How to Program a Basic PID Loop in ControlLogix
Summary
TLDRThis tutorial delves into programming a PID loop control using Rockwell Automation's ControlLogix 5000 PLC and the Enhanced PID controller function block (PIDE). It covers the basics of PID control, the significance of Proportional, Integral, and Derivative gains, and their application in process control. The video guides viewers through configuring the PIDE block in Studio 5000, setting up a control loop for a mixing tank temperature maintenance scenario, and introduces auto-tuning features. It concludes with tips on PID tuning, suggesting the Ziegler-Nichols method for beginners, and invites feedback for further training.
Takeaways
- 🔧 Programming a control loop is essential for controlling variables like temperature, pressure, and flow rate in automation.
- 🛠️ A PID controller is designed to apply corrective actions to a process to achieve a desired set point using feedback from a sensor.
- 🎯 The PIDE function block in Rockwell Automation's ControlLogix 5000 PLC offers enhanced capabilities over the standard PID controller.
- 📈 PID stands for Proportional, Integral, and Derivative, which are the three main components of a PID control loop.
- 🚗 The script uses a car's cruise control as an analogy to explain how PID control works, emphasizing the balance between speed and accuracy.
- 🔄 The PIDE instruction includes an auto-tune feature, which simplifies the tuning process for the control loop.
- 💻 The PIDE is programmed using function block diagrams and is not available for ladder logic programming.
- 📊 The PIDE uses the velocity form of the PID algorithm, which is beneficial for adaptive gains and multi-loop control.
- 🔧 The PIDE allows switching between 'Program' and 'Operator' modes, providing flexibility in control and full bumpless transfer.
- 🛠️ The tutorial walks through the process of setting up a PIDE control loop in Studio 5000, including creating tasks, programs, and configuring the PIDE block.
Q & A
What is a PID process loop controller used for?
-A PID process loop controller is used to generate an output that causes some corrective effort to be applied to a process, driving a measurable process variable towards the desired set point value.
What are the three components of a PID controller?
-The three components of a PID controller are the Proportional (P), Integral (I), and Derivative (D) control mechanisms.
What does PIDE stand for in the context of Rockwell Automation ControlLogix 5000 PLC?
-PIDE stands for Enhanced PID controller function block instruction, which is an Allen Bradley Logix5000 Process Automation Controller or 'PAC' family function block that improves on the standard PID.
What is the purpose of using a function block in programming a PID loop?
-Using a function block in programming a PID loop allows for a structured approach with clear input and output connections, making the control logic easier to understand and maintain.
How does the PIDE instruction differ from the standard PID instruction?
-The PIDE instruction offers an enhanced version with features such as a built-in auto tune feature, velocity form of the PID algorithm, the ability to switch between 'Program' and 'Operator' modes, and more fault handling selections.
What is the significance of the 'P', 'I', and 'D' in PID control?
-In PID control, 'P' stands for Proportional gain, 'I' for Integral time, and 'D' for Derivative gain, which together provide a method for a controller to adjust the process to achieve a desired set point.
Can you explain the concept of 'Proportional' control in PID?
-Proportional control in PID refers to the direct relationship between the controller's output and the current error, meaning the greater the deviation from the set point, the stronger the corrective action.
What is the role of 'Integral' control in a PID loop?
-Integral control in a PID loop accumulates the error over time to eliminate any persistent偏差 and ensure the process variable reaches the set point accurately, even if there are systematic errors.
How does 'Derivative' control contribute to a PID loop?
-Derivative control anticipates changes in the process variable based on its rate of change, helping to manage sudden surges and prevent overshooting the target set point.
What is the purpose of tuning a PID controller?
-Tuning a PID controller involves adjusting the P, I, and D parameters to achieve the desired balance between responsiveness and stability in the control loop, ensuring optimal performance.
Why is it important to set limits on the control variable in a PID loop?
-Setting limits on the control variable in a PID loop is important to prevent the actuator from exceeding its operational range and to ensure the process remains safe and within acceptable parameters.
