Learn How Kanban Systems are Used in a Lean Manufacturing Environment
Summary
TLDRThis module from Gemba Academy introduces the concept of Kanban in manufacturing, explaining its origin from Toyota's Just-In-Time production system. Kanban, a Japanese term for 'sign board,' serves as a visual signal for production or movement of items, aiming to prevent overproduction and inventory waste. The video discusses various types of Kanban systems, including the 2-card, 1-card, and 2-bin systems, highlighting their functions in setting production limits, linking material and information flow, and making abnormalities visible. The course promises further exploration into calculating Kanban quantities and managing the system effectively.
Takeaways
- 📚 Kanban is a Japanese term meaning 'sign board' or 'sign', used in production control to authorize the production or movement of items.
- 🚀 The Kanban system is likened to the nervous system in a lean production system, connecting information flow with material flow.
- 🔧 Developed by Taiichi Ohno of Toyota, Kanban was initially designed to prevent overproduction and reduce inventory costs.
- 🛒 Inspired by American supermarkets, the system mimics the 'pull' method of restocking shelves only after products are consumed.
- 📉 Kanban is a foundational tool in the Just in Time (JIT) system, aiming to produce or move items only when required.
- 🔄 The system contrasts with 'push' systems by maintaining a tight chain of production, ensuring the right inventory at the right time.
- ⚖️ Kanban sets production limits, using cards or signals as a form of currency that must be present for production or movement of items.
- 🔗 Kanban physically links material and information flow, making abnormalities visible by ensuring materials are always accompanied by a signal.
- 📊 The classic 2-card system uses production and withdrawal cards to signal the need for product replenishment.
- 📦 The 1-card system and 2-bin system are variations of Kanban that use alternative signals, such as empty containers or bins, to indicate the need for restocking.
Q & A
What does the term 'Kanban' literally mean in Japanese?
-The term 'Kanban' literally means 'sign board' or 'sign' in Japanese.
In the context of production control, what does Kanban refer to?
-In the context of production control, Kanban refers to the visual signals that authorize the production or movement of items.
Who developed the Kanban system and for what company?
-The Kanban system was developed by Taiichi Ohno of the Toyota Motor Corporation.
What was Taiichi Ohno's original aim in creating the Kanban system?
-Ohno's original aim was to stop overproduction in his machine shop, which was creating large inventories and costing a lot of money.
What inspired Ohno to create the Kanban system?
-Ohno was inspired by the product replenishment methods he observed in American supermarkets, particularly the way shelves were restocked only after products were consumed by customers.
How does a Kanban system connect information flow with material flow?
-A Kanban system connects information flow with material flow by attaching Kanban cards to the actual goods.
What is the basic function of a Kanban in a production system?
-At the most basic level, a Kanban is a signal that authorizes the production or movement of items.
What is the main difference between a push system and a Kanban pull-based system?
-In a push system, production is not based on demand, leading to uneven inventory levels. In contrast, a Kanban pull-based system produces only when required, resulting in a tight, efficient inventory.
What are some of the wastes that a Kanban system can be full of?
-A Kanban system can be full of wastes such as excessive handling, inventory, and processing.
What is the ideal Just-in-Time production system according to the script?
-The ideal Just-in-Time production system would use no Kanban at all, producing what the customer wants, when they want it, in the quantity they want.
What are the three main functions of Kanban mentioned in the script?
-The three main functions of Kanban are: setting limits within a production system, physically linking material and information flow, and making abnormalities visible.
What is the information typically contained on a Kanban card?
-A Kanban card normally contains information such as the Part name and number, the Supplier process name, the quantity per container, the Delivery address, the Storage address, and the number of cards in the system.
How does the 2-card system in Kanban work?
-In the 2-card system, a withdrawal Kanban signals the need for product from shipping to the supermarket, and a production Kanban signals the assembly department to replenish the item in the supermarket.
What is the concept behind the '1-card' Kanban system?
-The '1-card' system uses a signal such as empty containers, carts, or colored balls to indicate the need for replenishment, rather than a traditional card.
How does the 2-bin system function in Kanban?
-In the 2-bin system, two bins with equal amounts of goods are used. When the first bin is empty, it signals to replenish two more bins, and the second bin slides forward into position.
