Overall Equipment Effectiveness OEE
Summary
TLDRThis video explains Overall Equipment Effectiveness (OEE), a crucial metric in lean manufacturing, helping identify and quantify inefficiencies in operations. OEE measures three key components: availability, performance, and quality. The video introduces the concept of the six big losses—availability, speed, and quality losses—and walks through the calculation process using a fictional IT company as an example. The presenter demonstrates how to calculate OEE, interpret results, and use it to improve efficiency by pinpointing areas such as performance that are causing the most significant losses. The video highlights the practical application of OEE beyond traditional manufacturing settings.
Takeaways
- 😀 OEE (Overall Equipment Effectiveness) is a vital metric in lean manufacturing used to identify inefficiencies in operations.
- 😀 OEE allows for the quantification of inefficiencies, helping to pinpoint areas in operations where improvements are needed.
- 😀 An OEE of 100% means that all resources (machines, workers) are available, operating at top speed, and producing perfect products with no defects.
- 😀 OEE is calculated by multiplying three rates: availability, performance, and quality, each expressed as decimals (e.g., 100% becomes 1).
- 😀 Availability losses can result from breakdowns and setup times, reducing the planned output.
- 😀 Speed losses come from reduced operational speed or idling, which occurs when resources are waiting for input or instructions.
- 😀 Quality losses occur when defective products are produced, either as regular scrap or startup scrap during the beginning stages of production.
- 😀 The formula for calculating OEE helps to identify efficiency losses by measuring how planned output is reduced due to availability, speed, and quality issues.
- 😀 In an IT company example, the company faced availability losses (13 hours), speed losses (10%), and quality losses (5%), affecting the overall OEE.
- 😀 By calculating OEE, businesses can benchmark their performance against industry standards and locate the biggest sources of inefficiency, such as performance losses.
Q & A
What is Overall Equipment Effectiveness (OEE)?
-Overall Equipment Effectiveness (OEE) is a metric used in lean manufacturing and management to measure the efficiency of resources, such as machines or human resources, during production. It quantifies how well these resources perform relative to their planned availability, speed, and quality.
Why is OEE important in lean management?
-OEE is essential in lean management because it helps identify and quantify inefficiencies in production. It provides a clear understanding of where problems occur in the production process, allowing for targeted improvements to eliminate waste and enhance productivity.
What does an OEE score of 100% signify?
-An OEE score of 100% means that all resources (machines, workers, etc.) are fully available, performing at top speed, and producing perfect quality products without any defects. This is an ideal scenario in production.
What are the three main components of OEE?
-The three main components of OEE are: Availability (A), which measures if resources are available as scheduled; Performance (P), which checks if resources are operating at optimal speed; and Quality (Q), which tracks the percentage of defect-free products produced.
How is the Availability rate calculated?
-The Availability rate is calculated by dividing the Gross Output by the Planned Output. This shows the percentage of time that equipment or resources were actually available during the scheduled time.
What are the 'six big losses' in lean manufacturing?
-The 'six big losses' are common sources of inefficiency in production. They include Availability losses (due to breakdowns and setup times), Speed losses (due to reduced speed or idling), and Quality losses (due to regular scrap and startup scrap).
What are Availability losses, and how do they affect OEE?
-Availability losses occur when resources (such as machines or workers) are unavailable for production. They can be caused by breakdowns or setup times. These losses reduce the Gross Output and, in turn, lower the Availability rate in the OEE calculation.
What is the difference between regular scrap and startup scrap in terms of Quality losses?
-Regular scrap refers to defective products that are created during normal production, while startup scrap occurs at the beginning of a production run, when equipment is warming up. Startup scrap is typically more difficult to avoid and often considered inherent to the process.
How do you calculate the Performance rate?
-The Performance rate is calculated by dividing the Net Output by the Gross Output. This compares the actual performance of resources to their maximum potential performance, considering factors like reduced speed or idling.
What does the Quality rate measure, and how is it calculated?
-The Quality rate measures the percentage of defect-free products produced. It is calculated by dividing the Valuable Output (products that meet quality standards) by the Net Output, which accounts for both quality losses (scrap) and the total amount of production.