Outlines
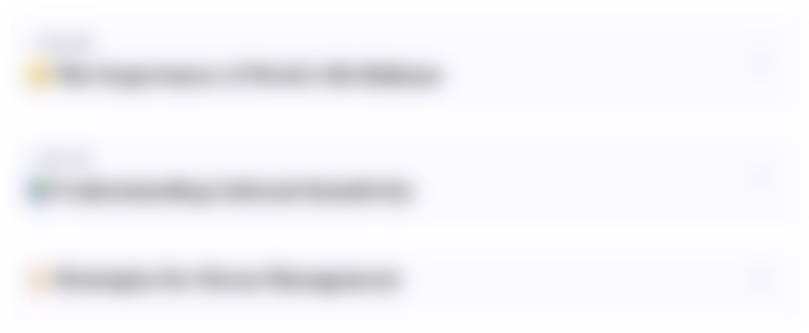
Cette section est réservée aux utilisateurs payants. Améliorez votre compte pour accéder à cette section.
Améliorer maintenantMindmap
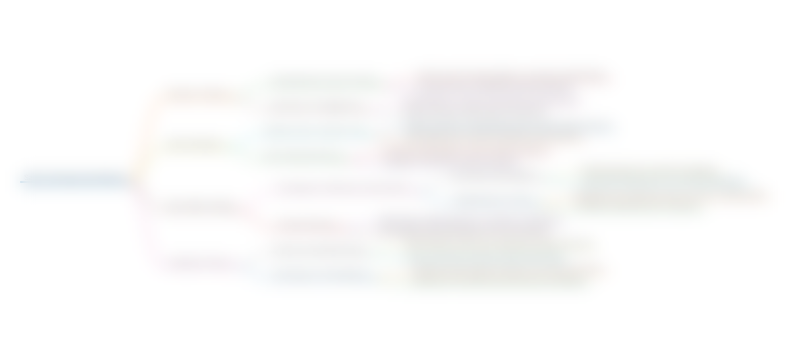
Cette section est réservée aux utilisateurs payants. Améliorez votre compte pour accéder à cette section.
Améliorer maintenantKeywords
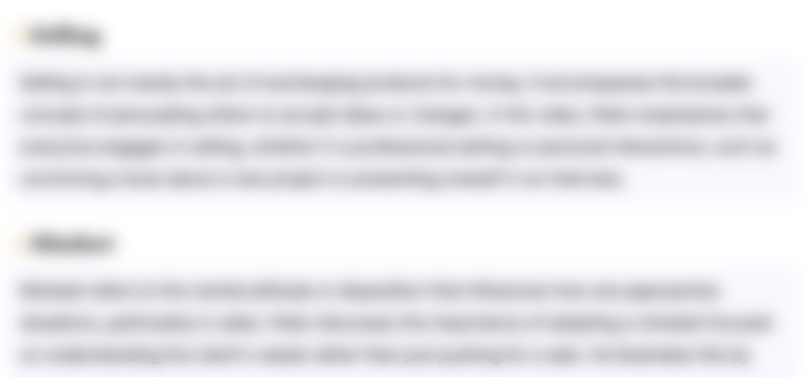
Cette section est réservée aux utilisateurs payants. Améliorez votre compte pour accéder à cette section.
Améliorer maintenantHighlights
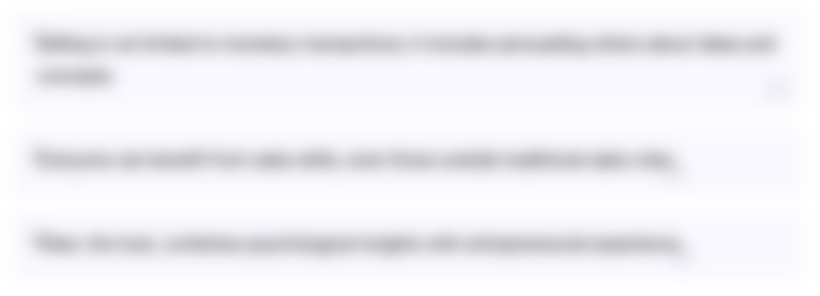
Cette section est réservée aux utilisateurs payants. Améliorez votre compte pour accéder à cette section.
Améliorer maintenantTranscripts
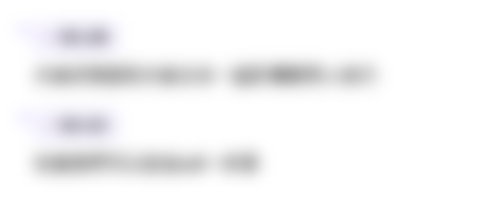
Cette section est réservée aux utilisateurs payants. Améliorez votre compte pour accéder à cette section.
