#PRODUCTIVITYTALKS | TOTAL QUALITY MANAGEMENT
Summary
TLDRThis video discusses the principles of Total Quality Management (TQM) and how it can boost productivity in various industries. It emphasizes the importance of system improvements, continuous process monitoring, and the prevention of recurring issues. Key concepts like the PDCA cycle, teamwork, and the focus on process over results are highlighted. By implementing TQM, companies can improve product quality, customer satisfaction, and profitability while enhancing employee engagement. The video also underscores the applicability of TQM across sectors and the connection between quality management and long-term business growth.
Takeaways
- 😀 Focus on improving systems, not just individual actions, to address underlying issues and achieve better outcomes.
- 😀 The PDC (Plan-Do-Check-Action) cycle is a key method for implementing continuous improvement and quality control.
- 😀 Quality control should emphasize the process, not just the final product, to avoid costly defects discovered too late.
- 😀 Preventing defects at earlier stages of production (e.g., logistics or final inspection) is crucial to reducing costs and maintaining customer satisfaction.
- 😀 Effective quality management systems aim to prevent recurring issues by identifying and addressing root causes through preventive actions.
- 😀 Managers should avoid blaming individuals for mistakes, as issues often arise from systemic problems that need to be fixed.
- 😀 Building teamwork is essential for successful implementation of Total Quality Management (TQM). Collaboration leads to better problem-solving and performance.
- 😀 Implementing TQM leads to improved product quality, increased customer satisfaction, and ultimately higher sales and market share.
- 😀 Continuous improvement (Kaizen) is central to increasing productivity, reducing defects, and enhancing employee engagement and satisfaction.
- 😀 TQM can be applied across various industries, including manufacturing, education, finance, retail, and even public administration, making it versatile and adaptable.
Q & A
What is the main focus of Total Quality Management (TQM)?
-The main focus of Total Quality Management (TQM) is to improve the overall system within an organization by enhancing processes, rather than blaming individuals, in order to achieve higher product quality, customer satisfaction, and productivity.
What does the PDCA (Plan-Do-Check-Act) cycle represent in TQM?
-The PDCA cycle represents a continuous improvement method where organizations plan, implement, check results, and take corrective actions. It is a fundamental tool in TQM for ensuring ongoing quality control.
Why is a process-oriented approach important in TQM?
-A process-oriented approach in TQM is essential because it focuses on controlling and improving processes rather than just the final outcomes. This helps in identifying and correcting defects early, thus reducing costs and ensuring quality throughout production.
How does TQM help in preventing recurring problems?
-TQM encourages organizations to establish preventive actions, address root causes of problems, and avoid repeating mistakes. This helps in maintaining consistent quality and improving long-term efficiency.
What role does teamwork play in TQM?
-Teamwork is crucial in TQM because it fosters collaboration, problem-solving, and collective responsibility. Effective teamwork helps implement continuous improvements and contributes to the overall success of the organization.
What are the main benefits of implementing TQM?
-The main benefits of implementing TQM include improved product quality, increased customer satisfaction, higher productivity, reduced costs, employee satisfaction, and overall profitability for the organization.
Can TQM be applied across different industries?
-Yes, TQM can be applied across a variety of industries including manufacturing, agriculture, mining, finance, public administration, education, and many others. Its principles are universal and adaptable to various sectors.
How does TQM support productivity growth?
-TQM supports productivity growth by enhancing the quality of products and services. This leads to higher customer satisfaction, repeat business, and market share growth, which in turn drives greater productivity and profitability.
What is the role of Kaizen in TQM?
-Kaizen, or continuous improvement, plays a central role in TQM by encouraging incremental improvements in processes and systems. Organizations that embrace Kaizen foster a culture of ongoing quality enhancements.
How can employees benefit from the implementation of TQM?
-Employees benefit from TQM implementation through higher job satisfaction, potential bonuses, and improved working conditions. As productivity and profitability increase, employees are rewarded, leading to a better standard of living.
Outlines
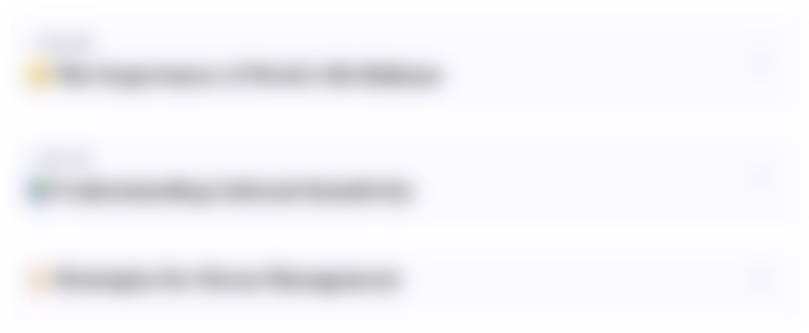
This section is available to paid users only. Please upgrade to access this part.
