How LVDT Works | Construction and Working
Summary
TLDRThis lecture delves into the workings of the Linear Variable Differential Transformer (LVDT), a device renowned for its precision in measuring linear displacement. It operates on the principle of mutual inductance, with a cylindrical former at its core, surrounded by a primary coil and two secondary coils. The movable ferromagnetic core's position relative to the coils determines the output voltage, indicating displacement direction and magnitude. The video explains the three core positions and the corresponding voltage outputs, highlighting the use of a phase-sensitive detector for direction sensitivity. Advantages include a wide measurement range, no frictional losses, high input sensitivity, low hysteresis, and direct conversion to electrical signals. However, the device's sensitivity to stray magnetic fields and environmental factors like vibrations and temperature are noted as drawbacks.
Takeaways
- π LVDT stands for Linear Variable Differential Transformer and operates on the principle of mutual inductance.
- π LVDTs are popular for measuring linear displacement with commercial models offering a range from plus/minus 0.25 millimeters to plus/minus 250 millimeters.
- ποΈ The construction of an LVDT includes a cylindrical former, a primary coil, and two secondary coils, with a ferromagnetic core that moves freely within.
- π The operation of LVDT is explained through three core positions: null (center), left of null, and right of null, affecting the output voltage.
- π§ A phase-sensitive detector is used with LVDT to determine the direction of core movement, as the output voltage alone cannot indicate direction.
- βοΈ When the core moves left, the EMF in secondary coil 1 is greater than in coil 2, resulting in a net negative displacement.
- π Conversely, when the core moves right, the EMF in secondary coil 2 exceeds that in coil 1, leading to a net positive displacement.
- π LVDTs offer several advantages, such as a wide measurement range, no frictional losses, high input and sensitivity, low hysteresis for excellent repeatability, and direct conversion to electrical signals.
- π They can also function as secondary transducers, converting other types of measurements, like pressure, into electrical signals after calibration.
- β οΈ Disadvantages include sensitivity to stray magnetic fields and susceptibility to vibrations and temperature changes, necessitating protective setups.
Q & A
What does LVDT stand for?
-LVDT stands for Linear Variable Differential Transformer.
What is the principle on which LVDT operates?
-LVDT operates on the principle of variation of mutual inductance.
What is the full scale displacement range of commercial LVDTs?
-Commercial LVDTs are available with a full scale displacement range of plus minus 0.25 millimeters to plus minus 250 millimeters.
What are the main components of an LVDT?
-The main components of an LVDT are a cylindrical former, a primary coil, two secondary coils, and a movable ferromagnetic core.
What type of voltage source is used to excite the primary winding of an LVDT?
-The primary winding of an LVDT is excited by a 1 to 10 volts AC voltage source.
How are the secondary coils in an LVDT connected?
-The secondary coils in an LVDT are connected in series.
What is the null position in an LVDT?
-The null position in an LVDT is when the core is at the center, resulting in equal voltage induced in both secondary coils and a net output of zero.
What is the role of a phase sensitive detector in LVDT?
-A phase sensitive detector is used to make the measurement direction sensitive by comparing the phase of the secondary output with the primary signal to judge the direction of movement.
What happens when the core of an LVDT moves to the left-hand side?
-When the core moves to the left-hand side, the EMF voltage induced in secondary coil one is greater than in secondary coil two, resulting in a net negative displacement.
What are some advantages of using an LVDT?
-Advantages of using an LVDT include a wide range for measurement of displacement, no frictional losses, high input and sensitivity, low hysteresis for excellent repeatability, direct conversion to electrical signals, and the ability to act as secondary transducers.
What are the disadvantages of using an LVDT?
-Disadvantages of using an LVDT include sensitivity to stray magnetic fields and being affected by vibrations and temperature.
