Safety Training Video : Why Lock-Out, Tag-Out Is Vitally Important By Panduit
Summary
TLDRThis video explains the importance of controlling hazardous energy sources in the workplace to prevent accidents and injuries. It covers OSHA's lockout/tagout (LOTO) program, which mandates procedures to ensure equipment is safely de-energized before maintenance. Key elements of a LOTO program include written energy control procedures, employee training, appropriate LOTO devices, and periodic inspections. It details the roles of authorized, affected, and other employees, and emphasizes proper shutdown and startup procedures to ensure safety. By following LOTO standards, workplaces can protect workers and comply with regulations, reducing risks of serious injury or fatalities.
Takeaways
- ⚡ Power and energy in various forms, such as electric, pneumatic, and hydraulic, are prevalent in the workplace and need to be controlled to prevent serious accidents.
- 🚨 OSHA reports that uncontrolled energy sources cause 50,000 injuries and 120 fatalities annually in the U.S., making safety procedures critical during maintenance.
- 🔒 Lockout/Tagout (LOTO) procedures are necessary to control hazardous energy during machine servicing or maintenance to prevent accidental startup.
- 📋 A comprehensive LOTO program includes four elements: energy control procedures, employee training, lockout/tagout hardware, and periodic inspections.
- 📝 Written energy control procedures must be machine-specific and clearly outline steps for safe shutdown, isolation, and securing of equipment.
- 👩🏫 Training is mandatory for employees under OSHA standards and must be tailored based on their responsibilities, whether they are authorized, affected, or other workers.
- 🔑 Lockout/tagout devices must meet specific OSHA requirements, be durable, identifiable, and prevent removal without tools like bolt cutters.
- 🛠 Inspections of lockout/tagout procedures must be done at least annually to ensure ongoing compliance and retraining where necessary.
- 🚧 Lockout/tagout procedures include physically locking and tagging out machines to ensure all energy sources are isolated before maintenance begins.
- 🔁 Group lockout/tagout procedures ensure that multiple employees working on the same equipment are protected, and coordination between shifts is critical.
Q & A
What are some forms of energy that can be present in a facility?
-Energy in a facility can exist in various forms, including electric, pneumatic, hydraulic, chemical, mechanical, and thermal.
Why is it important to control energy before servicing or maintaining machines?
-Uncontrolled energy can pose serious health and safety hazards. OSHA reports that in the U.S. alone, accidents involving uncontrolled energy sources result in 50,000 injuries and 120 deaths each year.
What is the purpose of the Lockout/Tagout (LOTO) program?
-The Lockout/Tagout program is designed to control hazardous energy during servicing or maintenance of machines and equipment, preventing the unexpected startup of equipment or release of stored energy that could cause injury.
What are the four elements of a complete Lockout/Tagout energy control program?
-The four elements are energy control procedures, employee training, Lockout/Tagout hardware, and periodic internal inspections.
What should energy control procedures document?
-Energy control procedures should document the scope, purpose, authorization, rules, and techniques used to control hazardous energy, as well as the steps for safely shutting down equipment and removing Lockout/Tagout devices.
What types of training are required under the Lockout/Tagout program?
-Training must be provided to authorized, affected, and other employees. Authorized employees are responsible for implementing energy control procedures, while affected and other employees must recognize when these procedures are in place.
What requirements must Lockout/Tagout devices meet according to OSHA?
-Lockout/Tagout devices must be standardized by color, shape, or size. Tags must be durable, identifiable, and include the employee's name. Locks must be substantial enough to prevent removal without special tools.
How often must Lockout/Tagout procedures be inspected?
-Lockout/Tagout procedures must be inspected at least once a year by an authorized employee other than the one performing the procedure. These inspections ensure procedures are adequate and properly implemented.
What steps must be taken before removing Lockout/Tagout devices and restoring energy?
-Before removing Lockout/Tagout devices, all tools and equipment must be removed, machine guards restored, and employees notified that energy will be restored. Only the employee who applied the devices may remove them.
What should be done when multiple employees need to perform servicing or maintenance?
-In cases where multiple employees are involved, group Lockout/Tagout procedures should be used, with each employee applying their own lock to a group lockout device to ensure safety for all workers.
