3 5s Orientation Part 1
Summary
TLDRThis video script provides an in-depth look at the 5S methodology, a workplace organizational strategy originating from Japan's Toyota Production System. The key components of 5S—Sort, Set in Order, Shine, Standardize, and Sustain—are discussed in relation to improving efficiency, safety, and cleanliness in the workplace. The video explains how implementing 5S can help eliminate waste, streamline processes, reduce costs, and ultimately lead to higher profits. The script also touches on the addition of a 6th S, 'Safety,' to create a well-rounded and safe work environment. Practical examples from manufacturing and office settings are used to illustrate the concepts.
Takeaways
- 😀 5S is a methodology originating from Japan, initially used in the Toyota Production System to improve efficiency and quality in manufacturing.
- 😀 The primary goal of 5S is to eliminate waste and improve workplace organization, ultimately increasing profitability and reducing costs.
- 😀 5S stands for Sort, Set in Order, Shine, Standardize, and Sustain, with Safety often added as an extra element in some systems.
- 😀 Waste (or 'muda' in Japanese) refers to anything unnecessary in a process, such as excess inventory, overproduction, or defects.
- 😀 Companies adopting 5S can reduce waste in several forms, including overproduction, waiting times, transportation inefficiencies, and defect-related issues.
- 😀 Sorting (Seiri) involves removing unnecessary items from the workplace to keep only what is essential for the job.
- 😀 Setting in Order (Seiton) ensures that necessary items are properly organized, labeled, and easy to find, creating an efficient workspace.
- 😀 Shining (Seiso) goes beyond regular cleaning to address the sources of contamination and ensure equipment is in optimal condition.
- 😀 Standardizing (Seiketsu) involves creating consistent processes and practices for maintaining the orderliness and cleanliness established in earlier steps.
- 😀 Sustaining (Shitsuke) requires developing a culture of discipline, ensuring that employees continue to follow and improve upon 5S practices over time.
- 😀 Safety (Anzen) is sometimes included as an additional S, emphasizing the importance of a safe and hazard-free workplace as a foundation for the success of 5S.
Q & A
What is the origin of the 5S methodology?
-The 5S methodology originated in Japan after World War II as part of the Toyota Production System (TPS). It was developed to help remove debris and improve efficiency in Japanese factories.
Why has the 5S system become popular globally?
-The 5S system has become popular globally because it helps companies improve workflow, reduce waste, enhance safety, and increase productivity. It is now applied in various industries, including manufacturing, service sectors, and offices.
What does '5S' stand for, and what are its main components?
-5S stands for five principles: Sort (Seiri), Set in Order (Seiton), Shine (Seiso), Standardize (Seiketsu), and Sustain (Shitsuke). An additional 'S' for Safety (Anzen) is sometimes added in modern adaptations.
What is the primary goal of implementing 5S in an organization?
-The primary goal of implementing 5S is to eliminate waste, improve efficiency, and ensure a clean, safe, and organized workplace. It aims to enhance quality and reduce costs while boosting overall productivity and profitability.
What does the 'Sort' (Seiri) step in 5S involve?
-The 'Sort' step involves identifying and separating necessary items from unnecessary ones in the workplace. Unnecessary items are removed to create a more organized and focused environment.
How does the 'Set in Order' (Seiton) step improve efficiency?
-The 'Set in Order' step involves organizing items in the workplace in a way that makes them easy to find and use. This reduces time spent searching for tools or materials, improving workflow efficiency.
Why is the 'Shine' (Seiso) step critical in the 5S system?
-The 'Shine' step is critical because it involves regular cleaning and maintenance of the workplace, ensuring that all equipment and materials are in good condition. This helps prevent contamination, wear and tear, and maintains a safe environment.
What does the 'Standardize' (Seiketsu) principle involve?
-The 'Standardize' principle involves establishing standardized practices and procedures for maintaining the order, cleanliness, and organization achieved in the previous steps. It ensures consistency across the workplace.
How does the 'Sustain' (Shitsuke) step ensure long-term success of 5S?
-The 'Sustain' step focuses on creating a culture of discipline where employees and management consistently adhere to the 5S principles. This step involves regular training, reminders, and reinforcing the importance of maintaining 5S practices.
What additional 'S' is sometimes added to the 5S system, and why?
-An additional 'S' for 'Safety' (Anzen) is sometimes added to the 5S system. This emphasizes the importance of maintaining a safe working environment alongside the other principles of organization, cleanliness, and efficiency.