Outlines
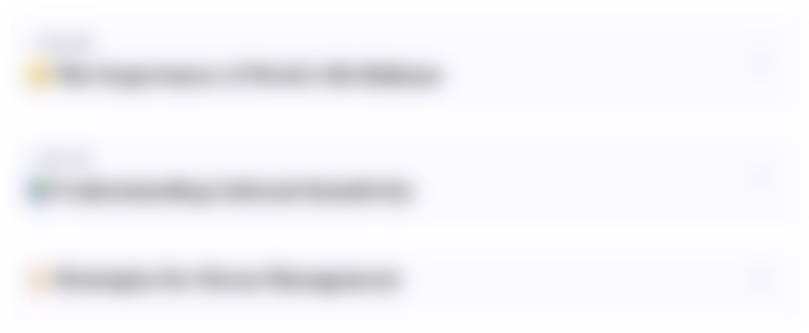
This section is available to paid users only. Please upgrade to access this part.
Upgrade NowMindmap
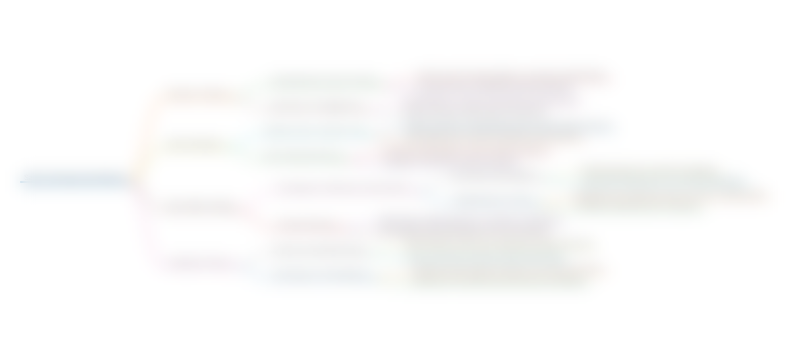
This section is available to paid users only. Please upgrade to access this part.
Upgrade NowKeywords
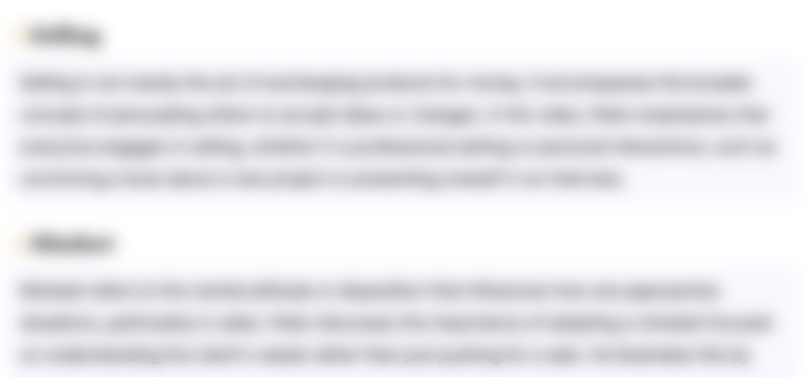
This section is available to paid users only. Please upgrade to access this part.
Upgrade NowHighlights
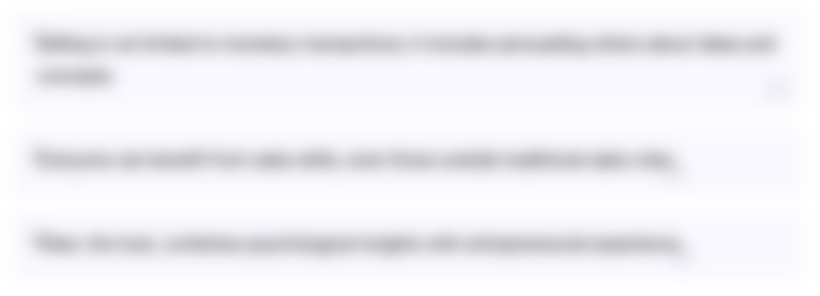
This section is available to paid users only. Please upgrade to access this part.
Upgrade NowTranscripts
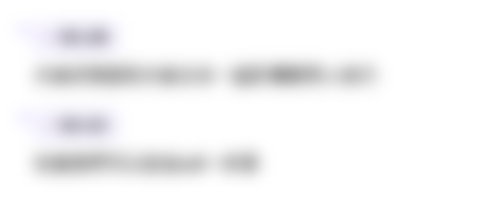
This section is available to paid users only. Please upgrade to access this part.
