What is the Difference between Absolute and Incremental Encoders?
Summary
TLDRThis video explores various types of encoders, focusing on linear and rotary encoders with absolute and incremental measurement capabilities. It explains how encoders like optical, magnetic, inductive, capacitive, and laser work to provide feedback on position, speed, and direction. The script delves into practical applications, such as CNC machines and robotics, and clarifies the differences between absolute and incremental encoders, highlighting their respective advantages in safety-critical and setup-intensive environments. Aimed at helping viewers make informed choices for their specific needs, the video also encourages learning PLC programming for career advancement.
Takeaways
- ๐ Encoders are essential components in various applications, and this video script provides an in-depth look at different types and their uses.
- ๐ There are two main sensing techniques for encoders: Linear and Rotary, with each category further divided into Absolute and Incremental measurement types.
- ๐ ๏ธ Linear Encoders use a transducer to measure distance between two points, and can be used in applications like CNC milling machines for precise movement.
- ๐ฏ Rotary Encoders, also known as Shaft Encoders, collect data based on the rotation of an object and can be used in applications ranging from computer input devices to robotics.
- ๐ Position Encoders are used to determine the mechanical position of an object, which can be either Absolute or Incremental, and are widely used in industrial applications for tooling and multi-axis positioning.
- ๐ Optical Encoders interpret data in pulses of light, determining position, direction, and velocity, and can be used in applications like printers, CNC milling machines, and robotics, with Absolute or Incremental capabilities.
- ๐ Absolute vs. Incremental: Absolute encoders, like Rotary Absolute, have a unique code pattern that allows for precise position detection, ideal for safety-critical applications. Incremental encoders, on the other hand, start at zero and count each revolution, useful for applications where the exact position is not crucial.
- ๐ ๏ธ For Rotary Absolute encoders, the slotted disc on a shaft, in conjunction with a stationary pickup device, produces a unique code pattern for each position, ensuring accurate positioning.
- ๐ Incremental encoders begin their count at zero and record each revolution, making them suitable for applications where the exact position is not needed, but the relative change is.
- ๐ The script provides a practical example of using an incremental encoder to determine the travel count of an object on a conveyor, highlighting the difference between Absolute and Incremental measurements.
Q & A
What are the two main sensing techniques of encoders mentioned in the script?
-The two main sensing techniques of encoders mentioned are Linear and Rotary.
What is the purpose of a Linear Encoder in an application?
-A Linear Encoder uses a transducer to measure the distance between two points and can be used to determine the position of an object, such as in a CNC milling machine for precise movement measurements.
How does a Rotary Encoder differ from a Linear Encoder?
-A Rotary Encoder collects data and provides feedback based on the rotation of an object, converting an object's angular position or motion, whereas a Linear Encoder measures the distance between two points.
What are the two types of encoder measurement types discussed in the script?
-The two types of encoder measurement types discussed are Absolute and Incremental.
What is the difference between Absolute and Incremental Rotary Encoders?
-Absolute Rotary Encoders can measure angular positions, while Incremental Rotary Encoders can measure distance, speed, and position based on the number of signals per revolution.
In which applications are Rotary Encoders commonly used?
-Rotary Encoders are used in various applications such as computer input devices like mice and trackballs, as well as in robotics.
What is a Position Encoder and how is it used?
-A Position Encoder is used to determine the mechanical position of an object, providing an absolute position or detecting a change in position relative to the encoder, and is widely used in industrial applications for tooling and multi-axis positioning.
How do Optical Encoders interpret data to determine position, direction, and velocity?
-Optical Encoders interpret data in pulses of light, using a rotating disc with opaque segments that represent a particular pattern to determine the movement of an object for rotary or shaft applications, and exact position in linear functions.
What are the two types of Absolute Measurement Encoders mentioned in the script?
-The two types of Absolute Measurement Encoders mentioned are Single-turn and Multi-turn, with Single-turn used for short distances and Multi-turn for longer distances and more complex positioning.
How does an Incremental Encoder determine the position of an object?
-An Incremental Encoder creates an output signal each time the shaft rotates a measured amount, and the position is determined based on the count of signals from zero, without a definitive position unless a reference point is established.
What is the advantage of using an Absolute Encoder over an Incremental Encoder in safety-critical applications?
-Absolute Encoders are preferred in safety-critical applications because they provide a high degree of certainty regarding the exact position at all times, based on the unique pattern produced, without the need for a reference point after power disruptions.
