3D Machine Vision with Geometric Measurement Techniques
Summary
TLDRIn this video, Josh Harrington, a Product Applications Engineer at Hermary, introduces geometric methods for capturing 3D machine vision data, focusing on triangulation techniques. The video covers key concepts like stereo vision, laser triangulation, coded light projection, and multi-shot structured light, highlighting their applications across various industries. Harrington explains how these techniques work, their advantages, and limitations, emphasizing their role in enhancing automation and optimization. Viewers are encouraged to engage with questions and comments, setting the stage for further exploration of 3D measurement techniques in future videos.
Takeaways
- ๐ Understanding geometric methods is essential for capturing 3D machine vision data in industrial applications.
- ๐ Stereo vision mimics human perception using two or more cameras with overlapping fields of view to capture 3D information.
- ๐ Laser triangulation is a widely used technique that illuminates an object with a laser and measures depth using an off-axis camera.
- ๐ Coded light projection involves using a light projector to illuminate a scene with a unique pattern, aiding in 3D data capture.
- ๐ Multi-shot structured light captures multiple images with varying patterns, providing high-resolution depth measurements.
- ๐ Active stereo enhances contrast in scenes, allowing for effective 3D measurements even with low visibility.
- ๐ Each geometric method has specific applications, with stereo vision commonly used in self-driving cars and robotic navigation.
- ๐ Laser triangulation is effective in various industries, including lumber production, electronics, and automotive.
- ๐ Challenges with 3D measurement techniques include high computational requirements and the need for object stability during capture.
- ๐ The evolution of 3D machine vision technologies continues to transform automation and optimization in various sectors.
Q & A
What is the primary focus of this video on machine vision?
-The video focuses on geometric methods used to capture 3D machine vision data, particularly triangulation-based techniques.
Who is the presenter of the video, and what is his role?
-The presenter is Josh Harrington, a Product Applications Engineer at Hermary, a leading manufacturer of machine vision hardware.
What are the two primary categories of 3D machine vision techniques discussed?
-The two primary categories are triangulation-based methods and light-based methods.
How does stereo vision work in 3D machine vision?
-Stereo vision requires two or more cameras with overlapping fields of view. It captures the position of objects by triangulating their locations based on the fixed distance between the cameras.
What is active stereo, and why is it used?
-Active stereo is a technique that uses a light projector to project a random pattern onto the scene, providing 'texture' that enhances the contrast and allows for easier feature identification.
What is laser triangulation, and in which industries is it commonly used?
-Laser triangulation involves illuminating an object with a laser and measuring the reflected light with an off-axis camera to determine depth. It is commonly used in industries such as lumber production, electronics, and automotive.
What are some limitations of using laser triangulation?
-Limitations include difficulty measuring specularly reflective surfaces and the need for relative motion between the measurement device and the object.
What is coded light projection, and how does it differ from stereo vision?
-Coded light projection replaces one camera with a coded light projector that illuminates the scene with a unique light pattern, allowing for depth measurement. Unlike stereo vision, it does not rely solely on camera imagery.
What is the process of multi-shot structured light measurement?
-Multi-shot structured light uses a series of images with different fringe patterns to capture depth information. This technique provides high-resolution measurements but requires the object to remain still during the capture process.
What is the anticipated content of the next video in the series?
-The next video will cover 3D measurement techniques associated with the properties of light, expanding on the capabilities of 3D machine vision.
Outlines
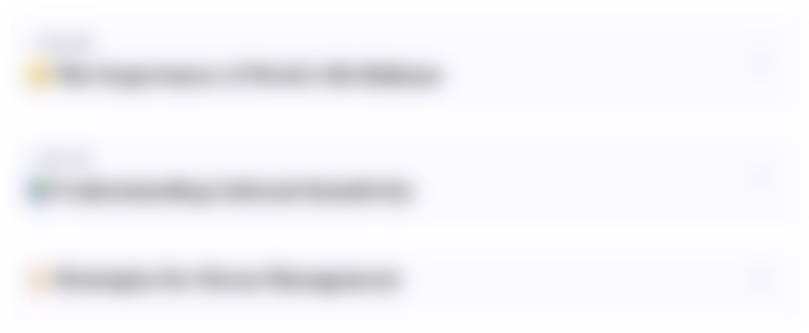
This section is available to paid users only. Please upgrade to access this part.
