Hot Rolling Mill
Summary
TLDRThis film provides an insightful overview of the hot rolling process in steel production. Beginning with the reheating of slabs to around 1200°C, the material undergoes various stages, including surface cleansing, reduction in thickness, and coiling. Key steps include rolling in the roughing mill, temperature equalization in the coil box, and precision rolling in the finishing mill to achieve the desired thickness and material properties. Finally, the coiled steel is either sold directly or processed further, such as through cold rolling, ensuring high-quality end products.
Takeaways
- 😀 The hot rolling process involves the plastic deformation of steel at high temperatures to produce long strips used in manufacturing products like steel plates.
- 😀 Material is heated to around 1200°C in walking beam furnaces, which are crucial for ensuring proper material properties by dissolving carbides and nitrates.
- 😀 The heating process must be controlled, as insufficient heating can lead to poor material properties due to undissolved carbides and nitrates.
- 😀 A mill scale (oxide layer) forms on the surface of the material during heating, which must be removed before rolling to prevent defects in the final product.
- 😀 High-pressure water sprays (160 bar) are used to clean the material’s surface of the oxide layer before the rolling process.
- 😀 In the roughing mill, the material is reduced in thickness from 22 cm to about 3 cm in multiple passes using a powerful four-high rolling mill.
- 😀 Vertical rolls control the width of the material during the roughing process, and the material is referred to as transfer bars after this stage.
- 😀 The coil box stores transfer bars, helping to equalize temperature differences and improve material uniformity before the next stage of rolling.
- 😀 In the finishing mill, transfer bars (now strips) are rolled into thinner sheets ranging from 16 mm to 1.8 mm, with precise control over profile and flatness.
- 😀 The cooling rate in the finishing process is carefully controlled to ensure the proper microstructure and material properties before the strip is coiled and prepared for further processing or direct sale.
Q & A
What is the primary goal of the hot rolling process described in the script?
-The primary goal of the hot rolling process is to reduce the thickness of steel material at high temperatures and produce long strips that can be used to manufacture products like steel plates.
Why is heating the material in the reheating furnace important?
-Heating the material in the reheating furnace is essential to achieve the correct material properties. If the material is not sufficiently heated, incorrect material properties can arise due to carbides and nitrates failing to dissolve.
What is the function of the walking beam furnaces in the reheating process?
-The walking beam furnaces feed the material through the oven and heat it to approximately 1200°C. This is necessary for ensuring the material is at the right temperature for further processing.
What is mill scale, and why is it problematic during the hot rolling process?
-Mill scale is an oxide layer that forms on the surface of the material due to its reaction with oxygen in the air. If the oxide layer is not removed, it can be rolled into the steel, negatively affecting the surface quality of the final product.
How is the mill scale removed from the material before it enters the rolling mill?
-The mill scale is removed by spraying water at high pressure (160 bar) to cleanse the surface of the material before it enters the roughing mill.
What happens to the material in the roughing mill, and what is its purpose?
-In the roughing mill, the material is rolled from its original thickness of 22 cm down to about 3 cm. This is a significant reduction, and the purpose is to prepare the material for further thinning and shaping in subsequent stages.
What is the function of the coil box after the roughing mill?
-The coil box's primary purpose is to save space. It also helps in equalizing the temperature throughout the transfer bar by coiling the material, which minimizes temperature differences between its ends.
What role does the up looper play in the finishing mill?
-The up looper controls the line speed and strip tension while also adjusting itself to maintain the correct profile and flatness of the strips being rolled in the finishing mill.
What are the key factors controlled during the rolling process in the finishing mill?
-In the finishing mill, the key factors controlled include the strip profile and flatness. The first stands of the mill manage the profile, while the later stands focus on ensuring the strip is flat.
How does the cooling process affect the final product?
-The cooling process is critical for producing the desired microstructure and material properties in the final product. The cooling rate is adjusted based on the strip's characteristics to ensure it meets the required specifications.
