Scientific Management
Summary
TLDRThe script explores the origins of scientific management, pioneered by Frederick Taylor, who sought to optimize work efficiency. After facing hostility from workers due to productivity pressures, Taylor developed four principles: creating a science for each task, scientifically selecting and training workers, cooperating with employees to implement these principles, and sharing responsibilities for productivity. His goal was to harmonize the interests of both employees and employers, ensuring fair compensation for a fair day's work.
Takeaways
- 👷♂️ Frederick Taylor is recognized as the father of scientific management, which focuses on identifying the most efficient work methods through systematic study and experimentation.
- 🏭 Taylor's early career at Midvale Steel Company involved various roles, from worker to chief engineer, giving him firsthand experience of worker dynamics and productivity issues.
- 🔨 Taylor's struggle with 'soldiering', or workers deliberately restricting output, led him to develop the principles of scientific management as a solution to improve productivity and worker relations.
- 🛠️ Scientific management involves four main principles: developing a science for each element of work, scientifically selecting and training workers, cooperating with employees, and dividing work and responsibilities between management and workers.
- 🧘 Rest breaks for physical labor, a controversial idea at the time, were advocated by Taylor and proven through experiments to increase worker productivity.
- 📊 The systematic selection and training of workers based on aptitude rather than favoritism or nepotism was a key aspect of Taylor's approach to improving efficiency.
- 🤝 Taylor emphasized the importance of cooperation between management and workers, arguing that their interests were not inherently antagonistic but could be aligned for mutual benefit.
- 📉 The division of work and responsibilities was crucial to ensure that scientific principles were implemented, addressing the issue of workers being solely responsible for productivity.
- 💰 Taylor believed in determining a 'fair day's work' and compensating workers fairly for their efforts, aiming to create a balance between employee and employer interests.
- 🛑 The implementation of scientific management faced resistance, with workers threatening Taylor and breaking machines, highlighting the social pressures and hostility involved in changing established work practices.
- 🔄 Taylor's personal experiences and reflections led him to develop scientific management as a remedy for the 'horrid life' of constant conflict between workers and management.
Q & A
What is scientific management?
-Scientific management is a method of organizing work that involves the thorough study and testing of different work methods to identify the most efficient way to complete a job.
Who is considered the father of scientific management?
-Frederick Taylor is considered the father of scientific management.
What was Taylor's initial career path at the Midvale Steel Company?
-Taylor began his career as a worker, was promoted to pattern maker, supervisor, and then became the chief engineer at the Midvale Steel Company.
What was Taylor's struggle during his three-year period at Midvale Steel Company?
-Taylor struggled to get the men who worked for him to do what he called 'a fair day's work,' which was a quantity output agreed upon by the workers that was limited to about one-third of what they could actually do.
What was Taylor's approach to increasing output when he became the boss?
-Taylor tried to increase output by doing the job himself, showing workers it was possible to produce more, hiring and training new workers, and enforcing strict rules, including firing workers who broke machines or violated rules.
How did the workers respond to Taylor's efforts to increase output?
-The workers responded with hostility, social pressure, and even threats of violence, as they saw Taylor's efforts as attempts to 'bust the rates' and disrupt their established work pace.
What was Taylor's solution to the conflict between workers and management?
-Taylor's solution was the development of scientific management, which emphasized systematic study to find the best way to perform tasks and improve productivity without hostility.
What were the four principles of Taylor's scientific management?
-The four principles were: 1) Develop a science for each element of work, 2) Scientifically select, train, teach, and develop workers, 3) Cooperate with employees to implement scientific principles, and 4) Divide work and responsibilities equally between management and workers.
Why did Taylor propose giving rest breaks to factory workers?
-Taylor believed that rest breaks would increase worker productivity, and he demonstrated this through systematic experiments showing that workers with frequent breaks could greatly increase their daily output.
How did Taylor's approach to hiring workers differ from the common practice of his time?
-Taylor instructed supervisors to hire first-class workers based on their aptitude and ability to do the job well, rather than on favoritism or nepotism.
What was Taylor's view on the relationship between the interests of employees and employers?
-Taylor believed that the true interests of employees and employers were not antagonistic but rather aligned, with long-term prosperity for the employer dependent on the prosperity of the employees and vice versa.
What was Taylor's definition of a 'fair day's work'?
-A 'fair day's work' was defined by Taylor as what an average worker could produce at a reasonable pace day in and day out, and it was management's responsibility to pay workers fairly for this amount of work.