Upgrade NowBrowse More Related Video
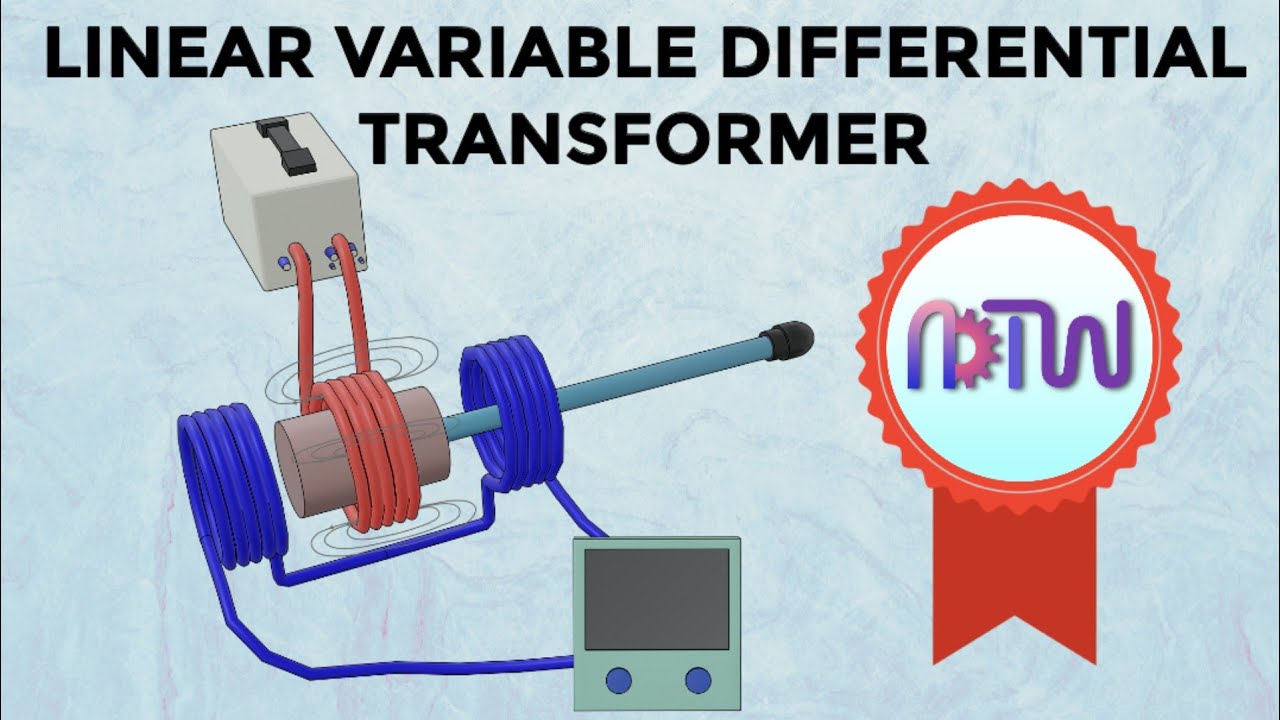
LVDT - Linear Variable Differential Transformer or Transducer Working

A concept of Differential Equation