Outlines
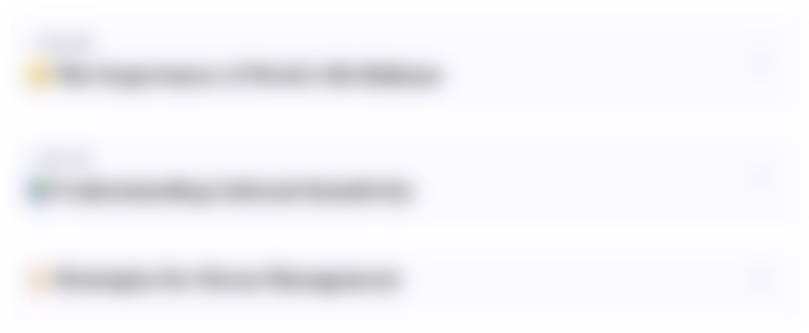
This section is available to paid users only. Please upgrade to access this part.
Upgrade NowMindmap
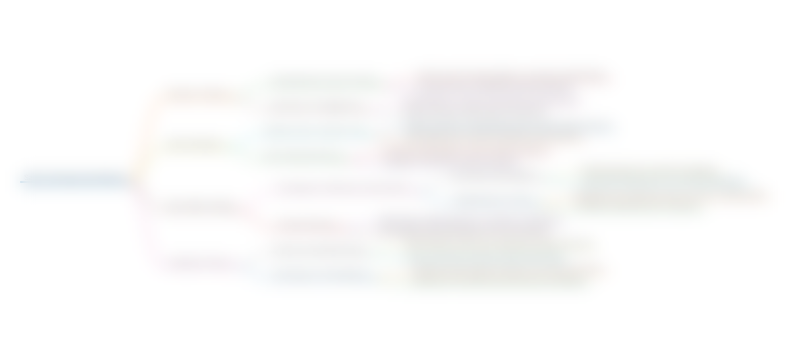
This section is available to paid users only. Please upgrade to access this part.
Upgrade NowKeywords
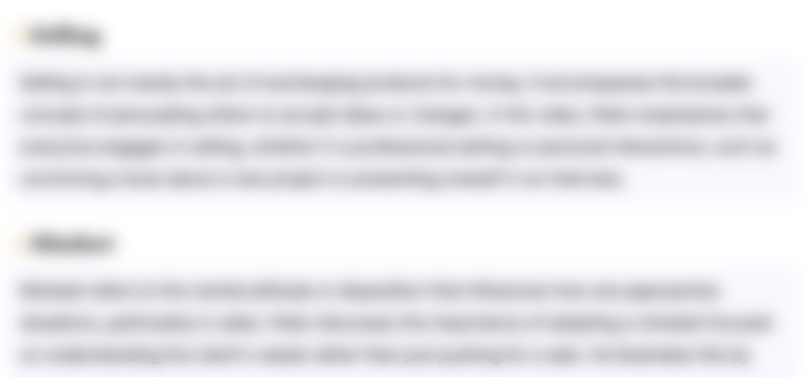
This section is available to paid users only. Please upgrade to access this part.
Upgrade NowHighlights
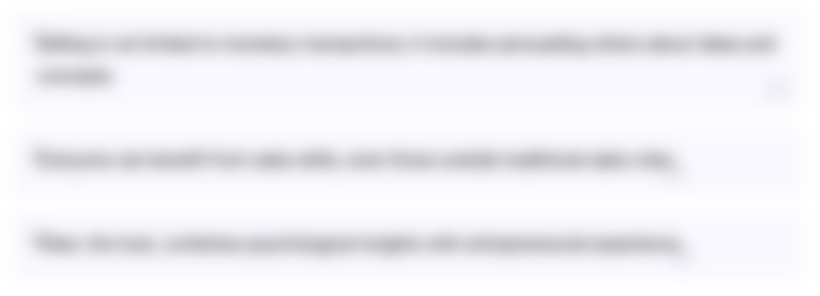
This section is available to paid users only. Please upgrade to access this part.
Upgrade NowTranscripts
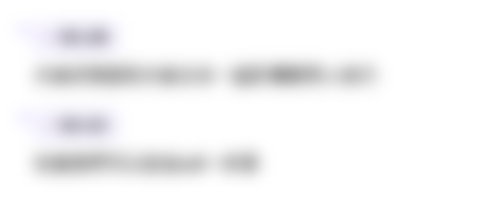
This section is available to paid users only. Please upgrade to access this part.
Upgrade NowBrowse More Related Video
5.0 / 5 (0 votes)