HHO Generator - Water to Fuel Converter
Summary
TLDRThis script details a DIY project to create a hydroxy generator, transforming water into a highly explosive gas using electricity. The process involves crafting stainless steel plates, assembling acrylic and ABS components, and using potassium hydroxide as a catalyst. The result is a system producing OxyHydrogen gas, capable of generating thousands of liters of fuel from a small amount of water, showcasing a potentially powerful and sustainable energy source.
Takeaways
- 🔧 The project involves building a generator that converts water into a highly explosive gas, hydroxy gas, using electricity.
- 🛠️ Materials needed include stainless steel, ABS cleanout fittings, poly tubing, and acrylic tubing, along with other hardware.
- ⚙️ Stainless steel plates are cut to specific sizes using a hydraulic punch and then sanded to increase surface area for efficiency.
- 🔩 The assembly process involves attaching various fittings and tubing with silicone caulking and ABS cement for a watertight seal.
- 💦 The generator is filled with a mixture of distilled water and potassium hydroxide, which acts as a catalyst for the production of hydroxy gas.
- 🔬 The process of creating hydroxy gas involves a chemical reaction that turns water back into a fuel source, which can then be converted back into water.
- 🛡️ Safety measures such as using protective gear and working in a well-ventilated area are implied throughout the project.
- 🔬 The script describes a DIY approach to creating a fuel source from one of the most abundant materials on earth, highlighting the potential of water as a renewable resource.
- 🔌 The generator is designed to be connected to a power source, such as car batteries, to initiate the conversion process.
- 💨 The end product, hydroxy gas, is described as an extremely powerful fuel that can produce a significant amount of energy.
- 🌐 The video script is from a project shared on 'www.thekingofrandom.com', suggesting a community interest in innovative and practical DIY projects.
Q & A
What is the primary material used in the project described in the script?
-The primary material used in the project is stainless steel, specifically 20 gauge stainless steel.
What is the purpose of the generator built in the project?
-The purpose of the generator is to convert water into a highly explosive gas, specifically OxyHydrogen gas, using electricity.
What are the dimensions of the stainless steel plates mentioned in the script?
-The dimensions of the stainless steel plates are 12 plates measuring 3" x 6", 4 plates at 1 1/2" x 6", and three connector bands that are 6", 4 1/2", and 3 1/4".
Why is the protective layer peeled from the plates and the surface sanded?
-The protective layer is peeled from the plates to reveal the attractive surface, which is then sanded to create scuff marks that increase the surface area on the plates and improve the efficiency of the generator.
What is used to smooth down the jagged edges around the holes in the plates?
-A belt sander is used to smooth down the jagged edges around the holes in the plates.
What materials are used to create the bubbler and how are they connected?
-The bubbler is created using 4" ABS cleanout fittings, 3/8" poly tubing, and scrap acrylic tubing. The connections are made using silicone caulking and ABS cement.
How does the script describe the process of attaching the acrylic tubing to the clean out adaptor?
-The process involves applying silicone caulking around the outer base and inside of the clean out adaptor, then tapping the tubing into place with a rubber hammer and cleaning up the excess silicone with a paper towel.
What is the role of the 1/4" 90-degree elbow in the bubbler assembly?
-The 1/4" 90-degree elbow is attached to the cap of the bubbler and is used to connect the bubbler to the acrylic tubing, creating a sealed and professional-looking assembly.
What is the significance of the swivel elbow used in the generator plates assembly?
-The swivel elbow, which allows 360-degree rotation, is used for convenience in the assembly of the generator plates, providing flexibility in the positioning of the components.
How is the generator connected to the 4" plug and what materials are used for this connection?
-The generator is connected to the 4" plug using 5/16" x 2" stainless steel bolts, nuts, and 1/4" washers with one side being stainless steel and the other rubber.
What is the final product of the project and how does it function?
-The final product is a hydroxy generator that produces OxyHydrogen gas. It runs on 2 car batteries and produces about 5 liters of gas per minute, which, when used, turns back into water.