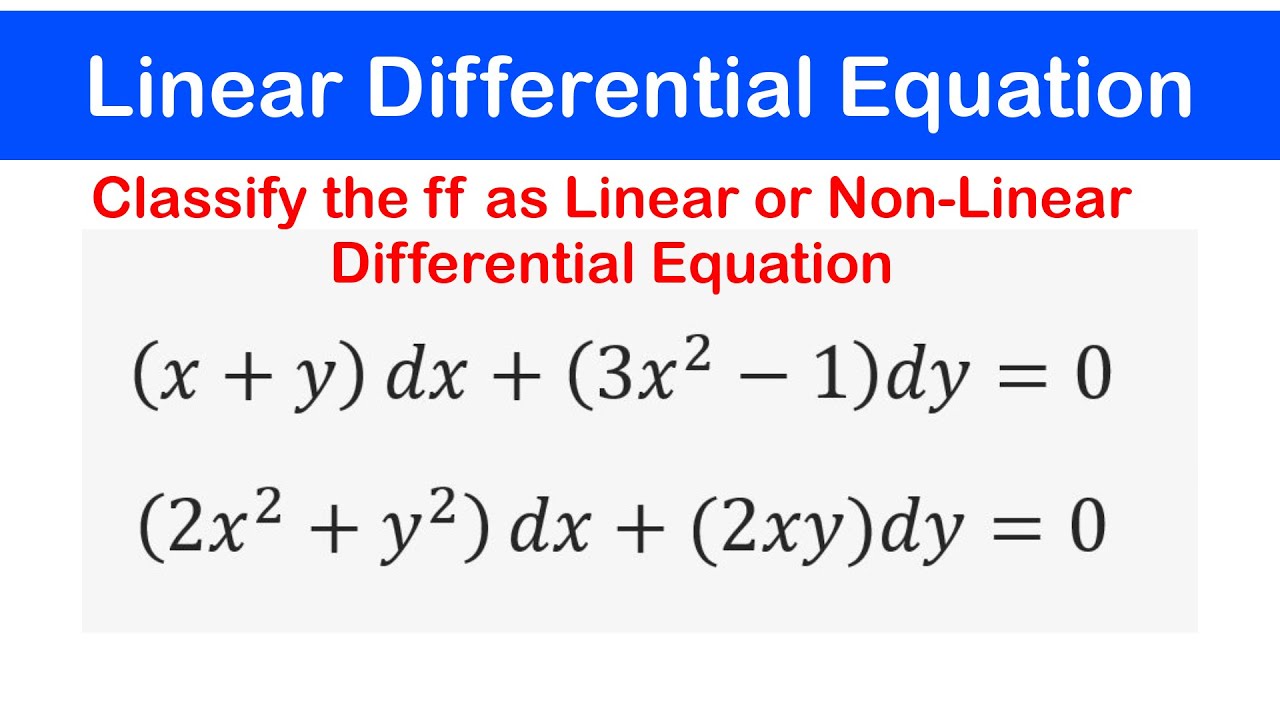
π΅03 - Linear and Non-Linear Differential Equations: Solved Examples

Solved Example | Finite Element Method | Part#1
