Lockout/Tagout (2018)
Summary
TLDRThe video script emphasizes the importance of lockout/tagout procedures in safeguarding nearly 3.3 million workers from machinery-related injuries and fatalities. It outlines the OSHA standard 29 CFR 1910.147, detailing how to control hazardous energy during maintenance. The script covers training requirements, proper lockout/tagout techniques, and special considerations for group work and contractor scenarios. It stresses the need for compliance to prevent accidents and the critical role of regular inspections and employee retraining.
Takeaways
- ๐ Lockout tagout is a safety procedure designed to prevent accidental activation of machinery during maintenance, protecting nearly 3.3 million employees each year.
- ๐จ The standard is crucial for compliance, preventing an estimated 120 fatalities and 50,000 injuries annually.
- ๐ ๏ธ It applies to all employees working with machinery that requires service or maintenance where hazardous energy could be released.
- ๐ OSHA's 29 CFR 1910.147 standard mandates lockout tagout to control hazardous energy before servicing or maintenance.
- ๐ทโโ๏ธ Three types of employees are identified for training: authorized employees, affected employees, and other employees, each with specific training requirements.
- ๐ ๏ธ Employers must provide written lockout tagout procedures and ensure they are followed, including isolating machines from energy sources and using locks or tags.
- ๐ Lockout devices must be standardized, durable, and identifiable, while tagout devices must be clear, tough, and attached with a non-reusable cable.
- ๐ Annual inspections of lockout tagout procedures by employers are required to ensure compliance and safety.
- ๐ Special procedures are needed for group lockout tagout, outside contractors, and during shift changes to maintain continuity of protection.
- โ ๏ธ The script emphasizes the importance of following lockout tagout procedures correctly to prevent injuries and fatalities.
Q & A
What does 'lockout tagout' refer to in the context of workplace safety?
-Lockout tagout refers to specific practices and procedures designed to safeguard employees from the unexpected energization or startup of machinery and equipment, or the release of hazardous energy during service or maintenance activities.
Why is compliance with the lockout tagout standard important?
-Compliance with the lockout tagout standard is crucial as it is estimated to prevent 120 fatalities and 50,000 injuries each year, ensuring the safety of employees working with machinery that may require servicing or maintenance.
Which standard does OSHA address lockout tagout under, and what is its purpose?
-OSHA addresses lockout tagout under the standard 29 CFR 1910.147, 'The Control of Hazardous Energy.' Its purpose is to ensure that machines or equipment are isolated from energy sources and rendered inoperative before servicing or maintenance to prevent accidental activation.
How does the lockout tagout standard protect employees?
-The lockout tagout standard protects employees by requiring that before any servicing or maintenance is performed, machines or equipment must be isolated from the energy source, rendered inoperative, and secured with lockout or tagout devices to prevent unexpected energization or startup.
What are the estimated benefits of the lockout tagout standard in industries like automobile and steelmaking?
-The lockout tagout standard has reduced fatalities from unexpected activation of machinery in industries such as automobile and steelmaking by 20 to 55 percent since its implementation.
What should be included in an employer's written lockout tagout procedures?
-Employers should provide written procedures that outline the scope, purpose, authorization rules, and techniques for the lockout tagout process, including specific steps for isolating, blocking, shutting down the machine or equipment, and the responsibilities for lockout tagout devices.
Who are the three types of employees identified by OSHA for lockout tagout training, and what training should they receive?
-OSHA identifies 'authorized employees,' who are trained to lockout or tagout machines; 'affected employees,' who must understand the importance of not using locked out or tagged out machines; and 'other employees,' who need to understand lockout tagout rules but are not part of the process. Each type receives training appropriate to their role.
What is the responsibility of an authorized employee in the lockout tagout process?
-An authorized employee is responsible for knowing how machines are powered, recognizing hazardous energy sources, isolating and controlling energy sources, and disconnecting equipment from power sources using lockout or tagout methods.
How often should the lockout tagout energy control procedure be inspected by the employer?
-The lockout tagout energy control procedure should be inspected by the employer at least once a year to ensure all employees are following the procedure and to identify and correct any problems.
What are the criteria that locks and tags used in the lockout tagout procedure must meet?
-Locks must be durable, standardized within the facility, and strong enough to prevent removal without heavy force or tools. Tags must be standardized, readable in various conditions, tough, and attached with a non-reusable, self-locking nylon cable that can withstand significant pressure.
What steps should be followed when removing lockout tagout devices from a machine?
-Before removing lockout tagout devices, the authorized employee must verify isolation, ensure tools are removed, confirm all employees are at a safe distance, and notify all affected employees. If the employee who applied the device is absent, the employer must verify their absence, attempt to contact them, and inform them of the removal upon their return.