Outlines
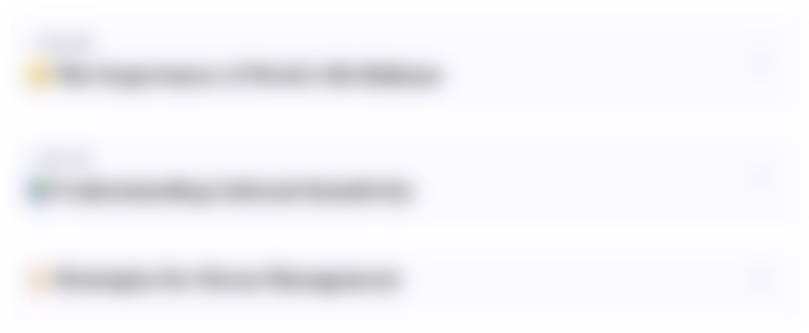
This section is available to paid users only. Please upgrade to access this part.
Upgrade NowMindmap
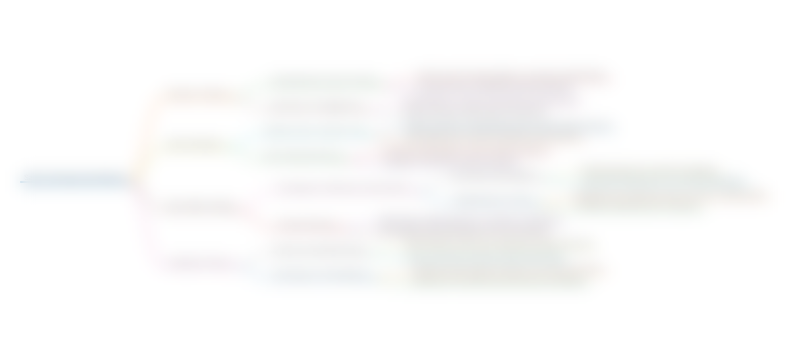
This section is available to paid users only. Please upgrade to access this part.
Upgrade NowKeywords
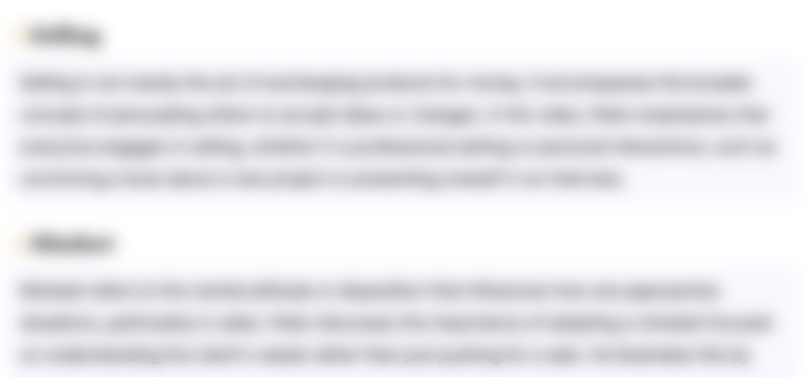
This section is available to paid users only. Please upgrade to access this part.
Upgrade NowHighlights
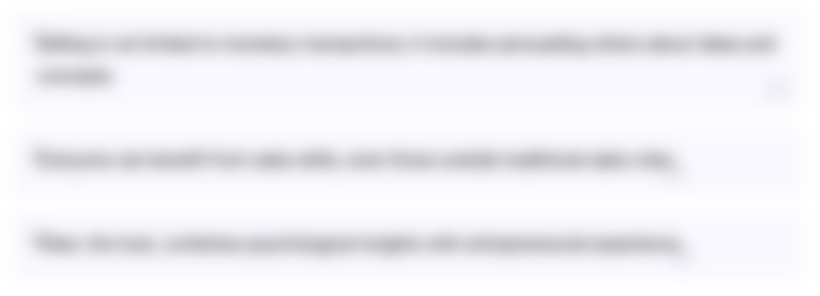
This section is available to paid users only. Please upgrade to access this part.
Upgrade NowTranscripts
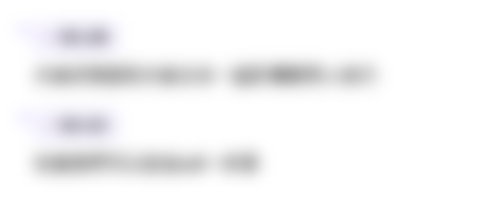
This section is available to paid users only. Please upgrade to access this part.