Outlines
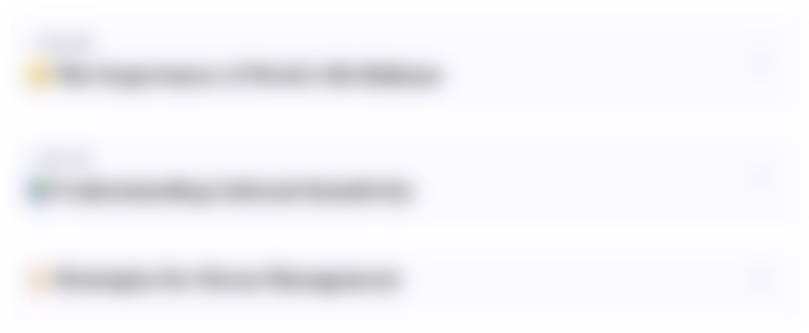
This section is available to paid users only. Please upgrade to access this part.
Upgrade NowMindmap
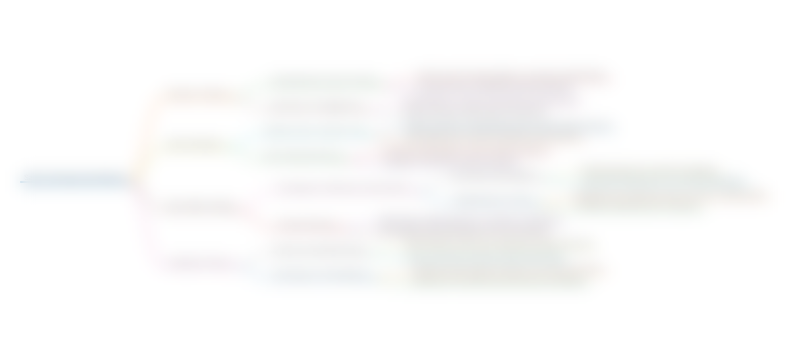
This section is available to paid users only. Please upgrade to access this part.
Upgrade NowKeywords
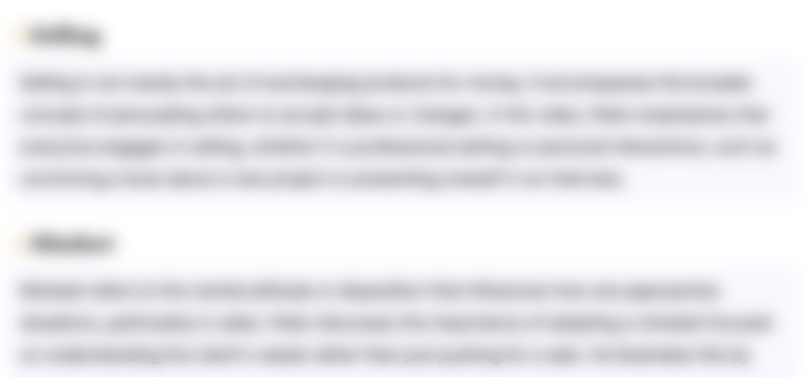
This section is available to paid users only. Please upgrade to access this part.
Upgrade NowHighlights
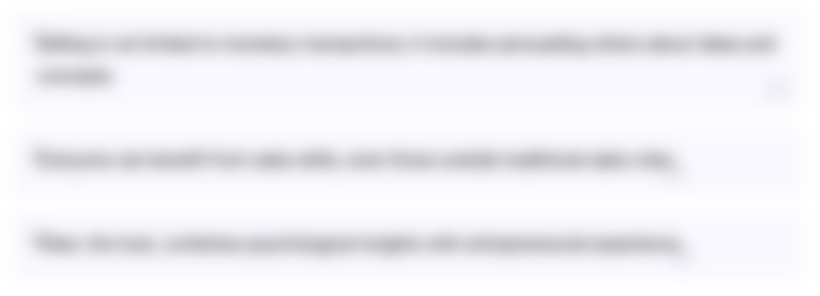
This section is available to paid users only. Please upgrade to access this part.
Upgrade NowTranscripts
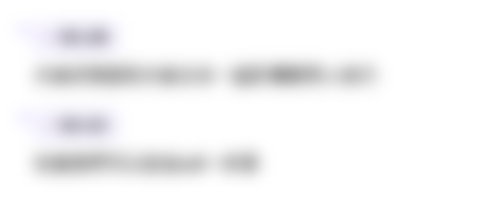
This section is available to paid users only. Please upgrade to access this part.
Upgrade Now5.0 / 5 (0 votes)