Améliorer maintenantVoir Plus de Vidéos Connexes
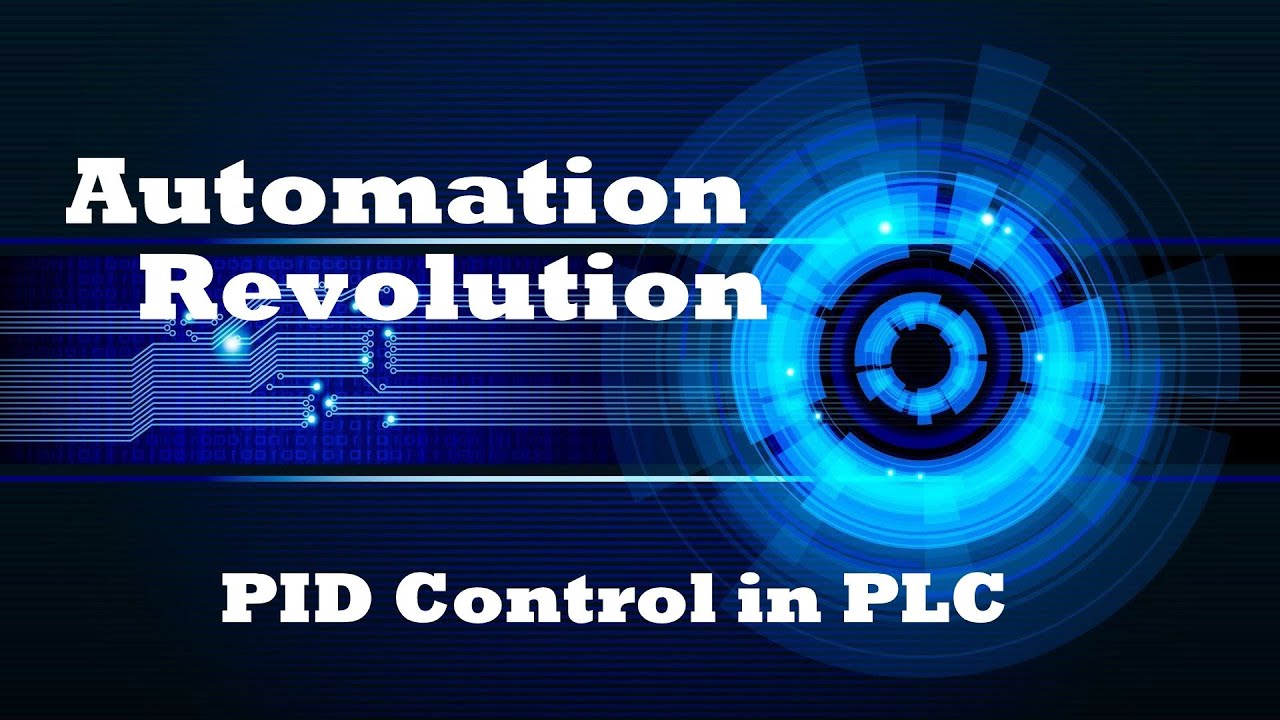
PLC Tutorial 8 : PID Control in Programmable Logic Controller (PLC)

What is a PID Controller?
