IIoT & Industry 4.0 RANT by Walker Reynolds
Summary
TLDRThis video explores the crucial role of Industry 4.0 and IIoT in modern manufacturing, highlighting the inefficiencies and limitations of traditional systems like ERP, CRM, and MES. The speaker argues that the key to unlocking growth and operational efficiency lies in connecting disparate systems through a Unified Namespace, allowing real-time data flow across all layers of a business. With insights on OEE (Overall Equipment Effectiveness) and the importance of predictive maintenance, the video emphasizes the need for manufacturers to embrace digital transformation or risk falling behind in an increasingly competitive market.
Takeaways
- 😀 Every manufacturer, regardless of size, follows the same basic workflow: sell, plan, produce, store, ship, invoice, and seek repeat business.
- 💼 As manufacturers grow, the complexity of managing this workflow increases, requiring more specialized software like CRM, ERP, and MES.
- 📉 Traditional ERP systems often fail to integrate effectively with operational technology (OT) like MES, SCADA, and PLCs, limiting real-time data flow and operational efficiency.
- 🔧 Many manufacturers waste money on ERP systems that do not improve real-time operational insight, with middleware often being an ineffective solution.
- 💻 The real challenge is connecting business applications to operational systems, but IT departments often resist such connections due to outdated security concerns.
- 📊 The solution to these problems is Industry 4.0, specifically the use of a **Unified Namespace (UNS)**, which enables real-time data sharing between all systems (ERP, MES, SCADA, etc.) without complex middleware.
- ⚙️ MES systems allow manufacturers to track **OEE (Overall Equipment Effectiveness)**, which measures machine availability, quality, and performance, enabling better operational decision-making.
- 📈 OEE scores typically start low (in the 30s) but can be improved to 80-90% with proper MES implementation, increasing manufacturing capacity without additional investment in physical assets.
- 🔮 Predictive maintenance, powered by IIoT, allows manufacturers to decrease scheduled downtime and improve machine performance by predicting failures before they happen.
- 🚀 The next phase of operational growth involves optimizing the **edge**—improving machine performance directly and minimizing inefficiencies in scheduling and machine availability.
- 📉 Manufacturers who fail to adopt IIoT and Industry 4.0 technologies risk falling behind competitors like Amazon, Tesla, and Boeing, who have already integrated these systems to enhance operational performance.
- 🧑💻 The future of manufacturing jobs lies in operations analysis and IIoT infrastructure management, as data analysis and real-time insights become central to driving efficiency and growth.
Q & A
What is the core workflow that every manufacturer follows, regardless of size?
-Every manufacturer, whether a small mom-and-pop shop or a large enterprise, follows the same basic workflow: selling products, planning production, executing manufacturing, storing products, shipping them, invoicing, getting paid, and then asking customers if they want more.
What are the common software tools manufacturers use as they grow?
-As manufacturers grow, they typically start with a simple CRM to manage customer relations and QuickBooks as an ERP system. As the company scales, they often migrate to more robust ERP systems, implement MES (Manufacturing Execution Systems), SCADA software, and eventually adopt warehouse management systems (WMS) and standalone shipping software.
Why do manufacturers tend to delay implementing MES and SCADA software?
-MES and SCADA systems are often among the last pieces of software that manufacturers buy because, initially, other systems like ERP or CRM are prioritized. MES and SCADA typically come later as the company needs greater visibility and control over production processes.
Why is it a mistake for manufacturers to rely solely on ERP systems?
-ERP systems are often marketed as comprehensive solutions, but they don't provide the real-time operational data that manufacturers need to run their business efficiently. Relying only on ERP can lead to inefficiencies and wasted investment, as ERP systems often lack the ability to manage real-time operations and data from the production floor.
What role does Industry 4.0 play in improving manufacturing operations?
-Industry 4.0 involves the use of digital transformation tools like IIoT (Industrial Internet of Things), unified namespaces, and real-time data to enhance manufacturing operations. It enables seamless integration between different systems and provides real-time insights into the production process, which helps manufacturers make better decisions and optimize efficiency.
What is a unified namespace in the context of Industry 4.0?