Outlines
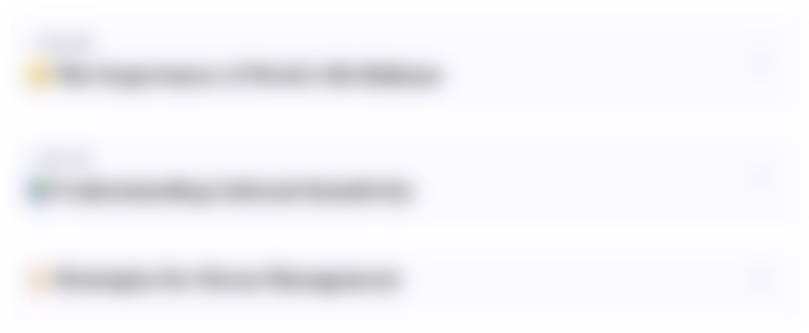
このセクションは有料ユーザー限定です。 アクセスするには、アップグレードをお願いします。
今すぐアップグレードMindmap
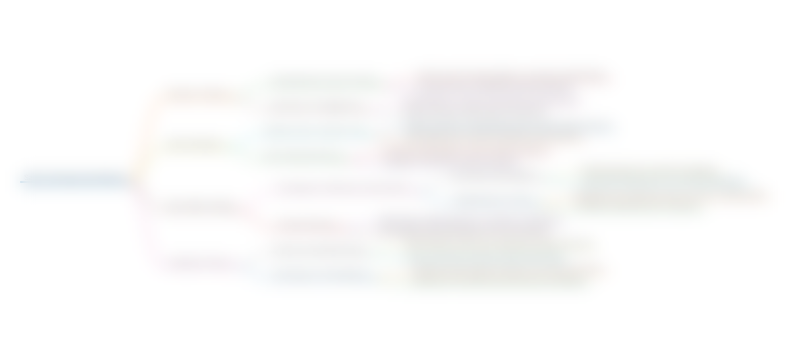
このセクションは有料ユーザー限定です。 アクセスするには、アップグレードをお願いします。
今すぐアップグレードKeywords
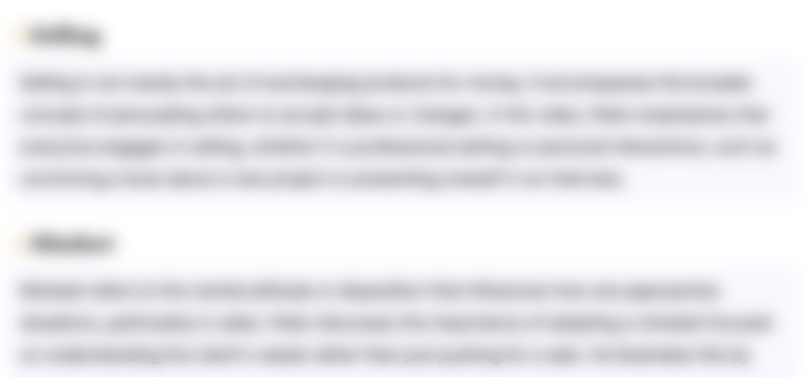
このセクションは有料ユーザー限定です。 アクセスするには、アップグレードをお願いします。
今すぐアップグレードHighlights
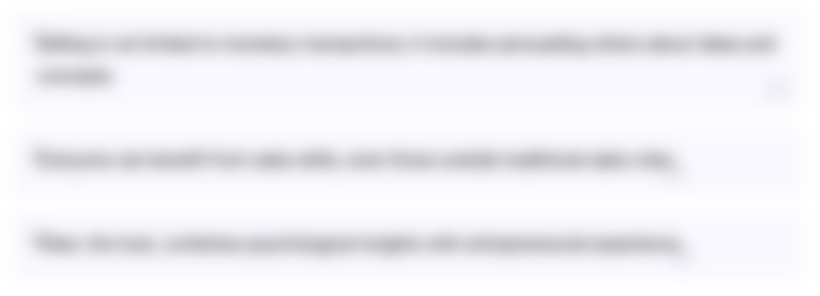
