What is Multi Jet Fusion (MJF) and How Does it Work?
Summary
TLDRThe video introduces MultiJet Fusion (MJF), an HP-designed additive manufacturing technology for creating detailed, functional prototypes and low to mid-volume production parts. MJF offers speed, isotropic mechanical properties, and design freedom without support structures. It uses PA materials, with plans for metal and other materials. Advantages include fast production and cost-efficiency, though MJF is a closed system with limited materials. Post-processing is necessary, but MJF provides a strong solution for small to midsize parts production.
Takeaways
- ๐ Multijet Fusion (MJF) is an additive manufacturing technology developed by HP, first released in May 2016.
- ๐ ๏ธ MJF is part of the powder bed fusion family, alongside SLS and binder jetting, and is known for its detailed and functional prototypes.
- โ๏ธ MJF printers are capable of producing mechanically isotropic parts with high strength and detail, and are notably fast compared to SLS.
- ๐ฅ The MJF process involves spreading a layer of material and then using a thermal inkjet array to apply fusing and detailing agents, followed by heating to fuse the material.
- ๐๏ธ The detailing agent in MJF acts as a cooling agent to prevent part bleeding into the powder and contributes to smooth surfaces and fine detail.
- ๐ฆ The Jet Fusion system primarily uses PA2 materials, with reinforced options and other materials like polypropylene, TPU, and TPA available, with future expansion to metals.
- ๐ MJF offers advantages such as fast production, cost efficiency, and design freedom without the need for support structures during printing.
- ๐ข The optimal part density for MJF is between 8-12%, which is crucial for maximizing production speed and minimizing energy use.
- ๐ Post-processing for MJF is relatively light, but parts require cooling, removal of unfused powder, and may need additional finishing processes.
- ๐ซ One of the key disadvantages of MJF is its closed proprietary system controlled by HP, limiting material options and customizability compared to more open ecosystems.
- ๐ค MJF is faster than SLS for producing larger quantities of parts and has a higher recyclability rate of recovered powder, but is optimized for smaller to midsize parts.
- ๐จ While MJF parts are typically printed in gray, they can be dyed post-process, unlike SLS which offers a broader range of materials and colors during printing.
Q & A
What is MultiJet Fusion (MJF)?
-MultiJet Fusion is an additive manufacturing technology designed by HP, used for producing detailed, functional prototypes and low to mid-volume production parts. It is part of the powder bed fusion family, alongside SLS and binder jetting.
When was the first MultiJet Fusion printer released?
-The first MultiJet Fusion printer was released in May 2016.
What are the key advantages of MJF over its competitors like SLS?
-MJF offers speed, isotropic properties, and the ability to print 100 to 250 small to midsize parts in one build volume in a day, making it a serious production solution for a wide range of manufacturing challenges.
How does the MultiJet Fusion process work?
-The process involves spreading a layer of material on the print bed, applying fusing and detailing agents with a thermal inkjet array, and heating the surface to fuse the material. The detailing agent acts as a cooling agent to prevent part bleeding into the powder.
What role does the detailing agent play in the MJF process?
-The detailing agent, a kind of black ink, is applied around the fusing agent to function as a cooling agent, preventing the part from bleeding into the powder and helping to create smooth surfaces and fine detail.
What materials are commonly used in the Jet Fusion system?
-The Jet Fusion system primarily focuses on PA2, with PA 11 and glass bead reinforced PA2 being most common. Other materials like polypropylene, flexible TPU, and TPA are also available, with the potential for metal and other materials in the future.
What is the significance of part density in MJF printing?
-Part density is crucial for maximizing the speed of part production and costs. HP suggests a 'magical density number' of 8%, but in practice, it's between 8 and 12%, which helps in effectively filling the build chamber.
How does MJF compare to SLS in terms of design freedom?
-MJF, being part of the powder bed fusion family, does not require support structures, allowing for more design freedom and no visible removal marks, making it suitable for detailed geometries.
What are the mechanical properties of parts produced by MJF?
-MJF parts are 97 to 98% isotropic, meaning they have mechanically consistent properties along all directions of the part's geometry, which is beneficial for parts with crucial features on multiple surfaces.
What is the minimum feature size that MJF can print?
-MJF can print small features with a minimum feature size of 0.02 inches or 0.5 mm, printing at a layer thickness of 80 microns.
What are some disadvantages of MJF technology?
