The Insane Engineering of the 787
Summary
TLDR本视频深入探讨了波音787梦想飞机如何革新航空工业。通过大量使用复合材料,如碳纤维增强塑料,波音787实现了更轻、更坚固的机身设计,从而提高了燃油效率和乘客舒适度。视频还讨论了787的创新特性,包括其超临界机翼、电加热除冰系统以及为减少阻力而设计的特别技术。尽管复合材料带来了一些挑战,如与铝的电偶腐蚀问题,但波音通过使用钛等材料和创新的3D打印技术来解决这些问题。
Takeaways
- 🛫 航空业正在经历一场革命,大型客机如A380和B747的时代已经结束,新一代飞机正在崛起。
- 💰 波音公司的787梦想飞机是对航空业未来300亿美元的赌注,这一赌注取得了成功。
- 🌐 787梦想飞机是第一款主要使用复合材料(如碳纤维增强塑料)制造的商业客机,复合材料的比重占到了55%。
- 🔨 复合材料由两种或更多种材料组成,如碳纤维增强塑料,它由极其坚固的碳纤维和塑料树脂粘合而成。
- 🚀 波音使用自动化带材铺设技术生产大型飞机部件,提高了生产效率并减少了人工成本。
- 📈 787梦想飞机的机身强度允许其内部气压更高,相当于更低的海拔高度,提升了乘客的舒适度。
- 🪟 由于复合材料的疲劳免疫特性,787的窗户可以做得非常大,而不会产生应力集中。
- 🌬️ 787的机身和机翼设计减少了空气阻力,提高了气动效率,尤其是采用了超临界翼型。
- 🛠️ 波音公司为了降低成本,采用了3D打印钛金属零件的技术,减少了材料浪费并提高了生产速度。
- ⚡️ 787梦想飞机的设计考虑了雷电击中的保护措施,如铜条的铺设和氮气惰化系统。
- 🔄 787是第一款取消传统引气防冰系统的商业客机,采用了更高效的电加热毯技术。
- 🎥 该视频脚本提供了对波音787梦想飞机革命性设计的深入分析,突出了其在材料、结构和系统方面的创新。
Q & A
波音787梦想飞机的开发背景是什么?
-波音787梦想飞机的开发背景是航空业的一次革命,旨在取代以往的大型客机如A380和波音747。随着新飞机的加入,航空公司能够提供更多的直飞航线,并且票价也更为便宜。
波音787梦想飞机在材料上有哪些创新?
-波音787梦想飞机在材料上的创新主要体现在其大量使用了复合材料,如碳纤维增强塑料,这使得它成为第一款主要使用这种新材料的商用客机。复合材料的使用带来了诸多优势,如减轻重量、提高燃油效率和增强飞机的舒适性。
复合材料在波音787梦想飞机中的比重是多少?
-在波音787梦想飞机中,复合材料的比重达到了55%。
波音787梦想飞机的制造过程中使用了哪些先进技术?
-波音787梦想飞机的制造过程中使用了自动化带材铺设技术,通过将预先浸渍有塑料树脂的碳纤维带材包裹在旋转的模具上来制造机身。此外,还使用了大型定制烤箱来固化树脂,并采用了钛合金3D打印技术来减少材料浪费和生产成本。
波音787梦想飞机的燃油效率如何?
-波音787梦想飞机的燃油效率非常高,这得益于其轻量化设计和先进的空气动力学特性。复合材料的使用减少了飞机的重量,而流线型的机身和机翼设计则减少了空气阻力,从而降低了燃油消耗。
波音787梦想飞机的窗户为何比传统飞机更大?
-波音787梦想飞机的窗户之所以比传统飞机更大,是因为其使用复合材料制造的机身具有更高的强度和耐疲劳性能,这使得飞机能够承受更大的窗口开口而不会出现结构问题。
波音787梦想飞机的机翼设计有哪些特点?
