Non-destructive testing (NDT) at TWI
Summary
TLDRThis video script offers an insightful introduction to non-destructive testing (NDT) techniques, essential for maintaining structural integrity without damaging components. It covers six common NDT methods: magnetic particle inspection, liquid penetrant inspection, radiography, ultrasonic testing, eddy current testing, and thermography. Each method's principle, application, and benefits are outlined, highlighting the importance of these techniques in various industries for detecting flaws and ensuring safety.
Takeaways
- 🔨 **Destructive vs. Non-Destructive Testing**: Destructive testing damages the component, making it unusable post-test, while non-destructive testing (NDT) allows for continued use of the component.
- 🧲 **Magnetic Particle Inspection (MPI)**: MPI is used to find surface and near-surface discontinuities in ferromagnetic materials by applying a magnetic field and observing the pattern of ferrous particles.
- 🌈 **MPI Techniques**: MPI can be performed using color contrast or fluorescent methods, with the latter being more sensitive for detecting defects.
- 💧 **Liquid Penetrant Inspection**: This NDT method is used for non-ferromagnetic materials to find surface defects by applying a colored penetrant that is drawn into surface-breaking defects.
- 📼 **Radiography**: X-rays are used to detect internal flaws in materials; digital radiography is becoming more prevalent over traditional wet radiography due to its efficiency and image quality.
- 🔊 **Ultrasonic Testing (UT)**: UT uses high-frequency sound waves to detect discontinuities within a material; it's effective for various applications, including the inspection of welds and pressure vessels.
- 🌊 **Time-of-Flight Diffraction (TOFD)**: A type of UT that is particularly useful for sizing planar flaws, though it can be less reliable with certain material conditions.
- 📊 **Phased Array Systems**: These systems use ultrasonic beams at various angles for inspections, offering a more efficient method for detecting flaws in welds and other structures.
- 🌐 **Surface Ultrasonics**: Used for detecting surface-breaking cracks, especially in petrochemical plants and civil engineering structures like bridges.
- 🌊 **Long-Range Guided Wave Ultrasonics**: This technique uses low-frequency waves for detecting corrosion and erosion in pipes, providing a quick screening method for long pipe lengths.
- 🔗 **Eddy Current Testing**: A method for detecting surface-breaking cracks and material composition variations, especially effective for non-ferritic materials.
- 🔥 **Thermography**: Uses infrared cameras to detect temperature anomalies in components, useful for remote inspection of equipment, including those operating at high temperatures.
Q & A
What is the primary difference between destructive and non-destructive testing?
-Destructive testing leaves you without a serviceable component or test specimen once the testing is over, whereas non-destructive testing allows the structure to remain in daily service after testing.
What is Magnetic Particle Inspection (MPI) used for?
-MPI is used to find surface and just beneath the surface discontinuities in ferromagnetic materials by introducing a magnetic flux into the material and using ferrous particles that are drawn to the site of flux leakage.
How do color contrast and fluorescent techniques in MPI differ?
-In color contrast MPI, a thin layer of white paint is applied and black ink is sprayed on, showing defects as black against white. The fluorescent technique uses a fluorescent medium and a fluorescent lamp to make defects appear as bright green, which is more sensitive than color contrast.
What is Liquid Penetrant Inspection and how does it work?
-Liquid Penetrant Inspection is used for locating surface defects on non-ferromagnetic materials. It involves cleaning and degreasing the component, applying a colored penetrant, and then using a powder developer to draw the penetrant out of flaws, making them stand out.
How does Radiographic testing work and what are its requirements?
-Radiographic testing uses X-rays to detect flaws within a material. It requires access to both sides of the component, with a sensitive film on one side to capture the X-ray image, which reveals flaws by showing where the X-rays are absorbed or transmitted differently.
What is the difference between wet and digital radiography?
-Wet radiography uses photographic films and requires traditional darkroom technology, while digital radiography relies on substances that fluoresce when exposed to X-radiation, converting this fluorescence into a digital signal for easier manipulation and storage.
What is Ultrasonic Testing (UT) and how does it locate discontinuities?
-UT is a method that uses ultrasonic signals above audible frequencies to detect discontinuities. The signal is passed from a probe into the component, and when it encounters a discontinuity, it reflects back. By measuring the time it takes for the signal to return, the location of the discontinuity can be determined.
What is the purpose of Time-of-Flight Diffraction (TOFD) in UT?
-TOFD is used mainly for sizing planar flaws oriented perpendicular to the surface. It is less reliable with a high density of defects, scattered inclusions, or coarser grained materials.
How do Phased Array systems in UT differ from standard UT?
-Phased Array systems offer the possibility of performing inspections with ultrasonic beams of various angles and focal lengths using a single array of transducers, making it quicker and with reduced scanning requirements compared to standard UT.
What is the application of Long-Range Guided Wave Ultrasonics and what advantages does it offer?
-Long-Range Guided Wave Ultrasonics uses low-frequency guided waves to detect corrosion and erosion in pipe work. It provides 100% initial screening coverage of a long length of pipe and only requires local access to the pipe surface, making it suitable for various pipe work applications.
How does Eddy Current Testing work and what is its primary use?