-MJF is a closed proprietary system controlled by HP, which limits material options and the use of open software ecosystems. Additionally, while post-processing is relatively light, parts are not finished straight out of the printer and are not optimized for printing larger parts.
How does MJF differ from SLS in terms of material options and mechanical properties?
-MJF parts are almost always printed in gray due to the printing process, and while they can be dyed, they offer less color variety than SLS. Mechanically, MJF parts are more isotropic, providing consistent properties in all directions, compared to SLS parts which are less isotropic.
What is the post-processing procedure for MJF parts?
-After printing, MJF parts need to be cooled, the unfused powder vacuumed for recovery, and the parts bead blasted, air blasted, or water blasted to remove remaining powder. Additional finishing processes like painting, coating, tumbling, or polishing may also be required.
Outlines
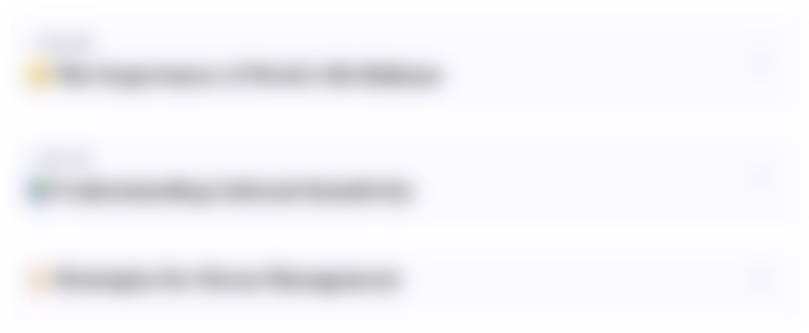
This section is available to paid users only. Please upgrade to access this part.
Upgrade NowMindmap
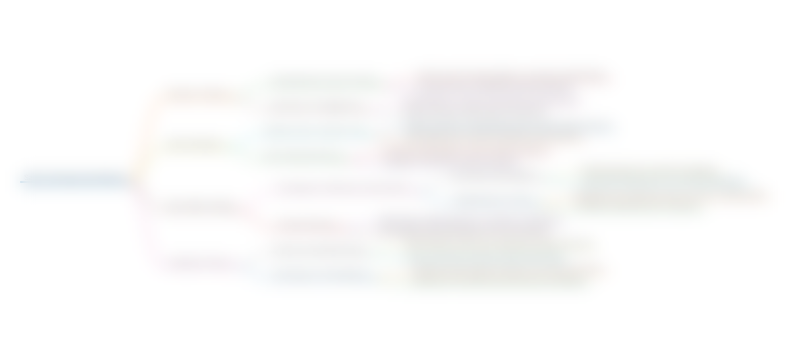
This section is available to paid users only. Please upgrade to access this part.
Upgrade NowKeywords
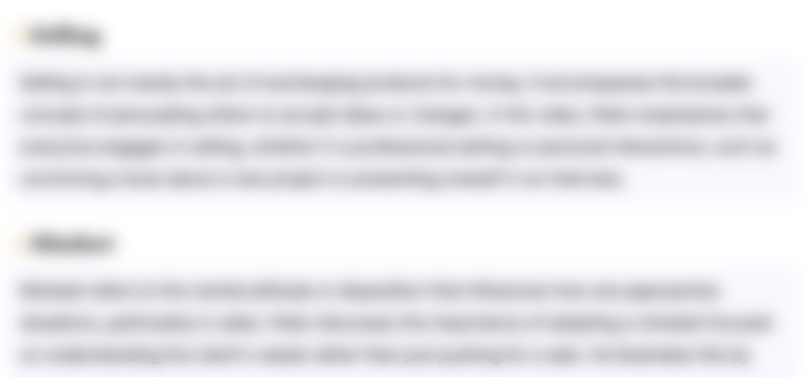
This section is available to paid users only. Please upgrade to access this part.
Upgrade NowHighlights
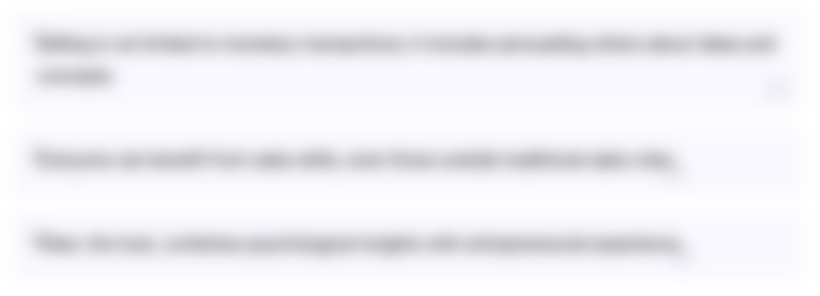
This section is available to paid users only. Please upgrade to access this part.