Outlines
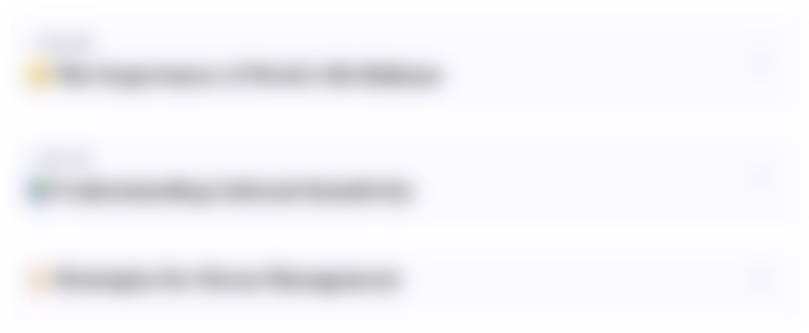
This section is available to paid users only. Please upgrade to access this part.
Upgrade NowMindmap
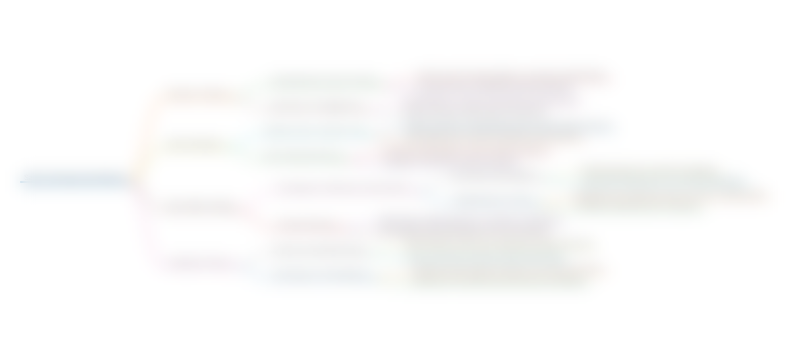
This section is available to paid users only. Please upgrade to access this part.
Upgrade NowKeywords
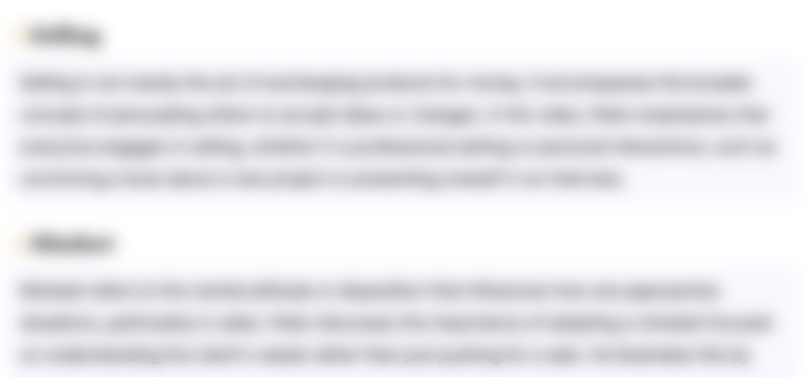
This section is available to paid users only. Please upgrade to access this part.
Upgrade NowHighlights
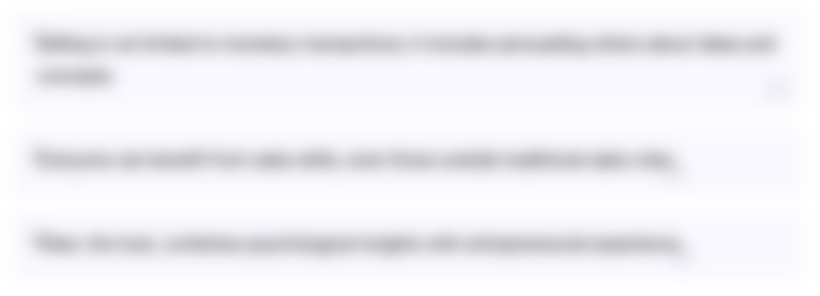
This section is available to paid users only. Please upgrade to access this part.
Upgrade NowTranscripts
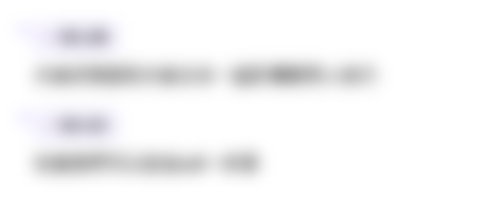
This section is available to paid users only. Please upgrade to access this part.
Upgrade NowBrowse More Related Video
5.0 / 5 (0 votes)