Outlines
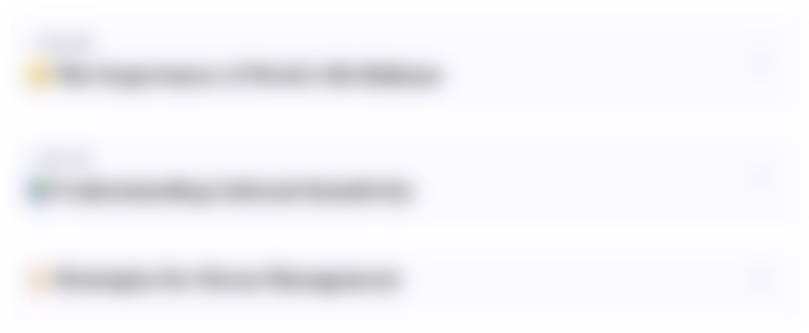
Cette section est réservée aux utilisateurs payants. Améliorez votre compte pour accéder à cette section.
Améliorer maintenantMindmap
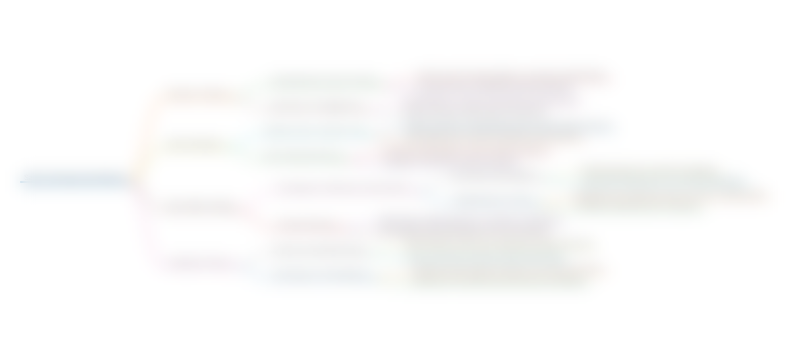
Cette section est réservée aux utilisateurs payants. Améliorez votre compte pour accéder à cette section.
Améliorer maintenantKeywords
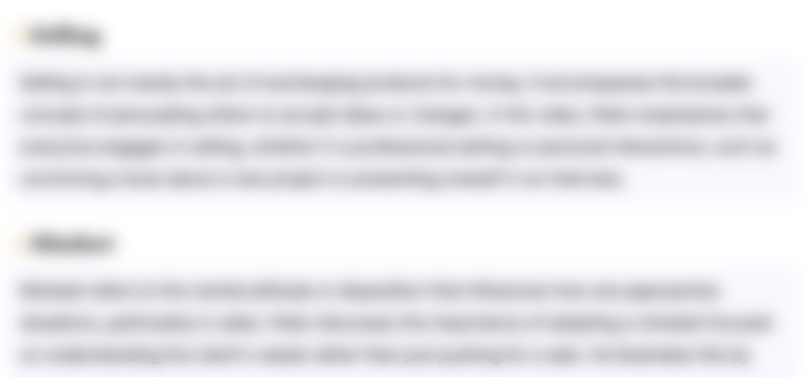
Cette section est réservée aux utilisateurs payants. Améliorez votre compte pour accéder à cette section.
Améliorer maintenantHighlights
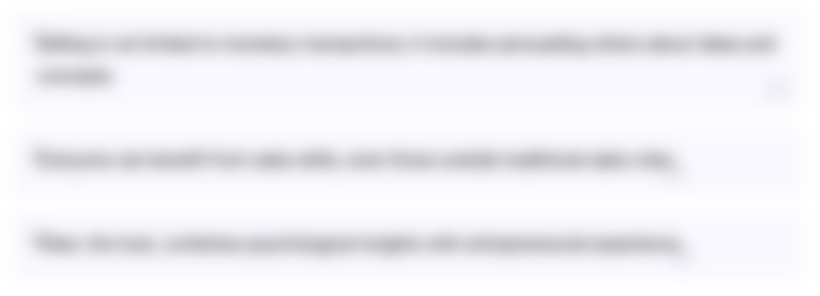
Cette section est réservée aux utilisateurs payants. Améliorez votre compte pour accéder à cette section.
Améliorer maintenantTranscripts
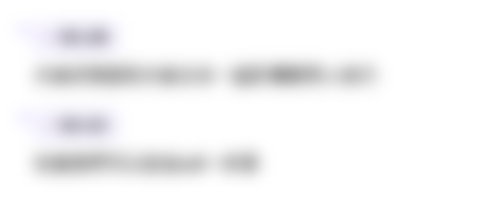
Cette section est réservée aux utilisateurs payants. Améliorez votre compte pour accéder à cette section.
