Menon and Menon - Kagal Plant
Summary
TLDRThe script outlines the establishment of a state-of-the-art foundry in India, designed to produce high-quality, cost-effective cylinder blocks and heads for automotive OEMs. A cross-functional team visited leading foundries globally to select top-tier equipment and an optimized layout. The plant features advanced machinery, including an automatic core center, high-speed sand mixer, and casting simulation software, ensuring precision and quality. It also adheres to stringent ISO standards and incorporates pollution control measures. Men and Men Limited, with decades of experience, is set to further enhance its capabilities with a modern CNC-based fettling shop.
Takeaways
- ๐ The automotive OEM industry in India was previously reliant on costly imports for cylinder blocks and heads.
- ๐ A world-class foundry was envisioned to meet the requirements of intricate cylinder blocks and heads locally.
- ๐ A cross-functional team visited leading foundries globally, including in Japan, Thailand, Germany, Spain, and China.
- ๐ญ State-of-the-art equipment and an optimized lean layout were selected to produce castings cost-effectively.
- ๐ง The foundry is capable of producing thin-wall, low-weight, low-variation castings in large numbers.
- ๐ It caters to overseas Auto Giants establishing plants in India.
- ๐ค Automation is a key feature, with robotic handling of cores and palletized core assembly.
- ๐ฅ A continuous core oven with dual fuel and PLC-controlled burner ensures fuel efficiency and core drying.
- ๐ฌ Quality assurance is emphasized with high-end casting simulation software and ISO certified quality management systems.
- ๐ฑ The foundry is committed to environmental sustainability with pollution control equipment like dusting systems and fume extraction.
- ๐ฉ Men and Men Limited, with over four decades of experience, is known for its engine engineering expertise and now operates a high-pressure casting line.
Q & A
What was the initial problem the automotive OEM industry in India faced that led to the establishment of a new foundry?
-The automotive OEM industry in India was facing the issue of relying on costly imports to meet their requirements for new generation cylinder blocks and cylinder heads.
What was the vision behind the creation of this new foundry?
-The vision was to establish a world-class foundry capable of meeting the intricate requirements of cylinder blocks and cylinder heads in a cost-effective manner.
Which international foundries did the cross-functional team visit to gather insights for their project?
-The team visited the Toyota Foundry in Japan, the Kubota Foundry in Thailand, and other foundries in Germany, Spain, and China.
What type of equipment was selected for the new foundry to ensure world-class production?
-The foundry selected world-class equipment based on the inputs and insights gathered from the visits to leading foundries worldwide.
What is special about the core shop in this new foundry?
-The core shop is equipped with a fully automatic core center, cold-box, high-speed core sand mixer, online core cleaning facility, and robotic handling throughout assembly, making, and painting.
How does the continuous core oven in the foundry contribute to fuel efficiency and core drying?
-The continuous core oven features a dual fuel PLC-controlled burner for fuel efficiency and interlocks with the painting robot to ensure core drying at set temperatures.
What is the role of the sand plant in the foundry's production process?
-The sand plant, equipped with a high-speed intensive sand mixer, ensures uniform mixing of green sand and online control of sand compatibility for the right quality sand to be released to molding.
What are the key features of the molding line in the foundry?
-The molding line features multi-piston squeezing for uniform mold hardness, quick pattern change within the cycle time, automatic sprew cutting, mold venting, and automatic core setting.
What is the capacity of the melting furnace and how does it ensure constant pouring rate and temperature?
-The melting furnace has an induction capacity of 6 metric tons per hour, with a double-acting fume hood and load cell for crucibles, ensuring a constant pouring rate and temperature for each box.
How does the foundry ensure the quality and consistency of the metallurgical properties of its products?
-The foundry has a chemical lab and a spectro lab with trained and experienced quality assurance engineers, and uses high-end casting simulation software for proper simulation before actual processing.
What are the environmental pollution control measures implemented in the foundry?
-The foundry has pollution control equipment such as dusting systems, fume extraction systems, and an ammonia scrubber to maintain the quality of the environment in and around the factory.
What certifications does the foundry's quality management system hold?
-The quality management systems are certified to ISO TS 16949 and ISO 9001:2008 standards by UL DQS Incorporated.
What future plans does the foundry have for expanding its capabilities?
-The foundry plans to set up a modern CNC-based fettling shop with equipment like MAWS and SiC, and a machine shop capable of fully finishing cylinder blocks and cylinder heads.