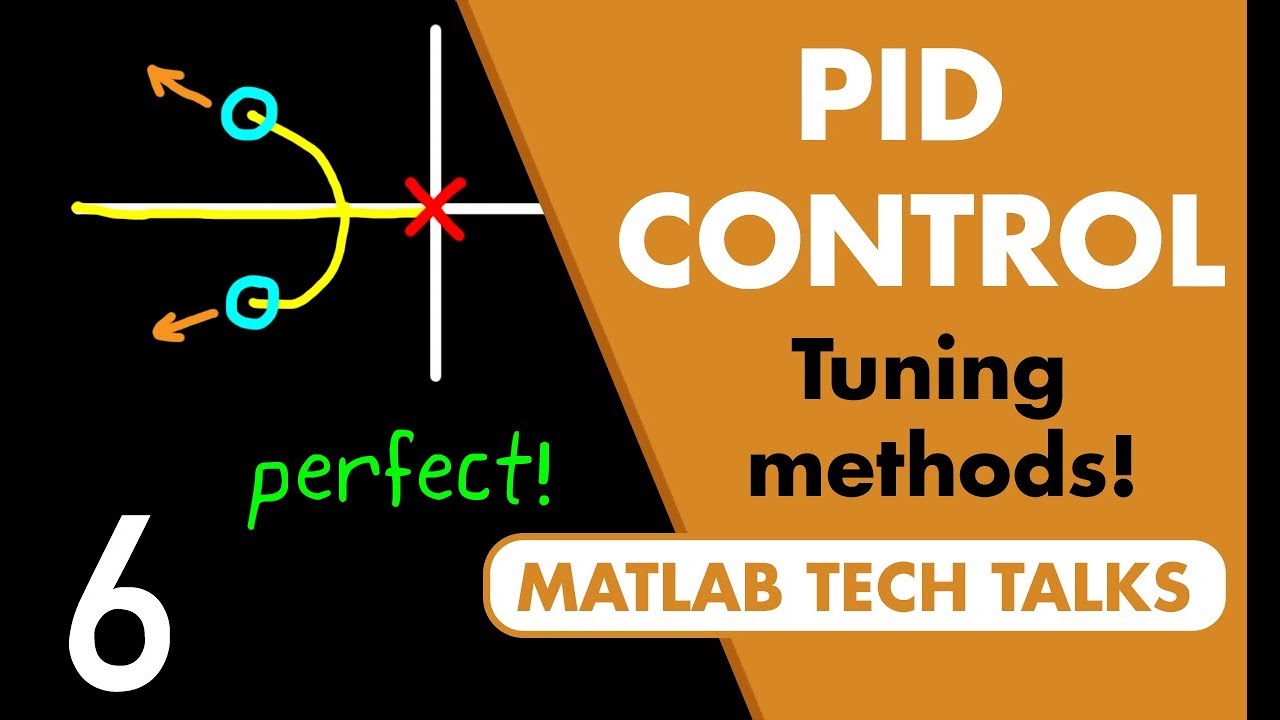
Manual and Automatic PID Tuning Methods | Understanding PID Control, Part 6

PEMROGRAMAN PLC UNTUK OTOMASI INDUSTRI
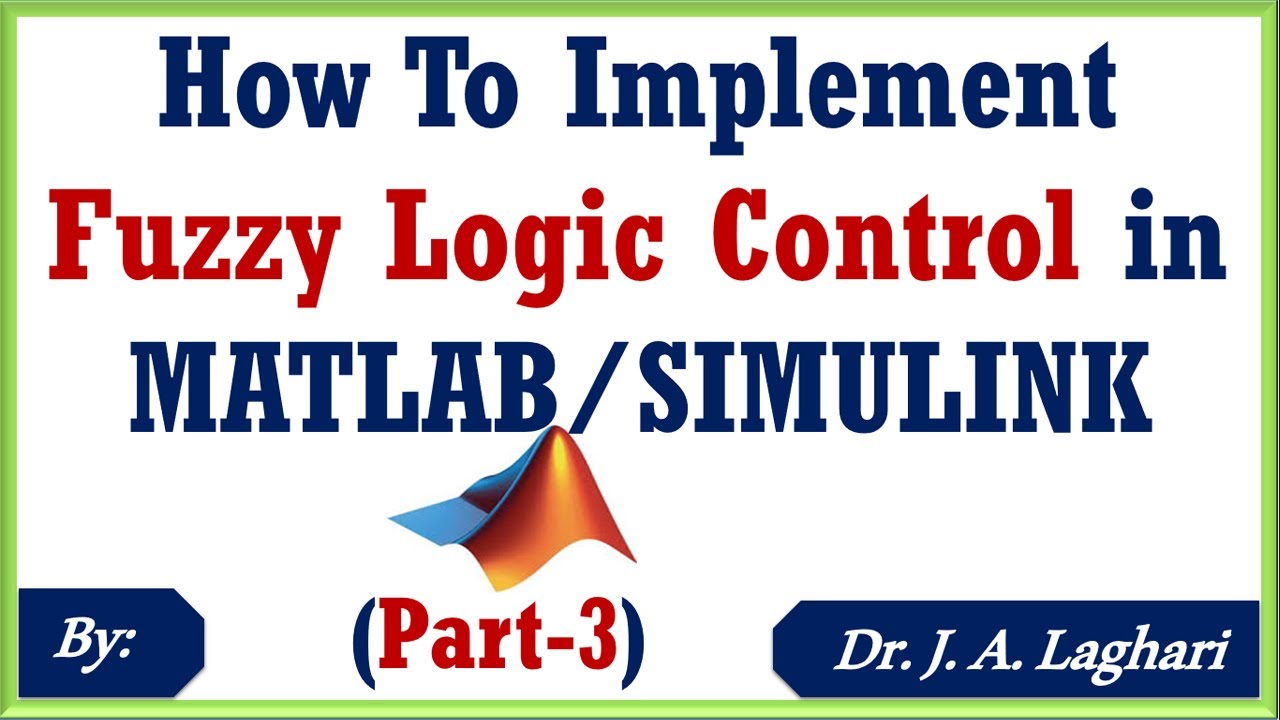
