Golf Clubs | How It's Made
Summary
TLDRThis video script details the meticulous process of crafting golf club heads from aerospace-grade stainless steel. It begins with creating a wax replica, which is then coated in ceramic and silica sand, forming a mold. The wax is melted out, and molten steel is carefully poured to form the clubhead. After breaking the mold, the clubheads are sanded, adorned with a metal badge, and painted to indicate the club's angle. The shaft, made of extruded steel or carbon fiber, is attached with epoxy, and the grip is precisely aligned for optimal hand positioning. Finally, a computer checks and adjusts the clubhead's lie and loft to ensure precision and quality.
Takeaways
- 🛠️ The golf club heads are made from aerospace-grade stainless steel, indicating high-quality materials.
- 🏭 The manufacturing process starts with a wax replica of the clubhead, showcasing a detailed and intricate initial step.
- 🔥 Hot wax is injected into a mold to create the wax pattern, highlighting the use of heat in the molding process.
- 🤖 A robot assembles the wax patterns with wax parts to form gates and runners, demonstrating automation in the process.
- 🏺 The patterns are dipped into liquid ceramic material and silica sand is applied to create a hardened shell, showing a multi-step coating process.
- 🔥 The wax is melted out, and the shell becomes a mold for casting metal clubheads, revealing a crucial step in the casting process.
- 🔩 A furnace heats steel bars to 3,000 degrees Fahrenheit for casting, emphasizing the high temperatures required.
- ⚙️ A pneumatic hammer is used to break apart the mold after casting, indicating a mechanical post-casting step.
- 🔨 Workers grind off remnants of gates and runners, and the clubheads are finished with a sandblaster, detailing the refinement process.
- 🏹 A metal badge with the club's model name is attached, and automotive paint is used for color-coding club angles, showing branding and customization.
- 🪵 The clubhead is lined with epoxy, and the shaft is inserted, highlighting the assembly of the club's components.
- 🔧 The shaft is made of either extruded steel or carbon fiber, offering options in material composition.
- 📏 The shaft is cut to length, and a rubber grip is applied with precision, emphasizing the importance of correct sizing and grip.
- 💻 A computer reads and adjusts the lie and loft angles, ensuring the club's specifications are met with high precision.
Q & A
What material are the heads of these golf clubs made from?
-The heads of these golf clubs are made from aerospace-grade stainless steel.
How is the wax replica of the clubhead created?
-The wax replica, also known as the wax pattern, is created by injecting hot wax into a mold.
What is the purpose of using hot wax as an adhesive?
-Hot wax is used as an adhesive to join several wax patterns to other wax parts in the shape of gates and runners.
What is the function of gates and runners in the casting process?
-Gates and runners are channels that guide molten metal into the casting mold.
How many times are the patterns dipped into liquid ceramic material?
-The patterns are dipped into liquid ceramic material four times.
What happens to the ceramic and sand after they harden around the wax patterns?
-The hardened ceramic and sand form a shell around the wax patterns, which then serves as a mold for casting the metal clubheads.
How is the wax removed from the shell to create the mold for casting?
-The wax is melted out of the shell, leaving behind a mold for casting the metal clubheads.
What temperature does the furnace heat the steel bars to for casting?
-The furnace heats the steel bars to 3,000 degrees Fahrenheit.
Why is the pouring technique critical during the casting process?
-The pouring technique is critical to ensure the metal flows at a consistent rate to prevent the formation of air bubbles.
How are the clubheads separated from the gates and runners after the mold is broken apart?
-Workers saw off the gates and runners to separate the clubheads.
What is the purpose of the sandblasting process in the clubhead production?
-The sandblasting process gives the metal a particular finish.
What is the significance of the color applied to the metal badge on the clubhead?
-The color identifies the angle of the club, with 12 different angles represented by different colors.
How is the shaft attached to the clubhead?
-The shaft is attached to the clubhead by lining the neck of the clubhead with epoxy, coating the end of the shaft with epoxy, and sliding it into the neck, followed by a pneumatic hammer pushing the shaft in as far as it can go.
What materials are the shafts of the golf clubs made from?
-The shafts are made of either extruded steel or carbon fiber.
How is the club's grip aligned during the assembly process?
-A laser line helps align the grip in the right position on the shaft.
What does the term 'lie' refer to in the context of golf clubs?
-The term 'lie' refers to the angle of the clubhead relative to the ground.
What adjustments are made to the clubhead after the computer reads the loft and lie?
-Technicians make adjustments to the clubhead's angle based on the computer's analysis of the loft and lie to ensure they meet the quality specifications.
