Milling machine tutorial - cutter selection, speeds and feeds, coolant, high speed machining
Summary
TLDRThis tutorial covers cutter selection, speed, and feed for vertical milling machines, focusing on CNC but applicable to manual machines. It emphasizes choosing the right cutter size and material, with a case study on milling aluminum. Key points include using the largest appropriate cutter, avoiding overly long tools for rigidity, selecting tool material and coatings based on the task, and calculating cutting parameters like spindle speed and feed rate. The video also touches on high-speed machining, climb vs. conventional milling, and the importance of rigidity in machining operations.
Takeaways
- ๐ง The tutorial focuses on cutter selection, speeds, and feeds for vertical milling machines, with emphasis on CNC but also applicable to manual machines.
- โ๏ธ For a simple pocket milling task in aluminum, a 3/8-inch diameter milling cutter is recommended to match the part's geometry.
- ๐ ๏ธ It's crucial to choose the largest diameter cutter possible that can produce the correct part geometry to ensure efficient material removal.
- ๐ Cutter length should be as short as necessary to maintain rigidity and avoid deflection, which can lead to poor surface finishes.
- ๐ก๏ธ High Speed Steel (HSS) tooling is suggested for hobbyists and small shops due to its cost-effectiveness and suitability for aluminum and plastic materials.
- โ๏ธ Coating on tools can be beneficial for tool life, but for aluminum and plastic, an uncoated sharp tool is often preferred to avoid dulling from material burnishing.
- ๐ฉ The spindle speed (RPM) for the cutter is determined by the material properties and should not exceed the tool's limit to prevent edge breakdown.
- ๐ The feed rate, or how fast the cutter moves through the material, is influenced by the chip load, which is the thickness of material removed per tooth.
- ๐ฉ When milling slots, it's advised not to plunge more than half the cutter's diameter to prevent tool breakage and ensure material is removed in manageable amounts.
- ๐ง Coolant is beneficial when machining aluminum due to its softness causing chips to stick and heat to build up; it helps in chip evacuation and cooling.
Q & A
What is the main focus of the tutorial in the script?
-The tutorial focuses on cutter selection, speeds, and feeds for vertical milling machines, specifically for CNC milling but also applicable to manual machines.
Why did the instructor choose the specific part for demonstration?
-The instructor chose the part because it has both an outside feature and an inside feature, which allows the tutorial to cover a broad range of cutter selection and application scenarios.
What is the first consideration when selecting a milling cutter according to the script?
-The first consideration when selecting a milling cutter is to use the largest diameter cutter that can produce the correct geometry for the part being machined.
Why is it not advisable to use a very long cutter for a shallow feature?
-Using a very long cutter for a shallow feature is not advisable because the extra length of the cutter can flex, leading to a bad finish due to wobbling and reduced rigidity.
What are the advantages of using carbide tooling over high speed steel tooling?
-Carbide tooling allows for faster machining speeds, which is beneficial for production shops where time is a critical factor.
Why might coatings on cutting tools be considered a waste of time for certain materials?
-Coatings on cutting tools might be considered a waste of time for materials like aluminum and plastics because these soft materials do not benefit from the hardness provided by coatings, and an uncoated sharp tool works just as well.
How is the spindle speed for milling aluminum determined?
-The spindle speed for milling aluminum is determined by consulting a speeds and feeds chart, which provides a recommended range based on the material and tooling material properties.
What is the significance of chip load in milling operations?
-Chip load signifies the amount of material removed per tooth of the cutter as it passes through the material. It is crucial for determining the feed rate and ensuring that the tool does not dull prematurely or cause excessive wear.
Why is it important to not plunge a milling cutter more than half its diameter in one pass?
-Plunging a milling cutter more than half its diameter in one pass can lead to the cutter snapping off due to the excessive force applied to the cutter.
What is the purpose of doing roughing cuts before finishing cuts in milling?
-Roughing cuts are done to remove the majority of material quickly, followed by finishing cuts to achieve the final dimension and surface finish with less cutting load and deflection on the cutter.
How does the use of coolant affect the milling process, especially with aluminum?
-Coolant, either mist or flood, is beneficial when milling aluminum as it helps to remove heat and chips more effectively, preventing the material from sticking to the cutter and reducing the risk of global heating.