-A unified namespace in Industry 4.0 is a digital representation of the entire business, where all software systems (ERP, MES, SCADA, etc.) publish and consume data from a central repository. This simplifies integration and ensures that data from different systems is accessible and useful without needing complex connections or middleware.
What is the common misconception about IT departments in relation to Industry 4.0?
-A common misconception is that IT departments often resist connecting operational technology (like PLCs and HMIs) to business networks due to security concerns. However, the primary risk lies in multicast traffic, and using technologies like network address translation and outbound-only data reporting can mitigate these issues without compromising security.
Why do manufacturers struggle with digital transformation in Industry 3.0 to 4.0?
-Manufacturers often struggle with digital transformation because they can't even fully implement the basic Industry 3.0 systems, let alone leap to Industry 4.0. This is due to internal resistance, lack of understanding of new technologies, and difficulty integrating disparate systems effectively.
How does OEE (Overall Equipment Effectiveness) improve after implementing MES systems?
-After implementing MES systems, manufacturers often see a significant improvement in OEE, with average OEE numbers jumping from the 30% range to 80% in just a few months. This is due to better visibility into machine availability, quality, and performance, which leads to more efficient production and less downtime.
What are the next steps once a manufacturer achieves high OEE?
-Once a manufacturer achieves high OEE, the next step is to focus on improving the performance of machines at the edge. This includes optimizing PLC programming, decreasing scheduled downtime, and leveraging predictive maintenance using machine learning, which helps further increase efficiency without affecting OEE.
Outlines
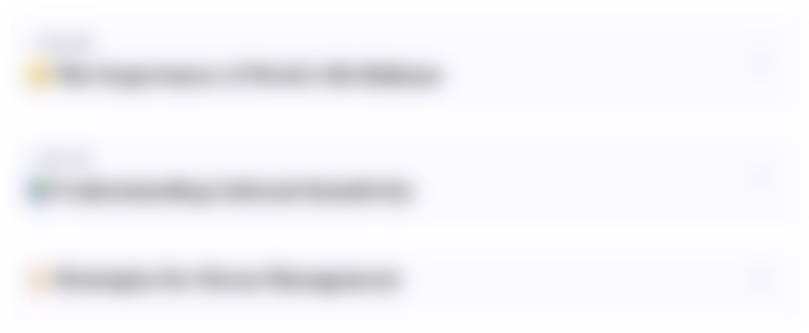
This section is available to paid users only. Please upgrade to access this part.
Upgrade NowMindmap
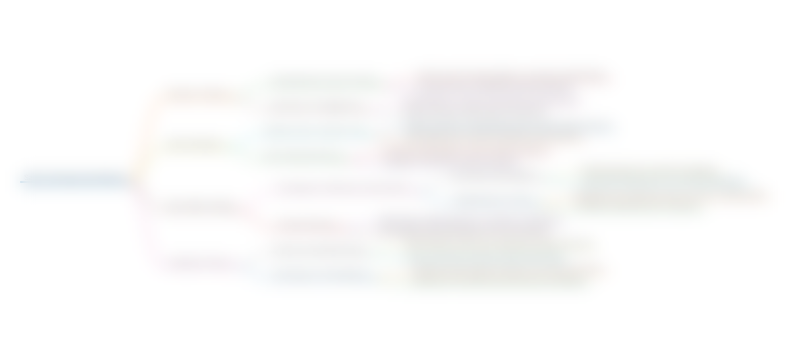
This section is available to paid users only. Please upgrade to access this part.
Upgrade NowKeywords
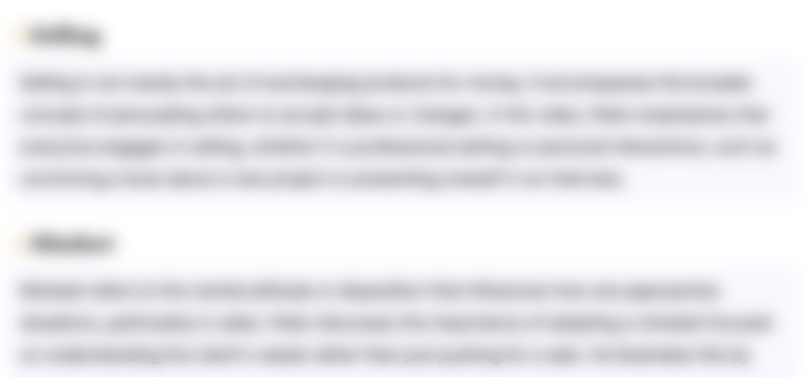
This section is available to paid users only. Please upgrade to access this part.
