Manajemen Persediaan (Just In Time - JIT)
Summary
TLDRIn this educational video, the host introduces the concept of inventory management, particularly focusing on the importance of managing raw materials, semi-finished goods, and finished products in manufacturing industries. The video covers key factors influencing inventory size, such as lead time, usage frequency, available funds, and product shelf life. It explores optimal inventory costs, including ordering and holding costs, and discusses Just in Time (JIT) production, a strategy pioneered by Toyota that minimizes inventory by producing only in response to demand. The video aims to help viewers understand the significance of inventory control for stable production and business profitability.
Takeaways
- 😀 Inventory management is crucial for businesses, as it involves managing raw materials, work-in-progress, and finished goods in manufacturing industries.
- 😀 The size of inventory is determined by factors like lead time, frequency of material usage, available funds, and product shelf life.
- 😀 Optimal inventory costs include ordering costs (variable depending on ordering frequency) and carrying costs (variable depending on the amount stored).
- 😀 Ordering costs involve several components, including order processing, shipping, receiving, inspection, and warehouse placement.
- 😀 Carrying costs include expenses related to warehouse rent, material handling, insurance, and potential product deterioration over time.
- 😀 The purpose of maintaining inventory includes stabilizing production, ensuring demand fulfillment, and taking advantage of bulk purchasing discounts.
- 😀 Just in Time (JIT) is a strategy where materials are delivered right when needed for production, minimizing inventory holding costs.
- 😀 The JIT method was first popularized by Toyota in 1978 and focuses on producing only according to actual demand, eliminating excess stock.
- 😀 Key benefits of JIT include reduced inventory levels, improved quality control, lower labor costs, and minimized warehouse space requirements.
- 😀 Successful JIT implementation requires trust and collaboration between suppliers, manufacturers, and customers to ensure timely deliveries and production schedules.
Q & A
What is the definition of inventory as explained in the video?
-Inventory is part of working capital, which can be divided into raw materials (BB), work-in-progress items, and finished goods. This varies depending on the type of industry, especially in manufacturing where raw materials are a key focus.
What are the factors that determine inventory size for raw materials?
-The four main factors determining inventory size are: lead time (the waiting time for an ordered item to arrive), frequency of material usage over a period (usually one year), available funds, and the shelf life of inventory (since some goods may expire or degrade faster than others).
What are the two types of costs considered in determining optimal inventory?
-The two types of costs are ordering costs (related to the frequency of ordering) and carrying costs (related to the quantity of goods held in storage). Both are variable costs, influenced by how often orders are placed and how much inventory is stored.
What are some examples of ordering costs in a business?
-Ordering costs include expenses related to the ordering process, such as placing orders, shipping, receiving, inspecting goods, weighing items, storing them in the warehouse, and handling payment processes.
What are some examples of carrying costs in inventory management?
-Carrying costs include warehouse rent, maintenance of stock, capital costs for storing goods, insurance, goods deterioration, and the risk of products becoming obsolete or expired.
What are the goals of inventory management in a business?
-The goals of inventory management include stabilizing production, taking advantage of bulk purchasing discounts, fulfilling additional or unexpected demand, anticipating market changes, avoiding stockouts, and mitigating supply chain disruptions.
What is the concept of Just In Time (JIT) inventory?
-Just In Time (JIT) is an inventory strategy where materials are ordered and delivered only when needed for production, reducing the need for stockpiling inventory. This method minimizes storage costs and ensures that inventory is not wasted.
Who introduced the Just In Time method and when?
-The Just In Time method was introduced by Taichi Ono at Toyota in 1978 as a way to streamline production and minimize inventory costs.
What are some benefits of implementing Just In Time (JIT) in a business?
-Benefits of JIT include reduced inventory levels, improved quality control, lower labor costs, reduced storage needs, minimized production delays, less waste from damaged goods, better machine utilization, and overall improved efficiency.
What is required for the successful implementation of Just In Time (JIT)?
-For JIT to be successful, there must be strong integration and trust among all parties in the supply chain, from suppliers to customers. Companies must also have reliable and efficient logistics and communication systems in place to ensure timely deliveries.