Outlines
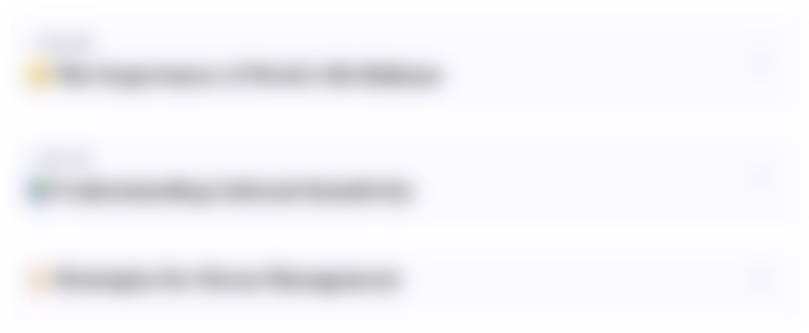
このセクションは有料ユーザー限定です。 アクセスするには、アップグレードをお願いします。
今すぐアップグレードMindmap
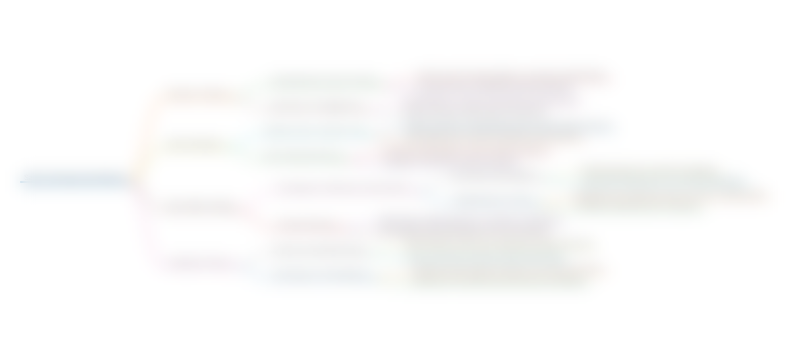
このセクションは有料ユーザー限定です。 アクセスするには、アップグレードをお願いします。
今すぐアップグレードKeywords
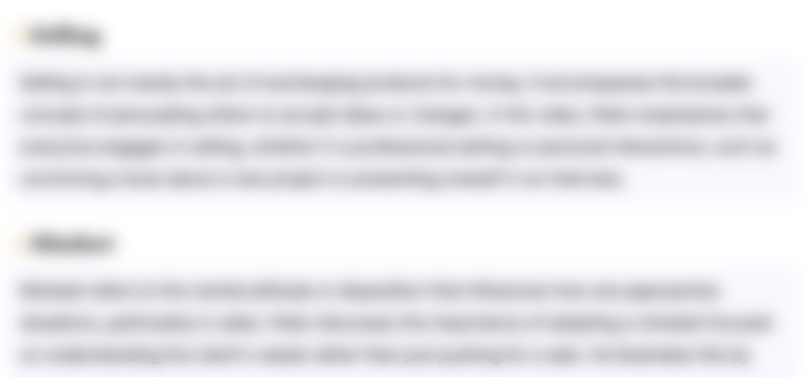
このセクションは有料ユーザー限定です。 アクセスするには、アップグレードをお願いします。
今すぐアップグレードHighlights