Upgrade NowHighlights
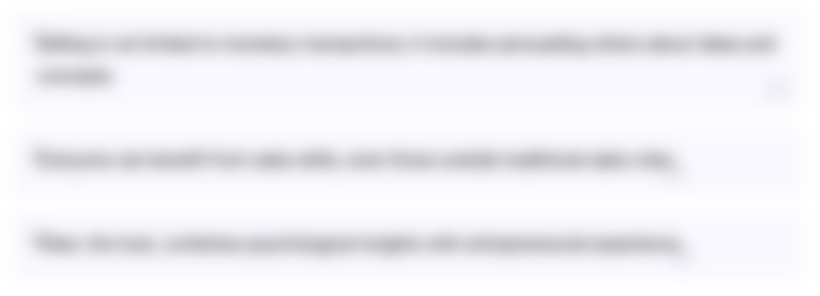
This section is available to paid users only. Please upgrade to access this part.
Upgrade NowTranscripts
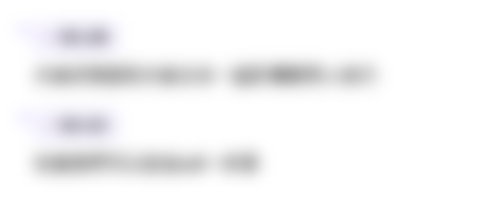
This section is available to paid users only. Please upgrade to access this part.
Upgrade NowBrowse More Related Video

WHAT IS THE HYDROSPHERE? | Educational Videos for Kids