Upgrade NowMindmap
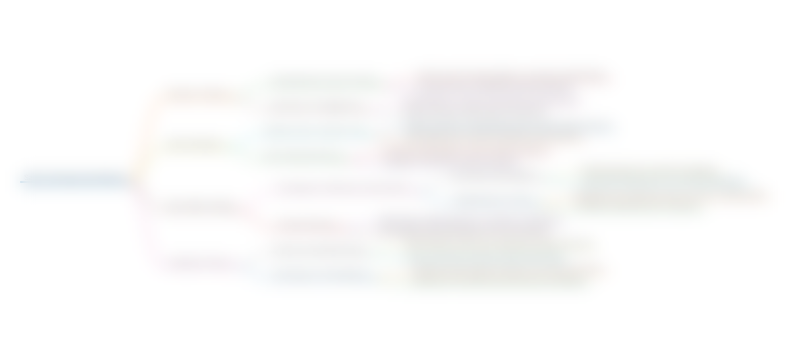
This section is available to paid users only. Please upgrade to access this part.
Upgrade NowKeywords
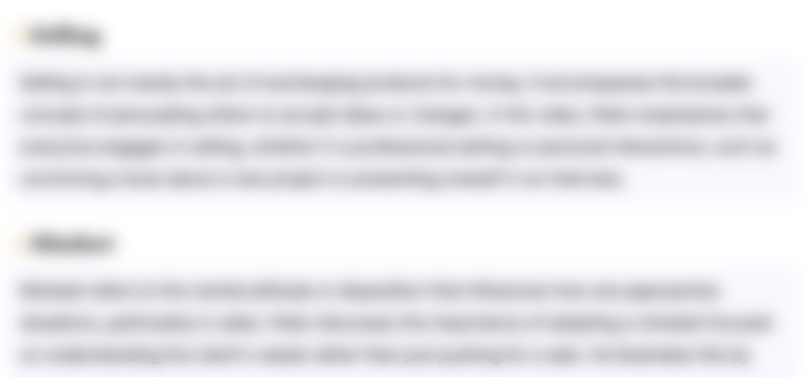
This section is available to paid users only. Please upgrade to access this part.
Upgrade NowHighlights
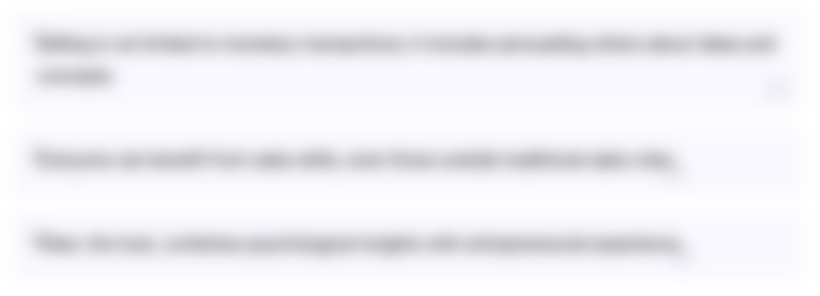
This section is available to paid users only. Please upgrade to access this part.
Upgrade NowTranscripts
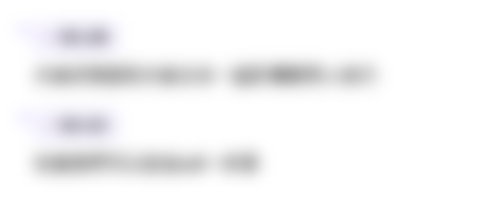
This section is available to paid users only. Please upgrade to access this part.