-波音787梦想飞机的机翼设计具有高展弦比,这使得机翼在飞行中具有更高的灵活性和更低的阻力。此外,机翼的主梁和肋骨分别使用了碳纤维复合材料和铝合金,以实现最佳的强度和重量比。
波音787梦想飞机如何应对雷电击中的风险?
-波音787梦想飞机通过在其机翼表面铺设铜带来确保电子有低电阻的路径沿着机翼表面流动,防止电子流向燃油箱并引发火花。同时,飞机还配备了氮气惰化系统,通过在油箱中填充氮气来防止点燃。
波音787梦想飞机的驾驶舱窗户框架最初是由什么材料制成的?
-波音787梦想飞机的驾驶舱窗户框架最初是由钛合金制成的,以防止与碳纤维复合材料接触时发生的电偶腐蚀。后来为了降低成本,这些框架被改为铝制,并涂有特殊涂层以防止腐蚀。
波音787梦想飞机的除冰系统与传统飞机有何不同?
-波音787梦想飞机采用了电加热毯来除冰,这种系统通过在飞机的缝翼上粘合电加热毯来加热机翼表面,从而融化或防止冰的形成。这与传统的从发动机提取热引气并将其输送到机翼前缘等易积冰区域的方法相比,更为高效且减少了燃油消耗。
波音787梦想飞机的燃油箱是如何防止爆炸风险的?
-波音787梦想飞机的燃油箱通过氮气惰化系统来防止爆炸风险。该系统通过在油箱中填充氮气来排除氧气,因为燃烧需要氧气的存在。此外,飞机的燃油箱密封件和紧固件也经过特殊设计,以防止电火花的产生。
Outlines
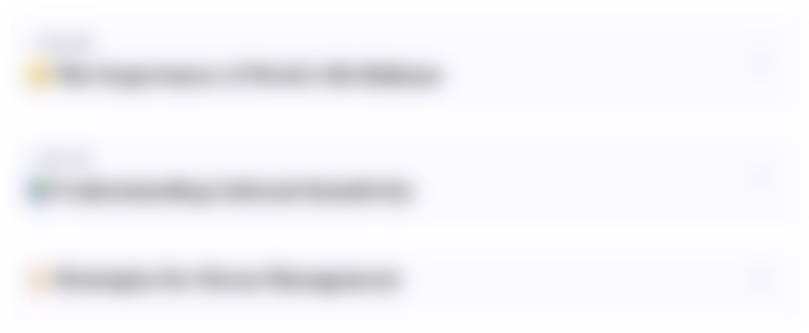
Cette section est réservée aux utilisateurs payants. Améliorez votre compte pour accéder à cette section.
Améliorer maintenantMindmap
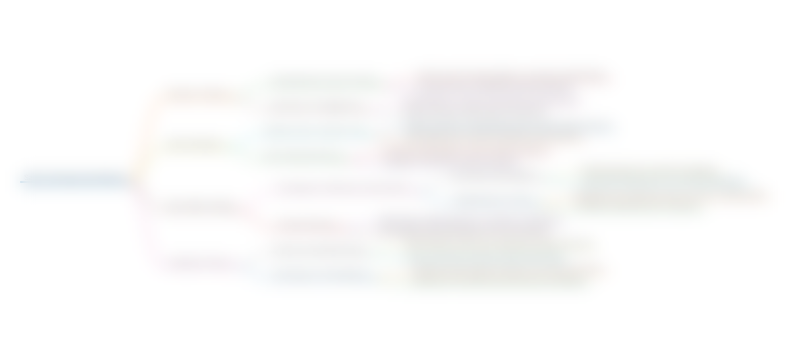
Cette section est réservée aux utilisateurs payants. Améliorez votre compte pour accéder à cette section.
