Rolling - Industrial Process - Mechanical
Summary
TLDRThe video script details the hot rolling process of steel, essential for shaping due to its resistance when cold. Steel is heated to the right temperature in a furnace, then rolled between massive mill stands exerting tens of millions of Newtons. The layout of rolling mills varies, with different roll arrangements for products like flat strips or construction sections. After hot rolling, steel is cooled and may undergo cold rolling for thinner, flatter products, often with added coatings for protection and aesthetics.
Takeaways
- 🔥 Steel is resistant to shaping when cold, so it's rolled hot to ensure malleability.
- 🔧 The process involves heating steel to the right temperature in a furnace with multiple temperature control zones.
- 🏗️ Hot rolling squeezes the steel between rolls to achieve the desired thickness and shape, requiring immense forces.
- 🛠️ Mill stands, equipped with powerful electric motors and robust bearings, apply the necessary pressure during rolling.
- 🔄 Rolling mills can have different layouts, from single to multiple stands, arranged side by side or in a line.
- 📏 Mill rolls can be plain for flat products like cladding or profiled for construction sections like beams and columns.
- 🔄 Different roll arrangements are used depending on the product, such as two-high, three-high, and four-high stands.
- 🏭 Universal beam mills feature both horizontal and vertical rolls to bear on the steel simultaneously for accurate rolling.
- ♻️ After hot rolling, steel is cooled and prepared for further processing like cold rolling or dispatch.
- 🔄 Cold rolling is a subsequent process used to produce thinner, flatter products with improved forming properties and surface finish.
Q & A
Why is steel rolled while it's hot?
-Steel is rolled while it's hot because it is highly resistant to shaping when cold. Hot rolling ensures the steel is at the correct temperature for shaping and rolling.
What is the purpose of the furnace in the steel rolling process?
-The furnace is used to heat the steel to the correct temperature for rolling. It has several temperature control zones that the steel travels through to reach the optimal temperature.
What forces are exerted by the rolls during the hot rolling process?
-During hot rolling, the rolls exert forces of tens of millions of Newtons, equivalent to the weight of thousands of tons, to achieve the desired thickness and shape of the steel.
What are Mill stands and what is their role in the hot rolling process?
-Mill stands are massive bearings mounted in housings of enormous strength and driven by powerful electric motors. They are used to squeeze the steel between rolls to achieve the final thickness and shape.
How does the layout of a Rolling Mill vary?
-The layout of a Rolling Mill can vary from a simple single stand Mill to several stands positioned either side by side or in a line, depending on the product being rolled.
What types of mill rolls are used for different steel products?
-Mill rolls can be plain for flat products like strip used for cladding, or profiled for sections like beams and columns used in construction.
What is the simplest roll arrangement used in a rolling mill and for what type of product is it used?
-The simplest roll arrangement is a two-high stand, which is mainly used for long products such as sections.
How do four-high stands differ from two-high stands in terms of roll arrangement?
-Four-high stands have two work rolls in contact with the steel supported by larger backup rolls. This arrangement prevents distortion caused by the rolling face and provides greater accuracy for rolling flat products.
What is a Universal beam Mill and how does it differ from other mills?
-A Universal beam Mill includes stands with both horizontal and vertical rolls bearing on the steel simultaneously, allowing for the rolling of complex shapes.
What is the purpose of cold rolling of strip and how does it differ from hot rolling?
-Cold rolling of strip is used to produce a thinner, flatter product than is possible on a hot mill, down to a thickness of 0.15 mm. It also allows for better forming properties, surface finish, and can be coated with materials like zinc, tin, or plastic for protection and decorative purposes.
How is the rolled steel prepared for further processing or dispatch after the hot rolling process?
-After hot rolling, the steel is cooled in a way appropriate to its end use and then prepared for further processing or dispatch, which may include cold rolling or coating.
