Case Studies
Summary
TLDRThis video explores key aspects of Total Quality Management (TQM) through various case studies, including Tata Steel’s journey to quality, Deming’s 14 points, and the Malcolm Baldrige and Deming awards. It highlights how companies have successfully applied quality principles to improve processes, reduce costs, and satisfy customers. With a focus on the application of TQM in real-world scenarios, the video also delves into Juran’s influence on quality cost estimation and the Japanese approach to quality. The video offers valuable insights into how TQM frameworks can lead to business excellence and sustainability in competitive markets.
Takeaways
- 😀 Deming Prize and Malcolm Baldrige Award are prestigious awards that recognize excellence in total quality management (TQM) and statistical quality control.
- 😀 The Deming Prize, established in Japan in 1951, rewards companies that successfully implement companywide quality control (CWQC) based on statistical quality control (SQC).
- 😀 The Malcolm Baldrige Award, named after Malcolm Baldrige, is similar to the Deming Prize but is specific to U.S. companies and includes rigorous application processes.
- 😀 Tata Steel's journey to total quality management (TQM) involved identifying customer needs, establishing cross-functional teams, and focusing on employee recognition to improve product quality.
- 😀 Tata Steel's TQM efforts included training employees on customer requirements and establishing quality councils to solve problems in various departments.
- 😀 Tata Steel focused on employee recognition programs, which contributed to better productivity and quality by motivating workers to meet quality improvement goals.
- 😀 Tata Steel also aligned its vision with continuous learning and change, aiming to become the most cost-competitive steel producer and a supplier of choice.
- 😀 Juran's influence on Tata Steel emphasized the importance of estimating and reducing the cost of poor quality, leading to significant savings through targeted projects.
- 😀 The company sought ISO 9000 certification and conducted self-assessment in line with the Baldrige Award, achieving global recognition for quality improvements.
- 😀 Deming's 14 points for TQM were successfully implemented by XYZ company to improve quality, productivity, and market share, with significant reductions in costs and defects.
Q & A
What is the main focus of the video on quality engineering and management?
-The video primarily focuses on case studies related to Total Quality Management (TQM) and its implementation in various organizations, including Tata Steel and other global companies. It also discusses key quality awards like the Deming Prize and Malcolm Baldrige Award.
What are the objectives learners should achieve after watching this video?
-Learners should be able to understand the Deming Prize and Malcolm Baldrige Award, explain Tata Steel's journey to Total Quality, discuss Juran's influence on Tata Steel, and describe various case studies such as the Japanese experience with quality.
What is the Deming Prize, and how is it awarded?
-The Deming Prize, established in 1951 in Japan, is awarded to organizations that successfully apply companywide quality control (CWQC) based on statistical quality control (SQC). It is awarded to individuals, companies, factories, small enterprises, and international industries.
How does a company apply for the Deming Prize?
-A company must submit an application to the Deming Prize committee, including details about its quality control practices. After an initial consultation and acceptance, the company must submit a comprehensive description of its practices, and if the committee finds the claims valid, the award is granted.
What is the Malcolm Baldrige Award, and how does it differ from the Deming Prize?
-The Malcolm Baldrige Award, named after Malcolm Baldrige, aims to recognize U.S. companies for their commitment to quality. Unlike the Deming Prize, the Baldrige Award involves submitting a detailed application report, followed by a site visit. The award is presented by the U.S. President.
How did Tata Steel start its journey toward Total Quality Management (TQM)?
-Tata Steel began its TQM journey by identifying customer needs through market surveys and focusing on customer satisfaction. The company trained employees to produce according to customer requirements and established internal quality councils and cross-functional teams to enhance quality.
What role did employee recognition play in Tata Steel’s quality improvement efforts?
-Employee recognition played a crucial role in Tata Steel’s quality improvement efforts. The company honored individuals who contributed to quality improvement, motivating them to continue working toward higher quality and productivity.
What impact did Juran’s influence have on Tata Steel’s quality management?
-Juran's influence led Tata Steel to focus on reducing the cost of poor quality by classifying it into internal failure costs, external failure costs, appraisal costs, and prevention costs. The company successfully reduced poor quality costs by half over five years through targeted projects.
What were the key results of Tata Steel’s quality improvement initiatives?
-As a result of its quality improvement efforts, Tata Steel saved millions of rupees in various divisions, achieved ISO 9000 certification, and won the J.D. Quality Value award. The company became a global leader in steel production while maintaining a strong focus on quality.
How did the Japanese experience with quality impact their industries?
