Common Mistakes Made By Newly Promoted Leaders
Summary
TLDRThe video script discusses a common leadership challenge where leaders feel compelled to solve every problem their team members bring to them, leading to inefficiency and dependency. Instead, it advocates for a leadership style where leaders encourage team members to collaborate and find solutions together. By checking in with the team and facilitating discussions rather than taking on all the problems themselves, leaders can foster independence and more efficient problem-solving, ultimately creating a more effective and satisfied team.
Takeaways
- 🔧 Brandon faces a challenge with his lathe, as it cannot cut the required 30° angle without significant adjustments.
- ⏰ Making the necessary adjustments to the lathe would require about two hours of overtime.
- 🔄 To avoid overtime, Brandon suggests cutting the flange at 25°, which could still work.
- 🤔 A colleague points out that if Brandon cuts the flange at 25° and another part is milled at 70°, the system won't seal properly.
- 📏 The team discusses the possibility of using a 65° angle instead to stay within the 5% variance allowed in the specifications.
- 💡 The decision to allow a 5° variance could lead to a 2 mm gap, potentially causing a three to five-day downtime.
- 👥 The script highlights the importance of involving the entire team in problem-solving rather than allowing one person to make decisions alone.
- 📉 Allowing employees to rely on a single leader for decisions can lead to inefficiency and a lack of personal growth among the team.
- 📚 The script emphasizes the need for leaders to guide their team in solving problems independently, fostering growth and efficiency.
- 💬 Regular check-ins and communication with the team can prevent issues from escalating and help maintain workflow.
Q & A
What problem does Brandon initially bring up in the conversation?
-Brandon's problem is that his machine cannot cut a flange at a 30° angle. Adjusting it to do so would require about two hours of overtime.
How does Brandon suggest resolving the issue with the flange angle?
-Brandon suggests cutting the flange at a 25° angle instead, thinking that it will work without causing significant problems.
Why does the supervisor initially agree to Brandon's suggestion?
-The supervisor agrees to Brandon's suggestion because it would avoid the two hours of overtime required to retool the machine for a 30° cut, and there is a 5° variance allowed in the specifications.
What issue arises after the supervisor approves the change to a 25° flange?
-Another team member points out that if the flange is cut at 25° and another part is milled at 70°, the system won't seal properly, leading to a potential 2mm gap and several days of downtime.
What leadership mistake is highlighted in the script when dealing with the problem?
-The leadership mistake highlighted is the tendency for leaders to take on all problems themselves, which can create a codependent relationship where employees rely on the leader for all solutions instead of solving problems independently.
What alternative leadership approach is suggested in the script?
-The script suggests an alternative leadership approach where leaders position themselves around the edge of the group, checking in with team members regularly to support them in solving problems rather than taking on the issues themselves.
How does the supervisor implement the suggested leadership approach in the script?
-The supervisor gathers the team members involved, discusses the problem collaboratively, and encourages them to come up with a solution together, which results in a more efficient resolution.
What final solution is proposed by the team to solve the flange cutting issue?
-The team proposes that another member helps Brandon retool the machine, which will allow them to complete the job without causing downtime or other complications.
What is the broader lesson on leadership that the script aims to convey?
-The broader lesson is that effective leadership involves empowering team members to solve problems themselves, which can lead to better outcomes and more capable, independent employees.
Why is it important for leaders to avoid taking on all problems themselves, according to the script?
-It's important because if leaders take on all problems, it can lead to them feeling overwhelmed and unfulfilled, while their team members may become less capable and more dependent on the leader for solutions.
Outlines
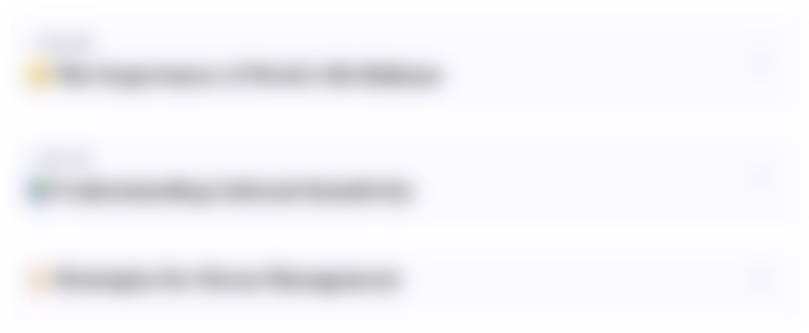
Cette section est réservée aux utilisateurs payants. Améliorez votre compte pour accéder à cette section.