Upgrade NowTranscripts
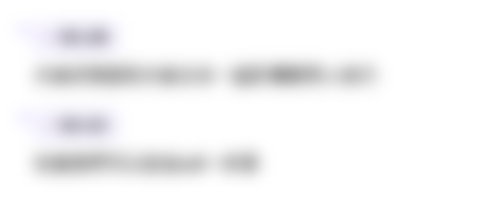
This section is available to paid users only. Please upgrade to access this part.
Upgrade NowBrowse More Related Video
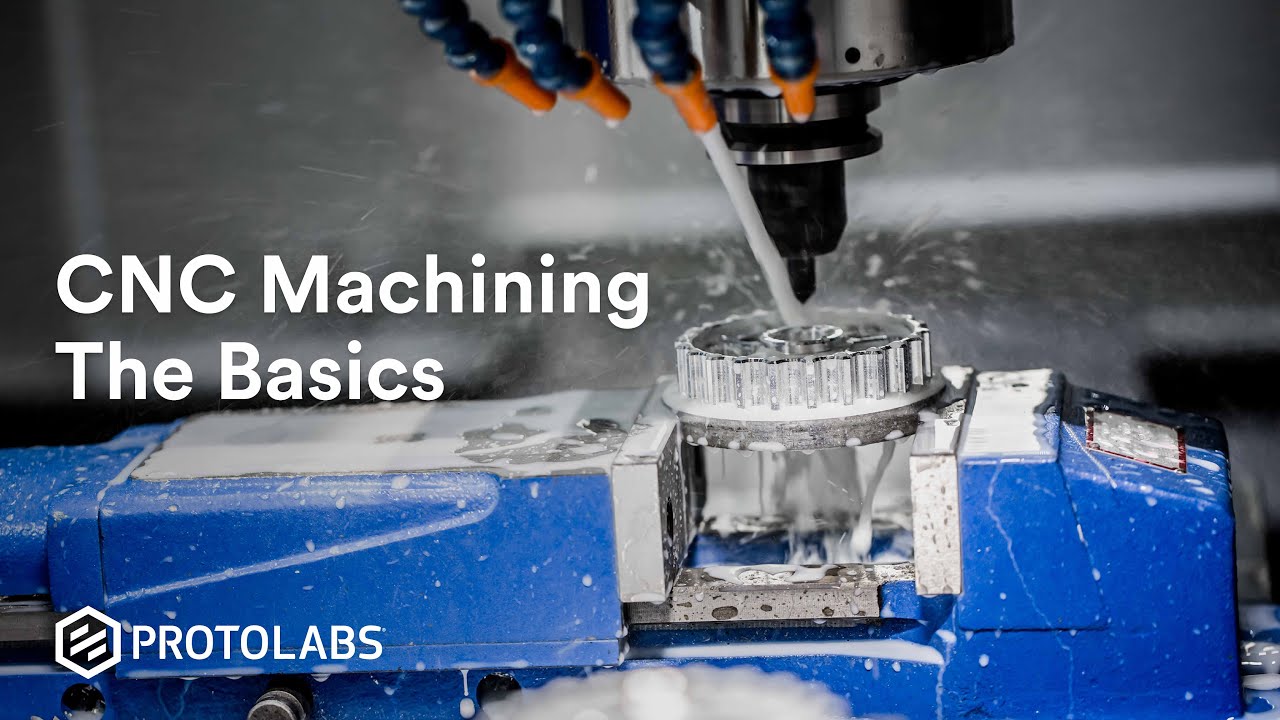