このセクションは有料ユーザー限定です。 アクセスするには、アップグレードをお願いします。
今すぐアップグレードTranscripts
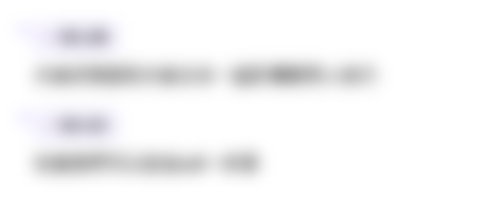
このセクションは有料ユーザー限定です。 アクセスするには、アップグレードをお願いします。
今すぐアップグレード関連動画をさらに表示
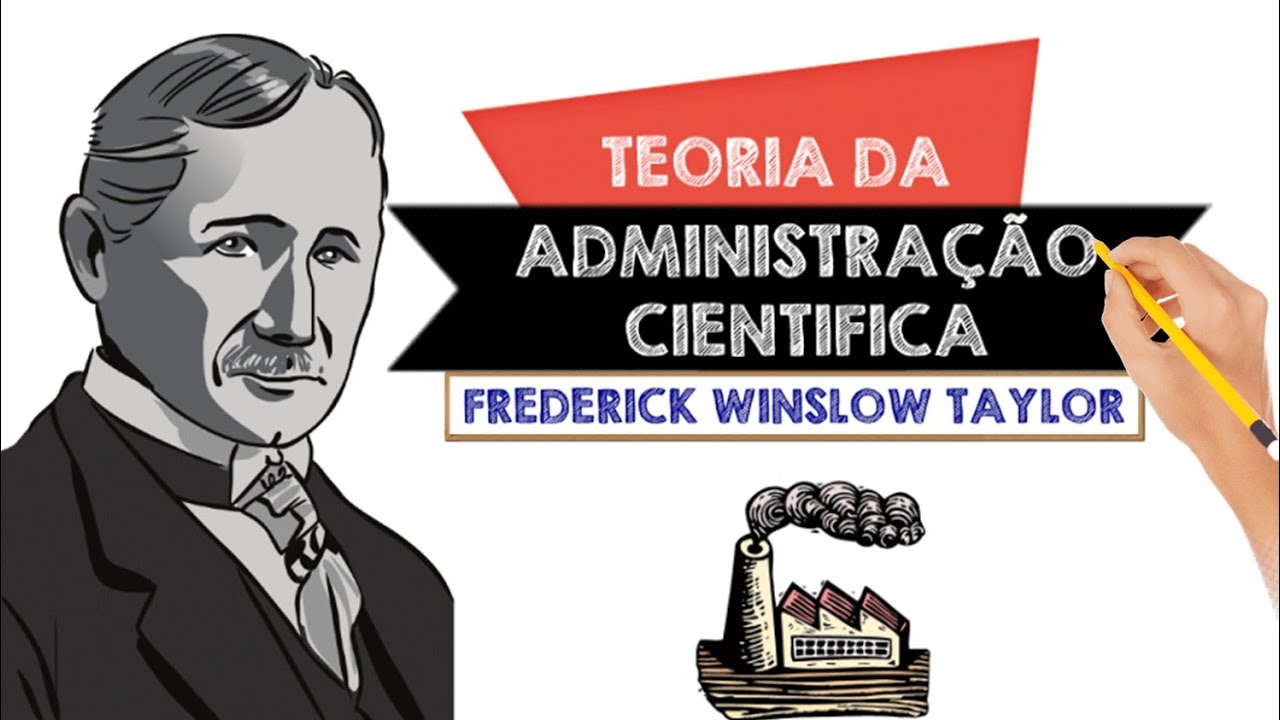
Administração Científica de Taylor || Introdução, Princípios, Vantagens, Desvantagens e Criticas

