and a more consistent surface finish.
Outlines
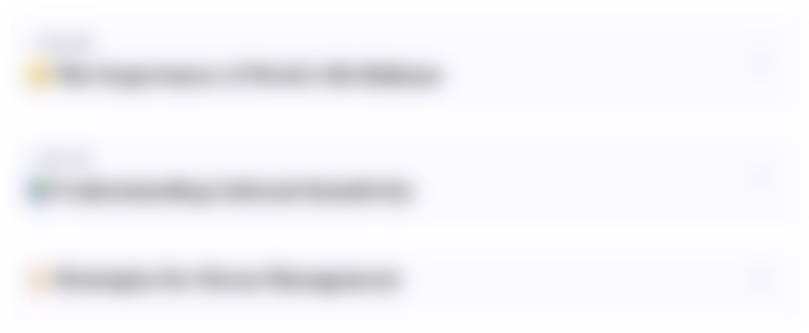
This section is available to paid users only. Please upgrade to access this part.
Upgrade NowMindmap
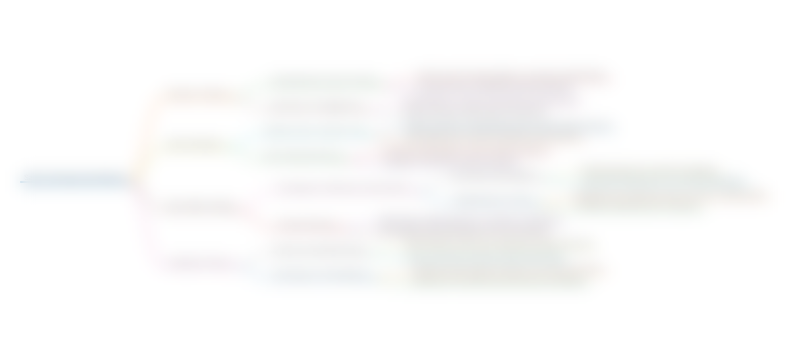
This section is available to paid users only. Please upgrade to access this part.
Upgrade NowKeywords
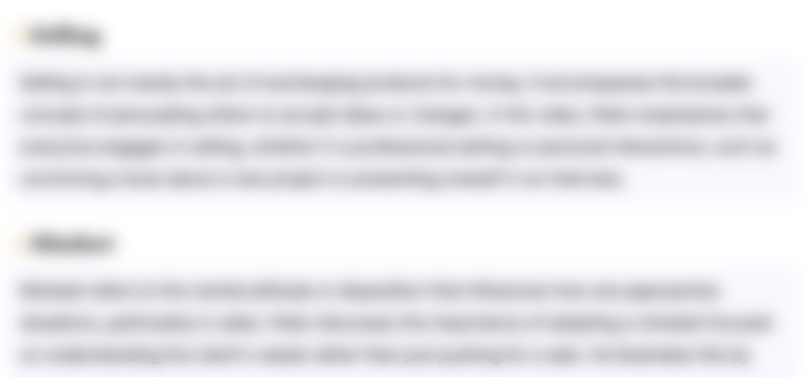
This section is available to paid users only. Please upgrade to access this part.
Upgrade NowHighlights
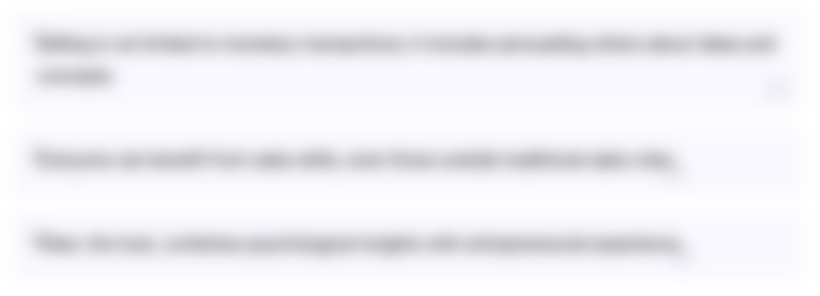
This section is available to paid users only. Please upgrade to access this part.