-The Japanese experience with quality emphasized identifying customer needs, reducing the cost of poor quality, and increasing worker awareness of quality. They adopted various quality tools and methods such as statistical process control, cause and effect analysis, and data flow diagrams, which were integral to their success.
Outlines
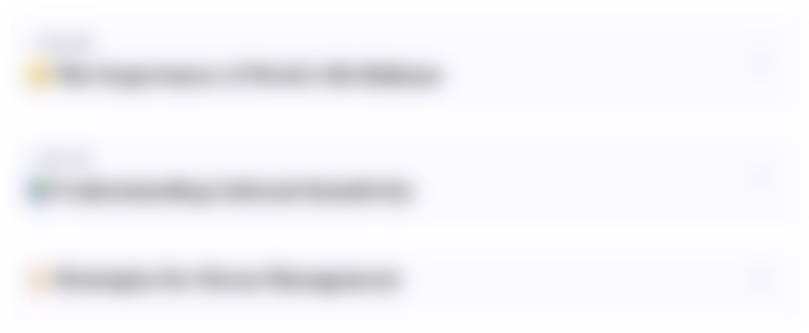
This section is available to paid users only. Please upgrade to access this part.
Upgrade NowMindmap
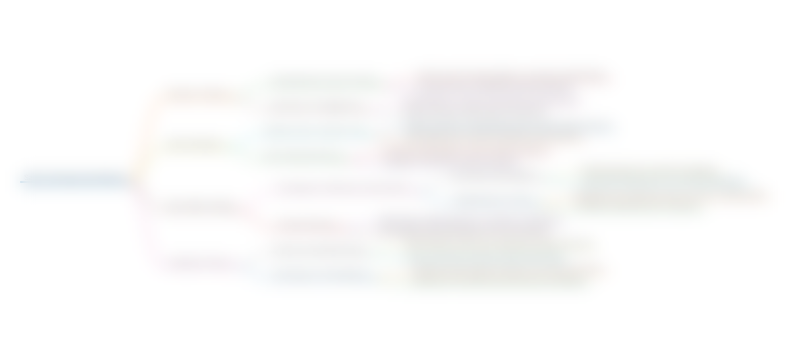
This section is available to paid users only. Please upgrade to access this part.
Upgrade NowKeywords
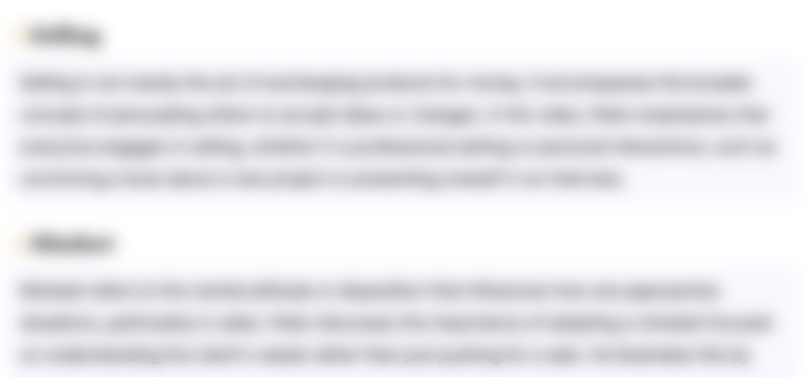
This section is available to paid users only. Please upgrade to access this part.
Upgrade NowHighlights
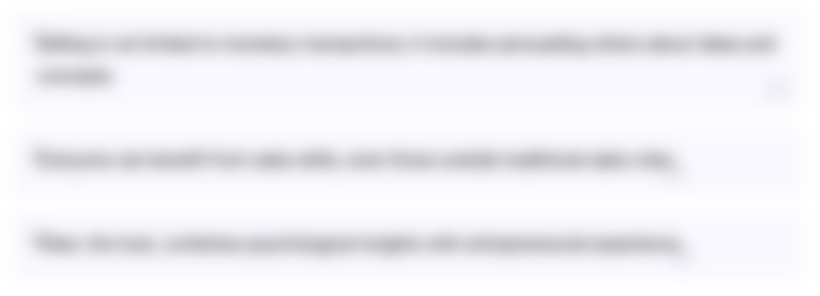
This section is available to paid users only. Please upgrade to access this part.
Upgrade NowTranscripts
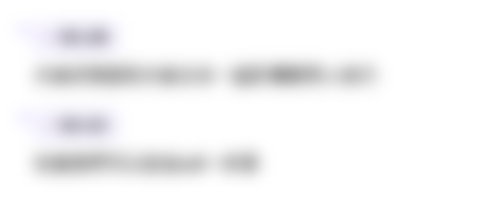
This section is available to paid users only. Please upgrade to access this part.