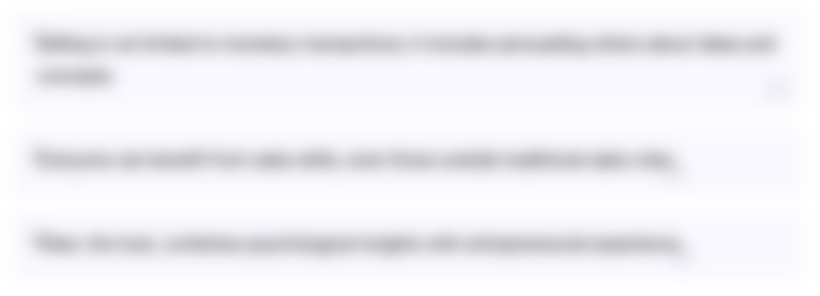
このセクションは有料ユーザー限定です。 アクセスするには、アップグレードをお願いします。
今すぐアップグレードTranscripts
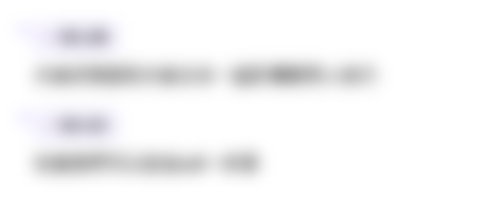
このセクションは有料ユーザー限定です。 アクセスするには、アップグレードをお願いします。
今すぐアップグレード関連動画をさらに表示
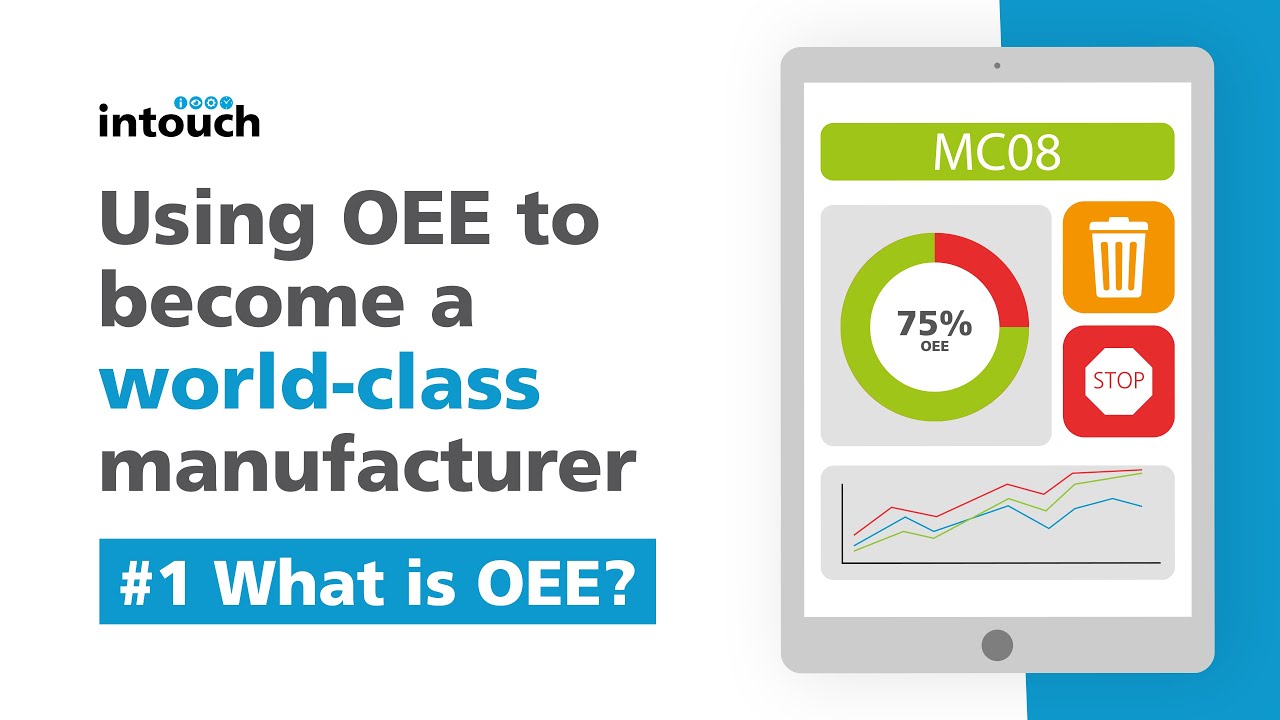
What is OEE and how do I calculate it? (Short Explanation)

IIoT & Industry 4.0 RANT by Walker Reynolds