Améliorer maintenantKeywords
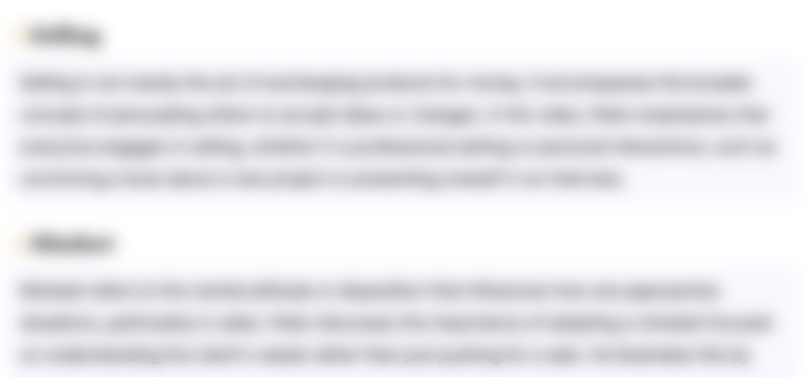
Cette section est réservée aux utilisateurs payants. Améliorez votre compte pour accéder à cette section.
Améliorer maintenantHighlights
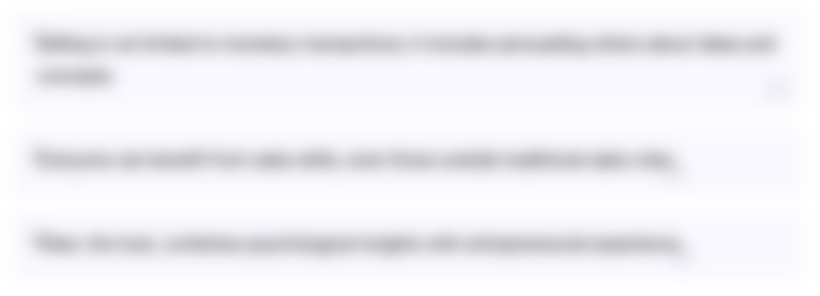
Cette section est réservée aux utilisateurs payants. Améliorez votre compte pour accéder à cette section.