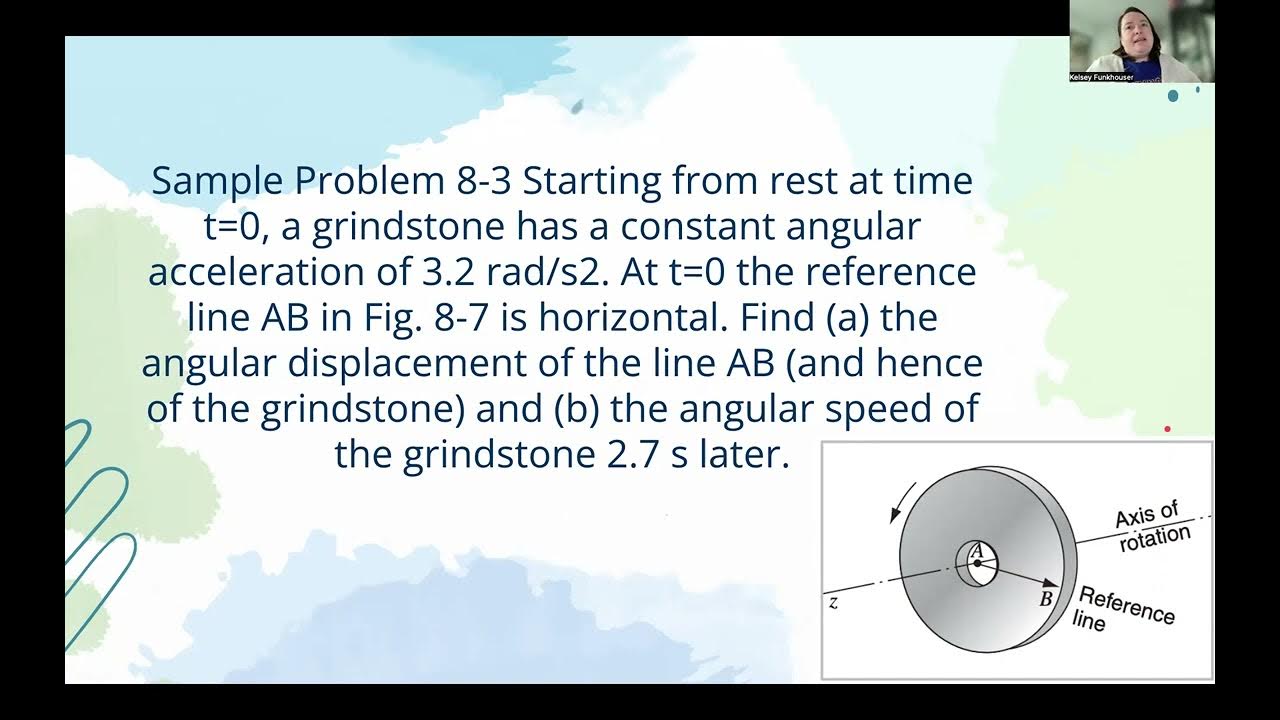
PHYS 121 - Week 6 Lecture 2 - Rotational Motion
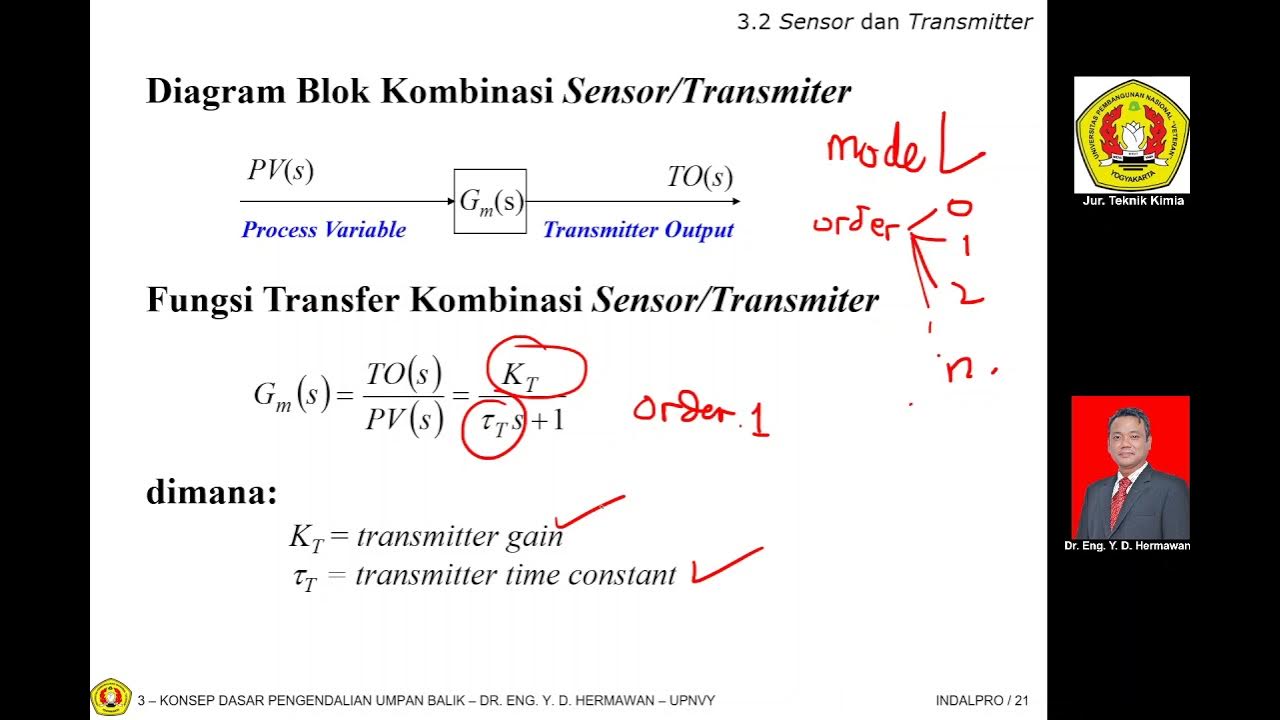
2021 04 05 IPP 3 2 Sensor Transmitter
5.0 / 5 (0 votes)