Futura Profissão - Técnico em Petroquímica
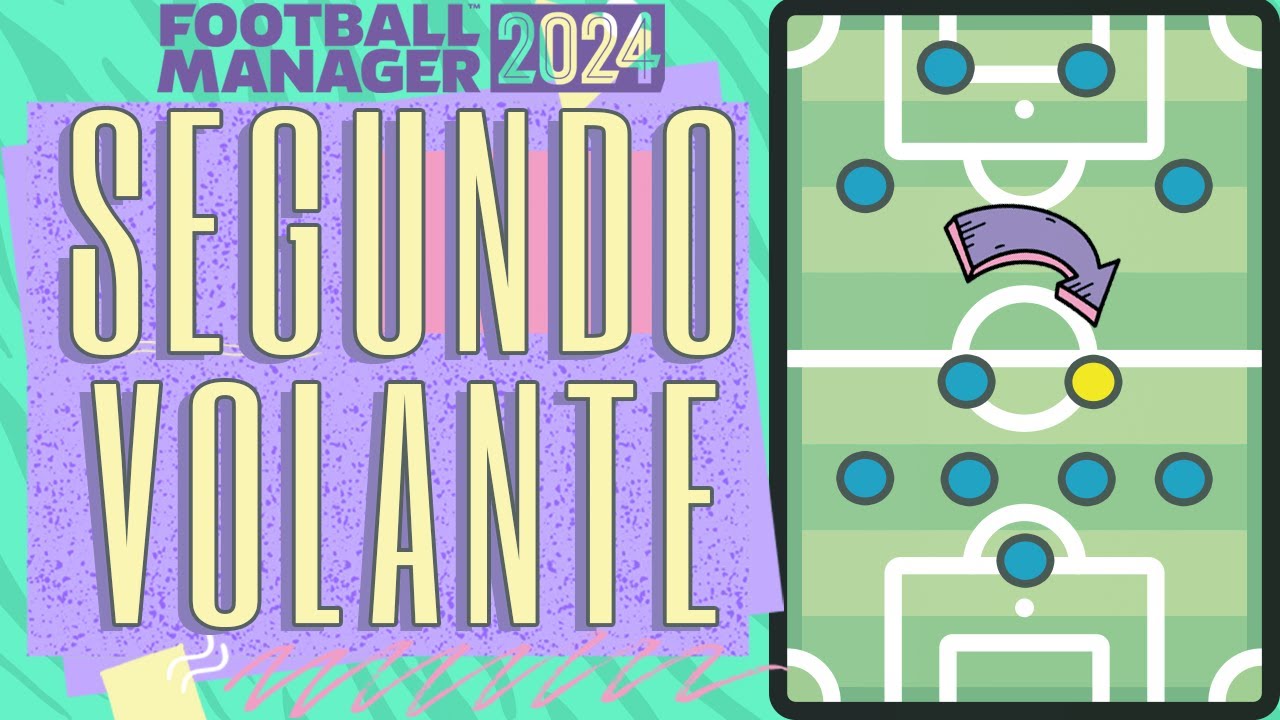
Segundo Volante FM24 Role Guide

DOE Ekspor perikanan dalam memenuhi standar keamanan dan keberlanjutan Global

pola permainan formasi 2 3 5 dalam menyerang dan bertahan
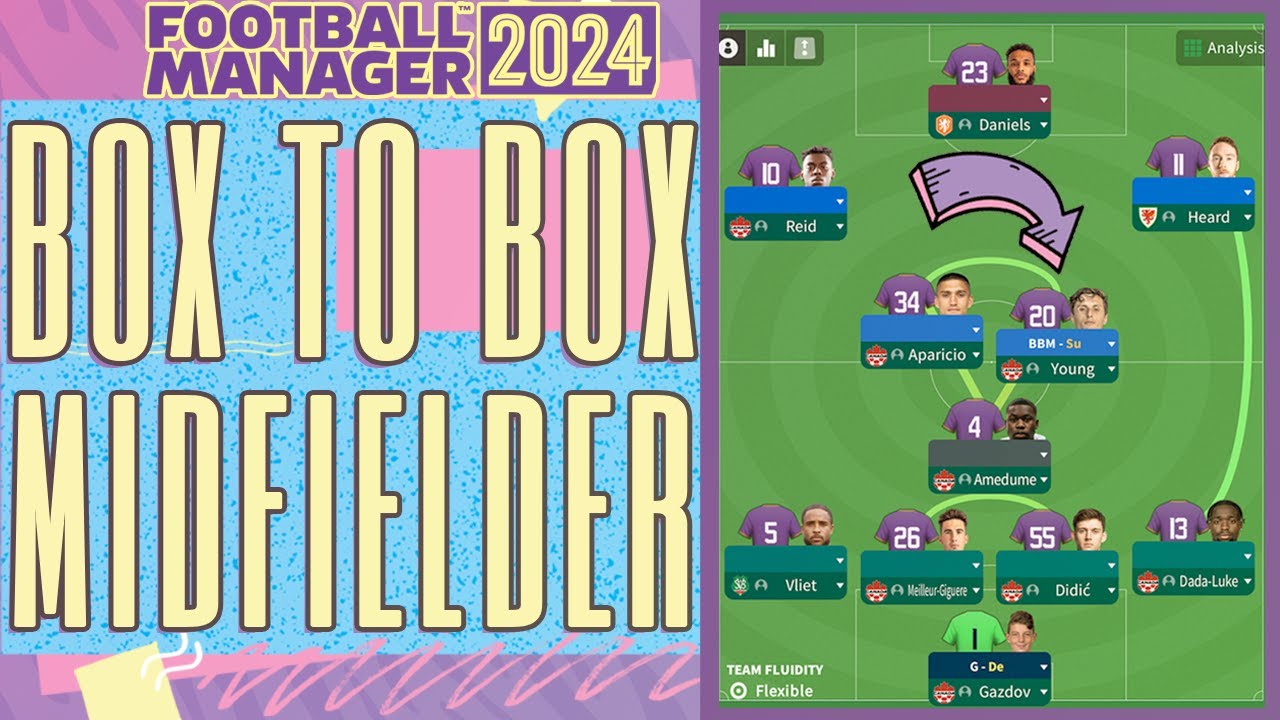
Box to Box Midfielder FM24 Role Guide

E003 - NFA Form Types
5.0 / 5 (0 votes)