Améliorer maintenantTranscripts
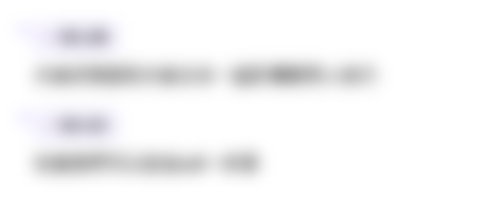
Cette section est réservée aux utilisateurs payants. Améliorez votre compte pour accéder à cette section.
Améliorer maintenantVoir Plus de Vidéos Connexes
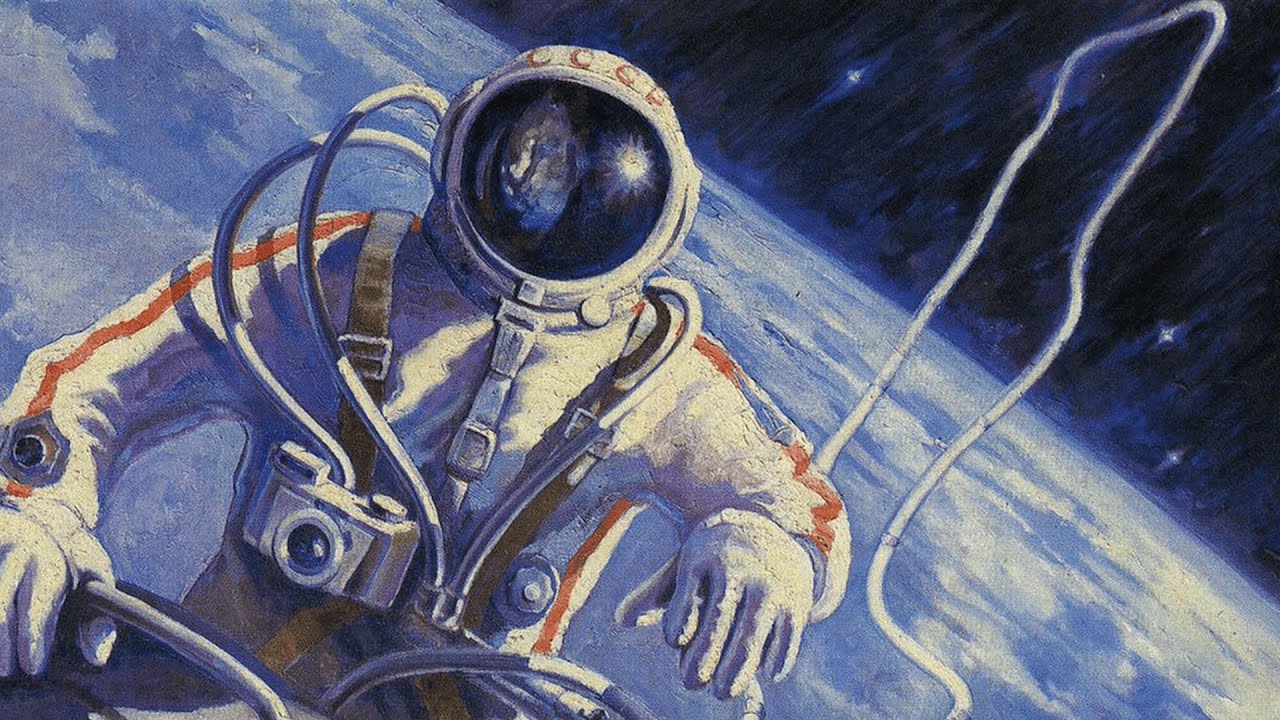
How Soviet Space Art Changed Everything | Video Essay
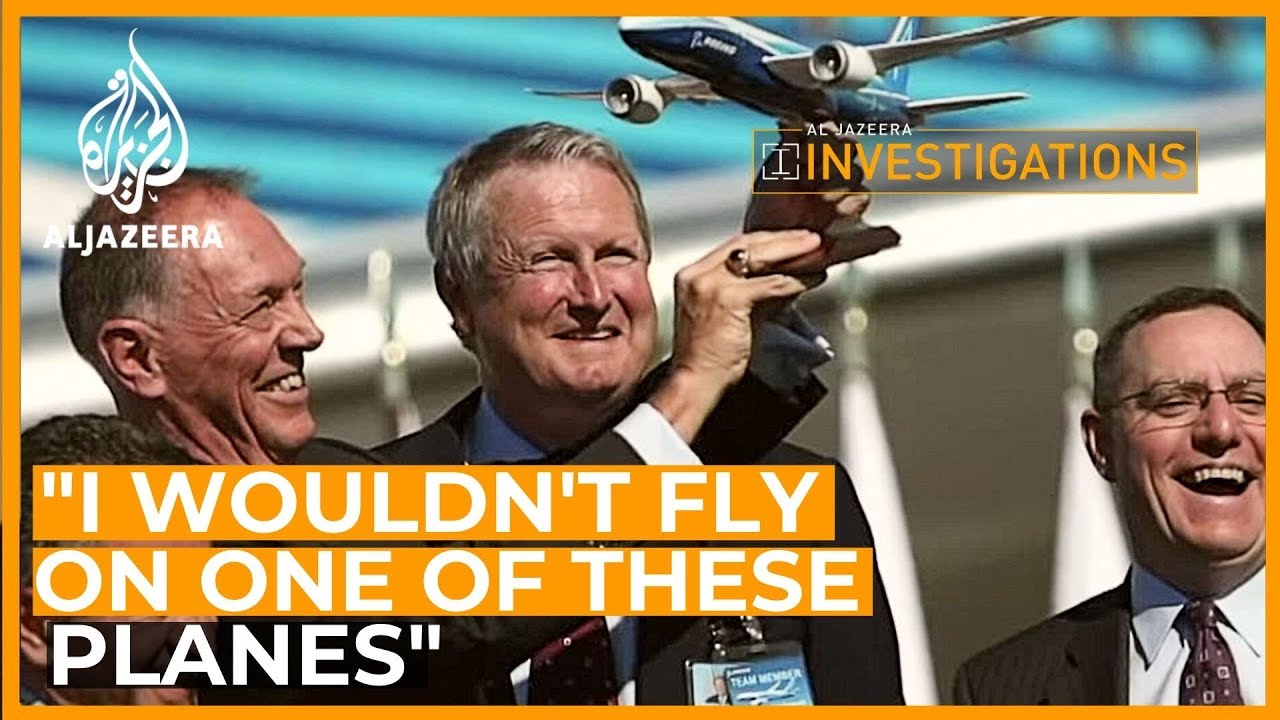