How to calculate OEE
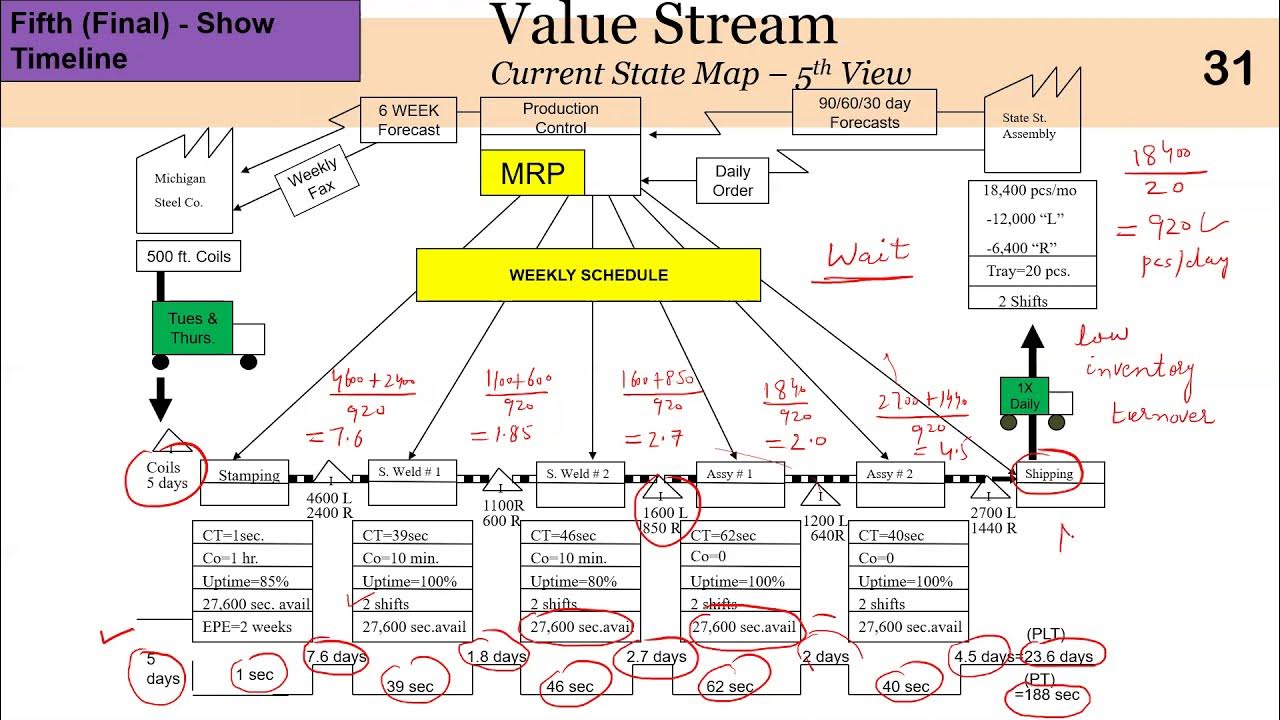
02_03_P2 Drawing the Current State Value Stream Map (VSM) - Acme Case Study
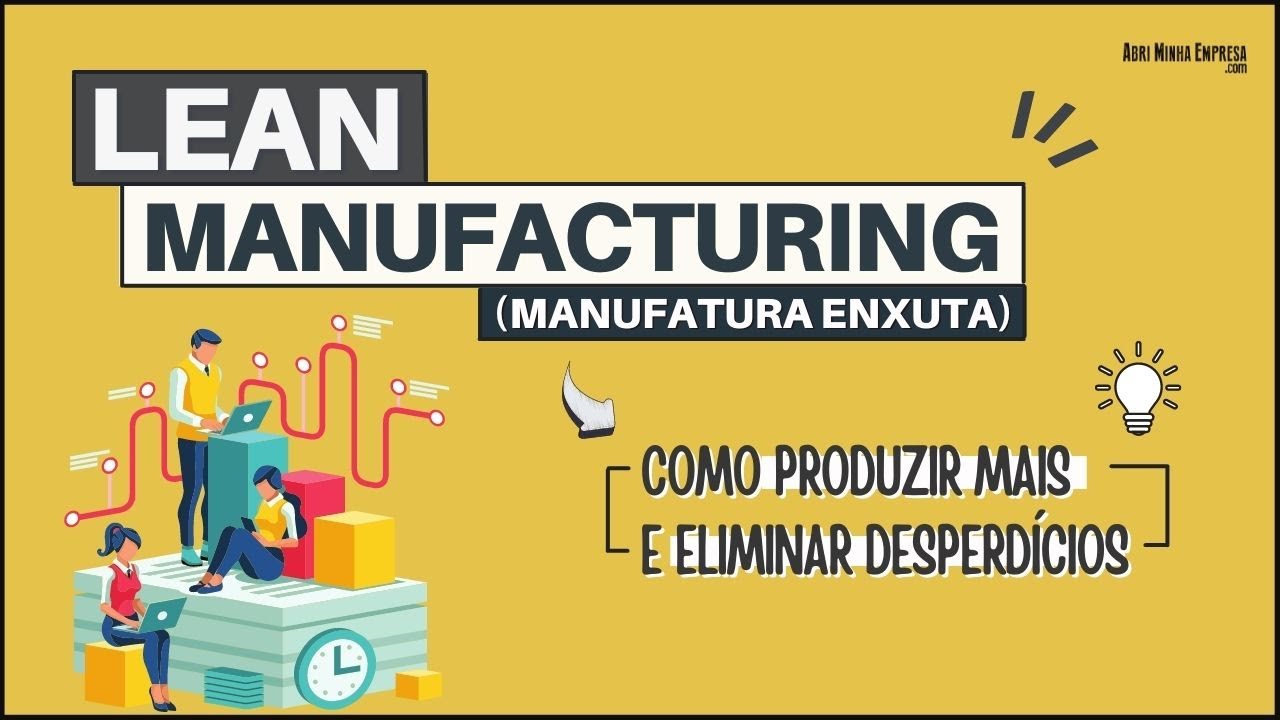
LEAN MANUFACTURING (Manufatura Enxuta) | Conheça os 8 Principais Tipos de Desperdícios

Working Capital Video Definition
5.0 / 5 (0 votes)