Améliorer maintenantVoir Plus de Vidéos Connexes
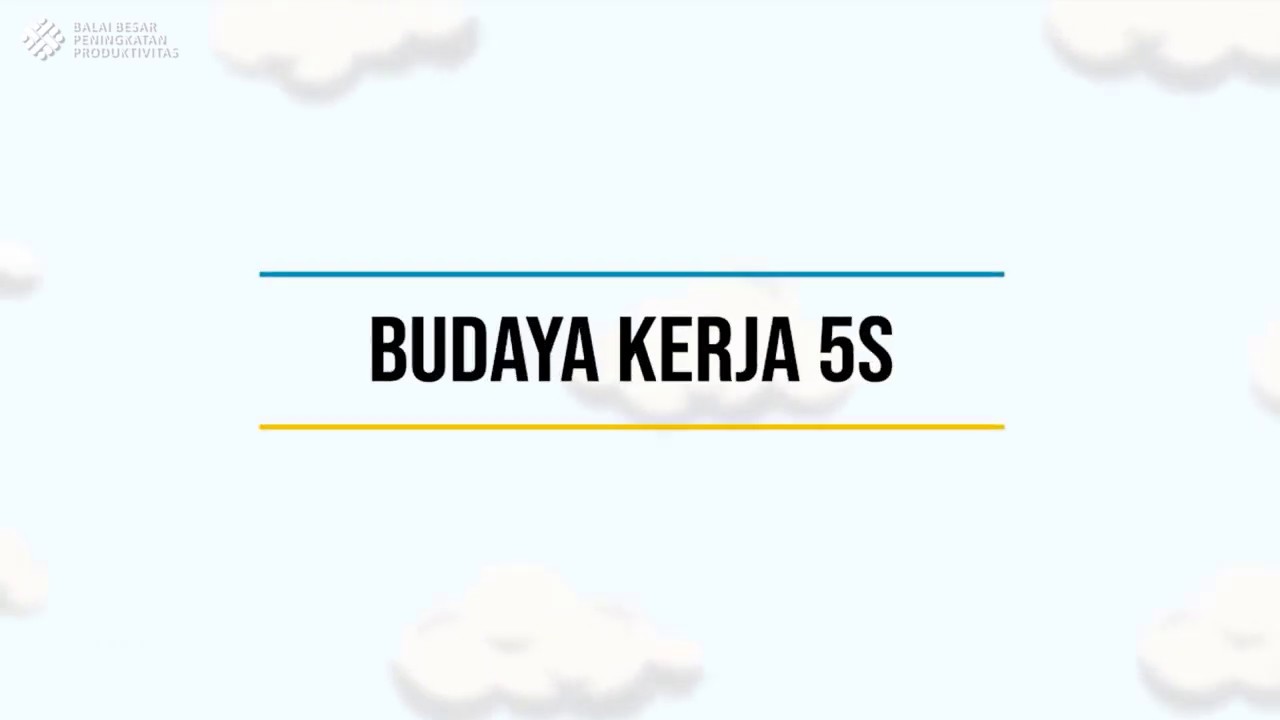
Apasih Budaya Kerja 5S?
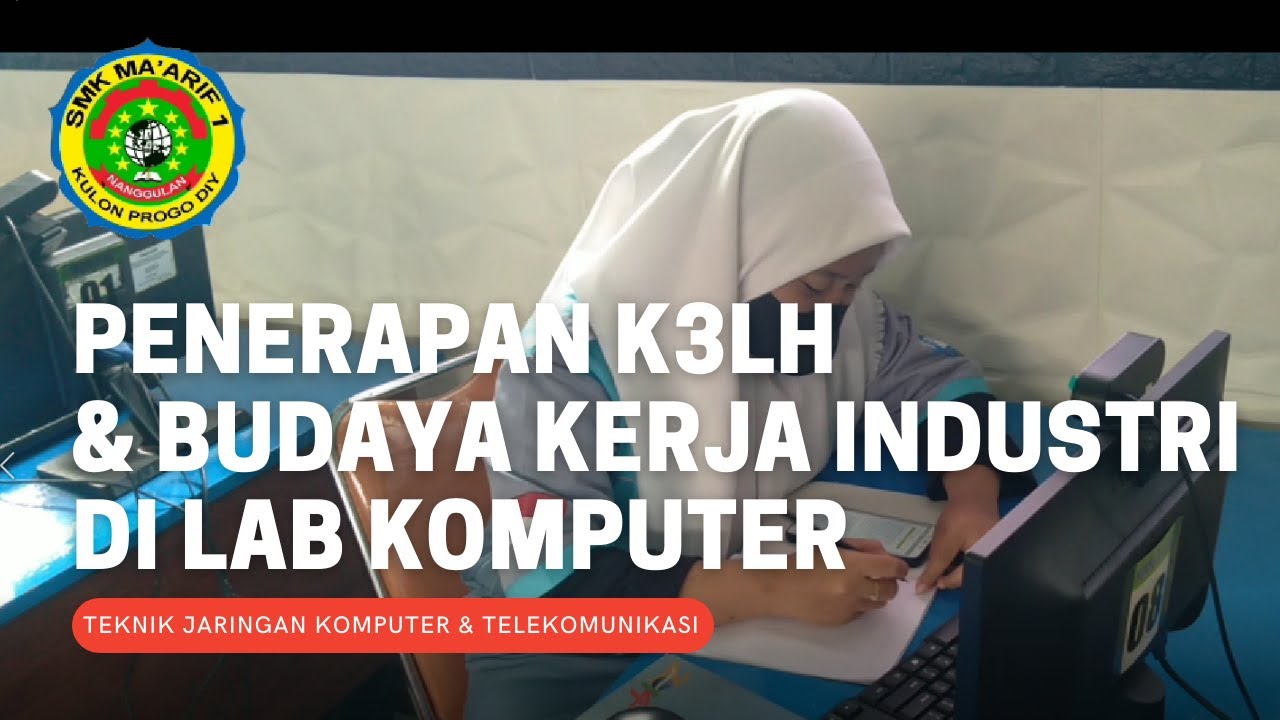
PENERAPAN K3LH DAN BUDAYA KERJA INDUSTRI DI LAB KOMPUTER

Toyota Production Documentary Toyota Manufacturing Production and Assembly at Toyota Factory