Outlines
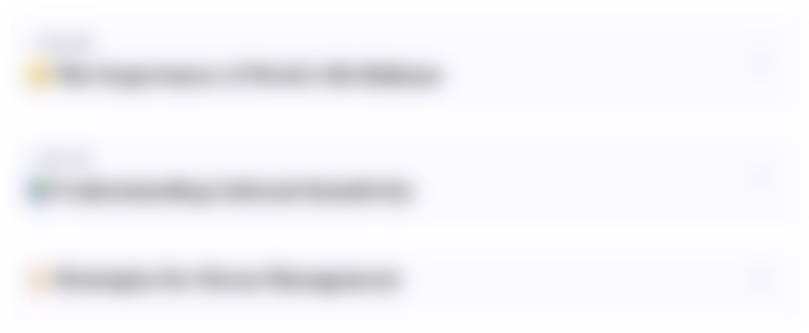
This section is available to paid users only. Please upgrade to access this part.
Upgrade NowMindmap
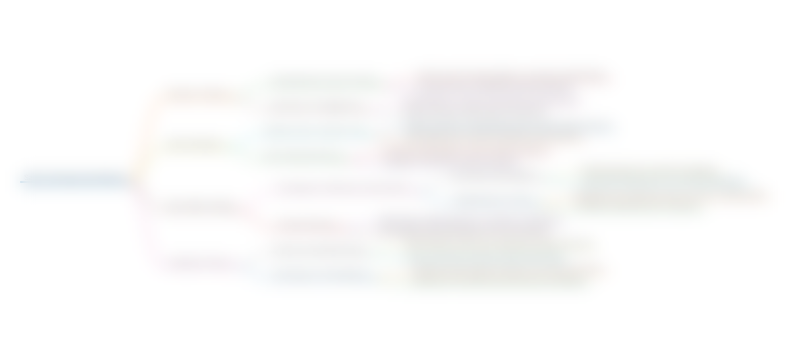
This section is available to paid users only. Please upgrade to access this part.
Upgrade NowKeywords
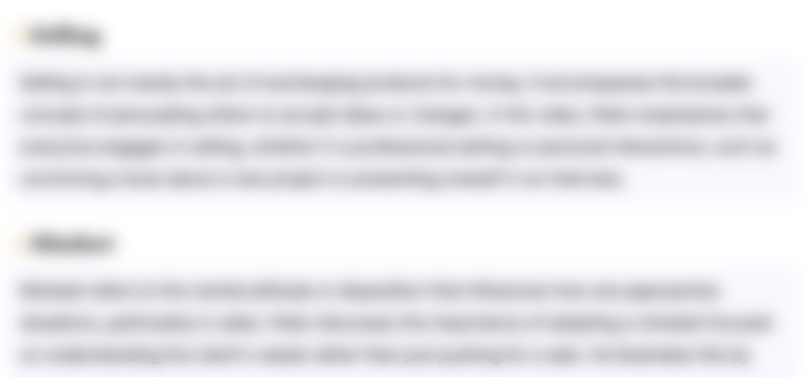
This section is available to paid users only. Please upgrade to access this part.
Upgrade NowHighlights
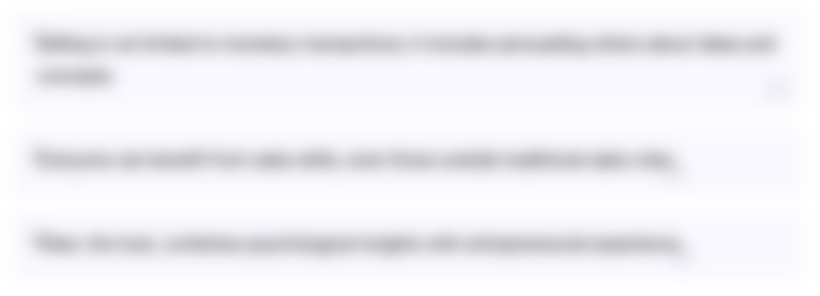
This section is available to paid users only. Please upgrade to access this part.
Upgrade NowTranscripts
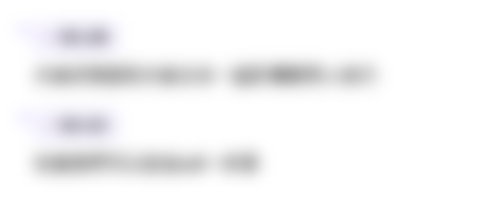
This section is available to paid users only. Please upgrade to access this part.
Upgrade Now5.0 / 5 (0 votes)