Upgrade NowMindmap
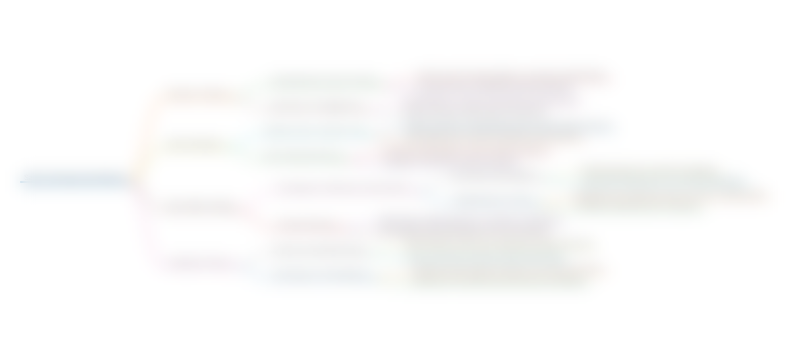
This section is available to paid users only. Please upgrade to access this part.
Upgrade NowKeywords
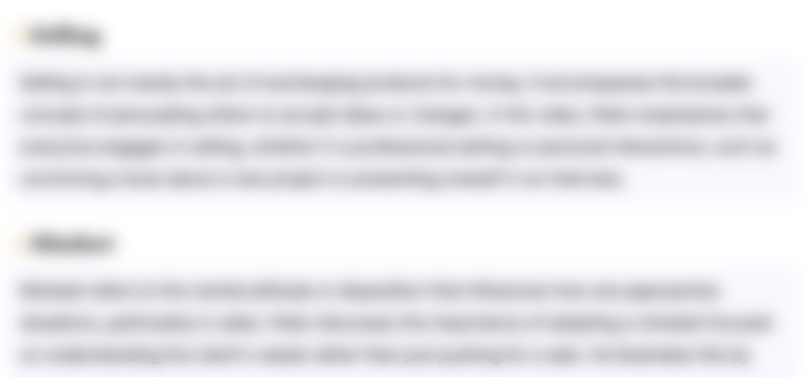
This section is available to paid users only. Please upgrade to access this part.
Upgrade NowHighlights
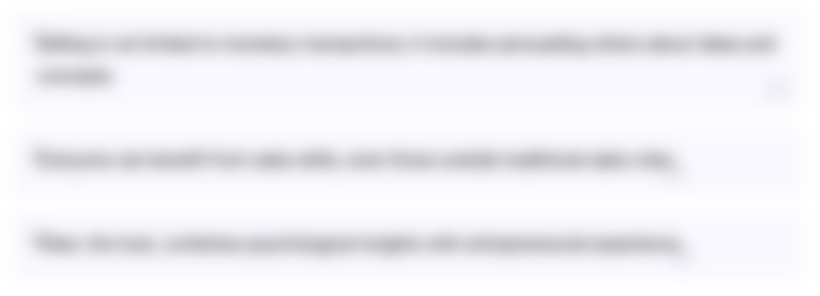
This section is available to paid users only. Please upgrade to access this part.
Upgrade NowTranscripts
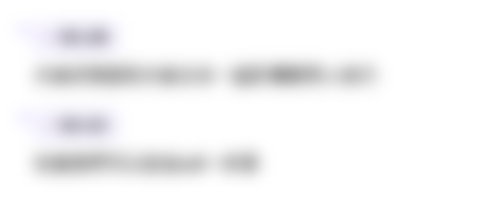
This section is available to paid users only. Please upgrade to access this part.
Upgrade Now5.0 / 5 (0 votes)