Upgrade NowBrowse More Related Video
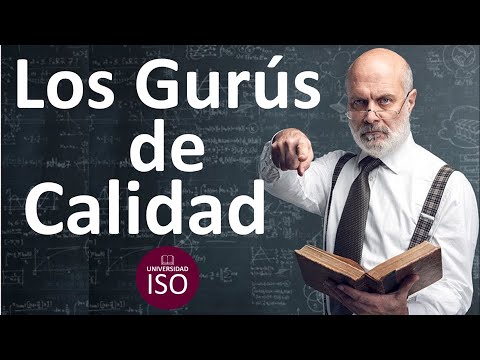
¿Quienes son los Gurús de Calidad? Edwards Deming | Philip B. Crosby | Kaoru Ishikawa Joseph Juran
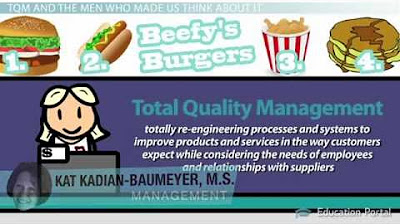
Deming, Juran & Crosby: Contributors to TQM (Total Quality Management)
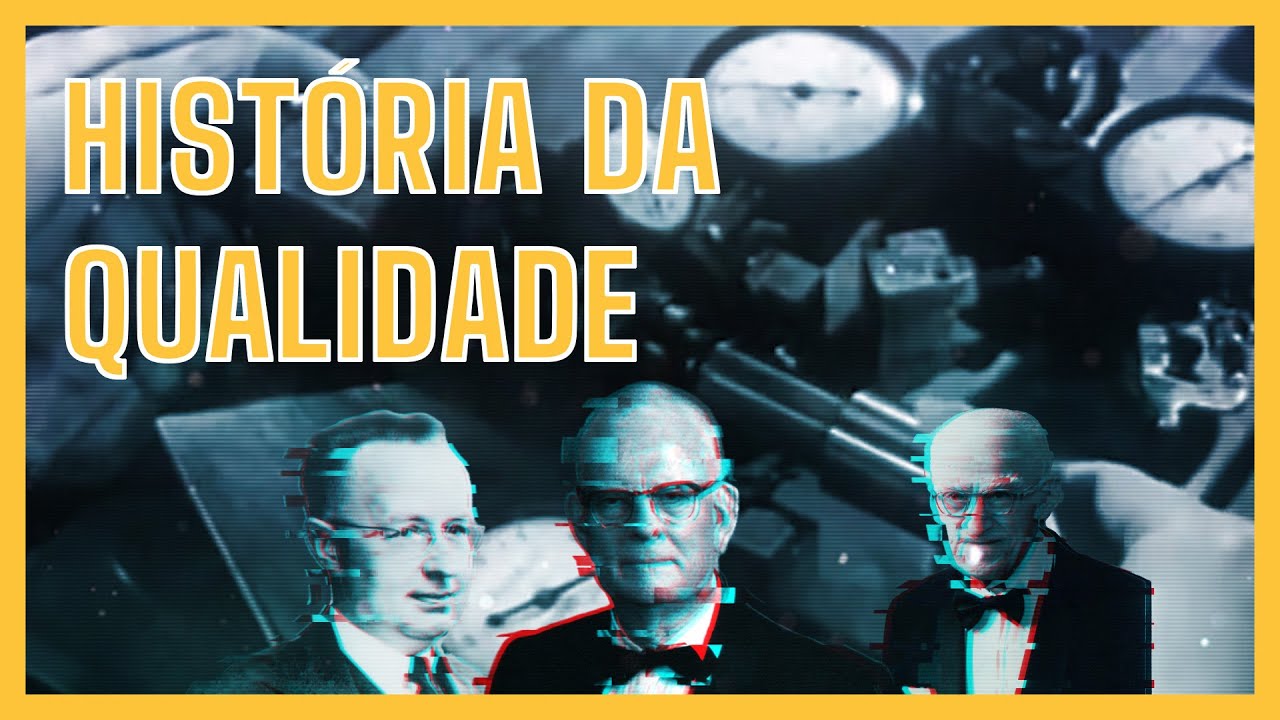
A História da Qualidade - A qualidade de um jeito diferente!

Lecture 38 - Improving Service Quality and Productivity - Part 3

Total Quality Management Tutorial | Self Assessment, Audits & Reviews - Chapter 8

What is Total Quality management (TQM)? | 7 Principles of Total Quality Management
5.0 / 5 (0 votes)