CNC machining - What is it and How Does it Work? (Must Know Basics)

Additive Manufacturing Processes
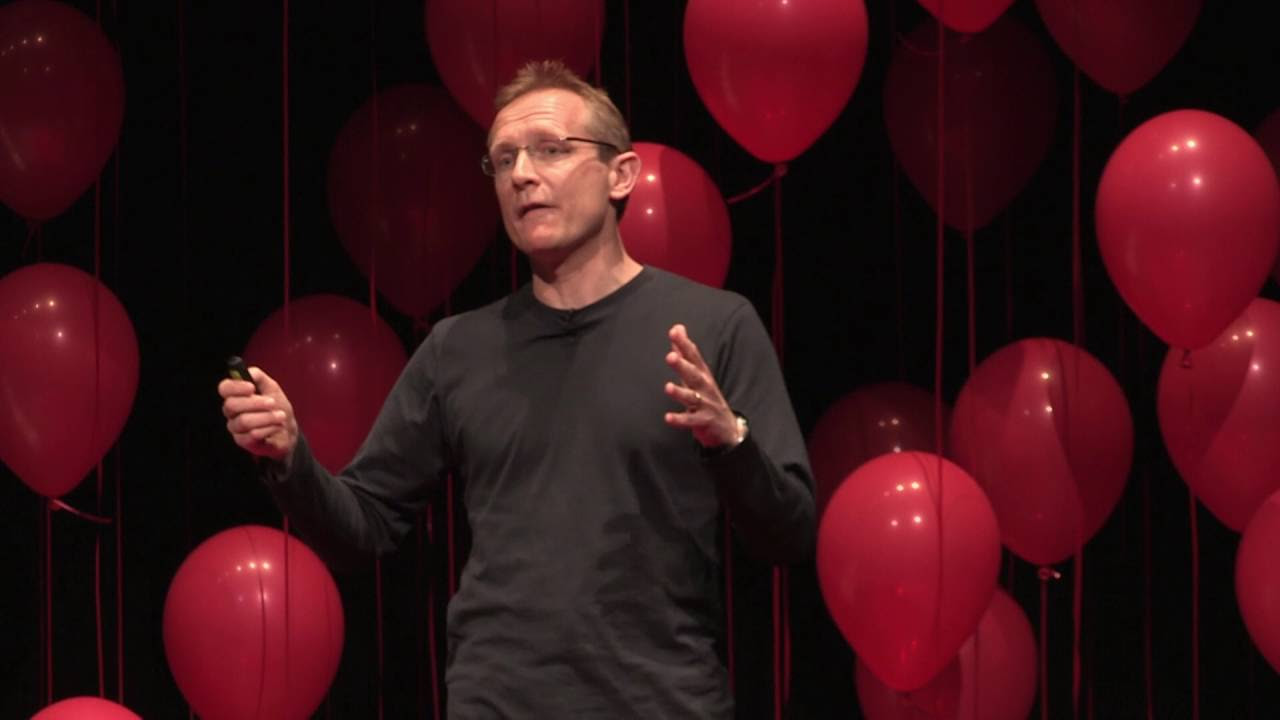
How 3D printing is enabling the โ4th Industrial Revolutionโ | Dr. Tim Minshall | TEDxOxBridge
