02_03_P2 Drawing the Current State Value Stream Map (VSM) - Acme Case Study
Summary
TLDRThe video covers a detailed case study on Acme Stamping Company, focusing on the production of steel instrument panel brackets for vehicle assembly. It explains the value stream mapping (VSM) process, emphasizing the flow of materials and information across departments like stamping, welding, and assembly. The presenter highlights the current state of Acme's operations, discussing inventory levels, cycle times, and inefficiencies in production, such as delays and imbalances between departments. The goal is to identify areas for improvement using lean manufacturing principles to optimize workflow and reduce lead times.
Takeaways
- ๐ง Acme Stamping Company produces steel instrument panel bracket assemblies for vehicle assembly plants, serving both left-hand and right-hand drive models.
- ๐ The company's customer is the State Street Vehicle Assembly Plant, requiring 18,400 pieces per month, with 12,000 of type LH and 6,400 of type RH.
- ๐ญ Acme operates in three main departments: Stamping, Welding, and Assembly, with daily shipments to the customer.
- ๐ฆ Michigan Steel Company supplies raw material (steel coils) to Acme twice a week on Tuesdays and Thursdays.
- ๐ Acme's Production Control Department manages forecasts from the customer (90, 60, 30 days) and issues weekly schedules for internal departments and six-week forecasts to suppliers.
- โณ Stamping department has an automated 200-ton press with a cycle time of one second, but with a 5-day inventory backlog before processing.
- โ๏ธ The welding workstations have manual processes, with varying cycle times (39 and 46 seconds), and accumulated inventory between departments creates inefficiencies.
- ๐ ๏ธ The assembly workstations have cycle times of 62 and 40 seconds, and despite 100% reliability, there's significant inventory buildup before assembly.
- ๐ The value-added time is just 188 seconds, compared to a total flow time of 23.6 days, indicating significant inefficiencies and delays in the system.
- ๐ There is considerable imbalance (mura) in the system, with excessive work-in-process inventory and cycle time differences between departments, leading to waste and inefficiency.
Q & A
What is the main focus of the Acme Stamping case study?
-The case study focuses on Acme Stamping Company, which produces steel instrument panel bracket assemblies for vehicle assembly plants. The analysis involves creating a current Value Stream Map (VSM) to identify inefficiencies in the production process.
What are the key departments involved in Acmeโs production process?
-The key departments in Acme's production process are Stamping, Welding, and Assembly. These departments are responsible for different stages of the manufacturing process.
Who supplies the steel coils to Acme, and how frequently are they delivered?
-The steel coils are supplied by Michigan Steel Company, and deliveries are made twice a week, on Tuesdays and Thursdays.
What is the daily customer requirement from Acme Stamping, and how is it structured?
-The customer, State Street Vehicle Assembly Plant, requires 18,400 pieces per month, which includes 12,000 left-hand brackets and 6,400 right-hand brackets. The components are shipped daily, with 20 brackets in a tray and up to 10 trays on a pallet.
How does Acmeโs production control department coordinate with both its suppliers and customers?
-Acmeโs production control department coordinates with customers by receiving 90, 60, and 30-day forecasts and daily firm orders. It communicates six-week forecasts and weekly confirmed orders to Michigan Steel Company, their supplier. The department also issues weekly build schedules to Acmeโs production departments.
What are the cycle times and machine reliability rates for the stamping and welding processes?
-The stamping machine has a cycle time of 1 second and a reliability (uptime) of 85%. The first welding workstation has a cycle time of 39 seconds with 100% reliability, while the second has a cycle time of 46 seconds and 80% reliability.
How much inventory is observed between the stamping and welding stages?
-Before the stamping process, there are five days' worth of steel coils. After stamping, there are 4,600 pieces of type LH and 2,400 pieces of type RH waiting to be spot welded.
What are the main issues identified in Acmeโs production process?
-The main issues in Acmeโs production process include excessive waiting times and queues between processes, leading to high work-in-process inventory and low inventory turnover. There is a significant contrast between the long product lead time (23.6 days) and the short value-adding time (188 seconds).
What is the total product lead time at Acme, and how does it compare to the value-adding time?
-The total product lead time within Acmeโs factory is 23.6 days. In contrast, the value-adding time (the time spent on actual productive work) is only 188 seconds, highlighting inefficiencies in the process.
What lean tools could be used to improve Acmeโs production process?
-Lean tools such as Value Stream Mapping (VSM) can be used to identify waste (muda), imbalance (mura), and overburden (muri) in the system. Acmeโs production process could benefit from reducing work-in-process inventory, balancing cycle times, and improving material flow between departments.