Outlines
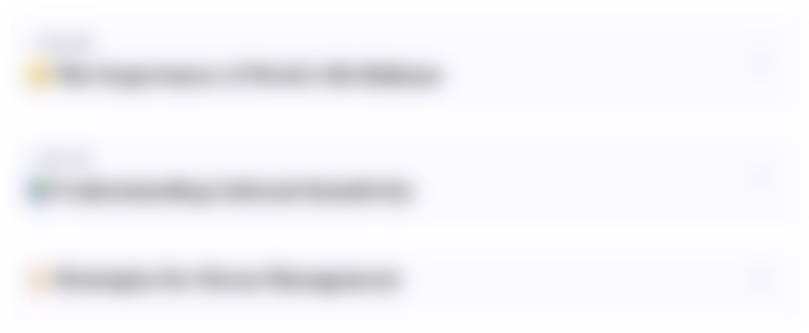
Этот раздел доступен только подписчикам платных тарифов. Пожалуйста, перейдите на платный тариф для доступа.
Перейти на платный тарифMindmap
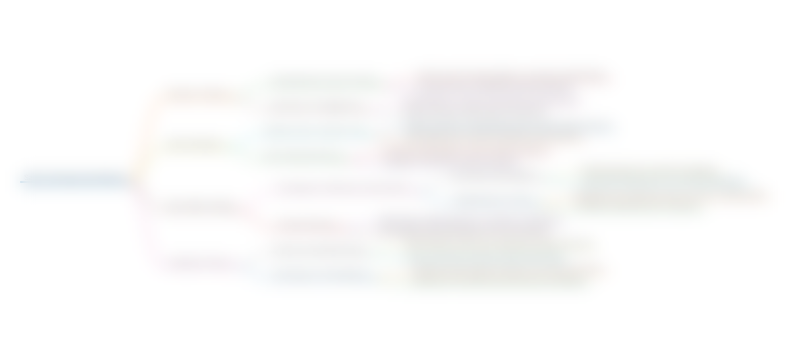
Этот раздел доступен только подписчикам платных тарифов. Пожалуйста, перейдите на платный тариф для доступа.
Перейти на платный тарифKeywords
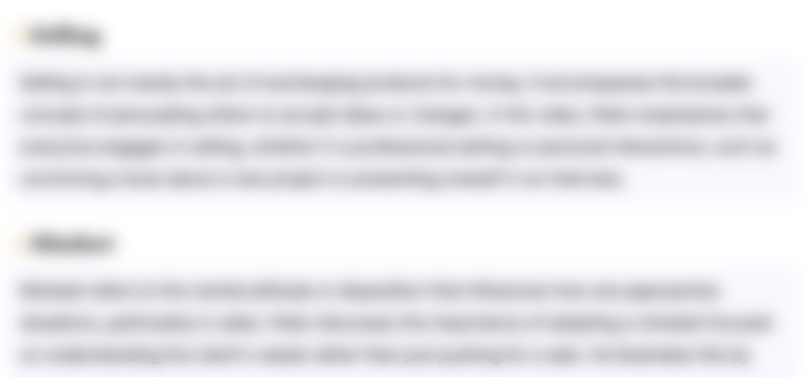
Этот раздел доступен только подписчикам платных тарифов. Пожалуйста, перейдите на платный тариф для доступа.
Перейти на платный тарифHighlights
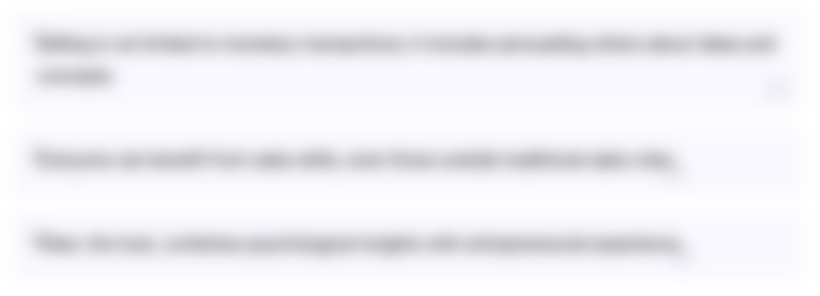
Этот раздел доступен только подписчикам платных тарифов. Пожалуйста, перейдите на платный тариф для доступа.
Перейти на платный тарифTranscripts
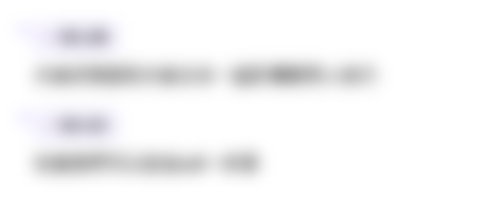
Этот раздел доступен только подписчикам платных тарифов. Пожалуйста, перейдите на платный тариф для доступа.
Перейти на платный тариф5.0 / 5 (0 votes)