Outlines
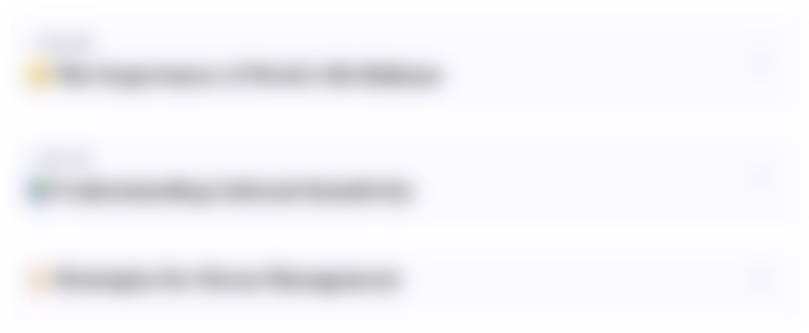
このセクションは有料ユーザー限定です。 アクセスするには、アップグレードをお願いします。
今すぐアップグレードMindmap
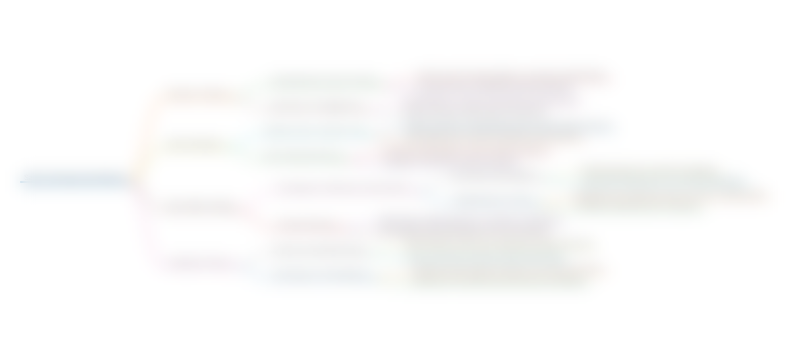
このセクションは有料ユーザー限定です。 アクセスするには、アップグレードをお願いします。
今すぐアップグレードKeywords
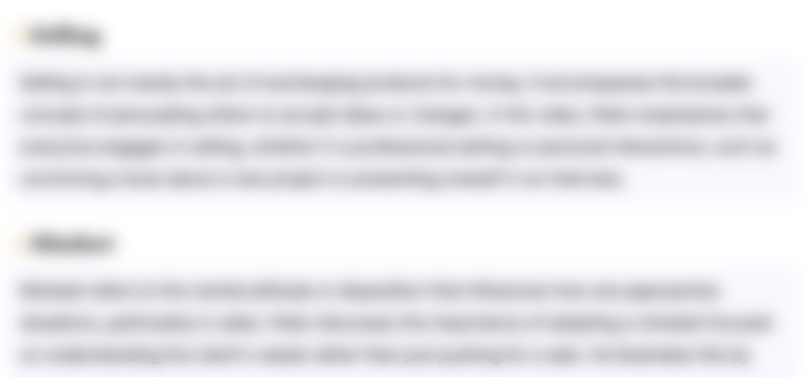
このセクションは有料ユーザー限定です。 アクセスするには、アップグレードをお願いします。
今すぐアップグレードHighlights
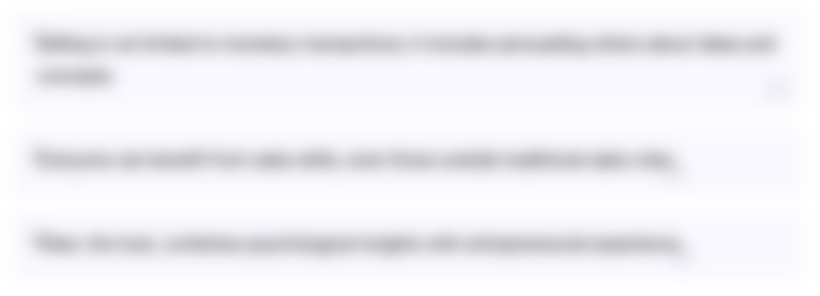