How To Implement Fuzzy Logic Control in MATLAB/SIMULINK ? (Part-3) | Dr. J. A. Laghari
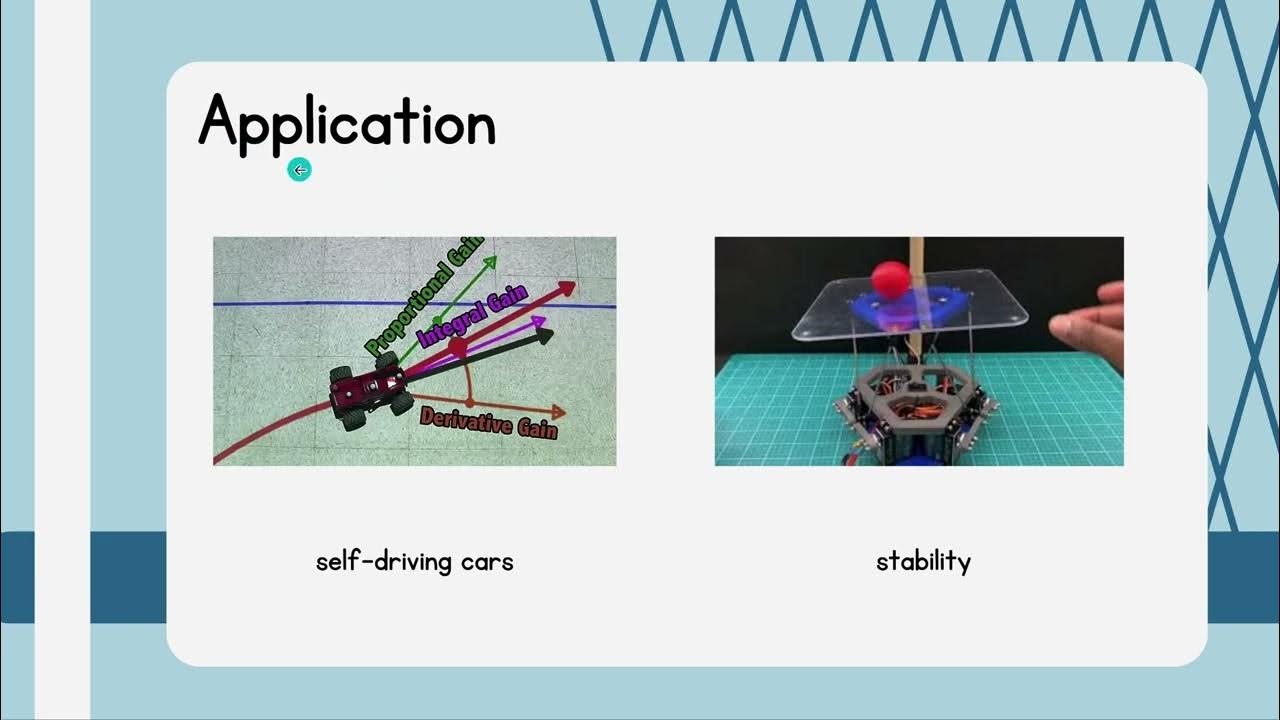
PID Automatic Control - presentation
5.0 / 5 (0 votes)