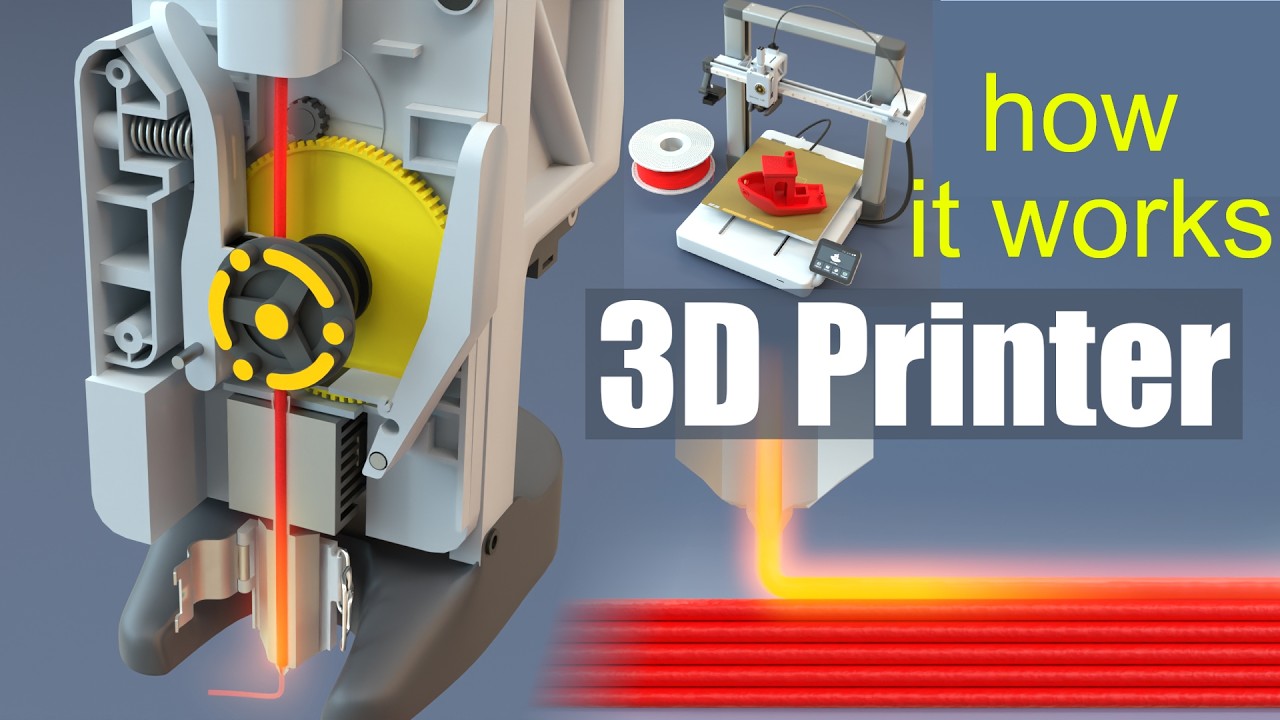
How does a 3D Printer work? (A1 by Bambu Lab)

Introduction to Flexible Manufacturing System (FMS)
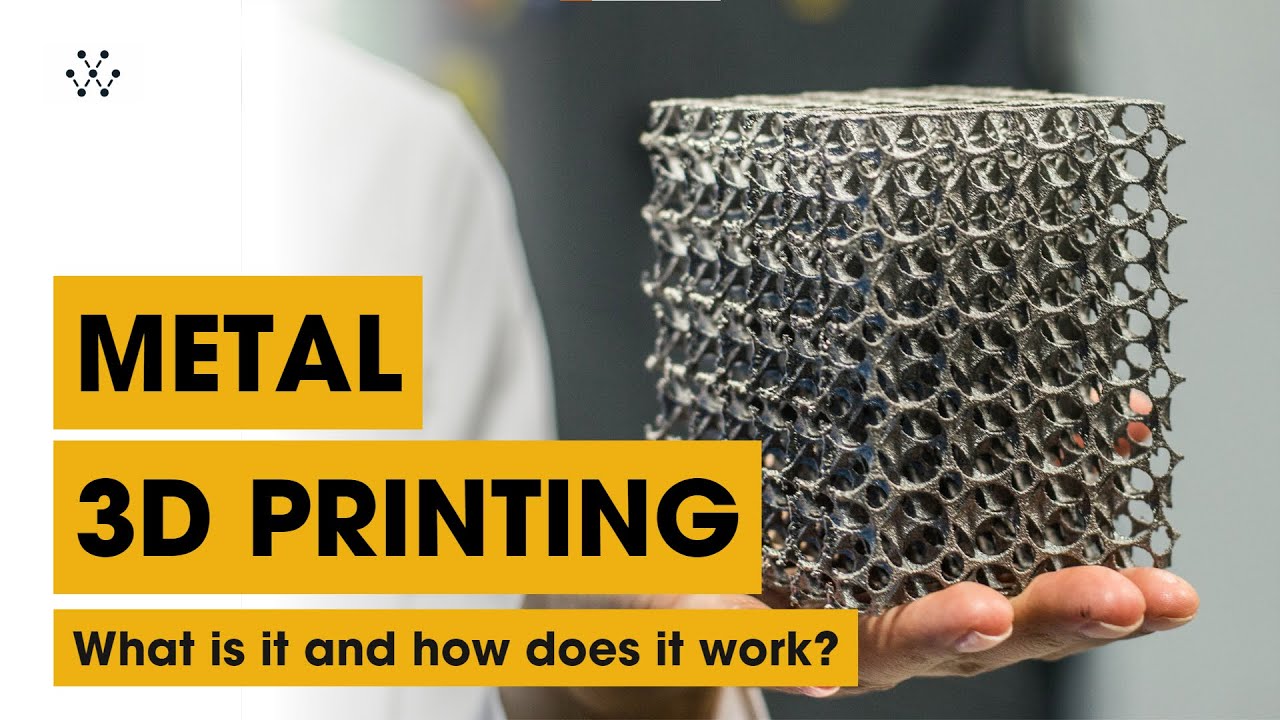
METAL 3D PRINTING | What is it and how does it work ?
5.0 / 5 (0 votes)