Upgrade NowBrowse More Related Video
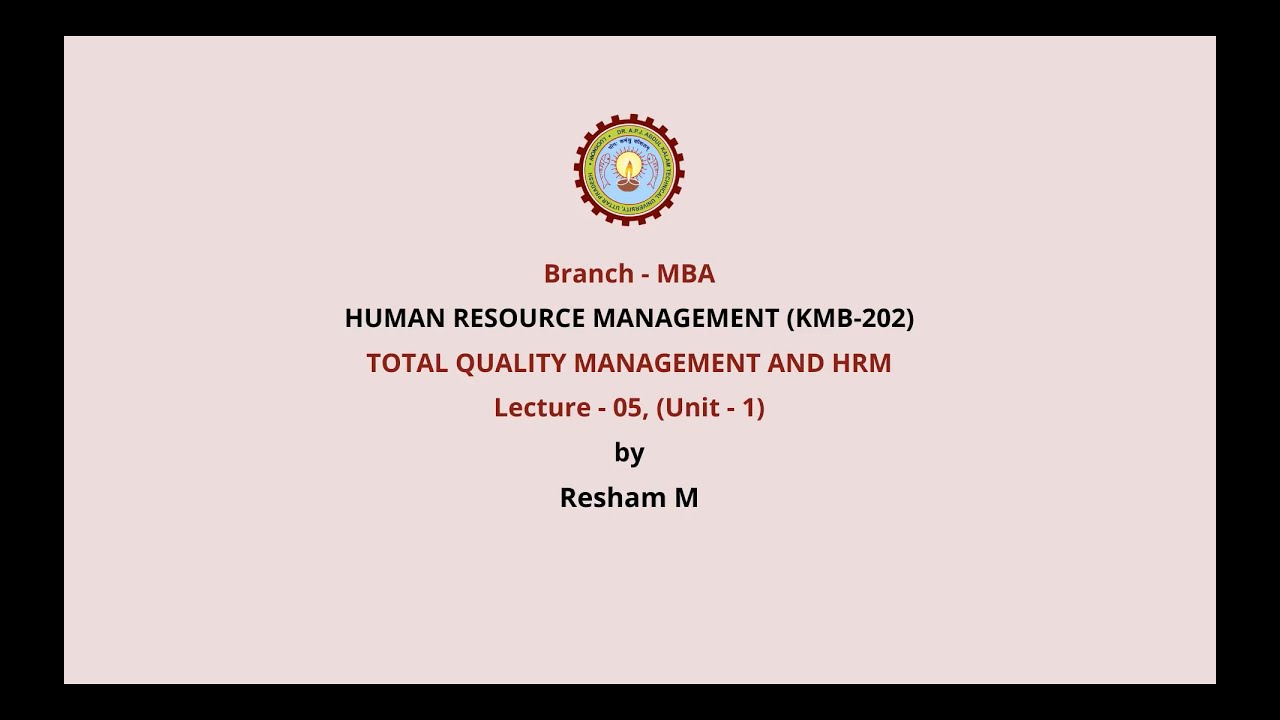
Human Resource Management | Total Quality Management and HRM | AKTU Digital Education

Case Studies

tugas
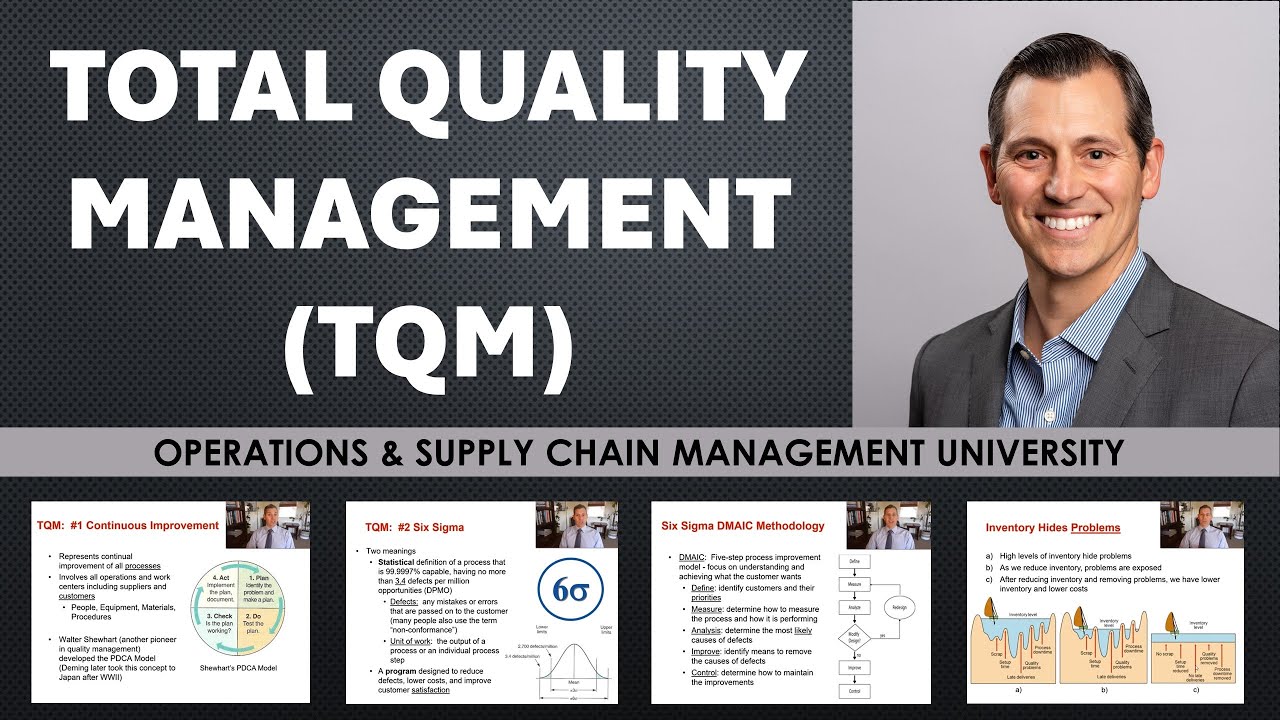