Outlines
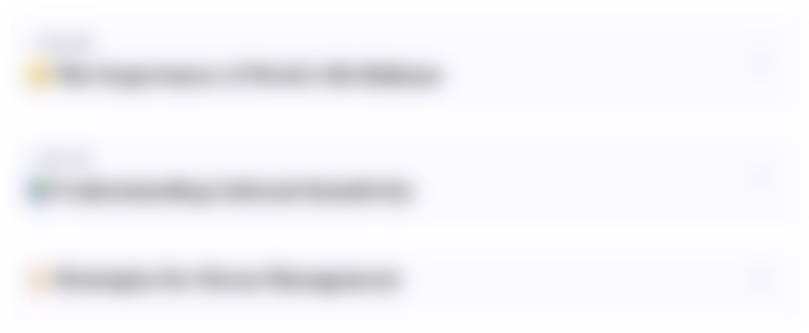
This section is available to paid users only. Please upgrade to access this part.
Upgrade NowMindmap
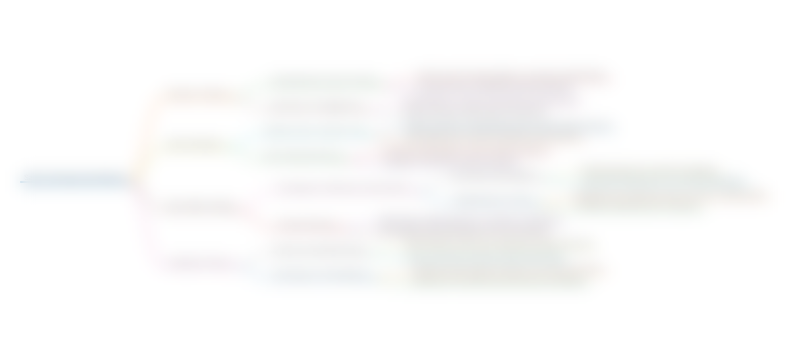
This section is available to paid users only. Please upgrade to access this part.
Upgrade NowKeywords
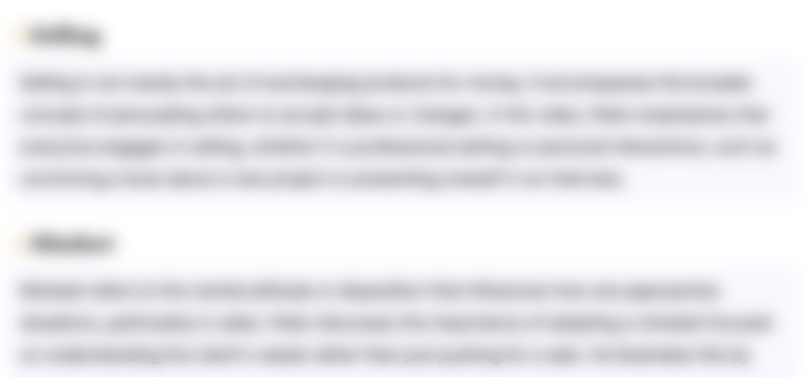
This section is available to paid users only. Please upgrade to access this part.
Upgrade NowHighlights
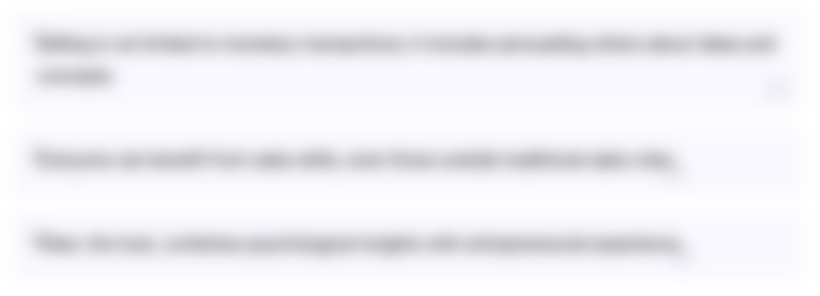
This section is available to paid users only. Please upgrade to access this part.
Upgrade NowTranscripts
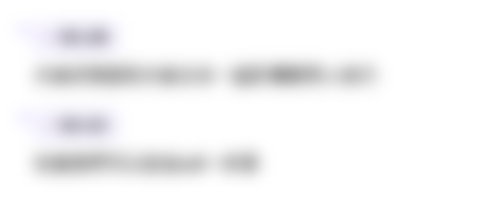
This section is available to paid users only. Please upgrade to access this part.
Upgrade NowBrowse More Related Video
5.0 / 5 (0 votes)