Améliorer maintenantMindmap
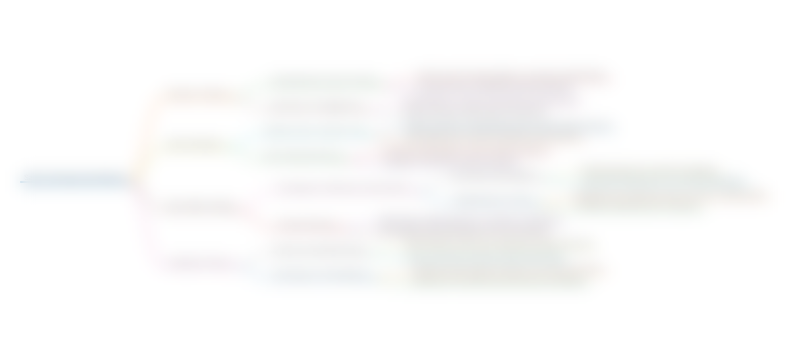
Cette section est réservée aux utilisateurs payants. Améliorez votre compte pour accéder à cette section.
Améliorer maintenantKeywords
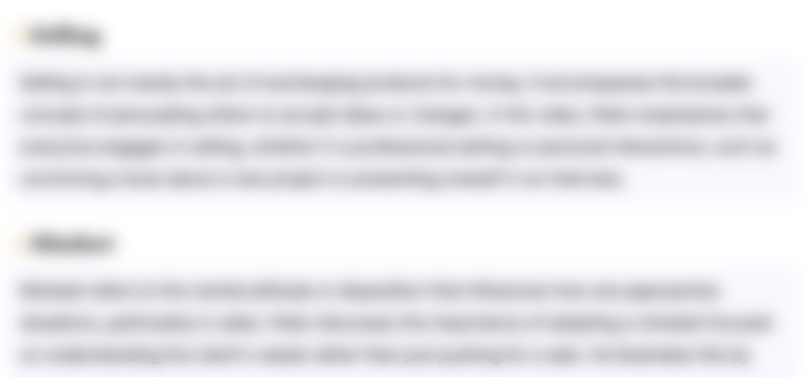
Cette section est réservée aux utilisateurs payants. Améliorez votre compte pour accéder à cette section.
Améliorer maintenantHighlights
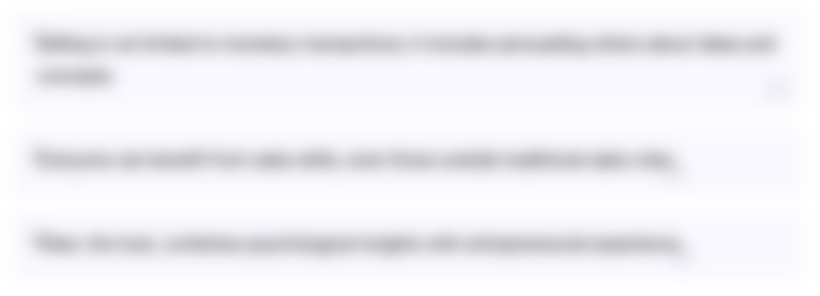
Cette section est réservée aux utilisateurs payants. Améliorez votre compte pour accéder à cette section.
Améliorer maintenantTranscripts
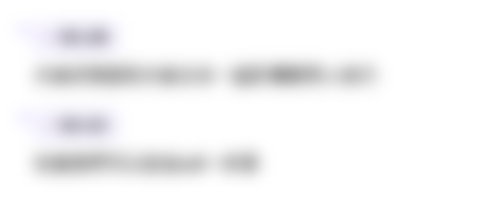
Cette section est réservée aux utilisateurs payants. Améliorez votre compte pour accéder à cette section.
Améliorer maintenant5.0 / 5 (0 votes)