Outlines
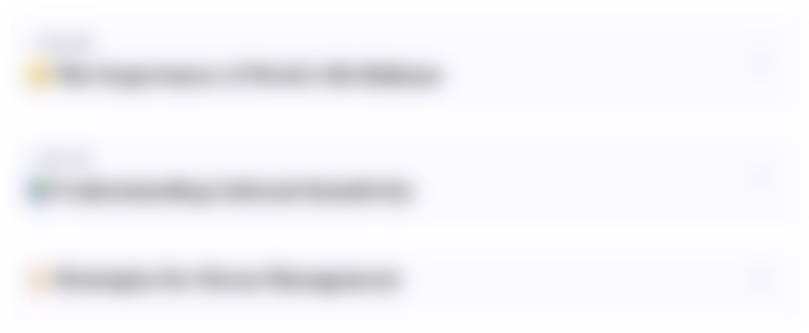
This section is available to paid users only. Please upgrade to access this part.
Upgrade NowMindmap
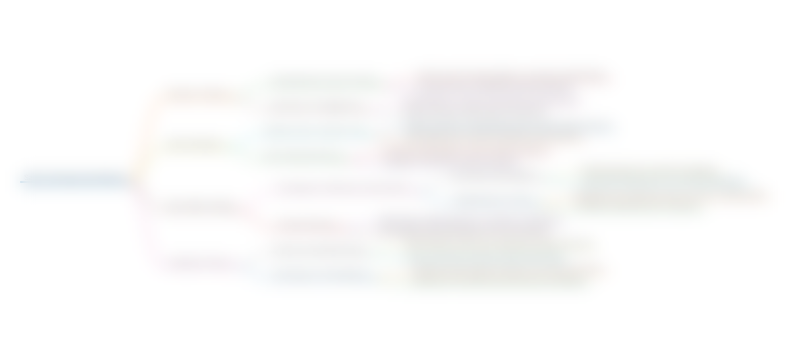
This section is available to paid users only. Please upgrade to access this part.
Upgrade NowKeywords
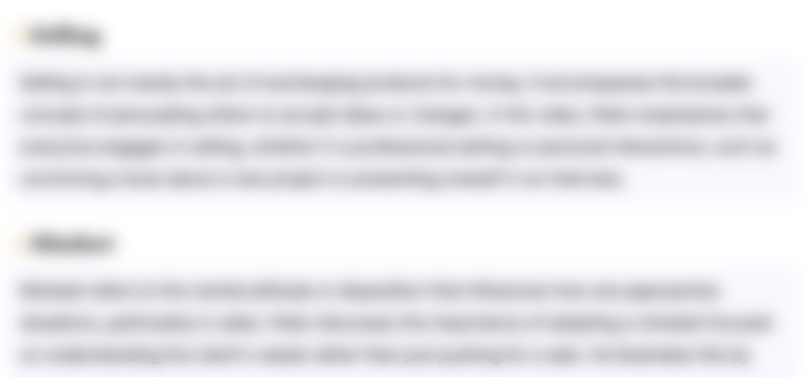
This section is available to paid users only. Please upgrade to access this part.
Upgrade NowHighlights
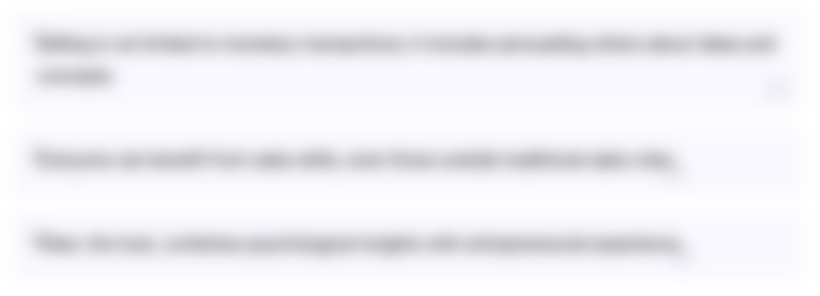
This section is available to paid users only. Please upgrade to access this part.
Upgrade NowTranscripts
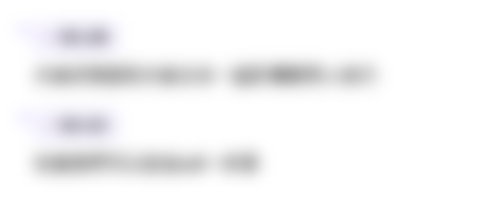
This section is available to paid users only. Please upgrade to access this part.
Upgrade NowBrowse More Related Video
5.0 / 5 (0 votes)