Estudos Organizacionais - Abordagem Científica da Administração - Introdução às Teorias... (LIBRAS)

LA ADMINISTRACION CIENTIFICA

Padres de la administración: Frederick Taylor
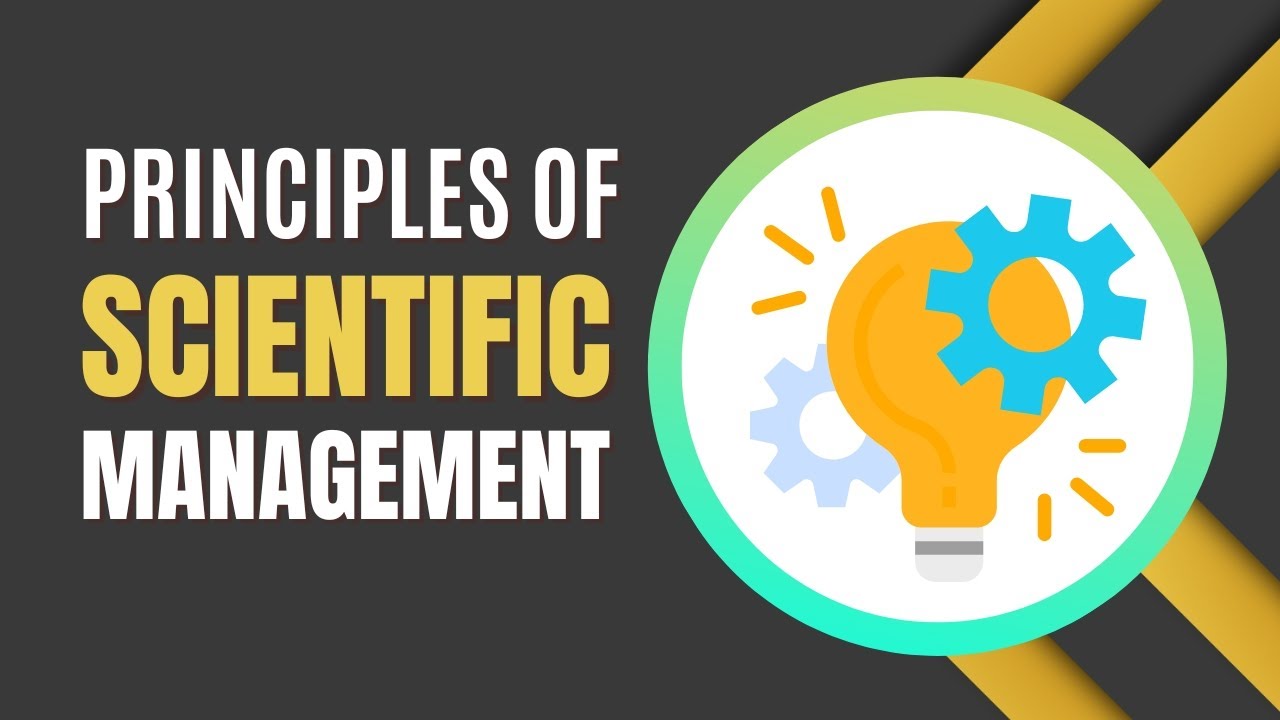
Principles of Scientific Management | Meaning and Techniques
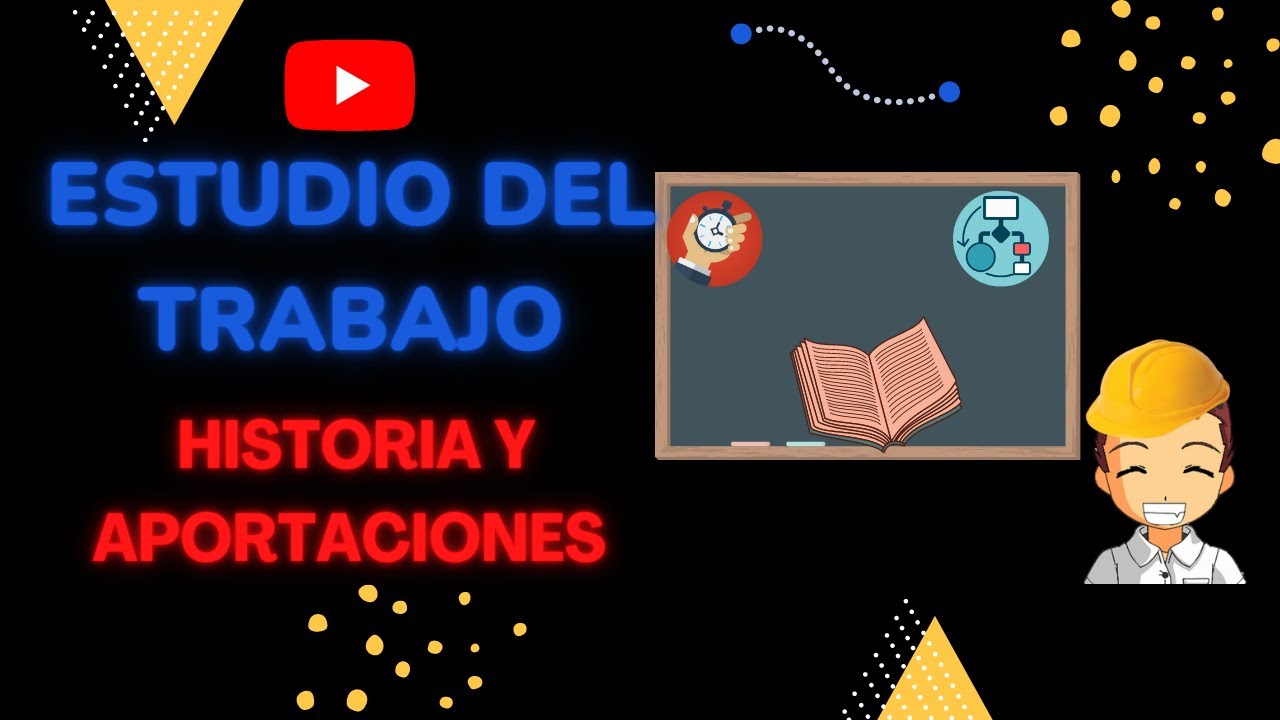
📚 Historia del ESTUDIO DEL TRABAJO - ¿Cómo surgió el ANÁLISIS DE MÉTODOS?
5.0 / 5 (0 votes)