Upgrade NowTranscripts
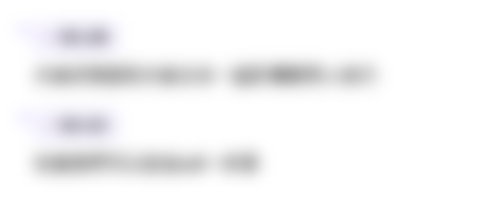
This section is available to paid users only. Please upgrade to access this part.
Upgrade NowBrowse More Related Video

Como funciona una inyectora de plastico
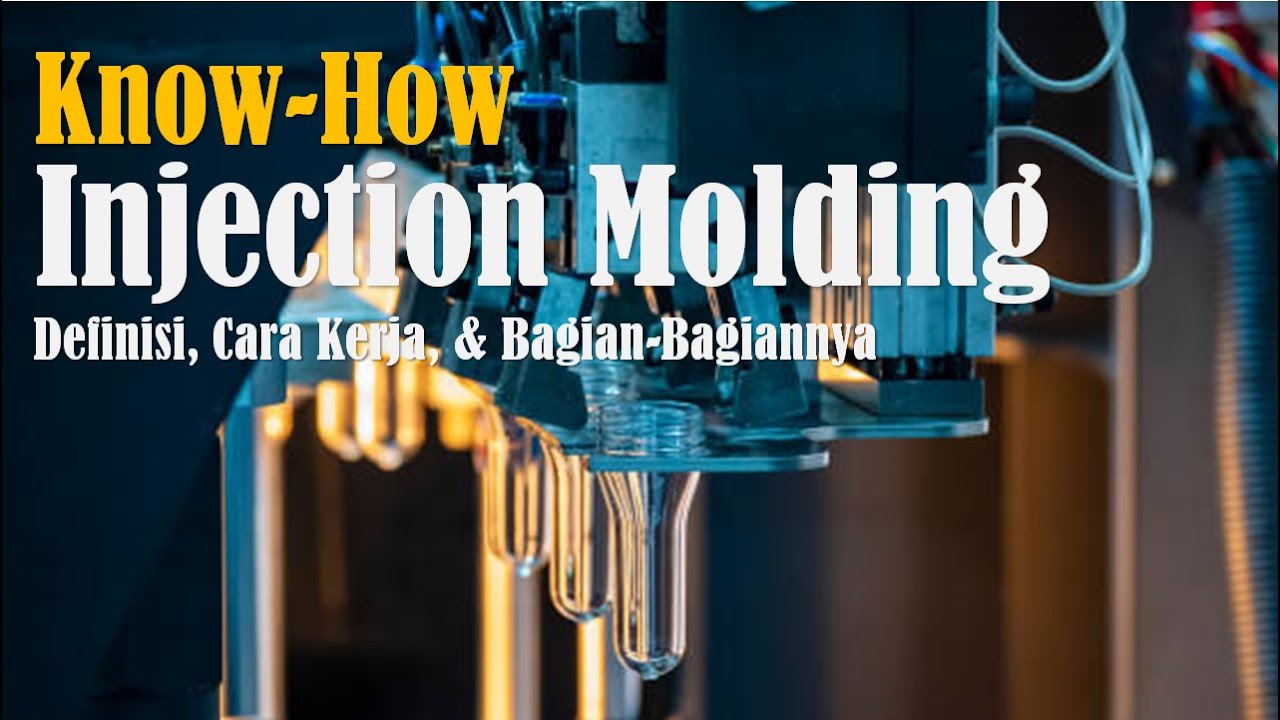
INJECTION MOLDING - DEFINISI, CARA KERJA, DAN BAGIAN-BAGIAN MESIN INJECTION MOLDING
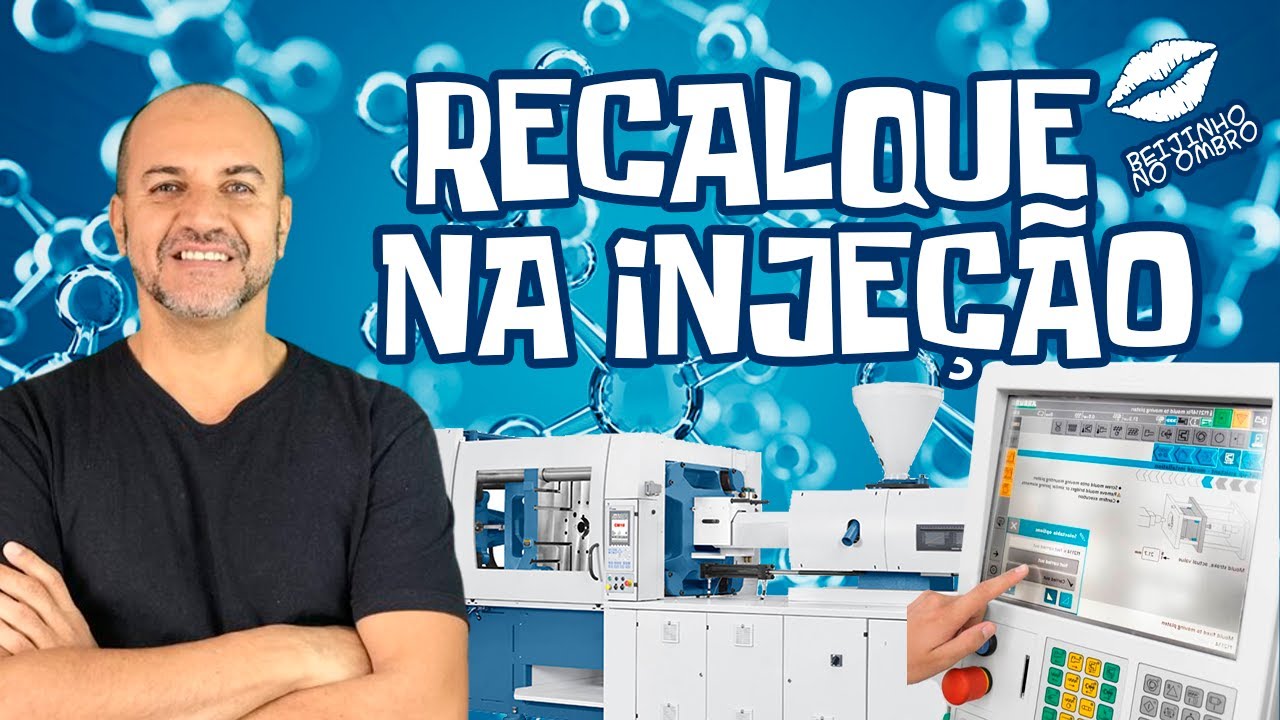
Recalque na injeção de material plástico
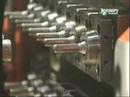