The Boeing 787: Broken Dreams l Al Jazeera Investigations

The Insane Engineering of the GEnX
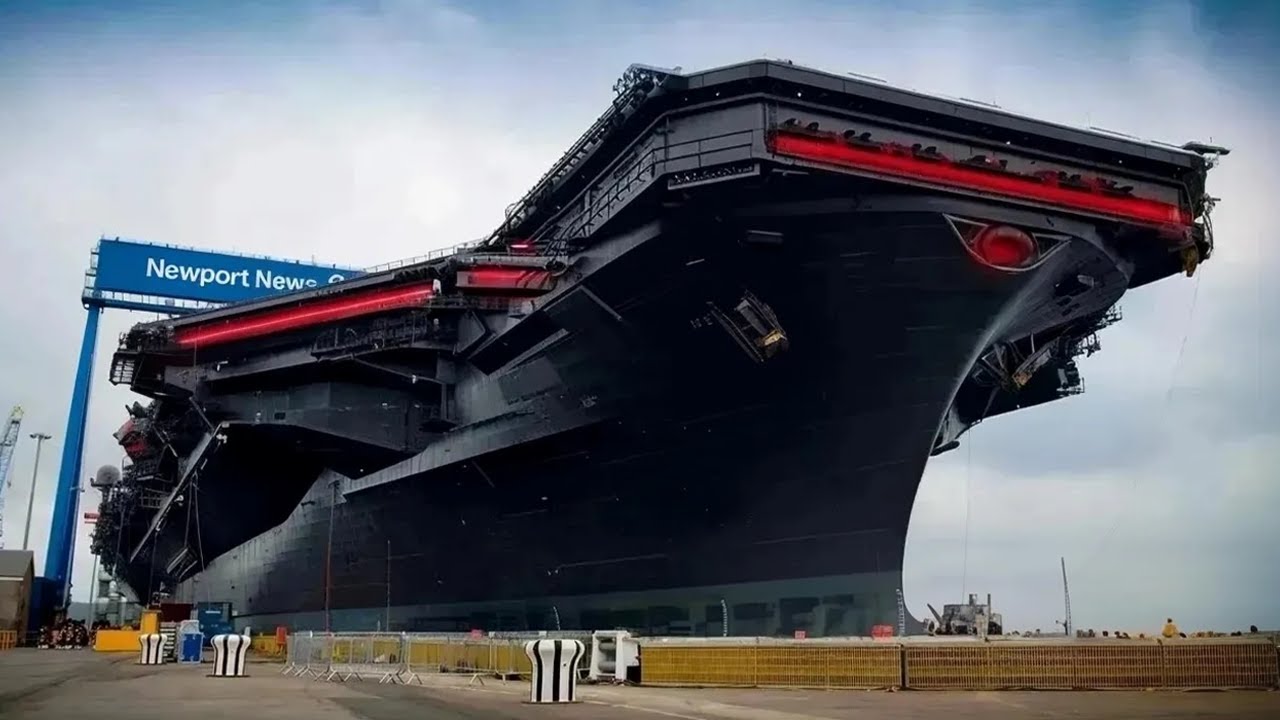
US Revealed Another Brand New $13 Billion Aircraft Carrier To Stop China

Harrier and F-35B: Mastering Vertical Takeoff and Landing in Modern Warfare

These US Air Force Invisible UFO Aircraft Defies All Physics!
5.0 / 5 (0 votes)