Upgrade NowBrowse More Related Video

Modelo Toyota de Produção - Just In Time & Kanban
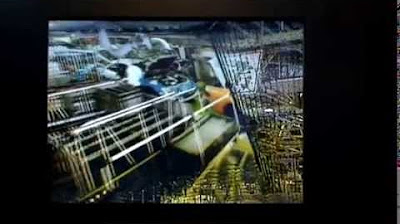
History of the Toyota Production System (TPS)
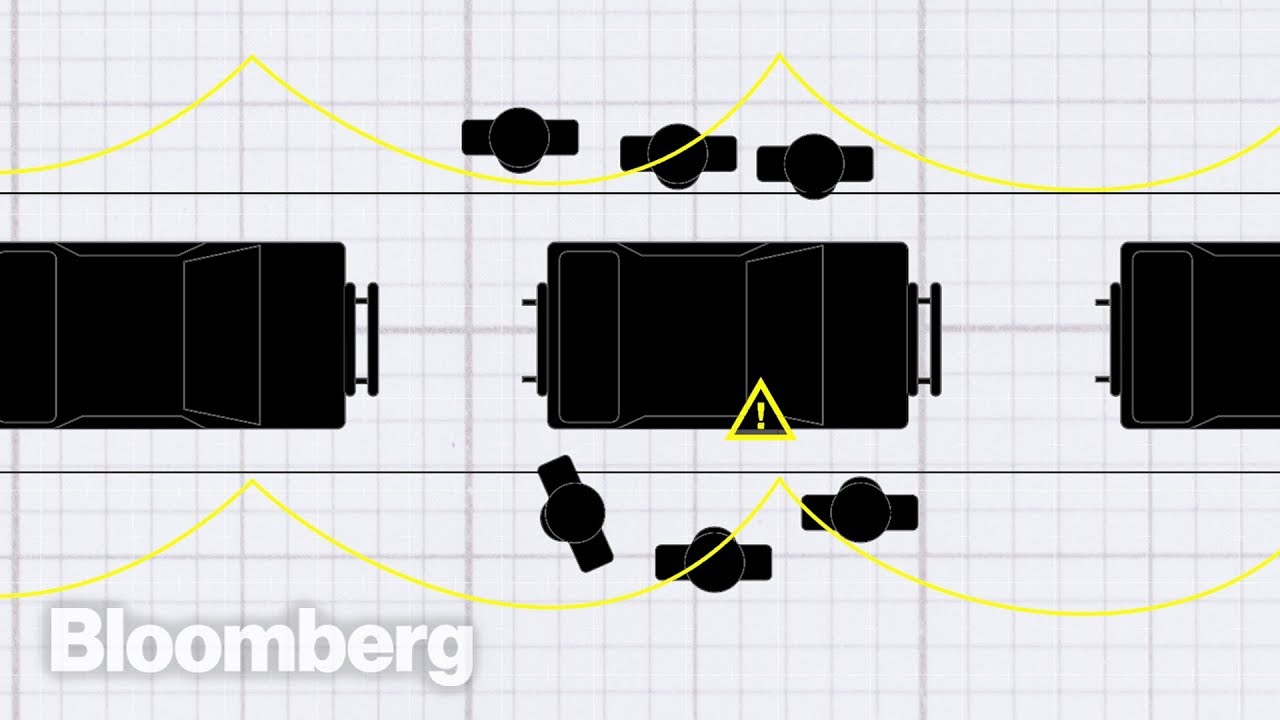
How Toyota Changed The Way We Make Things