Outlines
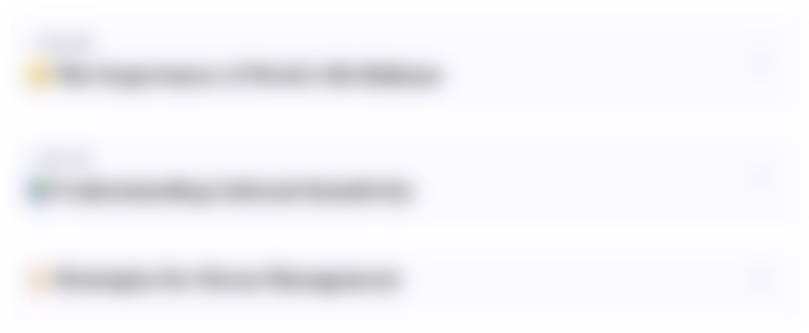
This section is available to paid users only. Please upgrade to access this part.
Upgrade NowMindmap
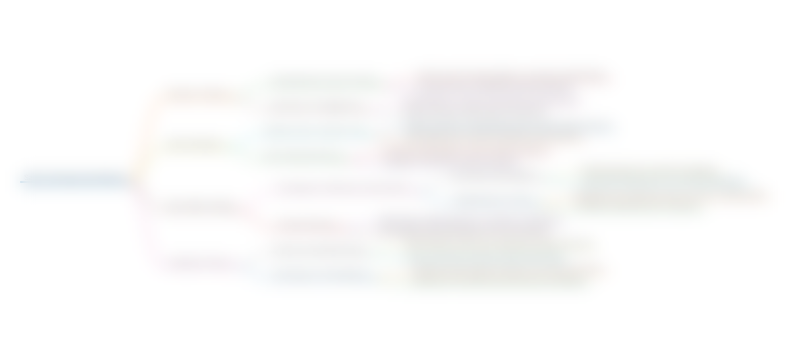
This section is available to paid users only. Please upgrade to access this part.
Upgrade NowKeywords
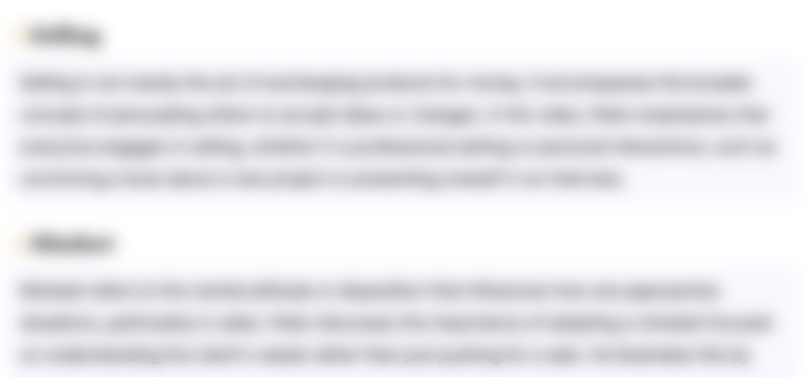
This section is available to paid users only. Please upgrade to access this part.
Upgrade NowHighlights
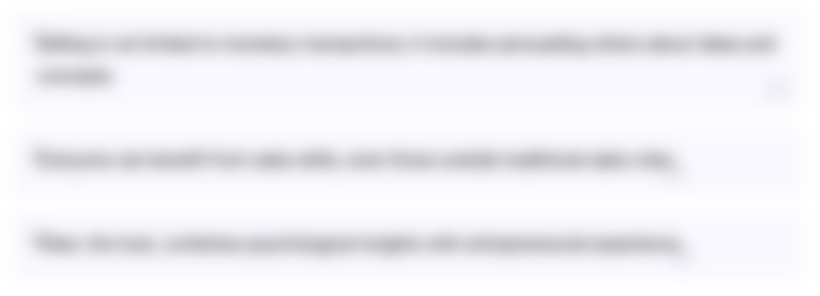
This section is available to paid users only. Please upgrade to access this part.
Upgrade NowTranscripts
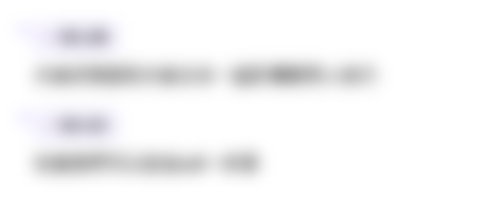
This section is available to paid users only. Please upgrade to access this part.
Upgrade Now5.0 / 5 (0 votes)