como se hacen las botellas de plastico
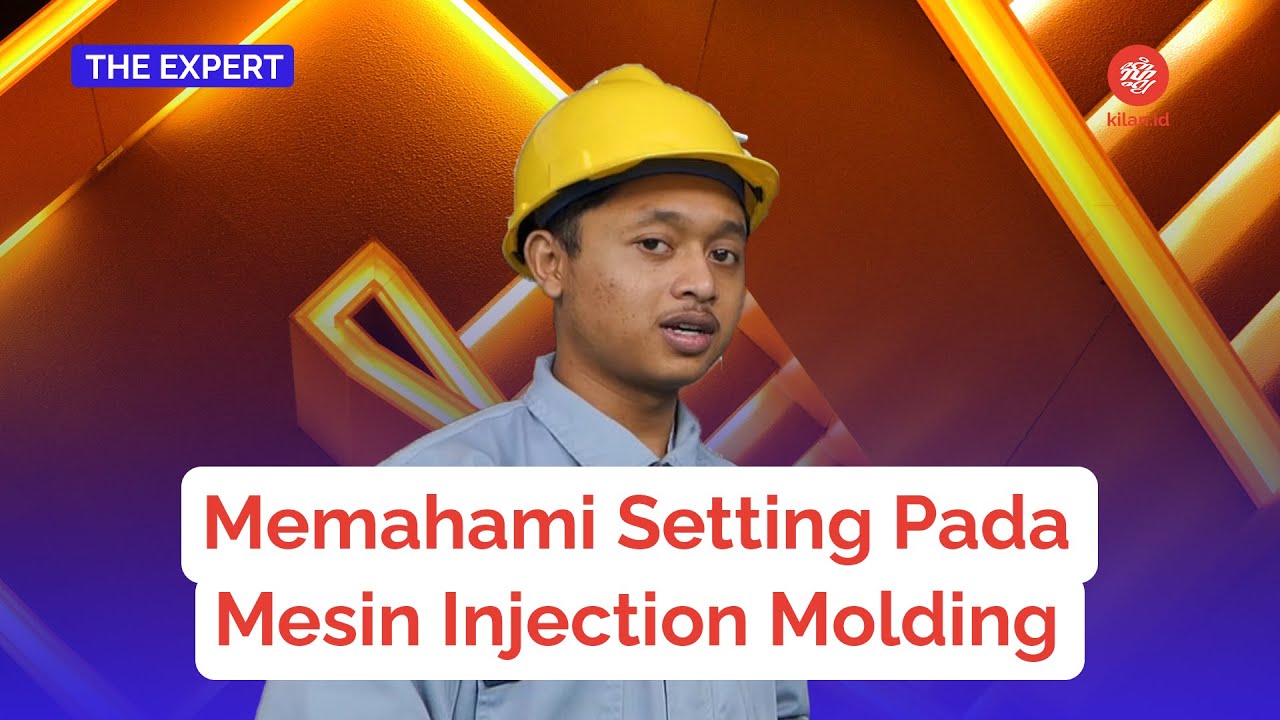
Memahami Setting Pada Mesin Injection Molding - THE EXPERT
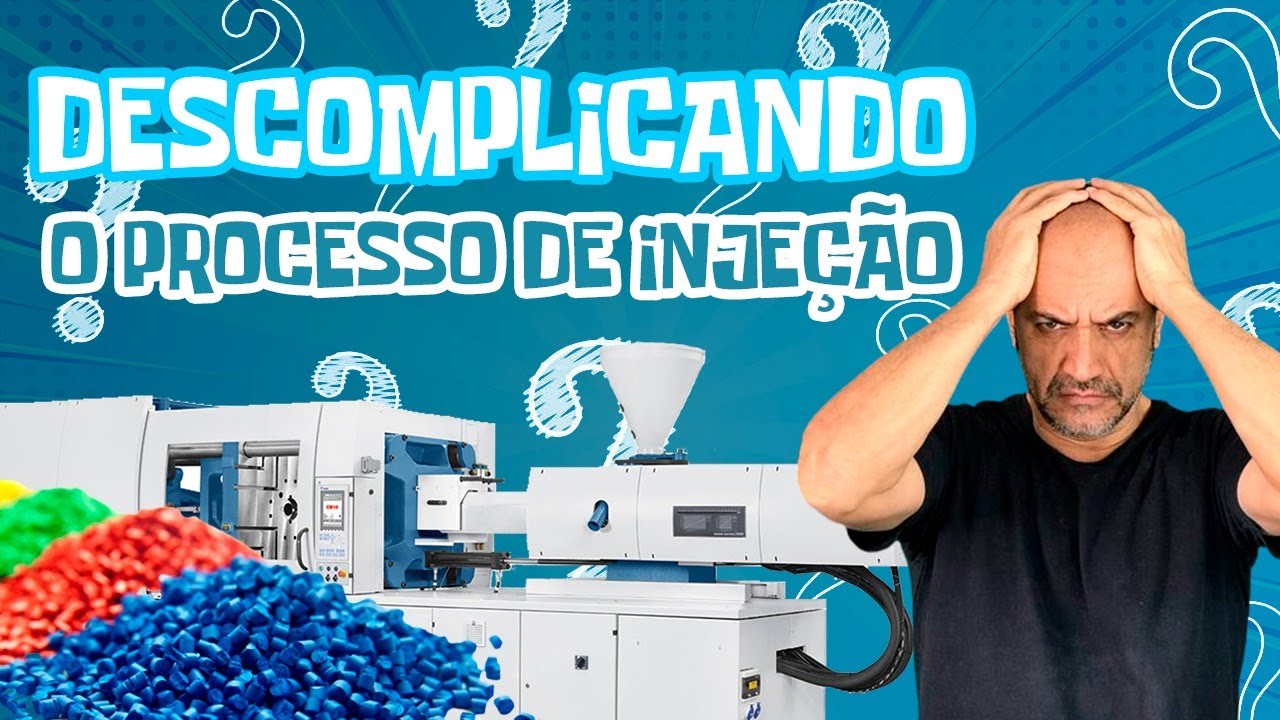
O básico do processo de injeção de plásticos
5.0 / 5 (0 votes)