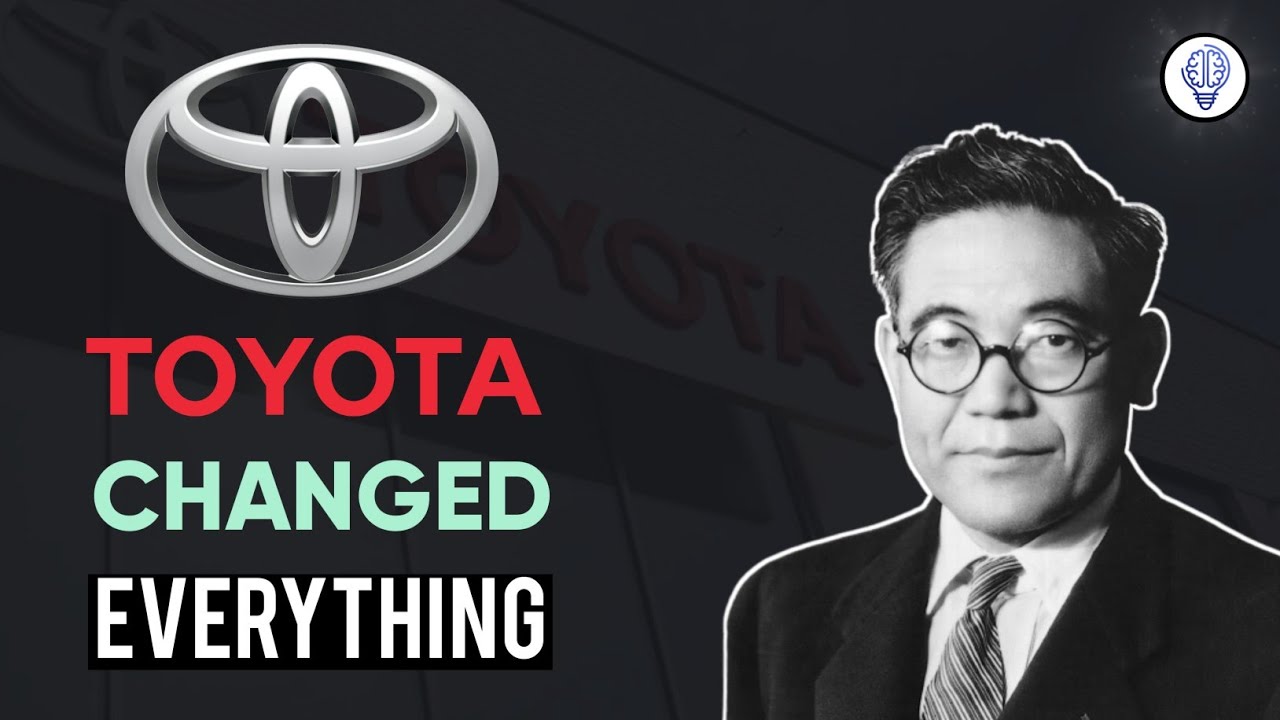
How did Toyota beat FORD & GM using its GENIUS Supply Chain Model?

03. Production Planning - Theory
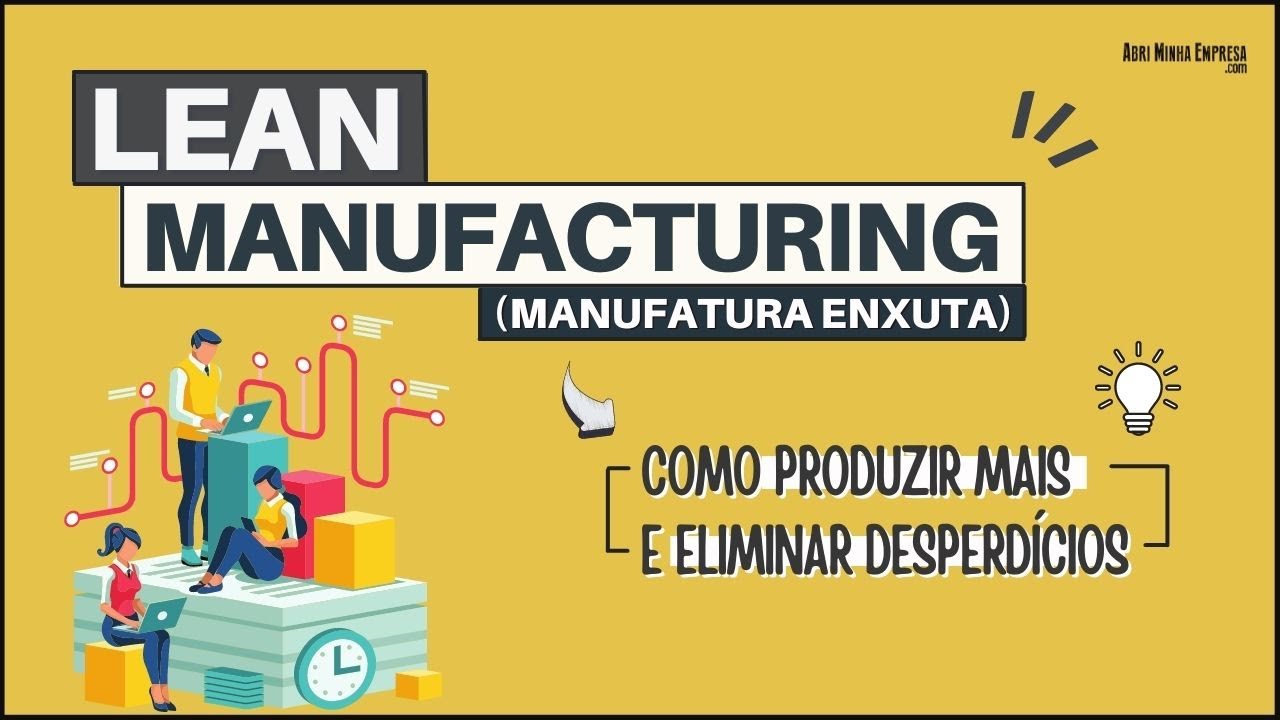
LEAN MANUFACTURING (Manufatura Enxuta) | Conheça os 8 Principais Tipos de Desperdícios
5.0 / 5 (0 votes)