BUDAYA KERJA INDUSTRI PERUSAHAAN JEPANG
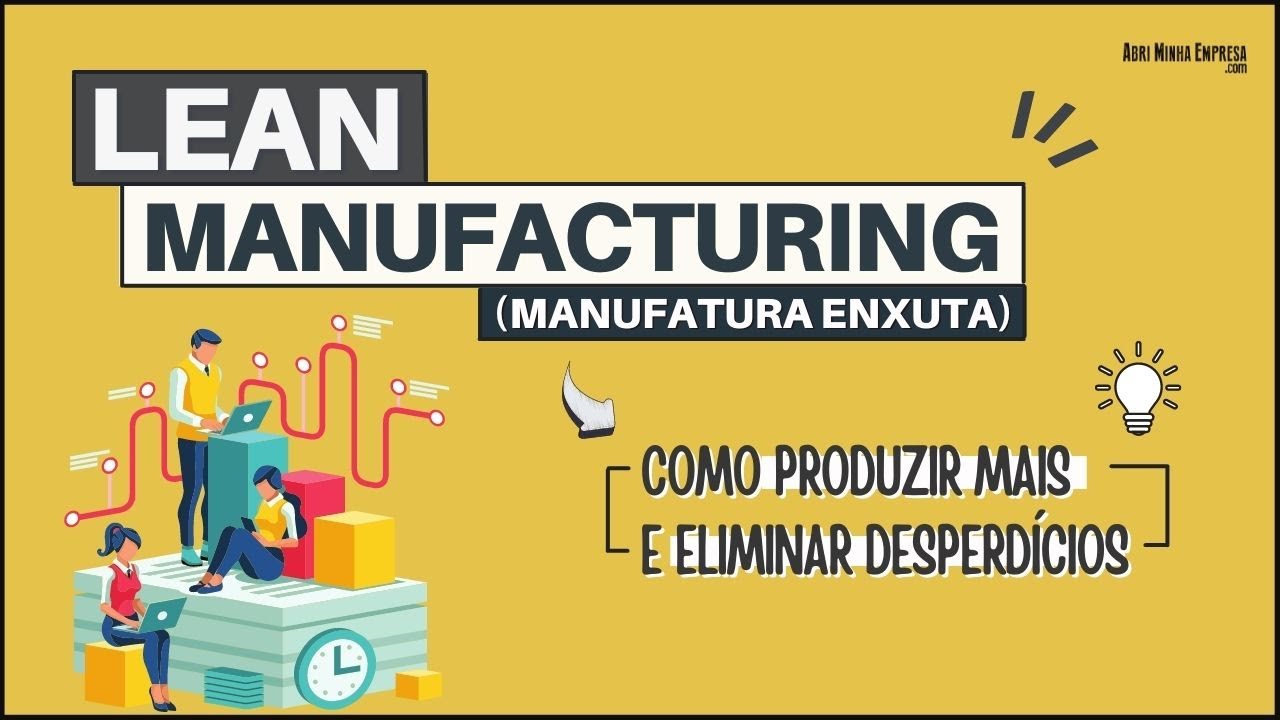
LEAN MANUFACTURING (Manufatura Enxuta) | Conheça os 8 Principais Tipos de Desperdícios

Budaya Kerja dan K3LH | Kompetensi Keahlian Akutansi
5.0 / 5 (0 votes)