このセクションは有料ユーザー限定です。 アクセスするには、アップグレードをお願いします。
今すぐアップグレードTranscripts
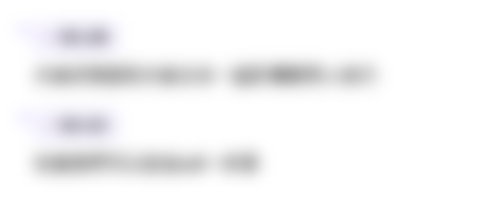
このセクションは有料ユーザー限定です。 アクセスするには、アップグレードをお願いします。
今すぐアップグレード関連動画をさらに表示

3 Types of Inventory (Raw Materials, WIP, and Finished Goods)
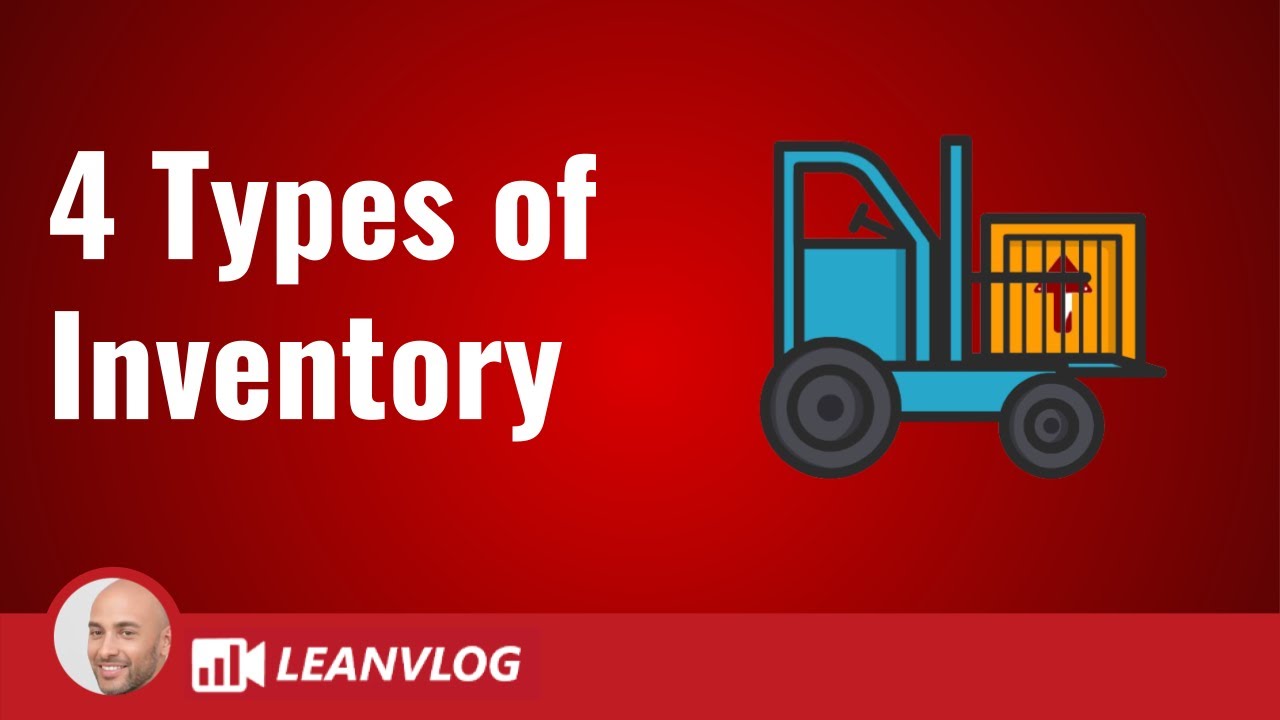
Types of Inventory : The 4 Different Buckets to Know