Total Quality Management (TQM) overview, including Six Sigma, Benchmarking & Just-in-Time concepts

Lecture 38 - Improving Service Quality and Productivity - Part 3
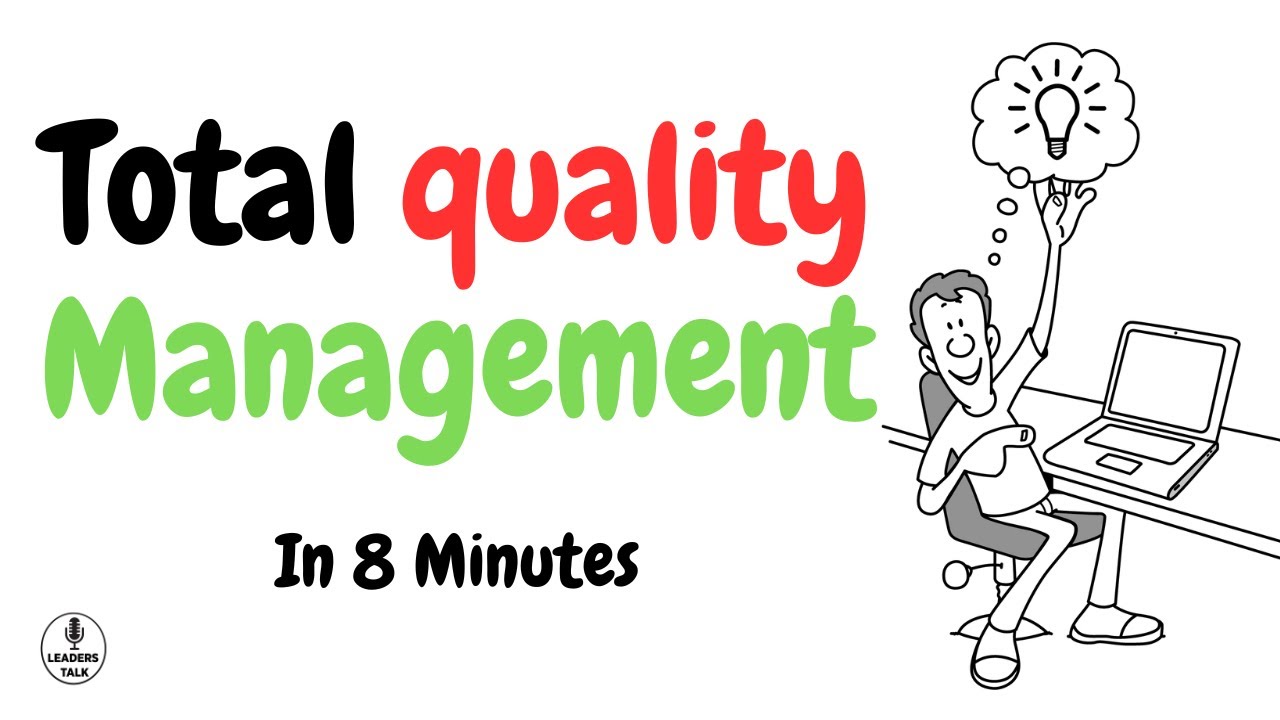
Total Quality Management Principles: A Comprehensive Overview
5.0 / 5 (0 votes)