CNC Basics - Everything a Beginner Needs To Know
Summary
TLDRThis video is an introduction to CNC machines for beginners. It explains the basics of CNC technology, specifically focusing on CNC mills and routers. Viewers will learn about the essential parts of a CNC machine, the design and setup process, tool paths, work holding, and the importance of offsets and feeds and speeds. The host also discusses the differences between CNC machines and 3D printers, along with practical tips for getting started with CNC machining. The video emphasizes that CNC machining involves more hands-on control and precision compared to other automated processes.
Takeaways
- 🛠️ CNC stands for Computer Numerical Control, a technology that moves machinery to cut materials.
- 🔧 CNC machines come in different types, including routers (for wood) and mills (for metal), though there is overlap.
- 🖼️ A CNC machine typically has a bed for material and a cutting head that moves on three axes; more advanced machines use four or five axes.
- ⚙️ The cutting tools used are called end mills, which differ from drill bits and come in various shapes and sizes.
- 🖥️ CNC machining involves several steps: design, tool path creation, work holding, and setting offsets.
- 📐 Design for CNC is different from 3D printing and often involves CAD software to account for machine limitations.
- 🚀 Tool paths and speeds must be calculated and programmed manually, often with help from CAM software.
- 🔩 Work holding secures materials during the cutting process and is critical to ensure the machine doesn't crash.
- 📏 Offsets, or datums, tell the machine where the material is placed before starting the cut.
- 🧹 Post-milling, the part often requires cleanup, such as sanding or deburring, to achieve a finished look.
Q & A
What is a CNC machine and how is it defined?
-A CNC machine, or Computer Numerical Control machine, is a device that uses computer programming to control its movements. This term is broad and can refer to various devices such as CNC mills, routers, plasma tables, 3D printers, laser cutters, and vinyl cutters. The main commonality is that they all use computer control to guide their operations.
What are the differences between CNC routers and CNC mills?
-CNC routers are typically used to cut wood and are generally lighter in build, while CNC mills are more robust and designed for cutting metals. Despite these distinctions, there can be overlap; some people use CNC routers to cut metal and CNC mills to cut wood. The primary difference lies in the intended use and build of each machine.
What basic components do all CNC machines share?
-Most CNC machines, regardless of type, have a bed (or table) and a cutting head (spindle or router) that moves in at least three axes. Some machines may offer more complex movements with 4, 5, or more axes. These components allow the machine to cut, carve, or engrave materials according to programmed paths.
How does designing for a CNC machine differ from designing for a 3D printer?
-Designing for a CNC machine requires considering the cutter’s limitations, such as the inability to create overhangs unless using more complex multi-axis machines. While 3D printers build objects layer by layer, CNC machines remove material, making the design process more about managing tool paths and material removal strategies.
What is CAM and how does it relate to CNC machining?
-CAM, or Computer-Aided Manufacturing, involves creating the tool paths that a CNC machine will follow. Unlike 3D printing, where the software automatically generates paths, CNC operators must manually set parameters like tool speed, feed rate, and path direction. CAM software helps in designing these paths and ensuring precise execution.
Why is work holding important in CNC machining?
-Work holding ensures that the material being cut remains securely in place. Because CNC machines apply forces in multiple directions, improper work holding can lead to movement or dislocation of the material, causing inaccurate cuts or potential damage to the machine and workpiece.
What are offsets and why are they crucial in CNC machining?
-Offsets, or datums, refer to the process of telling the CNC machine the exact location of the material on the bed. Since the machine has no inherent knowledge of where the material is placed, setting offsets accurately is crucial to ensure the tool paths align correctly with the material. Incorrect offsets can lead to crashes or misaligned cuts.
What is tool length compensation and why is it necessary?
-Tool length compensation involves informing the machine about the length of the cutting tool in use. This is necessary because different tools have varying lengths, and the machine needs this information to maintain the correct cutting depth and avoid collisions. It can be done manually or with automated touch-off devices.
What is fixturing and how does it differ from standard work holding?
-Fixturing is a specific type of work holding designed to enable the repeated, accurate placement of the same workpiece for multiple cuts. It is particularly useful for production runs where the same part needs to be machined multiple times without re-calibrating or re-setting the machine for each piece.
What factors should be considered when choosing a CNC machine?
-When choosing a CNC machine, consider what materials you plan to cut (wood, metal, etc.), the size of the workpieces, and your budget. For wood, CNC routers are typically more suitable, while CNC mills are better for metals. It's important to match the machine's capabilities with your intended projects.