Auditing inventory - part 3 - product costing for manufacturing firms
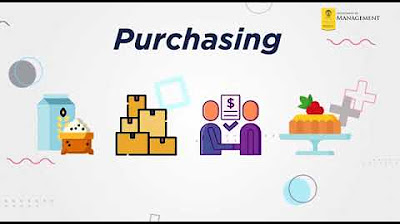
Pengantar Bisnis Sesi 11 Produksi dan Manajemen Operasi
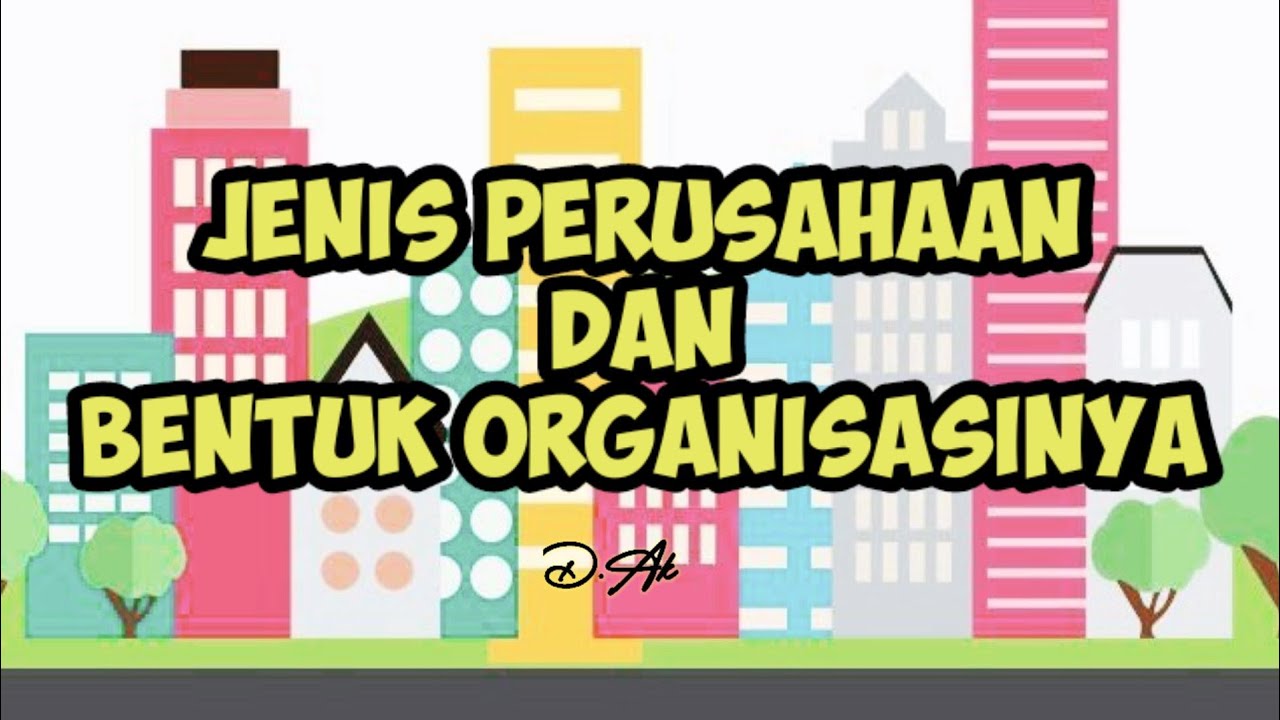
Jenis perusahaan dan bentuk organisasinya
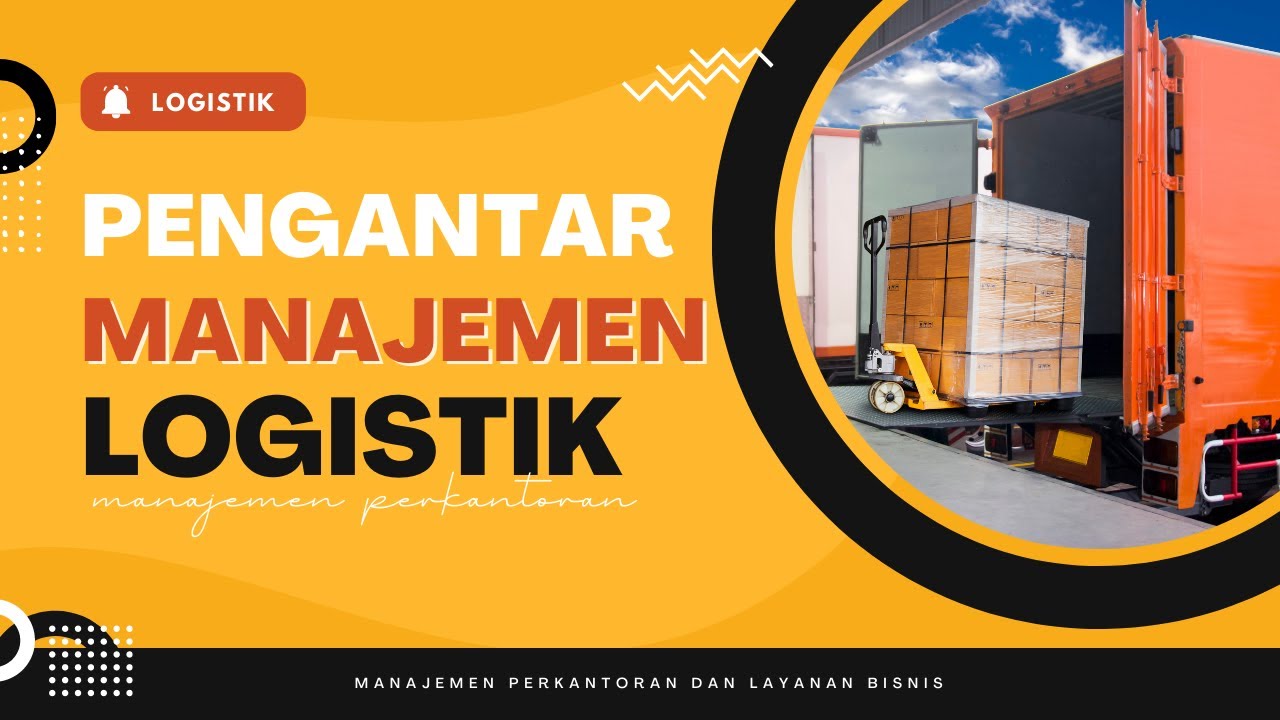
Pengantar Manajemen Logistik - MPLB CP 8
5.0 / 5 (0 votes)