Outlines
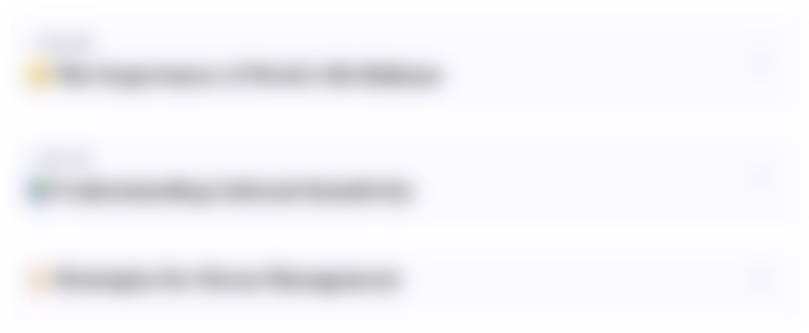
This section is available to paid users only. Please upgrade to access this part.
Upgrade NowMindmap
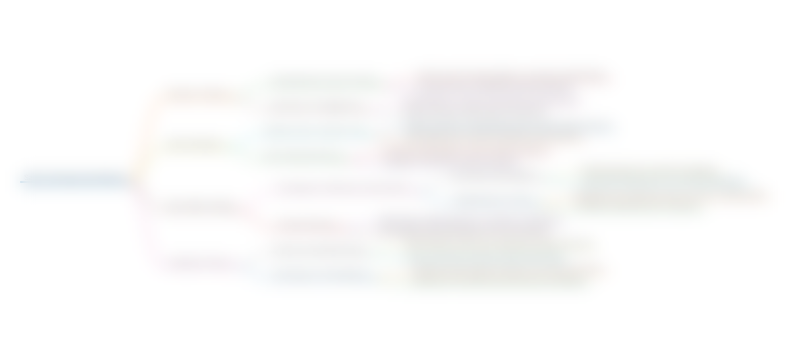
This section is available to paid users only. Please upgrade to access this part.
Upgrade NowKeywords
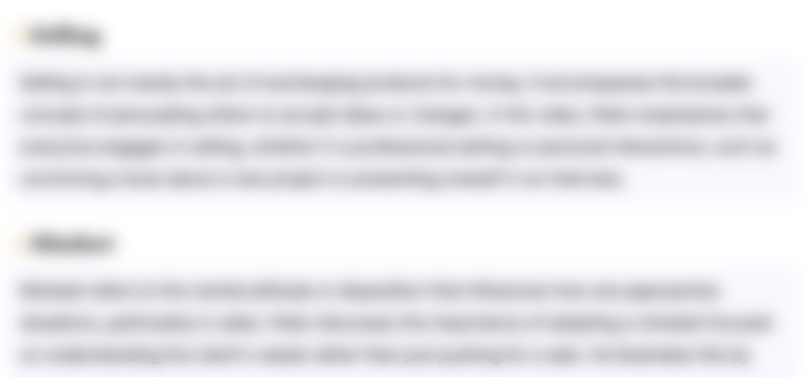
This section is available to paid users only. Please upgrade to access this part.
Upgrade NowHighlights
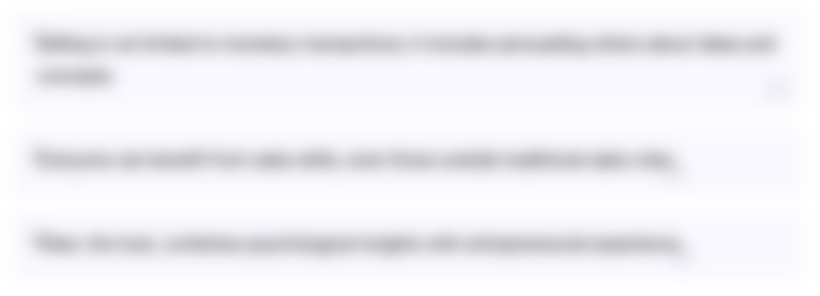
This section is available to paid users only. Please upgrade to access this part.
Upgrade NowTranscripts
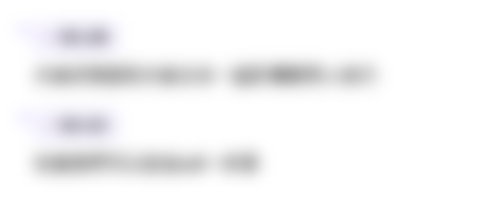
This section is available to paid users only. Please upgrade to access this part.
Upgrade NowBrowse More Related Video
5.0 / 5 (0 votes)