Outlines
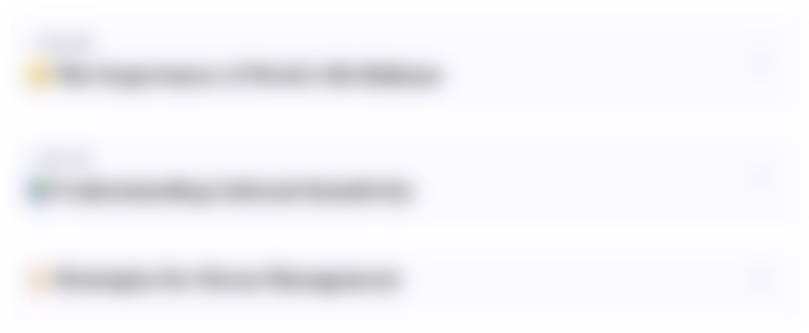
このセクションは有料ユーザー限定です。 アクセスするには、アップグレードをお願いします。
今すぐアップグレードMindmap
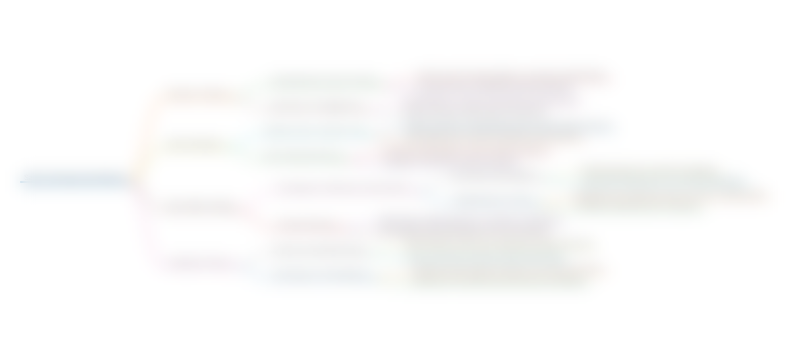
このセクションは有料ユーザー限定です。 アクセスするには、アップグレードをお願いします。
今すぐアップグレードKeywords
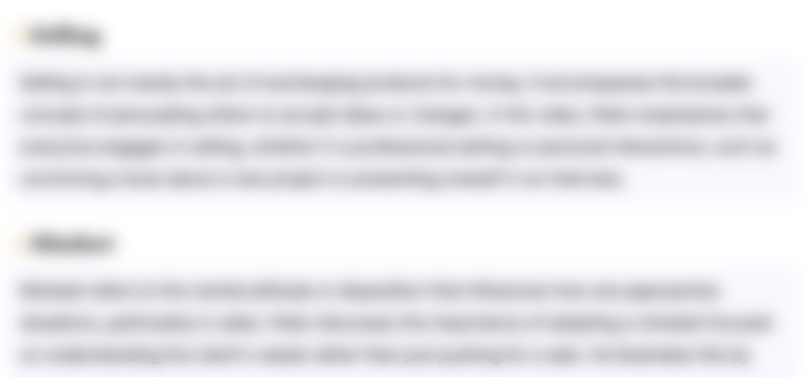
このセクションは有料ユーザー限定です。 アクセスするには、アップグレードをお願いします。
今すぐアップグレードHighlights
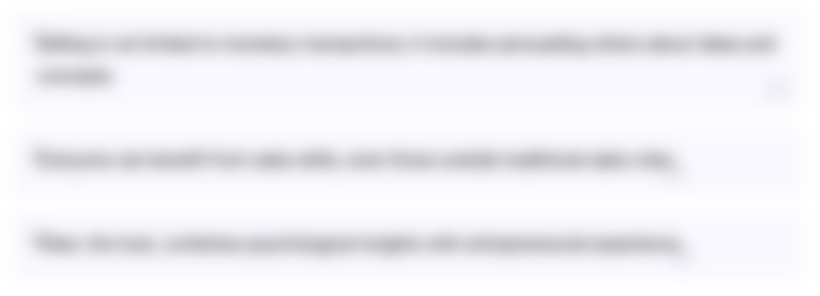
このセクションは有料ユーザー限定です。 アクセスするには、アップグレードをお願いします。
今すぐアップグレードTranscripts
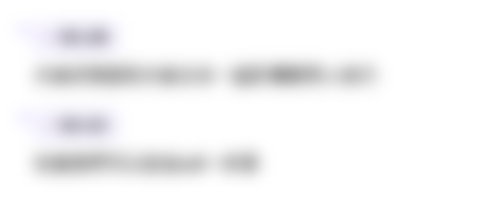
このセクションは有料ユーザー限定です。 アクセスするには、アップグレードをお願いします。
今すぐアップグレード関連動画をさらに表示
5.0 / 5 (0 votes)