Outlines
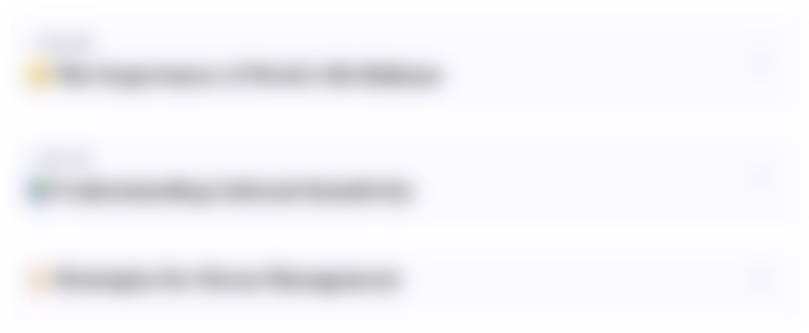
This section is available to paid users only. Please upgrade to access this part.
Upgrade NowMindmap
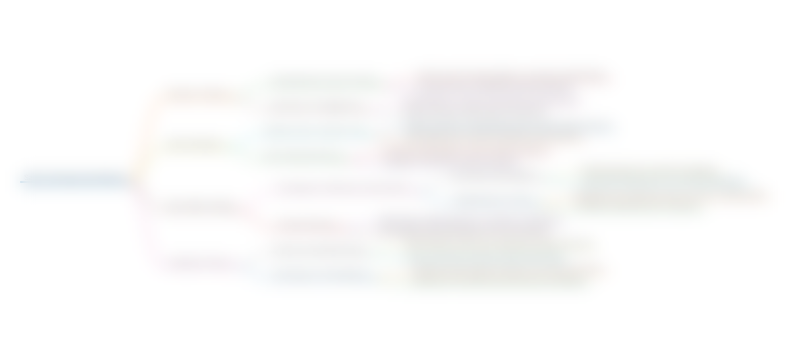
This section is available to paid users only. Please upgrade to access this part.
Upgrade NowKeywords
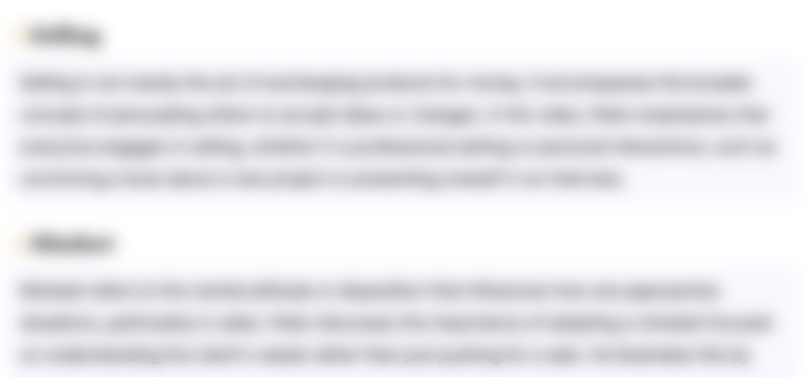
This section is available to paid users only. Please upgrade to access this part.
Upgrade NowHighlights
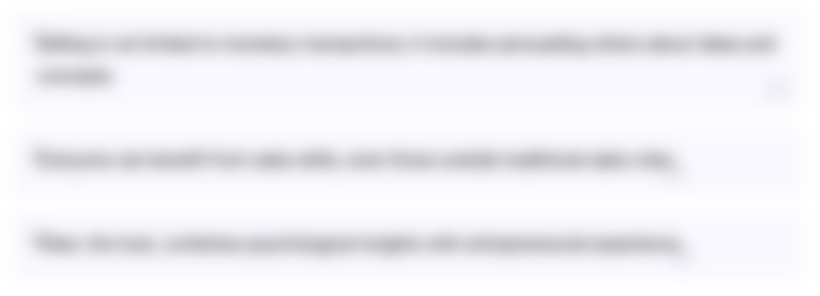
This section is available to paid users only. Please upgrade to access this part.
Upgrade NowTranscripts
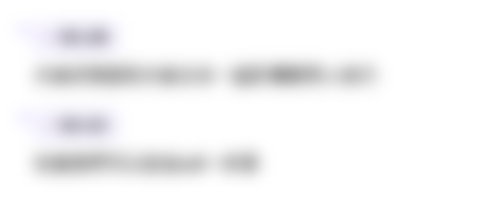
This section is available to paid users only. Please upgrade to access this part.
Upgrade Now5.0 / 5 (0 votes)