-Eddy Current Testing involves placing a circular coil carrying an alternating current near an electrically conductive specimen. The alternating current generates a changing magnetic field that induces eddy currents in the test object, which are useful for detecting surface-breaking or near-surface cracking and variations in material composition.
What is Thermography and how is it used in non-destructive testing?
-Thermography involves using an infrared camera to detect abnormally hot or cold areas on a component. It is a remote technique suitable for equipment operating at elevated temperatures and can be used for inspection of low conductivity materials like composites.
Outlines
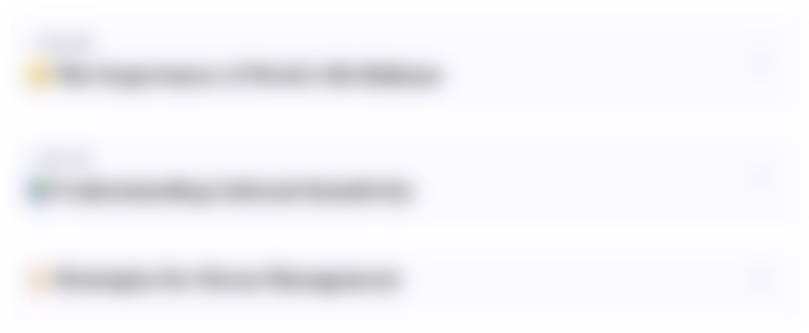
このセクションは有料ユーザー限定です。 アクセスするには、アップグレードをお願いします。
今すぐアップグレードMindmap
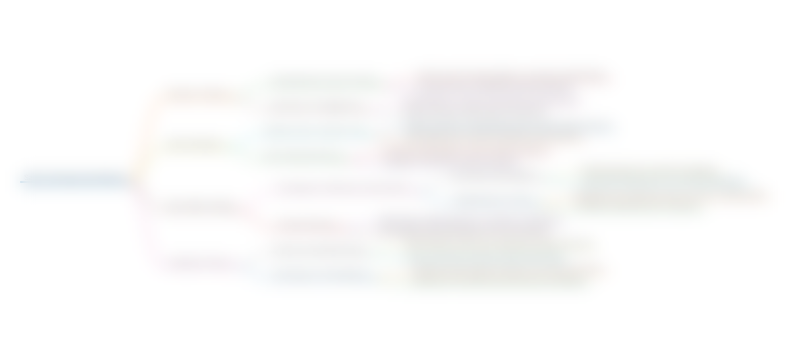
このセクションは有料ユーザー限定です。 アクセスするには、アップグレードをお願いします。
今すぐアップグレードKeywords
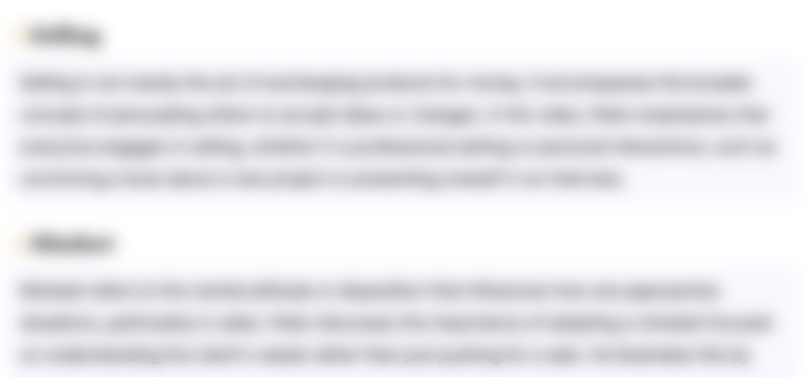
このセクションは有料ユーザー限定です。 アクセスするには、アップグレードをお願いします。
今すぐアップグレードHighlights
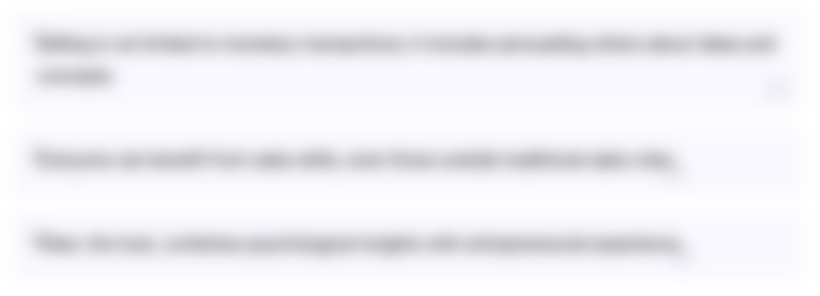
このセクションは有料ユーザー限定です。 アクセスするには、アップグレードをお願いします。
今すぐアップグレードTranscripts
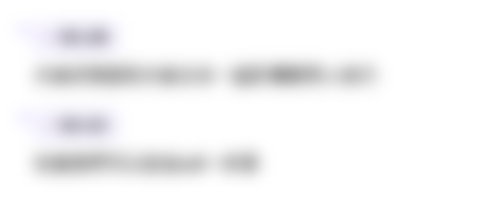
このセクションは有料ユーザー限定です。 アクセスするには、アップグレードをお願いします。
今すぐアップグレード5.0 / 5 (0 votes)